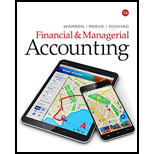
Calculate lead time
Williams Optical Inc. is considering a new lean product cell. The present manufacturing approach produces a product in four separate steps. The production batch sizes are 45 units. The process time for each step is as follows:
Process Step 1 | 5 minutes |
Process Step 2 | 8 minutes |
Process Step 3 | 4 minutes |
Process Step 4 | 3 minutes |
The time required to move each batch between steps is 5 minutes. In addition, the time to move raw materials to Process Step 1 is also 5 minutes, and the lime to move completed units from Process Step 4 to finished goods inventory is 5 minutes.
The new lean layout will allow the company to reduce the batch sizes from 45 units to 3 units. The time required to move each batch between steps and the inventory locations will be reduced to 2 minutes. The processing time in each step will stay the same.
Determine the value-added, non-value-added, and total lead times, and the value-added ratio under the (A) present and (B) proposed production approaches. (Round percentages to one decimal place.)

Trending nowThis is a popular solution!

Chapter 26 Solutions
Financial & Managerial Accounting
- SUBJECT - GENERAL ACCOUNT Department E had 4,000 units in Work in Process that were 40% completed at the beginning of the period at a cost of $14,114. Of the $14,114, $8,395 was for material and $5,719 was for conversion costs. 14,000 units of direct materials were added during the period at a cost of $25,963. 15,000 units were completed during the period, and 3,000 units were 75% completed at the end of the period. All materials are added at the beginning of the process. Direct labor was $33,809 and factory overhead was $19,934. If the average cost method is used what would be the conversion cost per unit? a. $1.91 b. $5.31 c. $3.45 d. $1.73arrow_forwardFinancial Accounting Question solve this problemarrow_forwardNeed help with this accounting questionsarrow_forward
- Managerial AccountingAccountingISBN:9781337912020Author:Carl Warren, Ph.d. Cma William B. TaylerPublisher:South-Western College PubFinancial And Managerial AccountingAccountingISBN:9781337902663Author:WARREN, Carl S.Publisher:Cengage Learning,Managerial Accounting: The Cornerstone of Busines...AccountingISBN:9781337115773Author:Maryanne M. Mowen, Don R. Hansen, Dan L. HeitgerPublisher:Cengage Learning
- Cornerstones of Cost Management (Cornerstones Ser...AccountingISBN:9781305970663Author:Don R. Hansen, Maryanne M. MowenPublisher:Cengage LearningPrinciples of Accounting Volume 2AccountingISBN:9781947172609Author:OpenStaxPublisher:OpenStax CollegeEssentials of Business Analytics (MindTap Course ...StatisticsISBN:9781305627734Author:Jeffrey D. Camm, James J. Cochran, Michael J. Fry, Jeffrey W. Ohlmann, David R. AndersonPublisher:Cengage Learning
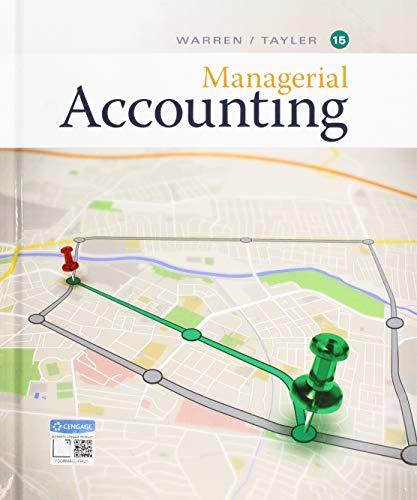
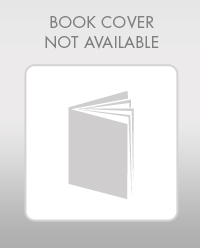
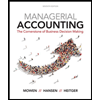
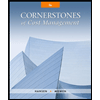
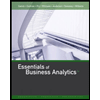