Managerial Accounting
15th Edition
ISBN: 9781337912020
Author: Carl Warren, Ph.d. Cma William B. Tayler
Publisher: South-Western College Pub
expand_more
expand_more
format_list_bulleted
Concept explainers
Textbook Question
Chapter 3, Problem 1E
Entries for materials cost flows in a
The Hershey Company manufactures chocolate confectionery products. The three largest raw materials are cocoa, sugar, and dehydrated milk. These raw materials first go into the Blending Department. The blended product is then sent to the Molding Department, where the bars of candy are formed. The candy is then sent to the Packing Department, where the bars are wrapped and boxed. The boxed candy is then sent to the distribution center, where it is eventually sold to food brokers and retailers.
Show the accounts debited and credited for each of the following business events:
- A. Materials used by the Blending Department
- B. Transfer of blended product to the Molding Department
- C. Transfer of chocolate to the Packing Department
- D. Transfer of boxed chocolate to the distribution center
- E. Sale of boxed chocolate
Expert Solution & Answer

Want to see the full answer?
Check out a sample textbook solution
Students have asked these similar questions
Liability?
Solve this question financial accounting
Production Efficiency
Chapter 3 Solutions
Managerial Accounting
Ch. 3 - Which type of cost system, process or job order,...Ch. 3 - In job order cost accounting, the three elements...Ch. 3 - In a job order cost system, direct labor and...Ch. 3 - Why is the cost per equivalent unit often...Ch. 3 - What is the purpose for determining the cost per...Ch. 3 - Rameriz Company is a process manufacturer with two...Ch. 3 - What is the most important purpose of the cost of...Ch. 3 - How are cost of production reports used for...Ch. 3 - Job order versus process costing Which of the...Ch. 3 - Kraus Steel Company has two departments, Casting...
Ch. 3 - The Rolling Department of Kraus Steel Company had...Ch. 3 - The Rolling Department of Kraus Steel Company had...Ch. 3 - The cost of direct materials transferred into the...Ch. 3 - The costs per equivalent unit of direct materials...Ch. 3 - In October, the cost of materials transferred into...Ch. 3 - Prob. 8BECh. 3 - Entries for materials cost flows in a process cost...Ch. 3 - Flowchart of accounts related to service and...Ch. 3 - Radford Inc. manufactures a sugar product by a...Ch. 3 - The cost accountant for River Rock Beverage Co....Ch. 3 - The Converting Department of Worley Company had...Ch. 3 - Data for the two departments of Kimble Pierce...Ch. 3 - The following information concerns production in...Ch. 3 - a. Based upon the data in Exercise 17-7, determine...Ch. 3 - Equivalent units of production Kellogg Company...Ch. 3 - Costs per equivalent unit Georgia Products Inc....Ch. 3 - The charges to Work in ProcessAssembly Department...Ch. 3 - a. Based on the data in Exercise 17-11, determine...Ch. 3 - Errors in equivalent unit computation Napco...Ch. 3 - Cost per equivalent unit The following information...Ch. 3 - Costs per equivalent unit and production costs...Ch. 3 - Cost of production report The debits to Work in...Ch. 3 - Cost of Production report The Cutting Department...Ch. 3 - Prob. 18ECh. 3 - Prob. 19ECh. 3 - Prob. 20ECh. 3 - The Converting Department of Tender Soft Tissue...Ch. 3 - Units of production data for the two departments...Ch. 3 - The following information concerns production in...Ch. 3 - Prob. 24ECh. 3 - The following information concerns production in...Ch. 3 - Prob. 26ECh. 3 - Prepare a cost of production report for the...Ch. 3 - Entries for process cost system Port Ormond Carpet...Ch. 3 - Cost of production report Hana Coffee Company...Ch. 3 - Equivalent units and related costs; cost of...Ch. 3 - Work in process account data for two months; cost...Ch. 3 - Sunrise Coffee Company roasts and packs coffee...Ch. 3 - Entries for process cost system Preston Grover...Ch. 3 - Cost of production report Bavarian Chocolate...Ch. 3 - Equivalent units and related costs; cost of...Ch. 3 - Work in process account data for two months; cost...Ch. 3 - Blue Ribbon Flour Company manufactures flour by a...Ch. 3 - Dura-Conduit Corporation manufactures plastic...Ch. 3 - Analyzing process cost elements across product...Ch. 3 - Analyzing process cost elements over time Pix...Ch. 3 - Determining cost relationships Midst ate...Ch. 3 - Ethics in Action You are the Cookie division...Ch. 3 - Communications Jamarcus Bradshaw, plant manager of...Ch. 3 - Accounting for materials costs In papermaking...Ch. 3 - During December, Krause Chemical Company had the...Ch. 3 - Jones Corporation uses a first-in, first-out...Ch. 3 - Kimbeth Manufacturing uses a process cost system...Ch. 3 - A company is using process costing with the...
Knowledge Booster
Learn more about
Need a deep-dive on the concept behind this application? Look no further. Learn more about this topic, accounting and related others by exploring similar questions and additional content below.Similar questions
arrow_back_ios
SEE MORE QUESTIONS
arrow_forward_ios
Recommended textbooks for you
- Managerial AccountingAccountingISBN:9781337912020Author:Carl Warren, Ph.d. Cma William B. TaylerPublisher:South-Western College PubFinancial And Managerial AccountingAccountingISBN:9781337902663Author:WARREN, Carl S.Publisher:Cengage Learning,Cornerstones of Cost Management (Cornerstones Ser...AccountingISBN:9781305970663Author:Don R. Hansen, Maryanne M. MowenPublisher:Cengage Learning
- Managerial Accounting: The Cornerstone of Busines...AccountingISBN:9781337115773Author:Maryanne M. Mowen, Don R. Hansen, Dan L. HeitgerPublisher:Cengage LearningExcel Applications for Accounting PrinciplesAccountingISBN:9781111581565Author:Gaylord N. SmithPublisher:Cengage Learning
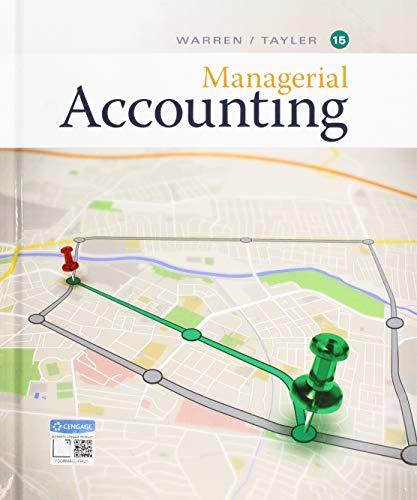
Managerial Accounting
Accounting
ISBN:9781337912020
Author:Carl Warren, Ph.d. Cma William B. Tayler
Publisher:South-Western College Pub
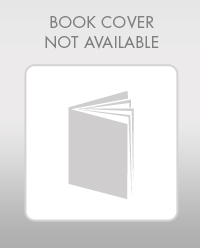
Financial And Managerial Accounting
Accounting
ISBN:9781337902663
Author:WARREN, Carl S.
Publisher:Cengage Learning,
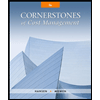
Cornerstones of Cost Management (Cornerstones Ser...
Accounting
ISBN:9781305970663
Author:Don R. Hansen, Maryanne M. Mowen
Publisher:Cengage Learning
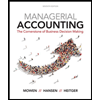
Managerial Accounting: The Cornerstone of Busines...
Accounting
ISBN:9781337115773
Author:Maryanne M. Mowen, Don R. Hansen, Dan L. Heitger
Publisher:Cengage Learning
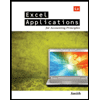
Excel Applications for Accounting Principles
Accounting
ISBN:9781111581565
Author:Gaylord N. Smith
Publisher:Cengage Learning
Cost Accounting - Definition, Purpose, Types, How it Works?; Author: WallStreetMojo;https://www.youtube.com/watch?v=AwrwUf8vYEY;License: Standard YouTube License, CC-BY