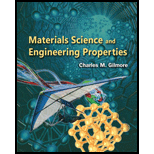
Concept explainers
(a)
The strain where the first change in elastic modulus occurs in composite material.
(a)

Answer to Problem 12.12P
Matrix will rupture before the fiber at the strain of
Explanation of Solution
Given:
Elastic modulus of Boronis
Tensile strength of Boronis
Elastic modulus of Aluminumis
Yield strength of Aluminumis
Ultimate tensile strength of aluminum is
Concept used:
Write the expression for failure strain in Fiber.
Here,
Write the expression for failure strain in Matrix.
Here,
Calculation:
Substitute
Substitute
Conclusion:
Thus, matrix will rupture before the fiber at the strain of
(b)
The composite stress where the change in elastic modulus occurs.
(b)

Answer to Problem 12.12P
The composite stress where the change in elastic modulus occurs is
Explanation of Solution
Given:
Volume percent of Boron fiber is
Volume percent of Aluminumis
Strain at fracture of Aluminumis
Concept used:
Write the expression for stress carried by composite.
Here,
Write the expression for stress in fiber by considering the iso-strain model for axial strain.
Here,
Calculation:
Substitute
Substitute
Conclusion:
Thus, the composite stress where the change in elastic modulus occurs is
(c)
The elastic modulus at low strain and the elastic modulus after Aluminum yields, if Aluminum yields before fiber fails.
(c)

Answer to Problem 12.12P
The elastic modulus at low strain is
Explanation of Solution
Concept used:
Write the expression for modulus of elasticity of composite.
Here,
Calculation:
Substitute
After yielding of matrix the elastic modulus of composite is the elastic modulus of fiber in it. Therefore, the elastic modulus will be equal to 60% of
Conclusion:
Thus, the elastic modulus at low strain is
(d)
Fracture strength of composite.
(d)

Answer to Problem 12.12P
Fracture strength of composite is
Explanation of Solution
Concept used:
Write the expression for fracture strength.
Here,
Calculation:
Substitute
Conclusion:
Thus, the Fracture strength of composite is
Want to see more full solutions like this?
Chapter 12 Solutions
Materials Science And Engineering Properties
- A solid rod of bronze 20 mm in diameter is surrounded by a fitting steel cylinder of external diameter 28 mm. If the permissible bending stress in bronze and steel are 100 and 150 N/mm², find the moment of resistance of the composite section. The Young's modulus for steel may be taken as 1.75 times that of bronze.arrow_forward(a) the modulus of elasticity in GPa for the Aluminum B) the proportional limit in MPa for the Aluminum C) the ultimate strength in MPa for the Aluminum D) Ductility of material based on percent elongationarrow_forwardA ceramic matrix composite contains internal flaws as large as 0.001 cm in length. The plane strain fracture toughness of the composite is 45 MPaÖm, and the tensile strength is 550 Mpa. Will the stress cause the composite to fail before the tensile strength is 550 MPa. Will the stress cause the composite to fail before the tensile strength is reached? Assume that f=1.arrow_forward
- The aluminum (E=15x10^10psi, α=11.6x10^-6/°F) shell is fully bonded to the brass (E=10.6x10^6psi, α=12.9x10^-6/°F) sore, and the assembly is unstressed at a temperature of 78°F. Considering only axial deformations, determine the stress when the temperature reaches 180°F (a) in the brass core (b) in the aluminum shellarrow_forwardIn the bulk modulus of Brass is 110 GPa and its Poisson's ratio is 0.30, then the elastic modulusarrow_forwardThe critical bending compressive stress in the extreme fibre of a structural steel section is 1000 MPa. It is given that the yield strength of the steel is 250 MPa, width of flange is 250 mm and thickness of flange is 15 mm. As per the provisions of IS: 800 -2007, the non-dimensional slenderness ratio of the steel cross-section is (a) 0.25 (c) 2.00 (b) 0.75 (d) 0.50arrow_forward
- The stainless steel specimen is shown in Figure 3 with tensile engineering stress-strain behaviour. a)Compute the modulus of elasticity. and Compute the yield strength at a strain offset of 0.002.arrow_forwardThe ultimate tensile stress of gray cast iron is------than the * ultimate compressive stressarrow_forward
- Materials Science And Engineering PropertiesCivil EngineeringISBN:9781111988609Author:Charles GilmorePublisher:Cengage Learning
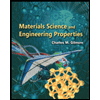