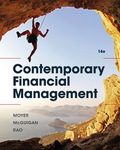
EBK CONTEMPORARY FINANCIAL MANAGEMENT
14th Edition
ISBN: 9781337514835
Author: MOYER
Publisher: CENGAGE LEARNING - CONSIGNMENT
expand_more
expand_more
format_list_bulleted
Question
Chapter 18, Problem 16P
a)
Summary Introduction
To calculate: The EOQ.
b)
Summary Introduction
To calculate: The total yearly cost of inventory for the policy.
c)
Summary Introduction
To calculate: The frequency of placing the order.
Expert Solution & Answer

Trending nowThis is a popular solution!

Students have asked these similar questions
Rho Merchandising supplies T-shirts to AK Mart. Currently, Rho orders T-shirts from various suppliers. One of the T-shirts is ordered in batches of 150 units. It has been estimated that an annual demand for T-shirts is 25,000 pieces. Furthermore, carrying cost is estimated to be P10 per T-shirt per year. Determine the ordering cost.
Chadwick Shoe Co. produces and sells an e xcellent-quality walking shoe. After production, the shoes are distributed to 20 warehouses around the country. Each warehouse services approximately 100 stores in its region. Chadwick uses an EOQ model to determine the number of pairs of shoes to order for each warehouse from the factory. Annual demand for Warehouse OR2 is approximately 120,000 pairs of shoes. The ordering cost is $250 per order. The annual carrying cost of a pair of shoes is $2.40 per pair.
Q. Although OR2’s average weekly demand is 2,500 pairs of shoes (120,000 , 12 months , 4 weeks), demand each week may vary with the following probability distribution:
Total demand for 1 week 2,000 pairs 2,250 pairs 2,500 pairs 2,750 pairs 3,000 pairs
Probability (sums to 1.00) 0.04 0.20 0.52 0.20 0.04
If a store wants shoes and OR2 has none in…
Morrison Manufacturing produces casings for sewing machines: large and small. To produce the different casings, equipment must be set up. The setup cost per production run is $18,000 for either casing. The cost of carrying small casings in inventory is $6 per casing per year; the cost of large casings is $18 per unit per year. To satisfy demand, the company produces 2,400,000 small casings and 800,000 large casings.
1. Compute the number of large casings that should be produced per setup to minimize total setup and carrying costs for this product.
2. Compute the setup, carrying, and total costs associated with the economic order quantity for the large casings.
Chapter 18 Solutions
EBK CONTEMPORARY FINANCIAL MANAGEMENT
Ch. 18 - Prob. 1QTDCh. 18 - Prob. 2QTDCh. 18 - Prob. 3QTDCh. 18 - Prob. 4QTDCh. 18 - Prob. 5QTDCh. 18 - Prob. 6QTDCh. 18 - Prob. 7QTDCh. 18 - Prob. 8QTDCh. 18 - Prob. 9QTDCh. 18 - Prob. 10QTD
Ch. 18 - Prob. 11QTDCh. 18 - Prob. 12QTDCh. 18 - Prob. 13QTDCh. 18 - Prob. 14QTDCh. 18 - Prob. 15QTDCh. 18 - Prob. 16QTDCh. 18 - Prob. 17QTDCh. 18 - Prob. 18QTDCh. 18 - Prob. 19QTDCh. 18 - Prob. 20QTDCh. 18 - Prob. 21QTDCh. 18 - Prob. 22QTDCh. 18 - Prob. 1PCh. 18 - Prob. 2PCh. 18 - Prob. 3PCh. 18 - Prob. 4PCh. 18 - Prob. 5PCh. 18 - Prob. 6PCh. 18 - Prob. 7PCh. 18 - Prob. 8PCh. 18 - Prob. 10PCh. 18 - Prob. 11PCh. 18 - Prob. 12PCh. 18 - Prob. 13PCh. 18 - Prob. 14PCh. 18 - Prob. 15PCh. 18 - Prob. 16PCh. 18 - Prob. 17PCh. 18 - Prob. 18PCh. 18 - Prob. 19PCh. 18 - Prob. 20PCh. 18 - Prob. 21P
Knowledge Booster
Similar questions
- Ingles Corporation is a manufacturer of tables sold to schools, restaurants, hotels, and other institutions. The table tops are manufactured by Ingles, but the table legs are purchased from an outside supplier. The Assembly Department takes a manufactured table top and attaches the four purchased table legs. It takes 16 minutes of labor to assemble a table. The company follows a policy of producing enough tables to ensure that 40 percent of next months sales are in the finished goods inventory. Ingles also purchases sufficient materials to ensure that materials inventory is 60 percent of the following months scheduled production. Ingless sales budget in units for the next quarter is as follows: Ingless ending inventories in units for July 31 are as follows: Required: 1. Calculate the number of tables to be produced during August. 2. Disregarding your response to Requirement 1, assume the required production units for August and September are 2,100 and 1,900, respectively, and the July 31 materials inventory is 4,000 units. Compute the number of table legs to be purchased in August. 3. Assume that Ingles Corporation will produce 2,340 units in September. How many employees will be required for the Assembly Department in September? (Fractional employees are acceptable since employees can be hired on a part-time basis. Assume a 40-hour week and a 4-week month.) (CMA adapted)arrow_forwardChadwick Shoe Co. produces and sells an e xcellent-quality walking shoe. After production, the shoes are distributed to 20 warehouses around the country. Each warehouse services approximately 100 stores in its region. Chadwick uses an EOQ model to determine the number of pairs of shoes to order for each warehouse from the factory. Annual demand for Warehouse OR2 is approximately 120,000 pairs of shoes. The ordering cost is $250 per order. The annual carrying cost of a pair of shoes is $2.40 per pair. Q. Assume each month consists of approximately 4 weeks. If it takes 1 week to receive an order, at what point should warehouse OR2 reorder shoes?arrow_forwardChadwick Shoe Co. produces and sells an e xcellent-quality walking shoe. After production, the shoes are distributed to 20 warehouses around the country. Each warehouse services approximately 100 stores in its region. Chadwick uses an EOQ model to determine the number of pairs of shoes to order for each warehouse from the factory. Annual demand for Warehouse OR2 is approximately 120,000 pairs of shoes. The ordering cost is $250 per order. The annual carrying cost of a pair of shoes is $2.40 per pair. Q. Use the EOQ model to determine the optimal number of pairs of shoes per orderarrow_forward
- Malburn Construction Ltd. Manufactures and distributes window frames. The company uses 600,000metal strips in producing the frames for the year. Each strip cost $15, the storage cost is 10% of the costprice and $180 is required to make an order.(i). Find the order size Malburn Construction needs to minimize its inventory costs. Calculate for the company:(ii). the number of orders placed per year. (iii).the length of the stock cycle in days. (iv). the annual ordering cost (v). the annual holding cost (vi). the total annual costarrow_forwardWesley Power Tools manufactures a wide variety of tools and accessories. One of its more popular items is a cordless power handisaw. Each handisaw sells for $50. Wesley expects the following unit sales: 2, 000 2, 500 3, 100 2, 900 January February March April May 2, 200 Wesley's ending finished goods inventory policy is 20 percent of the next month's sales. Each handisaw takes approximately 0.30 hours to manufacture, and Wesley pays an average labor wage of $15.00 per hour. Each handisaw requires a plastic housing that Wesley purchases from a supplier at a cost of $5.00 each. The company has an ending raw materials inventory policy of 10 percent of the following month's production requirements. Materials other than the housing unit total $4.00 per handisaw. Manufacturing overhead for this product includes $60,000 annual fixed overhead (based on production of 24,000 units) and $.80 per unit variable manufacturing overhead. Wesley's selling expenses are 5 percent of sales dollars, and…arrow_forwardRoberts Company manufactures home cleaning products. One of the products, Quickclean, requires 2 pounds of Material A and 5 pounds of Material B per unit manufactured. Material A can be purchased from the supplier for $0.30 per pound and Material B can be purchased for $0.50 per pound. The finished goods inventory on hand at the end of each month must be equal to 4,000 units plus 25% of the next month's sales. The raw materials inventory on hand at the end of each month (for either Material A or Material B) must be equal to 80% of the following month's production needs. Assume that the production budget calls for 26,000 units of Quickclean to be manufactured in June and 32,000 units of Quickclean to be manufactured in July. On May 31 there will be 41,600 pounds of Material A in inventory. The number of pounds of Material A needed for production during June would be: 61,600 51,200 35,600 52,000arrow_forward
- Roberts Company manufactures home cleaning products. One of the products, Quickclean, requires 2 pounds of Material A and 5 pounds of Material B per unit manufactured. Material A can be purchased from the supplier for $0.30 per pound and Material B can be purchased for $0.50 per pound. The finished goods inventory on hand at the end of each month must be equal to 4,000 units plus 25% of the next month's sales. The raw materials inventory on hand at the end of each month (for either Material A or Material B) must be equal to 80% of the following month's production needs. Assume that on January 1 the inventory of Quickclean was 8,000 units. Expected sales in January are 14,000 units and expected sales in February are 18,000 units. The number of units needed to be manufactured in January would be 14,500. Assume that the production budget calls for 26,000 units of Quickclean to be manufactured in June and 32,000 units of Quickclean to be manufactured in July. On May 31 there will be…arrow_forwardRoberts Company manufactures home cleaning products. One of the products, Quickclean, requires 2 pounds of Material A and 5 pounds of Material B per unit manufactured. Material A can be purchased from the supplier for $0.30 per pound and Material B can be purchased for $0.50 per pound. The finished goods inventory on hand at the end of each month must be equal to 4,000 units plus 25% of the next month's sales. The raw materials inventory on hand at the end of each month (for either Material A or Material B) must be equal to 80% of the following month's production needs. Assume that on January 1 the inventory of Quickclean was 8,000 units. Expected sales in January are 14,000 units and expected sales in February are 18,000 units. The number of units needed to be manufactured in January would be: A. 10,500 B. 14,000 C. 14,500 D. 15,000arrow_forwardJack’s Tracks sells 24,000 custom-designed GoKarts per year. These GoKarts are sold evenly throughout the year. The manufacturer charges Jack a $50 processing cost per order, and Jack incurs a carrying cost of $240 per year including storing each GoKart at a local warehouse. What is the economic order quantity for ordering materials?a. 100b. 1,000c. 2,000d. 10,000arrow_forward
- Crede Inc. has two divisions. Division A makes and sells student desks. Division B manufactures and sells reading lamps. Each desk has a reading lamp as one of its components. Division A can purchase reading lamps at a cost of $10.10 from an outside vendor. Division A needs 11,100 lamps for the coming year. Division B has the capacity to manufacture 49,600 lamps annually. Sales to outside customers are estimated at 38,500 lamps for the next year. Reading lamps are sold at $12.09 each. Variable costs are $6.87 per lamp and include $1.41 of variable sales costs that are not incurred if lamps are sold internally to Division A. The total amount of fixed costs for Division B is $75,900. Consider the following independent situations. What should be the minimum transfer price accepted by Division B for the 11,100 lamps and the maximum transfer price paid by Division A? (Round answers to 2 decimal places, e.g. 15.25.) Per unit Minimum transfer price accepted by Division B $_ Maximum transfer…arrow_forwardFlounder Inc. has two divisions. Division A makes and sells student desks. Division B manufactures and sells reading lamps. Each desk has a reading lamp as one of its components. Division A can purchase reading lamps at a cost of $10 from an outside vendor. Division A needs 9,000 lamps for the coming year. Division B has the capacity to manufacture 45,000 lamps annually. Sales to outside customers are estimated at 36,000 lamps for the next year. Reading lamps are sold at $12 each. Variable costs are $7 per lamp and include $2 of variable sales costs that are not incurred if lamps are sold internally to Division A. The total amount of fixed costs for Division B is $72,000. Consider the following independent situations.arrow_forwardIguana, Incorporated, manufactures bamboo picture frames that sell for $20 each. Each frame requires 4 linear feet of bamboo, which costs $1.50 per foot. Each frame takes approximately 30 minutes to build, and the labor rate averages $13 per hour. Iguana has the following inventory policies: Ending finished goods inventory should be 40 percent of next month's sales. • Ending direct materials inventory should be 30 percent of next month's production. Expected unit sales (frames) for the upcoming months follow: March April May June July August 325 350 400 500 475 525 Variable manufacturing overhead is incurred at a rate of $0.30 per unit produced. Annual fixed manufacturing overhead is estimated to be $6,000 ($500 per month) for expected production of 5,000 units for the year. Selling and administrative expenses are estimated at $550 per month plus $0.60 per unit sold. Iguana, Incorporated, had $12,000 cash on hand on April 1. Of its sales, 80 percent is in cash. Of the credit sales, 50…arrow_forward
arrow_back_ios
SEE MORE QUESTIONS
arrow_forward_ios
Recommended textbooks for you
- EBK CONTEMPORARY FINANCIAL MANAGEMENTFinanceISBN:9781337514835Author:MOYERPublisher:CENGAGE LEARNING - CONSIGNMENTCornerstones of Cost Management (Cornerstones Ser...AccountingISBN:9781305970663Author:Don R. Hansen, Maryanne M. MowenPublisher:Cengage Learning
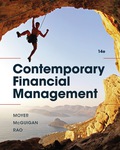
EBK CONTEMPORARY FINANCIAL MANAGEMENT
Finance
ISBN:9781337514835
Author:MOYER
Publisher:CENGAGE LEARNING - CONSIGNMENT
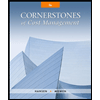
Cornerstones of Cost Management (Cornerstones Ser...
Accounting
ISBN:9781305970663
Author:Don R. Hansen, Maryanne M. Mowen
Publisher:Cengage Learning