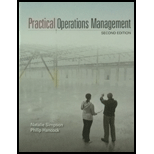
Practical Operations Management
2nd Edition
ISBN: 9781939297136
Author: Simpson
Publisher: HERCHER PUBLISHING,INCORPORATED
expand_more
expand_more
format_list_bulleted
Concept explainers
Question
Chapter 10, Problem 18P
Summary Introduction
Interpretation: The Average number of cards in shop as inventory is to be calculated.
Concept Introduction: Inventory management is the process of managing the company’s stock so that there are no stock outs. It includes ordering, storing, managing the stock.
Expert Solution & Answer

Want to see the full answer?
Check out a sample textbook solution
Students have asked these similar questions
Discuss the principle reasons that employee benefits have risen over the past 20 years, along with how best an organization can provide employees with a fair wage yet also provide some level of employee benefit coverage.
Please assist with the Case Study below as attached.
Read the case study below and answer the questions that follow.
The Importance of the Planning Phase to Project Success.
Traditional wisdom is that planning and analysis are very important and the more there is in a project, the more successful the project will be. Time spent on these activities will reduce risk and increase project success. On the other hand, inadequate analysis and planning will lead to a failed project. If poor planning has led to failed projects, then perhaps billions of dollars have been lost. But how much is too much? “Light weight” project management techniques such as agile are gaining popularity. Part of their ethos is that less initial planning is better and an evolutionary process is more efficient.
QUESTION 1
The article above states: “Traditional wisdom is that planning and analysis are very important and the more there is in a project, the more successful the project will be”.
Describe FIVE (5) ways…
On a daily basis, the van is dispatched from Maplewood Hospital to pickup blood and platelet donations made at its local donation centers. The distances in
miles between all locations may be found in the table below.
Click the icon to view mileage data for Vampire Van.
a. The van travels from the Hospital (A) to (B) to (C) to (D) to (E) and then returns to the Hospital (A). What is the total number of miles that the van must
travel using this route?
Route ABCDEA requires a total distance of 20.4 miles. (Enter your response rounded to one decimal place.)
b. Using Maplewood Hospital as the beginning location, create a route using the Nearest Neighbor heuristic. What is the total number of miles that the van
must travel using this route?
The new route is A
A and requires a total distance of miles. (Enter your response rounded to one decimal place.)
More Info
Maplewood
City Center
Westbrook
Hospital (A) Donation Site (B)
Donation Site (C)
Municipal Park
Donation Site (D)
Valley Hills…
Chapter 10 Solutions
Practical Operations Management
Ch. 10 - Prob. 1DQCh. 10 - Prob. 2DQCh. 10 - Prob. 3DQCh. 10 - Prob. 4DQCh. 10 - Prob. 5DQCh. 10 - Prob. 6DQCh. 10 - Prob. 1PCh. 10 - Prob. 2PCh. 10 - Prob. 3PCh. 10 - Prob. 4P
Ch. 10 - Prob. 5PCh. 10 - Prob. 6PCh. 10 - Prob. 7PCh. 10 - Prob. 8PCh. 10 - Prob. 9PCh. 10 - Prob. 10PCh. 10 - Prob. 11PCh. 10 - Prob. 12PCh. 10 - Prob. 13PCh. 10 - Prob. 14PCh. 10 - Prob. 15PCh. 10 - Prob. 16PCh. 10 - Prob. 17PCh. 10 - Prob. 18PCh. 10 - Prob. 19PCh. 10 - Prob. 20PCh. 10 - Prob. 21PCh. 10 - Prob. 22PCh. 10 - Prob. 23PCh. 10 - Prob. 24PCh. 10 - Prob. 25PCh. 10 - Prob. 26PCh. 10 - Prob. 27PCh. 10 - Prob. 28PCh. 10 - Prob. 29PCh. 10 - Prob. 30PCh. 10 - Prob. 31PCh. 10 - Prob. 2.1QCh. 10 - Prob. 2.2QCh. 10 - Prob. 2.3QCh. 10 - Prob. 2.4QCh. 10 - Prob. 3.1QCh. 10 - Prob. 3.2QCh. 10 - Prob. 3.3QCh. 10 - Prob. 3.4Q
Knowledge Booster
Learn more about
Need a deep-dive on the concept behind this application? Look no further. Learn more about this topic, operations-management and related others by exploring similar questions and additional content below.Similar questions
- View the video Noodles & Company (8.28minutes, Ctrl + Click on the link); what are your key takeaways (tie to one or more of the topics discussed in Chapters 7 & 7S – service process design, type of job design, methods analysis, work methods, job design, learning curve effect, etc.) after watching this video. https://media.gaspar.mheducation.com/GASPARPlayer/play.html?id=E5i8OKgpqhwywhgFmpp1bmM Note: As a rough guideline, please try to keep the written submission to one or two paragraphs. 2) Leland, the job analyst at Zevo Toys, wanted to perform a time study on the assembling of toys. He observed one of the workers, Magorium, for five hours. During that time, Magorium assembled 250 toys. Leland rated Magorium as performing at 110 percent. The allowance for rest, personal time, etc. at Zevo Toys is 12 percent. a) Compute the normal time for the job. b) Compute the standard time for the job. Note: You could work out the problem by hand or use excel; in chapter 7,…arrow_forward1) Noodles & Company View the video Noodles & Company (8.28minutes, Ctrl + Click on the link); what are your key takeaways (tie to one or more of the topics discussed in Chapters 7 & 7S – service process design, type of job design, methods analysis, work methods, job design, learning curve effect, etc.) after watching this video. https://media.gaspar.mheducation.com/GASPARPlayer/play.html?id=E5i8OKgpqhwywhgFmpp1bmM Note: As a rough guideline, please try to keep the written submission to one or two paragraphs. 2) Leland, the job analyst at Zevo Toys, wanted to perform a time study on the assembling of toys. He observed one of the workers, Magorium, for five hours. During that time, Magorium assembled 250 toys. Leland rated Magorium as performing at 110 percent. The allowance for rest, personal time, etc. at Zevo Toys is 12 percent. a) Compute the normal time for the job. b) Compute the standard time for the job. Note: You could work out the problem by hand or use…arrow_forwardAn investigation of career development opportunities and job satisfaction atarrow_forward
- The Donald Fertilizer Company produces industrial chemical fertilizers. The projected manufacturing requirements (in gallons) for the next four quarters are 90,000, 90,000, 60,000, and 140,000 respectively. A level workforce is desired, relying only on anticipation inventory as a supply option. Stockouts and backorders are to be avoided, as are overtime and undertime. a. Determine the quarterly production rate required to meet total demand for the year, and minimize the anticipation inventory that would be left over at the end of the year. Beginning inventory is 0. The quarterly production rate is 95000 gallons. (Enter your response as an integer.) b. Specify the anticipation inventory that will be produced. (Enter your responses as an integers.) Quarter Anticipation inventory (gallons) 1 5000 2 10000 3 4 45000 c. Suppose that the requirements (in gallons) for the next four quarters are revised to 140,000, 60,000, 90,000, and 90,000 respectively. If total demand is the same, what level…arrow_forwardPlease help with the attached Capstone proposal Requirements:arrow_forwardLong term capacity plans and how to properly make decisions regarding long-term planning Long-term capacity plans cover periods longer periods of time. These plans are suitable for large businesses that want to scale their operations with a proven strategy for achieving production targets and meeting customer demands. Long-term capacity plans consider other factors apart from the productive requirements of the company. How important is it, in your mind, to properly make decisions regarding long-term capacity planning? How does this decision impact the present and future profitability of an organization? Be specific and give examples.arrow_forward
- In addition to the Amazon case study you provided, I'm curious if you've encountered other examples of companies successfully applying Little's Law to enhance their supply chain risk management practices. For instance, have you seen organizations use queuing theory to assess the potential ripple effects of disruptions, stress-test their contingency plans, or identify critical control points that require heightened monitoring and agility? Please provide a referencearrow_forwardSam's Pet Hotel operates 48 weeks per year, 6 days per week, and uses a continuous review inventory system. It purchases kitty litter for $13.00 per bag The following information is available about these bags: > Demand 85 bags/week >Order cost $60.00/order > Annual holding cost = 35 percent of cost > Desired cycle-service level 80 percent > Lead time = 4 weeks (24 working days) > Standard deviation of weekly demand = 15 bags > Current on-hand inventory is 320 bags, with no open orders or backorders. a. Suppose that the weekly demand forecast of 85 bags is incorrect and actual demand averages only 65 bags per week. How much higher will total costs be, owing to the distorted EOQ caused by this forecast error? The costs will be $higher owing to the error in EOQ. (Enter your response rounded to two decimal places.)arrow_forwardOsprey Sports stocks everything that a musky fisherman could want in the Great North Woods. A particular musky lure has been very popular with local fishermen as well as those who buy lures on the Internet from Osprey Sports. The cost to place orders with the supplier is $3030/order; the demand averages 55 lures per day, with a standard deviation of 11 lure; and the inventory holding cost is $1.001.00/lure/year. The lead time form the supplier is 1010 days, with a standard deviation of 33 days. It is important to maintain a 9898 percent cycle-service level to properly balance service with inventory holding costs. Osprey Sports is open 350 days a year to allow the owners the opportunity to fish for muskies during the prime season. The owners want to use a continuous review inventory system for this item. Refer to the standard normal table LOADING... for z-values. Part 2 a. What order quantity should be used? enter your response here lures. (Enter your response rounded to the…arrow_forward
- 9. Research Methodology Fully explain the Quantitative research methodology that and add in the following sub-sections: . Data Collection • Data Analysisarrow_forwardRuby-Star Incorporated is considering two different vendors for one of its top-selling products which has an average weekly demand of 40 units and is valued at $80 per unit. Inbound shipments from vendor 1 will average 340 units with an average lead time (including ordering delays and transit time) of 2 weeks. Inbound shipments from vendor 2 will average 550 units with an average lead time of 1 week. Ruby-Star operates 52 weeks per year; it carries a 2-week supply of inventory as safety stock and no anticipation inventory. a. The average aggregate inventory value of the product if Ruby-Star used vendor 1 exclusively is $ (Enter your response as a whole number.)arrow_forwardThe Carbondale Hospital is considering the purchase of a new ambulance. The decision will rest partly on the anticipated mileage to be driven next year. The miles driven during the past 5 years are as follows: Year Mileage 1 3,000 2 3 4 4,000 3,450 3,850 5 3,800 a) Using a 2-year moving average, the forecast for year 6 = miles (round your response to the nearest whole number). b) If a 2-year moving average is used to make the forecast, the MAD based on this = miles (round your response to one decimal place). (Hint: You will have only 3 years of matched data.) c) The forecast for year 6 using a weighted 2-year moving average with weights of 0.40 and 0.60 (the weight of 0.60 is for the most recent period) = ☐ miles (round your response to the nearest whole number). miles (round your response to one decimal place). (Hint: You will have only 3 years of The MAD for the forecast developed using a weighted 2-year moving average with weights of 0.40 and 0.60 = matched data.) d) Using…arrow_forward
arrow_back_ios
SEE MORE QUESTIONS
arrow_forward_ios
Recommended textbooks for you
- Purchasing and Supply Chain ManagementOperations ManagementISBN:9781285869681Author:Robert M. Monczka, Robert B. Handfield, Larry C. Giunipero, James L. PattersonPublisher:Cengage LearningMarketingMarketingISBN:9780357033791Author:Pride, William MPublisher:South Western Educational Publishing
- Practical Management ScienceOperations ManagementISBN:9781337406659Author:WINSTON, Wayne L.Publisher:Cengage,Contemporary MarketingMarketingISBN:9780357033777Author:Louis E. Boone, David L. KurtzPublisher:Cengage Learning
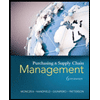
Purchasing and Supply Chain Management
Operations Management
ISBN:9781285869681
Author:Robert M. Monczka, Robert B. Handfield, Larry C. Giunipero, James L. Patterson
Publisher:Cengage Learning
Marketing
Marketing
ISBN:9780357033791
Author:Pride, William M
Publisher:South Western Educational Publishing
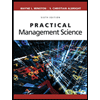
Practical Management Science
Operations Management
ISBN:9781337406659
Author:WINSTON, Wayne L.
Publisher:Cengage,
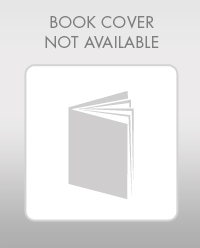
Contemporary Marketing
Marketing
ISBN:9780357033777
Author:Louis E. Boone, David L. Kurtz
Publisher:Cengage Learning
Inventory Management | Concepts, Examples and Solved Problems; Author: Dr. Bharatendra Rai;https://www.youtube.com/watch?v=2n9NLZTIlz8;License: Standard YouTube License, CC-BY