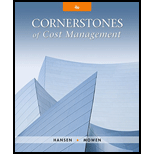
Baker, Inc., supplies wheels for a large bicycle manufacturing company. The bicycle company has recently requested that Baker decrease its delivery time. Baker made a commitment to reduce the lead time for delivery from seven days to one day. To help achieve this goal, engineering and production workers had made the commitment to reduce time for the setup activity (other activities such as moving materials and rework were also being examined simultaneously). Current setup times were 12 hours. Setup cost was $600 per setup hour. For the first quarter, engineering developed a new process design that it believed would reduce the setup time from 12 hours to nine hours. After implementing the design, the actual setup time dropped from 12 hours to seven hours. Engineering believed the actual reduction was sustainable. In the second quarter, production workers suggested a new setup procedure. Engineering gave the suggestion a positive evaluation, and they projected that the new approach would save an additional six hours of setup time. Setup labor was trained to perform the new setup procedures. The actual reduction in setup time based on the suggested changes was four hours.
Required:
- 1. What kaizen setup standard would be used at the beginning of each quarter?
- 2. Describe the kaizen subcycle using the two quarters of data provided by Baker.
- 3. Describe the maintenance subcycle for setups using the two quarters of data provided by Baker.
- 4. How much non-value-added cost was eliminated by the end of two quarters? Discuss the role of kaizen costing in activity-based management.
- 5. Explain why kaizen costing is compatible with activity-based responsibility accounting while
standard costing is compatible with financial-based responsibility accounting.

Trending nowThis is a popular solution!

Chapter 12 Solutions
Cornerstones of Cost Management (Cornerstones Series)
- Can you show me how to solve all the missing partsarrow_forwardComputer World, Inc. manufactures computer parts and keyboards. The annual production and sales of computer parts is 1,000 units, while 1,200 keyboards are produced and sold. The company has traditionally used direct labor hours to allocate its overhead to products. Computer parts require 3 direct labor hours per unit, while keyboards require 2.5 direct labor hours per unit. The total estimated overhead for the period is $114,000. The company is looking at the possibility of changing to an activity-based costing system for its products. What is the predetermined overhead allocation rate using the traditional costing system?arrow_forwardThe Decker Company maintains a fleet of 10 service trucks and crews that provide a variety of plumbing, heating, and cooling repair services to residential customers. Currently, it takes on average about six hours before a service team responds to a service request. Each truck and crew averages 12 service calls per week, and the average revenue earned per service call is $150. Each truck is in service 50 weeks per year. Owing to the diffi culty in scheduling and routing, there is considerable slack time for each truck and crew during a typical week. In an effort to more efficiently schedule the trucks and crews and improve their productivity, Decker management is evaluating the purchase of a prewritten routing and scheduling soft ware package. The benefits of the system will include reduced response time to service requests and more productive service teams, but management is having trouble quantifying these benefits. One approach is to make an estimate of how much service response…arrow_forward
- Marwick Innovations, Inc. produces exercise and fitness gear. Two of its newer products require a finishing process that can only be completed on machines that were recently purchased for this purpose. The machines have a maximum capacity of 10,500 machine hours, and no other products that the company makes use these machines.Sarah Jacob, the company’s operations manager, is preparing the production schedule for the coming month and can’t seem to find enough machine time to produce enough units to meet the customer demand that the marketing department has included in the sales budget.Michael Stoner, the company’s controller, has gathered the following information about the two products: DumbbellRack WeightBench Selling price per unit $50 $60 Direct materials 20 12 Direct labor 6 12 Variable overhead 3 6 Fixed overhead 5 10 Profit per unit $16 $20 Unit sales demand 5,000…arrow_forwardHagerty, Inc. a manufacturer of computer diskettes, currently uses a conventional process cost system. During February, Hagerty plans to purchase P 50,000 of raw materials. Of this amount 80% will be used for current production, while the remainder will serve as a buffer in inventory. Direct labor cost is expected to be P 10,000 During February, and the actual factory overhead is anticipated to total P 65,000. Paul William, the owner, has been considering the use of a JIT inventory system. If implemented at the beginning of February, only the materials needed for current production would be purchased. Requirements: Using T-accounts, enter the February transactions for the purchase and usage of materials under: a) Conventional Costing b) JIT Costing Using T-accounts, enter the February transactions for the labor and overhead costs under: a) Conventional Costing b) JIT Costing Do not record the entry for applied overhead.arrow_forwardRico Company produces custom-made machine parts. Rico recently has implemented an activity-based management (ABM) system with the objective of reducing costs. Rico has begun analyzing each activity to determine ways to increase its efficiency. Setting up equipment was among the first group of activities to be carefully studied. The study revealed that setup hours was a good driver for the activity. During the last year, the company incurred fixed setup costs of $860,200 (salaries of 17 employees). The fixed costs provide a capacity of 39,100 hours (2,300 per employee at practical capacity). The setup activity was viewed as necessary, and the value- added standard was set at 2,300 hours. Actual setup hours used in the most recent period were 37,110. Required: 1. Calculate the volume and unused capacity variances for the setup activity. Enter all amounts as positive values. Volume Variance 22 Unused Capacity Variance $ Show Me How 2. Prepare a report that presents value-added, non varue…arrow_forward
- Carla Vista Innovations, Inc. produces exercise and fitness gear. Two of its newer products require a finishing process that can only be completed on machines that were recently purchased for this purpose. The machines have a maximum capacity of 10,500 machine hours, and no other products that the company makes use these machines. Sarah Jacob, the company's operations manager, is preparing the production schedule for the coming month and can't seem to find enough machine time to produce enough units to meet the customer demand that the marketing department has included in the sales budget. Michael Stoner, the company's controller, has gathered the following information about the two products: Dumbbell Weight Rack Bench Selling price per unit $44 $60 Direct materials 19 16 Direct labor 4 8 Variable overhead 3 6 Fixed overhead 5 10 Profit per unit $13 $20 Unit sales demand 5,000 8,000 Machine hours per unit 0.75 1.5 LOarrow_forwardCarla Vista Innovations, Inc. produces exercise and fitness gear. Two of its newer products require a finishing process that can only be completed on machines that were recently purchased for this purpose. The machines have a maximum capacity of 10,500 machine hours, and no other products that the company makes use these machines. Sarah Jacob, the company's operations manager, is preparing the production schedule for the coming month and can't seem to find enough machine time to produce enough units to meet the customer demand that the marketing department has included in the sales budget. Michael Stoner, the company's controller, has gathered the following information about the two products: Dumbbell Weight Rack Bench Selling price per unit $44 $60 Direct materials 19 16 Direct labor 4 8 Variable overhead 3 6 Fixed overhead 10 Profit per unit $13 $20 Unit sales demand 5,000 8,000 Machine hours per unit 0.75 1.5arrow_forwardErie Company manufactures a small CD player called the Jogging Mate. The company uses stan- dards to control its costs. The labor standards that have been set for one Jogging Mate CD player are as follows: Standard Standard Rate Standard Hours per Hour Cost 18 minutes $12.00 $3.60 During August, 5,750 hours of direct labor time were needed to make 20,000 units of the Jogging Mate. The direct labor cost totaled $73,600 for the month. Required: 1. What direct labor cost should have been incurred to make 20,000 units of the Jogging Mate? By how much does this differ from the cost that was incurred? 2. Break down the difference in cost from (1) above into a labor rate variance and a labor effi- ciency variance. 3. The budgeted variable manufacturing overhead rate is $4 per direct labor-hour. During August, the company incurred $21,850 in variable manufacturing overhead cost. Compute the variable overhead rate and efficiency variances for the month.arrow_forward
- Erie Company manufactures a mobile fitness device called the Jogging Mate. The company uses standards to control its costs. The labor standards that have been set for one Jogging Mate are as follows: Standard Hours Standard Rate per Hour Standard Cost 18 minutes $ 17.00 $ 5.10 During August, 5,750 hours of direct labor time were needed to make 20,000 units of the Jogging Mate. The direct labor cost totaled $102,350 for the month. Please help with the following: A) What is the standard labor-hours allowed (SH) to makes 20,000 Jogging Mates? B) What is the standard labor cost allowed (SH × SR) to make 20,000 Jogging Mates? C) What is the labor spending variance? D) What is the labor rate variance and the labor efficiency variance? E) The budgeted variable manufacturing overhead rate is $4 per direct labor-hour. During August, the company incurred $21,850 in variable manufacturing overhead cost. Compute the variable overhead rate and efficiency variances for the month.arrow_forwardPERBANAS, Inc. installs heating systems in new homes built in the southern tier counties of New York state. Jobs are priced using the time and materials method. The president of PERBANAS, Fenturini, is pricing a job involving the heating systems for six houses to be built by a local developer. He has made the following estimates. Material cost $ 30,000 Labor hours 200 The following predictions pertain to the company’s operations for the next year. Labor rate, including fringe benefits $ 8.00 per hour Annual labor hours 6,000 hours Annual overhead costs: Material handling and storage $ 12,500 Other overhead costs $ 54,000 Annual cost of materials used $ 125,000 Perbanas adds a markup of $ 2 per hour on its time charges, but there is no markup on material costs. Required: 1. Calculate the company's time charges and the material charges percentage. 2. Compute the price for the job 3. What would be the price of the job if Perbanas also added a markup of 5 % on all material charges…arrow_forwardErie Company manufactures a mobile fitness device called the Jogging Mate. The company uses standards to control its costs. The labor standards that have been set for one Jogging Mate are as follows: Standard Hours 30 minutes Standard Rate per Hour $5.60 During August, 10,370 hours of direct labor time were needed to make 19,200 units of the Jogging Mate. The direct labor cost totaled $55,998 for the month. Standard Cost $2.80 Required: 1. What is the standard labor-hours allowed (SH) to makes 19,200 Jogging Mates? 2. What is the standard labor cost allowed (SH x SR) to make 19,200 Jogging Mates? 3. What is the labor spending variance? 4. What is the labor rate variance and the labor efficiency variance? 5. The budgeted variable manufacturing overhead rate is $4.50 per direct labor-hour. During August, the company incurred $53,924 in variable manufacturing overhead cost. Compute the variable overhead rate and efficiency variances for the month. (For requirements 3 through 5, indicate…arrow_forward
- Cornerstones of Cost Management (Cornerstones Ser...AccountingISBN:9781305970663Author:Don R. Hansen, Maryanne M. MowenPublisher:Cengage LearningEssentials of Business Analytics (MindTap Course ...StatisticsISBN:9781305627734Author:Jeffrey D. Camm, James J. Cochran, Michael J. Fry, Jeffrey W. Ohlmann, David R. AndersonPublisher:Cengage LearningManagerial AccountingAccountingISBN:9781337912020Author:Carl Warren, Ph.d. Cma William B. TaylerPublisher:South-Western College Pub
- Financial And Managerial AccountingAccountingISBN:9781337902663Author:WARREN, Carl S.Publisher:Cengage Learning,
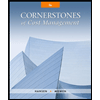
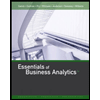
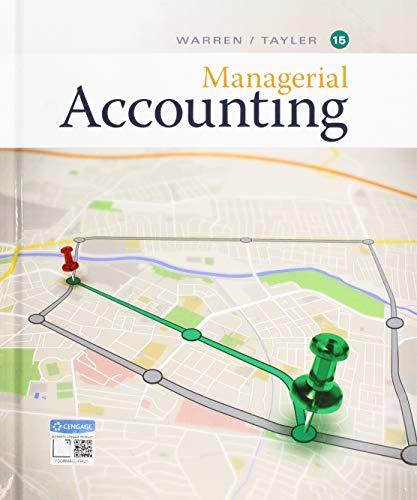
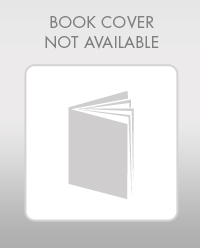