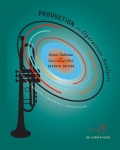
Concept explainers
(a)
To determine: The optimal rotational cycle time.
Introduction:Economic order quantity refers to the approach which is used to evaluate flow and volume of order needed to fulfill consumers demand while reducing the cost per order.Such tool is used by the organization to handle andmanage operations and logistic operations.
(a)

Explanation of Solution
Optimal cycle time of the fiber store is as follows.
Apply variables of each type of items and determine optimal cycle time by the following formula.
Similarly, the modified holding cost for each of the item should be calculated by the following method.
Item | Annual Sales | Cost | |||||
A | 25,900 | 1125000 | .003 | .00063 | .000615 | 120 | 15.9285 |
B | 42,000 | 1375000 | .002 | .00042 | .000407 | 80 | 17.094 |
C | 14,400 | 825000 | .008 | .00168 | .00165 | 160 | 23.76 |
D | 46,000 | 800000 | .002 | .00042 | .000395 | 80 | 18.17 |
E | 12,500 | 450000 | .001 | .0021 | .002041 | 60 | 25.5125 |
F | 75,000 | 975000 | .005 | .00105 | .000969 | 120 | 72.675 |
G | 30,000 | 725000 | .004 | .00084 | .000805 | 20 | 24.15 |
H | 18,900 | 300000 | .007 | .00147 | .001377 | 60 | 26.0253 |
SUM | 0.008259 | 700 | 223.315 |
Put the value of each item to determine the optimal cycle time.
Hence, the optimal rotation cycle time is 2.50 per year
(b)
To determine:TheSize of the lots.
Introduction: Economic order quantity sometimes EOQ refers to the technique used by the organizations to determine the volume and frequency or order needed to fulfill the customer demand while minimizing the cost of the item.
(b)

Explanation of Solution
Determine the optimal quantity of each item by the following formula.
Same procedure will be followed to calculate optimal quantity for each item
Item | Demand | Time | Quantity (Q) |
A | 25,900 | 2.5 | 64750 |
B | 42,000 | 2.5 | 105000 |
C | 14,400 | 2.5 | 36000 |
D | 46,000 | 2.5 | 115000 |
E | 12,500 | 2.5 | 31250 |
F | 75,000 | 2.5 | 187500 |
G | 30,000 | 2.5 | 75000 |
H | 18,900 | 2.5 | 47250 |
(C)
To determine:Average annual cost of holding and setup cost at the optimal solution.
Introduction: Economic order quantity sometimes EOQ refers to the technique used by the organizations to determine the volume and frequency or order needed to fulfill the customer demand while minimizing the cost of the item.
(C)

Explanation of Solution
Procedure to find average annual cost of holding and setup cost is discussed below.
Determine the annual holding and setup cost by the following formula.
Determine the values to calculate annual holding cost for the item A by the following method
Same procedure will be followed to calculate optimal quantity for each item
Item | Setup cost (K*D/Q) | Holding Cost (H*Q/2) | Total |
A | 48 | 19.91 | 67.91 |
B | 32 | 21.37 | 53.37 |
C | 64 | 29.70 | 93.70 |
D | 32 | 22.71 | 54.71 |
E | 24 | 31.89 | 55.89 |
F | 48 | 90.84 | 138.84 |
G | 8 | 30.19 | 38.19 |
H | 24 | 32.53 | 56.53 |
SUM | 559.14 |
Hence, annual cost of holding and setup is $559.14
(d)
To determine: Contractual obligation that G might have with the fabrics that would stop them from implementing the policy mention in part (a) and (b).
Introduction:Economic order quantity sometimes EOQ refers to the technique used by the organizations to determine the volume and frequency or order needed to fulfill the customer demand while minimizing the cost of the item.
(d)

Explanation of Solution
With the responsibility or obligation, the time required to supply 3 shipments will be 4 times in a year instead of 2.5. Hence, the size of the optimal quantity will vary as the cycle time being changed to 4 times in a year.
Hence, to make shipment thrice in a year it is very much important for the firm to change its cycle time and optimal quantity of every item to remain focused in their commitment.
Want to see more full solutions like this?
Chapter 4 Solutions
EBK PRODUCTION AND OPERATIONS ANALYSIS
- Demand for portable music players for joggers has caused Nancy Industries (Nancy) to grow almost 50 percent over the past year. The number of joggers continues to expand, so Nancy expects demand for music player to also expand, because, as yet, no safety laws have been passed to prevent joggers from wearing them. Demands for the players for last year was as follows : Month Demand (units) Jan 4200 Feb 4300 Mar 4000 Apr 4400 May 5000 Jun 4700 Jul 5300 Aug 4900 Sep 5400 Oct 5700 Nov 6300 Dec 6000 Question : From the choice of simple moving average, weighted moving average, exponential smoothing, and linear regression analysis, which forecasting technique would you consider the most accurate to Nancy Industries? Why?arrow_forwardWhich are some of the things that drive variability in demand management and forecasting? 1. MOQs 2. Promotional sales on products 3. Supplier contracting 4. Order fulfillment 5. Network planning 6. None of the above Please give me answer ASAP with clear explanation.arrow_forward(a) Give examples of independent and related dependent demand (b) APL company assembles and sales an electronics device (ED) on a contract basis. End item ED has composed of 3 units of subassembly BG and 5 units of component DD. BG is assembled using 3 DDs and 4 FCs. There are orders of 500 and 875 units of the device (ED) at the beginning of week 6 and week 8. In assembling BG, an extra 20 percent scrap allowance must be added. DD can only be ordered in whole cases of 400 units per case. One case of DD is received in each of week 1 and week 2. Also, there are 200 units of BG and 425 units of DD now on hand. The lead time for the item BG, DD, and FC is 2 weeks and that is for the item ED is 1 week.i. Calculate the required number of DD and FC for producing 100 units of ED. There is no stock of any item. ii. Prepare a material requirements plan for the component DD.arrow_forward
- ABC analysis on the following set of products Item Annual Demand Unit CostA 211 800 R9B 390 100 R90C 003 450 R6D 100 400 R100E 707 85 R2,000F 660 250 R320G 473 500 R75H 921 100 R75 Soft goods department sells 175 units per month of a certain large bath towel. The unit cost of a towel to the manufacturer is R2.50 and the cost of placing an order has been estimated to be R12.00. There is an inventory carrying charge of 27% of the unit cost per year. What is the optimal order quantity, the order frequency, and the annual holding and setup cost. If the ordering cost can be cut to R4.00, what will be the new economicorder quantity, the order frequency, and annual holding and setup costs.arrow_forwardSpecialty Toys, Inc., sells a variety of new and innovative children's toys. As with other products, Specialty faces the decision of how may Weather Teddy units to order for coming holiday season. Members of the management team suggested order quantities of 15,000, 18,000, 24,000, 28,000 units. The wide range of order quantities suggested indicates considerable disagreement concerning the market potential. The product management team ask you for analysis of the stock-out probabilities for various order quantities, an estimate of the product potential, and to help make an order quantity recommendation. Specialty expects to sell Weather Teddy for $24 based on cost of $16 per unit. If inventory remains after the holiday season, Specialty will sell all surplus inventory for $5 per unit. After reviewing the sales history of similar products, Specialty%u2019s sales forecaster predicted and expected demand of 20,000 units with a .95 probability that demand would be between 10,000 units and…arrow_forwardExplain what methods are the house of quality produced by in inventory management ?arrow_forward
- What is the effects of cutoff values on the accuracy and precision of classification methods.arrow_forwardc) Even if there is substantial uncertainty in the parameters in the EOQ-model, it is still quite a useful model. Discuss why.arrow_forwardNING SYSTEM (ACADEMIC) tory Management - Spring21 Time left 1:14:19 Alocal Omani retail store finds out the its competition is ordering 50O kgs each order of a coffee brand. Over years the local Omani store has realized that its competition has adopted an economic ordering quantity (EOQ) policy for ordering. Whereas, local Omani store has determined that it take OMR 25 to order and the annual holding cost is 25% of the price of the coffee brand. The price of the coffee brand is OMR 100 per kg. What is the annual demand for this coffee brand? Round up to the nearest integer None is correct Ob. 100,000 150,000 O d. 90,000 125.000 NEXT PAGE US PAGEarrow_forward
- Problem 7 Lynne Chappell manages the inventory of supplies in a large hospital. To determine which items should be closely monitored, Lynne decided to use the ABC classification schemeto group the items on the basis of their value. Asthe following table shows, she took a random sample of20 items and recorded the annual usage and unit cost ofeach. How should each item be classified?Inventory Item Unit cost(in U.S.dollars) AnnualUsageP21 $80 800A12 $400 70K43 $50 100S54 $60 90C25 $50 130D76 $30 170E27 $20 200F38 $300 90H19 $520 120Q10 $10 100R82 $20 80G65 $80 70L71 $220 200M94 $70 80V45 $15 60T62 $30 180I17 $20 80W22 $300 90O37 $700 85N88 $5 100arrow_forwardQ#3 · Let p + 3q/2 = 27 be an equation involving two variables p (price) and q (quantity). Indicate the meaningful domain and range of this function when (a) the price (b) the quality are considered independent variables.arrow_forwardAs with other products, Fisher-Price faces the decision of how many Weather Teddy units to order for the comingholiday season. Members of the management team suggested order quantities of 15,000, 18,000, 24,000, or28,000 units. The wide range of order quantities suggested indicates considerable disagreement concerning themarket potential. The product management team asks you for an analysis of the stock-out probabilities forvarious order quantities, an estimate of the profit potential, and to help make an order quantity recommendation.Fisher-Price expects to sell Weather Teddy for $24 based on a cost of $16 per unit. If inventory remains afterthe holiday season, Fisher-Price will sell all surplus inventory for $5 per unit. After reviewing the sales historyof similar products, Fisher-Price’s senior sales forecaster predicted an expected demand of 20,000 units with a.95 probability that demand would be between 10,000 units and 30,000 units. Compute the probability of a stock-out for the…arrow_forward
- Practical Management ScienceOperations ManagementISBN:9781337406659Author:WINSTON, Wayne L.Publisher:Cengage,Operations ManagementOperations ManagementISBN:9781259667473Author:William J StevensonPublisher:McGraw-Hill EducationOperations and Supply Chain Management (Mcgraw-hi...Operations ManagementISBN:9781259666100Author:F. Robert Jacobs, Richard B ChasePublisher:McGraw-Hill Education
- Purchasing and Supply Chain ManagementOperations ManagementISBN:9781285869681Author:Robert M. Monczka, Robert B. Handfield, Larry C. Giunipero, James L. PattersonPublisher:Cengage LearningProduction and Operations Analysis, Seventh Editi...Operations ManagementISBN:9781478623069Author:Steven Nahmias, Tava Lennon OlsenPublisher:Waveland Press, Inc.
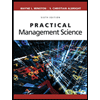
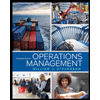
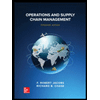
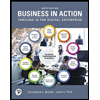
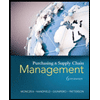
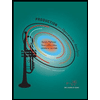