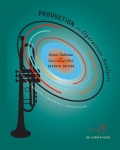
Concept explainers
(a)
Interpretation:
The total number of standing that should P’s have with its supplier and the ways these orders should be placed.
Concept Introduction:
The economic order quantity, often called EOQ refers to the order quantity that helps the organization in minimizing the ordering and holding cost of the organization’s business.
(a)

Explanation of Solution
Given data:
Monthly demand = 60 units
Annual demand
Ordering cost = $20
The economic order quantity will be calculated by the following formula.
Hence, the optimal order quantity that P should order with its suppliers is 216.22 units.
Cycle time will be calculated by the following formula.
Q*= Economic order quantity
Thus, the order should be placed after every 0.3 years or 3.6 months.
(b)
Interpretation:
If it takes 3 weeks to receive a shipment, then the total inventory in hand while placing the order.
Concept Introduction:
The re-order level refers to the inventory level at which an organization would place a new order or begin a new manufacturing run.
(b)

Explanation of Solution
The re-order level will be calculated by the following formula
Thus, on-hand inventory will be 45 units when the new order will be placed.
(c)
Interpretation:
The average annual holding and fixed costs associated with these filters assuming they adopted an optimal policy.
Concept Introduction:
The economic order quantity, often called EOQ refers to the order quantity that helps the organization in minimizing the ordering and holding cost of the organization’s business.
(c)

Explanation of Solution
The average annual holding cost will be calculated by the following formula.
The average annual holding cost is $133.194
(d)
Interpretation:
The store of P’s in the city is small, the ways this might affect the solution recommended in part (a).
Concept Introduction:
Inventory management is the process of ordering, storing, and using the organization’s inventory.
(d)

Explanation of Solution
When the inventory is sourced from the suppliers, it is required to store at a suitable place for future use. If space will be less, then it will definitely impact the optimal quantity as there is less space to hold or store inventory. Thus, space impacts the optimal quantity to be ordered as it needed to be stored for the continuing requirement during the cycle time of production.
Want to see more full solutions like this?
Chapter 4 Solutions
EBK PRODUCTION AND OPERATIONS ANALYSIS
- Jim's Job Shop buys two parts (Tegdiws and Widgets) for use in its production system from two different suppliers. The parts are needed throughout the entire 52-week year. Tegdiws are used at a relatively constant rate and are ordered whenever the remaining quantity drops to the reorder level. Widgets are ordered from a supplier who stops by every three weeks. Data for both products are as follows: a. What is the inventory control system for Tegdiws? Reorder quantity = 1,225 Reorder point = 824.24 b. Find the total inventory costs if using inventory policy. This is a case considering safety stock (Do not use Excel, show your work) Holding cost per unit per year is given as a percentage of item cost ITEM TEGDIW WIDGET Annual Demand 10,000 5,000 Holding cost (% of item cost) 20% 20% Set up or order cost $150.00 $25.00 Lead Time 4 weeks 1 week Safety stock 55 units 5 units Item cost $10.00 $2.00arrow_forwardAlina Limited is a manufacturer of widgets orders components for use in manufacturing. The estimated demand for the components during the coming year is 15,000. Order costs are $100 per order; carrying costs are $12 per component. Using the economic order quantity model What is Alina Ltd’s optimum order quantity? If the supplier guarantees a three (3) day delivery on any order that is placed, What is the re-order point?arrow_forwardJill's Job Shop buys two parts (Tegdiws and Widgets) for use in its production system from two different suppliers. The parts are needed throughout the entire 52-week year. Tegdiws are used at a relatively constant rate and are ordered whenever the remaining quantity drops to the reorder level. Widgets are ordered from a supplier who stops by every three weeks. Data for both products are as follows: A. Find the total inventory costs if using inventory policy. This is a case considering safety stock (make sure to use the right formula)arrow_forward
- David Alexander has compiled the following table of six itemsin inventory at Angelo Products, along with the unit cost andthe annual demand in units:IDENTIFICATION CODE UNIT COST ($) ANNUAL DEMAND(UNITS)XX1 5.84 1,200B66 5.40 1,1103CPO 1.12 89633CP 74.54 1,104R2D2 2.00 1,110RMS 2.08 961 Use ABC analysis to determine which item(s) should be care-fully controlled using a quantitative inventory technique and which item(s) should not be closely controlled.arrow_forwardJill's Job Shop buys two parts (Tegdiws and Widgets) for use in its production system from two different suppliers. The parts are needed throughout the entire 52-week year. Tegdiws are used at a relatively constant rate and are ordered whenever the remaining quantity drops to the reorder level. Widgets are ordered from a supplier who stops by every three weeks. Data for both products are as follows: a. What is the inventory control system for Tegdiws? That is, what is the reorder quantity and what is the reorder point? b. Find the total inventory costs if using inventory policy. This is a case considering safety stock (make sure to use the right formulas)arrow_forwardJill's Job Shop buys two parts (Tegdiws and Widgets) for use in its production system from two different suppliers. The parts are needed throughout the entire 52-week year. Tegdiws are used at a relatively constant rate and are ordered whenever the remaining quantity drops to the reorder level. Widgets are ordered from a supplier who stops by every three weeks. Data for both products are as follows: a. What is the inventory control system for Tegdiws? That is, what is the reorder quantity and what is the reorder point? b. Find the total inventory costs if using inventory policy.arrow_forward
- Jill's Job Shop buys two parts (Tegdiws and Widgets) for use in its production system from two different suppliers. The parts are needed throughout the entire 52-week year. Tegdiws are used at a relatively constant rate and are ordered whenever the remaining quantity drops to the reorder level. Widgets are ordered from a supplier who stops by every three weeks. Data for both products are as follows: a. What is the inventory control system for Tegdiws? That is, what is the reorder quantity and what is the reorder point? b. Find the total inventory costs if using inventory policy. This is a case considering safety stock (make sure to use the right formulas) Holding cost per unit per year is given as a percentage of item cost ITEM TEGDIW WIDGET Annual Demand 10,000 5,000 Holding cost (% of item cost) 20% 20% Set up or order cost $150.00 $25.00 Lead Time 4 weeks 1 week Safety stock 55 units 5 units Item cost $10.00 $2.00arrow_forward13.13 The TransCanada Lumber Company and Mill processes 10,000 logs annually, operating 250 days per year. Immediately upon receiving an order, the logging company's supplier begins delivery to the lumber mill at the rate of 60 logs per day. The lumber mill has determined that the ordering cost is $1600 per order, and the cost of carrying logs in inventory before they are processed is $15 per log on an annual basis. Determine the following: a. The optimal order size b. The total inventory cost associated with the optimal order quantity c. The number of operating days between orders d. The number of operating days required to receive an orderarrow_forwardI NEED IT TODAY, 1. B&H needs to decide how to manage its inventory of cameras. The demand for cameras at B&H is 200 cameras per week. Each time that B&H places an order for a new shipment of cameras, it must pay $80 in fixed processing fees. A camera costs B&H $60 to purchase. The cost for B&H to hold a camera in its store for one week is $4. Assume that the lead time for the delivery of a camera is 0 weeks.a. Suppose that B&H places orders for cameras in quantities of 50 cameras at a time and places a new order for cameras each time that it runs out. Draw a graph showing the number of cameras that B&H has on-hand in inventory at each point in time up until the time when it places its fourth order. Label the points in time at which B&H places a new order. Assume that B&H places its first order for 50 cameras on day 0.b. Suppose again that B&H places orders for 50 cameras at a time. What will be B&H’s average holding costs per week? What will…arrow_forward
- You are a newsvendor selling the San Pedro Times every morning. Before you get to work, you go to the printer and buy the day’s paper for $0.25 a copy. You sell a copy of the San Pedro Times for $1.00. Daily demand is distributed normally with mean 5 250 and standard deviation 5 50. At the end of each morning, any leftover copies are worthless and they go to a recycle bin. a. How many copies of the San Pedro Times should you buy each morning? b. Based on part (a), what is the probability that you will run out of stock?arrow_forwardexplain the characteristics of inventory situations: 1. lead time 2. sources and level of risk 3. Static versus dynamic problemsarrow_forwardCharlie's Pizza orders all of its pepperoni, olives, anchovies, and mozzarella cheese to be shipped directly from Italy. An American distributor stops by every four weeks to take orders. Because the orders are shipped directly from Italy, they take three weeks to arrive. Charlie's Pizza uses an average of 180 pounds of pepperoni each week, with a standard deviation of 28 pounds. Charlie's prides itself on offering only the best-quality ingredients and a high level of service, so it wants to ensure a 98 percent probability of not stocking out on pepperoni. Assume that the sales representative just walked in the door and there are currently 450 pounds of pepperoni in the walk-in cooler. How many pounds of pepperoni.arrow_forward
- Purchasing and Supply Chain ManagementOperations ManagementISBN:9781285869681Author:Robert M. Monczka, Robert B. Handfield, Larry C. Giunipero, James L. PattersonPublisher:Cengage Learning
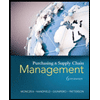