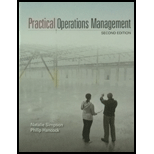
Concept explainers
a
Interpretation:
Amount paid by the hotel for desert and frequency of production of desert under its current policy.
Concept Introduction: Materials Requirement Planning is a process in which planning is made for the requirement of raw material required for manufacturing of the finished product.
a

Explanation of Solution
Demand for desert = 30,000 per year
Production rate = 125 per day
Set up cost = $4
Cost of dessert = $0.40
Daily demand for dessert is calculated by dividing annual demand with the number of days the company can operate in the year.
Hence, the daily demand is 82 desserts.
Calculation of holding cost.
It is given that holding cost is 300% of the cost of the dessert.
Hence, the holding cost per dessert is $1.2
Calculation of total holding and ordering cost for given batch quantity.
It is given that the current batch quantity is 300 desserts.
Calculation of annual holding cost:
Annual holding cost is calculated by multiplying the holding cost with two values. First value is calculated by dividing the quantity with 2. Second value is calculated by subtracting the value attained by dividing the daily demand with the production from 1.
Hence, the annual holding cost is $61.92
Calculation of annual ordering cost:
It is calculated by multiplying the setup cost with the value attained by dividing the annual demand with the batch quantity.
Hence, the annual ordering cost is $400.
Calculation of total cost of inventory:
It is calculated by adding the annual holding cost and annual ordering cost.
Hence, the total cost of inventory is $461.9
Calculation of frequency of dessert production:
It is calculated by dividing the annual demand with the batch quantity.
Hence, the company will produce 100 batches.
b
Interpretation:
Order size required to minimize the total annual cost and amount of savings by using order size.
Concept Introduction: Materials Requirement Planning is a process in which planning is made for the requirement of raw material required for manufacturing of the finished product.
b

Explanation of Solution
Calculation of order size:
It is calculated by dividing two values and taking the square root of the attained value. First value is the multiple of annual demand and set up cost with 2. Second value is calculated by multiplying the holding cost with the value attained by subtracting the dividing value of daily demand with production rate from 1.
Hence, the economic order quantity is 762.5
Calculation of total holding cost and ordering cost for optimal order quantity:
It is given that the optimal order quantity is 762.5 desserts.
Annual holding cost is calculated by multiplying the holding cost with two values. First value is calculated by dividing the quantity with 2. Second value is calculated by subtracting the value attained by dividing the daily demand with the production from 1.
Hence, the annual holding cost is $157.38
Calculation of annual ordering cost:
It is calculated by multiplying the setup cost with the value attained by dividing the annual demand with the batch quantity.
Hence, the annual ordering cost is $157.37
Calculation of total cost of inventory:
It is calculated by adding annual holding cost and annual ordering cost.
Annual saving in the total cost of optimal order quantity:
It is calculated by subtracting the total cost of optimal quantity from the total cost of given batch quantity.
Hence, the annual saving is $147.2
c
Interpretation:
Change in size of refrigerated pantry.
Concept Introduction: The efficiency of output is the actual productivity generated compared with the planned or effective capacity. It is usually calculated by dividing actual output by effective capacity.
c

Explanation of Solution
The plan to expand the capacity
The lowest inventory cost order size is 762 desserts. However, the refrigerator can only store 300 desserts. Thus, the capacity must increase 462 spaces.
Want to see more full solutions like this?
Chapter 10 Solutions
Practical Operations Management
- Assume the demand for a companys drug Wozac during the current year is 50,000, and assume demand will grow at 5% a year. If the company builds a plant that can produce x units of Wozac per year, it will cost 16x. Each unit of Wozac is sold for 3. Each unit of Wozac produced incurs a variable production cost of 0.20. It costs 0.40 per year to operate a unit of capacity. Determine how large a Wozac plant the company should build to maximize its expected profit over the next 10 years.arrow_forwardArthur Meiners is the production manager for Wheel-Rite, a small manufacturer of metal parts. Wheel-Rite sells 10,378 gear wheels each year. Wheel-Rite setup cost is $45 and maintenance cost is $0.60 per sprocket per year. Wheel-Rite can produce 493 gear wheels per day. The daily demand for the gear wheels is 51 units. Show your work. 1. What inventory management model should we use to solve this problem? Model for discount purchases Model Economic Quantity to Order Model Economic Quantity to Produce Model to handle dependent demand 2. What is the optimal amount of production? Response 3. What is the maximum inventory level of gear wheels that will be in the Wheel-Rite warehouse? Response 4. What is Wheel-Rite's annual setup cost? Response 5. What is the annual cost of maintaining Wheel-Rite? Responsearrow_forwardAn oil refinery buys crude oil on a long-term supply contract for $22.50 per barrel.When shipments of crude oil are made to the refinery, they arrive at the rate of10,000 barrels per day. The refinery uses the oil at a rate of 5,000 barrels per dayand plans to purchase 500,000 barrels of crude oil next year. If the carrying cost is25percent of acquisition cost per unit per year and the ordering cost is $7,500 perorder:a. What is the EOQ for the crude oil?b. What is the TSC at EOQ?c. How many days of production are supported by each order of crude oil?d. How much storage capacity is needed for the crude oil?arrow_forward
- Beach Republic Bank operates a network of automated teller machines (ATMs). Cash withdrawals at a particular ATM average approximately $80 per transaction. The average number of withdrawals per ATM is 120 per week. The bank estimates that it costs about $100 to fill the ATM each time regardless of the amount of cash that is added to the machine. Assume that the cost of capital for the bank is 10%, and there are 52 weeks in a year. What is the optimal cash filling policy and the associated total inventory ordering and holding cost? Suppose that the standard deviation of weekly number of withdrawals is 20 and the lead time to fill an ATM is half a week (3.5 days), how much cash should the bank allocate to an ATM to be 99% confident of not running out of money between deliveries? Given the information from parts a and b, what would the cost savings be for reducing the number of ATMs from 100 to 20? Discuss the pros and cons of pooling the cash inventory in this context.…arrow_forwardA plant makes monthly shipments of electric drills to a wholesaler in average lot sizes of 280 drills. The whole-saler’s average demand is 70 drills a week, and the lead time from the plant is 3 weeks. The wholesaler mustpay for the inventory from the moment the plant makes a shipment. If the wholesaler is willing to increase itspurchase quantity to 350 units, the plant will give priority to the wholesaler and guarantee a lead time of only2 weeks. What is the effect on the wholesaler’s cycle and pipeline inventories?arrow_forwardCassie Company manufactures a line of deluxe office fixtures. The annual demand for its miniature oak file is estimated to be 5,000 units. The annual cost of carrying one unit in inventory is P10, and the cost to initiate a production run is P1,000. There are no miniature oak files on hard, and Cassie has scheduled four equal production runs of the miniature oak file for the coming year, the first of which is to be run immediately. Cassie has 250 business days per year. Assume that sales occur uniformly throughout the year and that production is instantaneous. If Cassie does not maintain a safety stock, the estimated total carrying costs for the office fixtures for the coming year based on their current schedule is?The number of production runs per year of the miniature oak files that would minimize the sum of carrying costs and setup costs for the coming year is?arrow_forward
- A Mercedes dealer purchases vehicles for $20,000. The annual holding cost is estimated to be 25% of the dollar value of inventory. The dealer sells an average of 500 cars per year. He believes that demand is backlogged, but estimates that if he is short one car for one year, he will lose $20,000 in future profits. Each time the dealer places an order for cars, the ordering cost amounts to $10,000. Determine the Mercedes dealer's optimal (?,?) ordering policy.arrow_forwardLeaky Pipe, a local retailer of plumbing supplies, faces demand for one of its SKUs at a constant rate of 30,000 units per year. It costs Leaky Pipe $10 to process an order to replenish stock and $1 per unit per year to carry the item in stock. Stock is received 4 working days after an order is placed. No backordering is allowed. Assume 300 working days a year.a. What is Leaky Pipe’s optimal order quantity?b. What is the optimal number of orders per year?c. What is the optimal interval (in working days) between orders?d. What is the demand during the lead time?e. What is the reorder point?f. What is the inventory position immediately after an order has been placed?arrow_forwardABC Inc., purchases Widgets from an overseas supplier under a continuous review system. The average demand for a popular model is 300 units a day with a Lead Time standard deviation of 70 units. It costs $60 to process each order and there is a five-day lead-time. The holding cost for a widget is $0.25 per year and the company policy is to maintain a 98% service level. ABC operates 200 days per year. What is the additional cost in $ of holding the safety stock necessary to maintain the 98% service level? What service level in % does a reorder point of 1,570 imply?arrow_forward
- You are in charge of purchases at the student-run used-book supply program at your college, and you must decide how many introductory calculus, history, and marketing texts should be purchased from students for resale. Due to budget limitations, you cannot purchase more than 700 of these textbooks each semester. There are also shelf-space limitations: Calculus texts occupy 2 units of shelf space each, history books 1 unit each, and marketing texts 5 units each, and you can spare at most 1,200 units of shelf space for the texts. If the used book program makes a profit of $20 on each calculus text, $8 on each history text, and $16 on each marketing text, how many of each type of text should you purchase to maximize profit?arrow_forwardBold Vision, Inc., must purchase toner from a local supplier. The company does not wish to carry raw material inventory and therefore only purchases enough toner to satisfy the demand of each individual batch of cartridges. Each toner cartridge requires one pound of toner. The raw material supplier offers Bold Vision a purchase discount of $2.00 per pound if the company orders at least 2,000 pounds at a time. Should Bold Vision accept this offer and alter its toner purchase quantity?arrow_forwardWilson Publishing Company produces books for the retail market. Demand for a current book is expected to occur at a constant annual rate of 7,400 copies. The cost of one copy of the book is $11.50. The holding cost is based on an 18% annual rate, and production setup costs are $150 per setup. The equipment with which the book is produced has an annual production volume of 25,000 copies. Wilson has 250 working days per year, and the lead time for a production run is 15 days. Use the production lot size model to compute the following values. (Round your answers to two decimal places.) (a)Minimum cost production lot size (b)Number of production runs per year (c)Cycle time (d)Length of a production run (in days) days (e)Maximum inventory (f)Total annual cost (in $) $ (g)Reorder pointarrow_forward
- Practical Management ScienceOperations ManagementISBN:9781337406659Author:WINSTON, Wayne L.Publisher:Cengage,
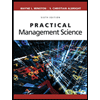