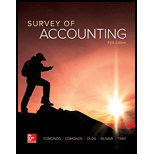
Survey Of Accounting
5th Edition
ISBN: 9781259631122
Author: Edmonds, Thomas P.
Publisher: Mcgraw-hill Education,
expand_more
expand_more
format_list_bulleted
Question
Chapter 12, Problem 8E
To determine
The correct cost driver for every overhead costs and identify the overall cost of each house.
Expert Solution & Answer

Want to see the full answer?
Check out a sample textbook solution
Students have asked these similar questions
Spree Party Lights overhead expenses are:
Indirect material, pounds per unit
0.30
Indirect material, cost per pound
$2
Indirect labor hours
1
Indirect labor rate per hour
$16.50
Variable maintenance per unit
$0.75
Variable utilities per unit
$0.20
Supervisor salaries
$11,000
Maintenance salaries
$9,000
Insurance
$3,000
Depreciation
$1,600
Prepare a manufacturing overhead budget if the number of units to produce for January, February, and March are 2,400, 3,100, and 2,800, respectively.
Spree Party LightsManufacturing Overhead BudgetFor the Quarter Ending January - March
January
February
March
Units to Produce
fill in the blank 1
fill in the blank 2
fill in the blank 3
Variable Costs
$- Select -
$- Select -
$- Select -
- Select -
- Select -
- Select -
- Select -
- Select -
- Select -
- Select -
- Select -
- Select -
Total Variable Manufacturing Costs
$fill in the blank 20
$fill in the blank 21
$fill in the blank 22…
Spree Party Lights overhead expenses are:
Indirect material, pounds per unit
0.25
Indirect material, cost per pound
$2
Indirect labor hours
1
Indirect labor rate per hour
$16.00
Variable maintenance per unit
$0.70
Variable utilities per unit
$0.20
Supervisor salaries
$10,000
Maintenance salaries
$9,000
Insurance
$4,000
Depreciation
$1,500
Prepare a manufacturing overhead budget if the number of units to produce for January, February, and March are 2,400, 2,900, and 2,700, respectively.
Spree Party Lights
Manufacturing Overhead Budget
For the Quarter Ending January - March
January
February
March
Units to Produce
fill in the blank 1
fill in the blank 2
fill in the blank 3
Variable Costs
Indirect Material
$fill in the blank 5
$fill in the blank 6
$fill in the blank 7
Indirect Labor
fill in the blank 9
fill in the blank 10
fill in the blank 11
Maintenance
fill in the blank 13
fill in the blank 14
fill in the blank 15
Utilities…
Single Plantwide Factory Overhead Rate
Scrumptious Snacks Inc. manufactures three types of snack foods: tortilla chips,
potato chips, and pretzels. The company has budgeted the following costs for the
upcoming period:
Factory depreciation
Indirect labor
Factory electricity
Indirect materials
Selling expenses
Administrative expenses
Total costs
Factory overhead is allocated to the three products on the basis of processing hours.
The products had the following production budget and processing hours per case:
Budgeted Volume
(Cases)
$9,442
23,400
2,668
5,542
13,137
7,389
$61,578
Tortilla chips
Potato chips
Pretzels
3,900
2,100
1,500
7,500
If required, round all per-case answers to the nearest cent.
Total
Processing Hours
Per Case
0.12
0.15
0.10
a. Determine the single plantwide factory overhead rate.
per processing hour
Chapter 12 Solutions
Survey Of Accounting
Ch. 12 - 1.What is a cost object? Identify four different...Ch. 12 - Prob. 2QCh. 12 - 3.If the cost object is a manufactured product,...Ch. 12 - Prob. 4QCh. 12 - Prob. 5QCh. 12 - Prob. 6QCh. 12 - Prob. 7QCh. 12 - Prob. 8QCh. 12 - Prob. 9QCh. 12 - 10.Why are some manufacturing costs not directly...
Ch. 12 - Prob. 11QCh. 12 - 12.On January 31, the managers of Integra, Inc....Ch. 12 - 13.Respond to the following statement: The...Ch. 12 - Prob. 14QCh. 12 - Define the term cost pool. How are cost pools...Ch. 12 - LO 4-1Exercise 4-1A Direct versus indirect costs...Ch. 12 - Prob. 2ECh. 12 - Prob. 3ECh. 12 - Exercise 4-4APooling overhead cost Ware...Ch. 12 - Prob. 5ECh. 12 - Exercise 4-5A Allocating overhead cost among...Ch. 12 - Prob. 7ECh. 12 - Prob. 8ECh. 12 - Exercise 4-6AAllocating overhead costs among...Ch. 12 - Exercise 4-9AAllocating to solve a timing problem...Ch. 12 - Prob. 11ECh. 12 - Exercise 4-11AHow the allocation of fixed cost...Ch. 12 - Prob. 13ECh. 12 - Problem 4-17A Cost accumulation and allocation...Ch. 12 - Problem 4-18A Selecting an appropriate cost driver...Ch. 12 - Problem 4-19A Cost allocation in a service...Ch. 12 - Prob. 17PCh. 12 - Problem 4-21A Allocation to accomplish smoothing...Ch. 12 - Problem 4-22A Allocating indirect costs between...Ch. 12 - Prob. 20PCh. 12 - Prob. 1ATCCh. 12 - Prob. 2ATCCh. 12 - ATC 4-3 Research Assignment Using real-world data...Ch. 12 - Prob. 4ATCCh. 12 - Prob. 5ATC
Knowledge Booster
Learn more about
Need a deep-dive on the concept behind this application? Look no further. Learn more about this topic, accounting and related others by exploring similar questions and additional content below.Similar questions
- Multiple production department factory overhead rates The total factory overhead for Bardot Marine Company is budgeted for the year at 600,000 divided into two departments: Fabrication, 420,000, and Assembly, 180,000. Bardot Marine manufactures two types of boats: speedboats and bass boats. The speedboats require 8 direct labor hours in Fabrication and 4 direct labor hours in Assembly. The bass boats require 4 direct labor hours in Fabrication and 8 direct labor hours in Assembly. Each product is budgeted for 250 units of production for the year. Determine (A) the total number of budgeted direct labor hours for the year in each department, (B) the departmental factory overhead rates for both departments, and (C) the factory overhead allocated per unit for each product using the department factory overhead allocation rates.arrow_forwardUse the following information for Exercises 9-63 and 9-64: Palladium Inc. produces a variety of household cleaning products. Palladiums controller has developed standard costs for the following four overhead items: Next year, Palladium expects production to require 90,000 direct labor hours. Exercise 9-64 Performance Report Based on Actual Production Refer to the information for Palladium Inc. above. Assume that actual production required 93,000 direct labor hours at standard. The actual overhead costs incurred were as follows: Required: Prepare a performance report for the period based on actual production.arrow_forwardVariable costs and activity bases in decision making The owner of Dawg Prints, a printing company, is planning direct labor needs for the upcoming year. The owner has provided you with the following information for next year's plans: Each color on the banner must be printed one at a time. Thus, for example, a four-color banner will need to be run through the printing operation four separate times. The total production volume last year was 600 banners, as shown below. The four-color banner is a new product offering for the upcoming year. The owner believes that the expected 600-unit increase in volume from last year means that direct labor expenses should increase by 100% (600 + 600). What do you think?arrow_forward
- Factory overhead rate Fabricator Inc., a specialized equipment manufacturer, uses a job order cost system. The overhead is allocated to jobs on the basis of direct labor hours. The overhead rate is now $3,000 per direct labor hour. The design engineer thinks that this is illogical. The design engineer has stated the following: Our accounting system doesn't make any sense to me. It tells me that every labor hour carries an additional burden of $3,000. This means that while direct labor makes up only 5% of our total product cost, it drives all our costs. In addition, these rates give my design engineers incentives to "design out" direct labor by using machine technology. Yet, over the past years as we have had less and less direct labor, the overhead rate keeps going up and up. I won't be surprised if next year the rate is $4,000 per direct labor hour. I'm also concerned because small errors in our estimates of the direct labor content can have a large impact on our estimated costs. Just a 30~minute error in our estimate of assembly time is worth $ 1,500. Small mistakes in our direct labor time estimates really swing our bids around. I think this puts us at a disadvantage when we are going after business. What do you think is a possible solution?arrow_forwardFactory overhead rate Fabricator Inc., a specialized equipment manufacturer, uses a job order cost system. The overhead is allocated to jobs on the basis of direct labor hours. The overhead rate is now $3,000 per direct labor hour. The design engineer thinks that this is illogical. The design engineer has stated the following: Our accounting system doesn't make any sense to me. It tells me that every labor hour carries an additional burden of $3,000. This means that while direct labor makes up only 5% of our total product cost, it drives all our costs. In addition, these rates give my design engineers incentives to "design out" direct labor by using machine technology. Yet, over the past years as we have had less and less direct labor, the overhead rate keeps going up and up. I won't be surprised if next year the rate is $4,000 per direct labor hour. I'm also concerned because small errors in our estimates of the direct labor content can have a large impact on our estimated costs. Just a 30~minute error in our estimate of assembly time is worth $ 1,500. Small mistakes in our direct labor time estimates really swing our bids around. I think this puts us at a disadvantage when we are going after business. What did the engineer mean about the large overhead rate being a disadvantage when plating bids and seeking new business?arrow_forwardHart Manufacturing makes three products. Each product requires manufacturing operations in three departments: A, B, and C. The labor-hour requirements, by department, are as follows: During the next production period the labor-hours available are 450 in department A, 350 in department B, and 50 in department C. The profit contributions per unit are 25 for product 1, 28 for product 2, and 30 for product 3. a. Formulate a linear programming model for maximizing total profit contribution. b. Solve the linear program formulated in part (a). How much of each product should be produced, and what is the projected total profit contribution? c. After evaluating the solution obtained in part (b), one of the production supervisors noted that production setup costs had not been taken into account. She noted that setup costs are 400 for product 1, 550 for product 2, and 600 for product 3. If the solution developed in part (b) is to be used, what is the total profit contribution after taking into account the setup costs? d. Management realized that the optimal product mix, taking setup costs into account, might be different from the one recommended in part (b). Formulate a mixed-integer linear program that takes setup costs provided in part (c) into account. Management also stated that we should not consider making more than 175 units of product 1, 150 units of product 2, or 140 units of product 3. e. Solve the mixed-integer linear program formulated in part (d). How much of each product should be produced and what is the projected total profit contribution? Compare this profit contribution to that obtained in part (c).arrow_forward
- Factory overhead cost budget Nutty Candy Company budgeted the following costs for anticipated production for August: Prepare a factory overhead cost budget, separating variable and fixed costs. Assume that factory insurance and depreciation are the only factory fixed costs.arrow_forwardSingle Plantwide factory Overhead Rate Scrumptious Snacks Inc. manufactures three types of snack foods: tortilla chips, potato chips, and pretzels. The company has budgeted the following costs for the upcoming period: Factory depreciation Indirect labor $20,770 51,474 Factory electricity Indirect materials Selling expenses Administrative expenses Total costs 5,870 12,192 28,898 16,255 $135,459 Factory overhead is allocated to the three products on the basis of processing hours. The products had the following production budget and processing hours per case: Budgeted Volume Processing Hours (Cases) Per Case Tortilla chips 5,100 0.12 Potato chips 3,300 0.15 Pretzels 4,500 0.10 Total 12,900 If required, round all per-case answers to the nearest cent. a. Determine the single plantwide factory overhead rate. $ ✗ per processing hour b. Use the overhead rate in (a) to determine the amount of total and per-case overhead allocated to each of the three products under generally accepted accounting…arrow_forwardsingle Plantwide Factory Overhead Rate Salty Sensations Snacks Company manufactures three types of snack foods: tortita chips, potato chips, and pretzels. The company has budgeted the following costs for the upcoming period: Factory depreciation Indirect labor Factory electricity tndirect materials selling expenses Administrative expenses Total costs $31,360 78,400 7,840 35,400 25,000 18,000 $196,000 Factory overhead is allocated to the three products on the basis of processing hours. The products had the following production budget and processing hours per case: If required, round all per unit ansyers to the nearest cent. a. Determine the single plantwide factory overhead rate. x per processing hour b. Use the factory overhead rate in (a) to determine the amount of total and per-case factory overhead allocated to each of the three products under generally accepted accounting principles. Total Per Casearrow_forward
arrow_back_ios
arrow_forward_ios
Recommended textbooks for you
- Survey of Accounting (Accounting I)AccountingISBN:9781305961883Author:Carl WarrenPublisher:Cengage LearningManagerial Accounting: The Cornerstone of Busines...AccountingISBN:9781337115773Author:Maryanne M. Mowen, Don R. Hansen, Dan L. HeitgerPublisher:Cengage LearningManagerial AccountingAccountingISBN:9781337912020Author:Carl Warren, Ph.d. Cma William B. TaylerPublisher:South-Western College Pub
- Principles of Cost AccountingAccountingISBN:9781305087408Author:Edward J. Vanderbeck, Maria R. MitchellPublisher:Cengage LearningEssentials of Business Analytics (MindTap Course ...StatisticsISBN:9781305627734Author:Jeffrey D. Camm, James J. Cochran, Michael J. Fry, Jeffrey W. Ohlmann, David R. AndersonPublisher:Cengage Learning
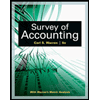
Survey of Accounting (Accounting I)
Accounting
ISBN:9781305961883
Author:Carl Warren
Publisher:Cengage Learning
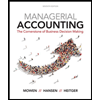
Managerial Accounting: The Cornerstone of Busines...
Accounting
ISBN:9781337115773
Author:Maryanne M. Mowen, Don R. Hansen, Dan L. Heitger
Publisher:Cengage Learning
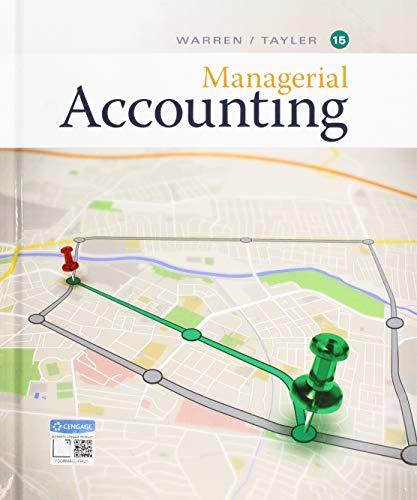
Managerial Accounting
Accounting
ISBN:9781337912020
Author:Carl Warren, Ph.d. Cma William B. Tayler
Publisher:South-Western College Pub
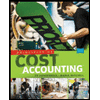
Principles of Cost Accounting
Accounting
ISBN:9781305087408
Author:Edward J. Vanderbeck, Maria R. Mitchell
Publisher:Cengage Learning
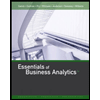
Essentials of Business Analytics (MindTap Course ...
Statistics
ISBN:9781305627734
Author:Jeffrey D. Camm, James J. Cochran, Michael J. Fry, Jeffrey W. Ohlmann, David R. Anderson
Publisher:Cengage Learning
Incremental Analysis - Sell or Process Further; Author: Melissa Shirah;https://www.youtube.com/watch?v=7D6QnBt5KPk;License: Standard Youtube License