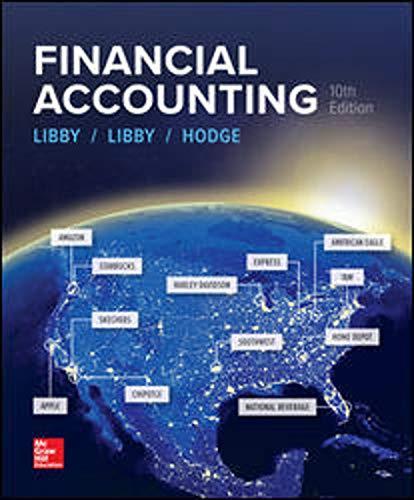
Concept explainers
Equivalent Units and Related Costs; Cost of Production Report; Entries
Dover Chemical Company manufactures specialty chemicals by a series of three processes, all materials being introduced in the Distilling Department. From the Distilling Department, the materials pass through the Reaction and Filling departments, emerging as finished chemicals.
The balance in the account Work in Process—Filling was as follows on January 1:
Work in Process—Filling Department | ||
(3,100 units, 60% completed): | ||
Direct materials (3,100 x $18.1) | $56,110 | |
Conversion (3,100 x 60% x $11.7) | 21,762 | |
$77,872 |
The following costs were charged to Work in Process—Filling during January:
Direct materials transferred from Reaction | ||
Department: 40,000 units at $17.8 a unit | $712,000 | |
Direct labor | 250,310 | |
Factory |
240,490 |
During January, 39,700 units of specialty chemicals were completed. Work in Process—Filling Department on January 31 was 3,400 units, 90% completed.
Required:
1. Prepare a cost of production report for the Filling Department for January. If an amount is zero, enter "0". If required, round your cost per equivalent unit answers to two decimal places.

Trending nowThis is a popular solution!
Step by stepSolved in 2 steps

- White Diamond Flour Company manufactures flour by a series of three processes, beginning with wheat grain being introduced in the Milling Department. From the Milling Department, the materials pass through the Sifting and Packaging departments, emerging as packaged refined flour. The balance in the account Work in Process-Sifting Department was as follows on July 1: Work in Process-Sifting Department (800 units, 3/5 completed): Direct materials (800 × $2.25) $1,800 Conversion (800 × 3/5 × $0.40) 192 $1,992 The following costs were charged to Work in Process-Sifting Department during July: Direct materials transferred from Milling Department: 16,400 units at $2.35 a unit $38,540 Direct labor 4,480 Factory overhead 2,945 During July, 16,100 units of flour were completed. Work in Process-Sifting Department on July 31 was 1,100 units, 4/5 completed. Required: 1. Prepare a cost of production report for the Sifting Department for July. If an…arrow_forwardWhite Diamond Flour Company manufactures flour by a series of three processes, beginning with wheat grain being introduced in the Milling Department. From the Milling Department, the materials pass through the Sifting and Packaging departments, emerging as packaged refined flour.The balance in the account Work in Process—Sifting Department was as follows on July 1: Attachment During July, 15,500 units of flour were completed. Work in Process—Sifting Department on July 31 was 1,100 units, 4⁄5 completed.Instructions1. Prepare a cost of production report for the Sifting Department for July.2. Journalize the entries for costs transferred from Milling to Sifting and the costs transferred from Sifting to Packaging.3. Determine the increase or decrease in the cost per equivalent unit from June to July for direct materials and conversion costs.4. Discuss the uses of the cost of production report and the results of part (3).arrow_forwardInstructions Radford Inc. manufactures a sugar product by a continuous process, involving three production departments-Refining, Dining, and Packing. Assume that records indicate that direct materials, direct labor, and applied factory overhead for the first department, Refining, were $371,000, $142,000, and $98,400, respectively. Also, work in process in the Refining Department at the beginning of the period totaled $29.200, and work in process at the end of the period totaled $28.400 Required: a (1) On September 30, journalize the entry to record the flow of costs into the Refining Department during the period for direct materials (2) a) On September 30, joumalize the entry to record the flow of costs into the Refining Department during the period for direct labor." On September 30, joumalize the entry to record the flow of costs into the Refining Department during the period for factory overhead b. On September 30, joumalize the entry to record the transfer of production costs to…arrow_forward
- a. Determine the number of units transferred to the next department. b. Determine the costs per equivalent unit of direct materials and conversion. If required, round your answer to two decimal places. Cost per equivalent unit of direct materials Cost per equivalent unit of direct materials c. Determine the cost of units started and completed in November.arrow_forwardUnits of production data for the two departments of Pacific Cable and Wire Company for November of the current fiscal year are as follows: Drawing Department Winding Department 5,700 units, 35% completed 1,700 units, 90% completed Work in process, November 1 Completed and transferred to next processing department during November Work in process, November 30 4,300 units, 60% completed 2,300 units, 20% completed a. If all direct materials are placed in process at the beginning of production, determine the direct materials and conversion equivalent units of production for November for the Drawing Department. If an amount is zero, enter in "0". Drawing Department Direct Materials and Conversion Equivalent Units of Production For November Inventory in process, November 1 Started and completed in November Transferred to Winding Department in November Inventory in process, November 30 Total 78,100 units Inventory in process, November 1 Started and completed in November Transferred to finished…arrow_forwardEntries for Flow of Factory Costs for Process Costing Keoni Inc. manufactures a sugar product by a continuous process, involving three production departments-Refining, Sifting, and Packing. Assume that records indicate that direct materials, direct labor, and applied factory overhead for the first department, Refining, were $522,500, $182,900, and $120,200, respectively. Also, work in process in the Refining Department at the beginning of the period totaled $29,300, and work in process at the end of the period totaled $36,100. a. Journalize the entries to record the flow of costs into the Refining Department during the period for (1) direct materials, (2) direct labor, and (3) factory overhead. If an amount box does not require an entry, leave it blank. 1. 2. 3. b. Journalize the entry to record the transfer of production costs to the second department, Sifting. If an amount box does not require an entry, leave it blank.arrow_forward
- White Diamond Flour Company manufactures flour by a series of three processes, beginning with wheat grain being introduced in the Milling Department. From the Milling Department, the materials pass through the Sifting and Packaging departments, emerging as packaged refined flour. The balance in the account Work in Process—Sifting Department was as follows on July 1:Work in Process—Sifting Department (900 units, 3/5 completed) on July 1Cost Source Dollar AmountDirect Materials (900 x $3.15) $2,835Conversion (900 x 3/5 x $0.30) 162Total Materials and Conversion 2,997The following costs were charged to Work in Process—Sifting Department during July:Work in Process—Sifting DepartmentCost Source Dollar AmountDirect materials transferred from Milling Department: 15,700 units at $2.30 a unit $36,110Direct Labor 5,420Factory Overhead 2,384During July, 15,500 units of flour were completed. Work in Process—Sifting Department on July 31 was 1,100 units, 4/5 completed.Instructionsa. Prepare a cost…arrow_forwardEntries for Flow of Factory Costs for Process Cost System Radford Inc. manufactures a sugar product by a continuous process, involving three production departments-Refining, Sifting, and Packing. Assume that records indicate that direct materials, direct labor, and applied factory overhead for the first department, Refining, were $527,700, $184,700, and $121,400, respectively. Also, work in process in the Refining Department at the beginning of the period totaled $29,600, and work in process at the end of the period totaled $36,400. a. Journalize the entries to record the flow of costs into the Refining Department during the period for (1) direct materials, (2) direct labor, and (3) factory overhead. If an amount box does not require an entry, leave it blank. 1. Work in Process-Refining Department. ✓ 284,500 X Materials 2. Work in Process-Refining Department Wages Payable Feedback ✓ 3. Work in Process-Refining Department -✓ Factory Overhead-Refining Department Feedback ✓ - ✓ Feedback…arrow_forwardEntries for Flow of Factory Costs for Process Cost System Radford Inc. manufactures a sugar product by a continuous process, involving three production departments-Refining, Sifting, and Packing. Assume that records indicate that direct materials, direct labor, and applied factory overhead for the first department, Refining, were $605,000, $211,800, and $139,200, respectively. Also, work in process in the Refining Department at the beginning of the period totaled $33,900, and work in process at the end of the period totaled $41,700. a. Journalize the entries to record the flow of costs into the Refining Department during the period for (1) direct materials, (2) direct labor, and (3) factory overhead. If an amount box does not require an entry, leave it blank. 1. 2. 3. b. Journalize the entry to record the transfer of production costs to the second department, Sifting. If an amount box does not require an entry, leave it blank.arrow_forward
- At Greytown Company, materials are entered at the beginning of each process. Work in process inventories, with the percentage of work done on conversion, and production data for its Painting Department in selected months are as follows: Beginning Work In Process Ending Work In Process Percentage Units Completed Percentage Month Units Completed and Transferred Out Units Completed July -0- — 11,000 1,500 90% Sept. 2,500 20% 9,000 5,000 70% Instructions Compute the equivalent units of production for materials and conversion costs for September.arrow_forwardThe following information summarizes the activities in the Mixing Department for the month of March. Beginning inventory 8,000 units, 80% complete Started and completed 196,000 units Ending inventory 24,000 units, 25% complete Material is added at the beginning of the process, and conversion costs are incurred evenly throughout the process. Calculate the equivalent units of production with respect to materials during the month of March using the weighted average method. Select one: a. 228,000 b. 212,000 c. 208,000 d. 244,000 e. 210,000arrow_forwardEquivalent Units of Production Data for the two departments of Kimble & Pierce Company for June of the current fiscal year are as follows: Winding Department Drawing Department 6,100 units, 30% completed 3,000 units, 90% completed Work in process, June 1 Completed and transferred to next processing department during June Work in process, June 30 4,600 units, 55% completed Production begins in the Drawing Department and finishes in the Winding Department. Inventory in process, June 1 Started and completed in June Transferred to Winding Department in June Inventory in process, June 30 Total a. If all direct materials are placed in process at the beginning of production, determine the direct materials and conversion equivalent units of production for June for the Drawing Department. If an amount is zero, enter in "0". Drawing Department Direct Materials and Conversion Equivalent Units of Production For June Feedback 83,600 units Inventory in process, June 1 Started and completed in June…arrow_forward
- AccountingAccountingISBN:9781337272094Author:WARREN, Carl S., Reeve, James M., Duchac, Jonathan E.Publisher:Cengage Learning,Accounting Information SystemsAccountingISBN:9781337619202Author:Hall, James A.Publisher:Cengage Learning,
- Horngren's Cost Accounting: A Managerial Emphasis...AccountingISBN:9780134475585Author:Srikant M. Datar, Madhav V. RajanPublisher:PEARSONIntermediate AccountingAccountingISBN:9781259722660Author:J. David Spiceland, Mark W. Nelson, Wayne M ThomasPublisher:McGraw-Hill EducationFinancial and Managerial AccountingAccountingISBN:9781259726705Author:John J Wild, Ken W. Shaw, Barbara Chiappetta Fundamental Accounting PrinciplesPublisher:McGraw-Hill Education
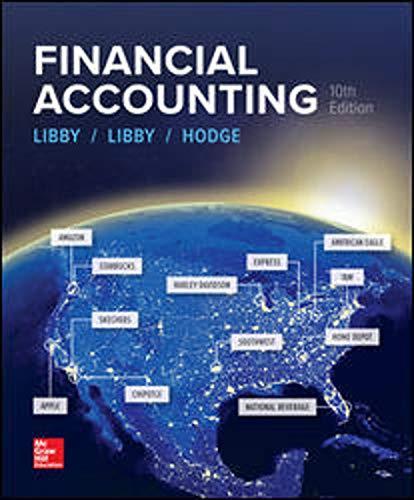
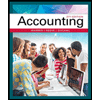
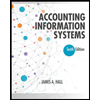
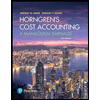
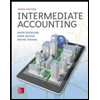
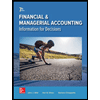