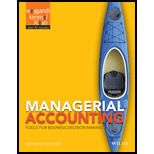
Use incremental analysis for make-or-buy decision.
(LO 3), E
Jobs. Inc. has recently started the manufacture of Tri-Robo. a three-wheeled robot that can scan a home for fires and gas leaks and then transmit this information to a smart-phone. The cost structure to manufacture 20.000 Tri-Robos is as follows.
Cost | |
Direct materials ($50 per robot) | $1,000,000 |
Direct labor ($40 per robot) | 800,000 |
Variable |
120,000 |
Allocated fixed overhead ($30 per robot) | 600,000 |
Total | $2,520,000 |
Jobs is approached by Tienh Inc., which offers to make Tri-Robo for $115 per unit or $2,300,000.
Instructions
(a) Using incremental analysis, determine whether Jobs should accept this offer under each of the following independent assumptions.
(1) Assume that $405,000 of the fixed overhead cost can be avoided.
(2) Assume that none of the fixed overhead can be avoided. However, if the robots are purchased from Tienh Inc., Jobs can use the released productive resources to generate additional income of $375,000.
(b) Describe the qualitative factors that might affect the decision to purchase the robots from an outside supplier.

Trending nowThis is a popular solution!

Chapter 7 Solutions
Managerial Accounting: Tools for Business Decision Making
- Munabhaiarrow_forwardRahularrow_forwardUse the information provided to create a standard cost card for production of one glove box switch. To make one switch it takes 16 feet of plastic-coated copper wire and 0.5 pounds of plastic material. The plastic material can usually be purchased for $20.00 per pound, and the wire costs $2.50 per foot. The labor necessary to assemble a switch consists of two types. The first type of labor is assembly, which takes 3.5 hours. These workers are paid $27.00 per hour. The second type of labor is finishing, which takes 2 hours. These workers are paid $29.00 per hour. Overhead is applied using labor hours. The variable overhead rate is $14.90 per labor hour. The fixed overhead rate is $15.60 per hour.arrow_forward
- Sir please help me urgently please provide a complete answerarrow_forwardA machine shop is considering combining machining and turning centers into a single Mazak Multi-Tasking machine center. Multitasking in the machine world is the combining of processes that were traditionally processed on multiple machines onto one machine. The ultimate goal is to turn, mill, drill, tap, bore, and finish the part in a single setup. The total investment cost is RM6 million with following anticipated cost savings: Current Cost (% saved) Savings Setup $340 000 75% Scrap/Rework 63 530 80% Operators 228 000 100% Fixturing 190 000 80% Programming time 85 000 75% Floor space 40 000 80% Maintenance 50 000 70% Coolant 20 000 65% Inspection 124 926 100% Documentation 10 000 65% Expediting 30 000 80% Total Annual Savings Most machine shops typically use 20 years and assume a 25% residual value at the end of the project life. It is also very common for a learning curve to take place in operating a complex new machine. To allow for the learning curve, assume that only 60% of the…arrow_forwardShow your solution and final answerarrow_forward
- i need the answer quicklyarrow_forwardWoodruff Company is currently producing a snowmobile that uses five specialized parts. Engineering has proposed replacing these specialized parts with commodity parts, which will cost less and can be purchased in larger order quantities. Current activity capacity and demand (with specialized parts required) and expected activity demand (with only commodity parts required) are provided. Activities Activity Driver ActivityCapacity Current ActivityDemand Expected ActivityDemand Material usage Number of parts 200,000 200,000 200,000 Installing parts Direct labor hours 20,000 20,000 16,000 Purchasing parts Number of orders 7,600 6,498 3,990 Additionally, the following activity cost data are provided: Material usage: $11 per specialized part used; $27 per commodity part; no fixed activity cost. Installing parts: $21 per direct labor hour; no fixed activity cost. Purchasing parts: Four salaried clerks, each earning a $47,000 annual salary; each clerk is capable of processing 1,900…arrow_forwardMozaic Inc. has decided to introduce a new product, which can be manufactured by either a computer-assisted manufacturing system (CAM) or a labor-intensive production system (LIP). The manufacturing method will not affect the quality of the product. The estimated manufacturing costs by the two methods are as follows: www CAM System LIP System Direct Material $5.00 $5.60 Direct Labor (DLH) 0.5 DLH x $12 $6.00 0.8 DLH x $9 $7.20 Variable Overhead 0.5 DLH x $6 $3.00 0.8 DLH x $6 $4.80 Fixed Overhead* $2,440,000 $1,320,000 * These costs are directly traceable to the new product line. They would not be incurred if the new product were not produced. The company's marketing research department has recommended an introductory unit sales price of $30. Selling expenses are estimated to be $500,000 annually plus $2 for each unit sold. (Ignore income taxes.) Required: 1. Describe the circumstances under which the firm should employ each of the two manufacturing methods. 2. Identify some business…arrow_forward
- Principles of Accounting Volume 2AccountingISBN:9781947172609Author:OpenStaxPublisher:OpenStax College