Principles of Accounting Volume 2
19th Edition
ISBN: 9781947172609
Author: OpenStax
Publisher: OpenStax College
expand_more
expand_more
format_list_bulleted
Question
thumb_up100%
I need help to see how I would get the capital expenditures for year 3, (520,387). I don't understand how this was gotten.
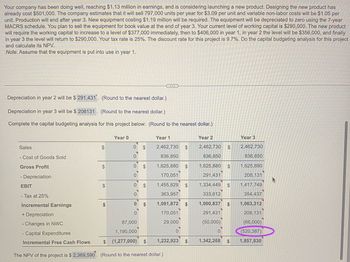
Transcribed Image Text:Your company has been doing well, reaching $1.13 million in earnings, and is considering launching a new product. Designing the new product has
already cost $501,000. The company estimates that it will sell 797,000 units per year for $3.09 per unit and variable non-labor costs will be $1.05 per
unit. Production will end after year 3. New equipment costing $1.19 million will be required. The equipment will be depreciated to zero using the 7-year
MACRS schedule. You plan to sell the equipment for book value at the end of year 3. Your current level of working capital is $290,000. The new product
will require the working capital to increase to a level of $377,000 immediately, then to $406,000 in year 1, in year 2 the level will be $356,000, and finally
in year 3 the level will return to $290,000. Your tax rate is 25%. The discount rate for this project is 9.7%. Do the capital budgeting analysis for this project
and calculate its NPV.
Note: Assume that the equipment is put into use in year 1.
Depreciation in year 2 will be $291,431. (Round to the nearest dollar.)
Depreciation in year 3 will be $ 208131. (Round to the nearest dollar.)
Complete the capital budgeting analysis for this project below: (Round to the nearest dollar.)
Sales
- Cost of Goods Sold
$
Gross Profit
- Depreciation
EBIT
- Tax at 25%
Incremental Earnings
+ Depreciation
-Changes in NWC
- Capital Expenditures
Year 0
S
$
Year 1
2,462,730 $
836,850
1,625,880 $
170,051
1,455,829 $
363,957
Year 2
Year 3
2,462,730 $
69
2,462,730
836,850
836,850
1,625,880 $
291,431
1,625,880
208,131
1,334,449 $
1,417,749
333,612
354,437
S
1,091,872 $
1,000,837 $
1,063,312
170,051
291,431
208,131
87,000
29,000
(50,000)
(66,000)
1,190,000
0
0
(520,387)
1,342,268 $
1,857,830
Incremental Free Cash Flows
$ (1,277,000) $ 1,232,923
The NPV of the project is $ 2,369,590. (Round to the nearest dollar.)
Expert Solution

This question has been solved!
Explore an expertly crafted, step-by-step solution for a thorough understanding of key concepts.
Step by stepSolved in 2 steps

Knowledge Booster
Similar questions
- Flanders Manufacturing is considering purchasing a new machine that will reduce variable costs per part produced by $0.15. The machine will increase fixed costs by $18,250 per year. The information they will use to consider these changes is shown here.arrow_forwardTalbot Industries is considering launching a new product. The new manufacturing equipment will cost $17 million, and production and sales will require an initial $5 million investment in net operating working capital. The company’s tax rate is 25%. What is the initial investment outlay? The company spent and expensed $150,000 on research related to the new product last year. What is the initial investment outlay? Rather than build a new manufacturing facility, the company plans to install the equipment in a building it owns but is not now using. The building could be sold for $1.5 million after taxes and real estate commissions. What is the initial investment outlay?arrow_forwardGardner Denver Company is considering the purchase of a new piece of factory equipment that will cost $420,000 and will generate $95,000 per year for 5 years. Calculate the IRR for this piece of equipment. For further Instructions on internal rate of return in Excel, see Appendix C.arrow_forward
- Talbot Industries is considering launching a new product. The new manufacturing equipment will cost 17 million, and production and sales will require an initial 5 million investment in net operating working capital. The companys tax rate is 40%. a. What is the initial investment outlay? b. The company spent and expensed 150,000 on research related to the new product last year. Would this change your answer? Explain. c. Rather than build a new manufacturing facility, the company plans to install the equipment in a building it owns but is not now using. The building could be sold for 1.5 million after taxes and real estate commissions. How would this affect your answer?arrow_forwardGina Ripley, president of Dearing Company, is considering the purchase of a computer-aided manufacturing system. The annual net cash benefits and savings associated with the system are described as follows: The system will cost 9,000,000 and last 10 years. The companys cost of capital is 12 percent. Required: 1. Calculate the payback period for the system. Assume that the company has a policy of only accepting projects with a payback of five years or less. Would the system be acquired? 2. Calculate the NPV and IRR for the project. Should the system be purchasedeven if it does not meet the payback criterion? 3. The project manager reviewed the projected cash flows and pointed out that two items had been missed. First, the system would have a salvage value, net of any tax effects, of 1,000,000 at the end of 10 years. Second, the increased quality and delivery performance would allow the company to increase its market share by 20 percent. This would produce an additional annual net benefit of 300,000. Recalculate the payback period, NPV, and IRR given this new information. (For the IRR computation, initially ignore salvage value.) Does the decision change? Suppose that the salvage value is only half what is projected. Does this make a difference in the outcome? Does salvage value have any real bearing on the companys decision?arrow_forwardNico Parts, Inc., produces electronic products with short life cycles (of less than two years). Development has to be rapid, and the profitability of the products is tied strongly to the ability to find designs that will keep production and logistics costs low. Recently, management has also decided that post-purchase costs are important in design decisions. Last month, a proposal for a new product was presented to management. The total market was projected at 200,000 units (for the two-year period). The proposed selling price was 130 per unit. At this price, market share was expected to be 25 percent. The manufacturing and logistics costs were estimated to be 120 per unit. Upon reviewing the projected figures, Brian Metcalf, president of Nico, called in his chief design engineer, Mark Williams, and his marketing manager, Cathy McCourt. The following conversation was recorded: BRIAN: Mark, as you know, we agreed that a profit of 15 per unit is needed for this new product. Also, as I look at the projected market share, 25 percent isnt acceptable. Total profits need to be increased. Cathy, what suggestions do you have? CATHY: Simple. Decrease the selling price to 125 and we expand our market share to 35 percent. To increase total profits, however, we need some cost reductions as well. BRIAN: Youre right. However, keep in mind that I do not want to earn a profit that is less than 15 per unit. MARK: Does that 15 per unit factor in preproduction costs? You know we have already spent 100,000 on developing this product. To lower costs will require more expenditure on development. BRIAN: Good point. No, the projected cost of 120 does not include the 100,000 we have already spent. I do want a design that will provide a 15-per-unit profit, including consideration of preproduction costs. CATHY: I might mention that post-purchase costs are important as well. The current design will impose about 10 per unit for using, maintaining, and disposing our product. Thats about the same as our competitors. If we can reduce that cost to about 5 per unit by designing a better product, we could probably capture about 50 percent of the market. I have just completed a marketing survey at Marks request and have found out that the current design has two features not valued by potential customers. These two features have a projected cost of 6 per unit. However, the price consumers are willing to pay for the product is the same with or without the features. Required: 1. Calculate the target cost associated with the initial 25 percent market share. Does the initial design meet this target? Now calculate the total life-cycle profit that the current (initial) design offers (including preproduction costs). 2. Assume that the two features that are apparently not valued by consumers will be eliminated. Also assume that the selling price is lowered to 125. a. Calculate the target cost for the 125 price and 35 percent market share. b. How much more cost reduction is needed? c. What are the total life-cycle profits now projected for the new product? d. Describe the three general approaches that Nico can take to reduce the projected cost to this new target. Of the three approaches, which is likely to produce the most reduction? 3. Suppose that the Engineering Department has two new designs: Design A and Design B. Both designs eliminate the two nonvalued features. Both designs also reduce production and logistics costs by an additional 8 per unit. Design A, however, leaves post-purchase costs at 10 per unit, while Design B reduces post-purchase costs to 4 per unit. Developing and testing Design A costs an additional 150,000, while Design B costs an additional 300,000. Assuming a price of 125, calculate the total life-cycle profits under each design. Which would you choose? Explain. What if the design you chose cost an additional 500,000 instead of 150,000 or 300,000? Would this have changed your decision? 4. Refer to Requirement 3. For every extra dollar spent on preproduction activities, how much benefit was generated? What does this say about the importance of knowing the linkages between preproduction activities and later activities?arrow_forward
- Your company has been doing well, reaching $1 million in earnings, and is considering launching a new product. Designing the new product has already cost $500,000. The company estimates that it will sell 820,000 units per year for $6.75 per unit and variable non-labor costs will be $1.5 per unit. Production will end after year 3. New equipment costing $1 million will be required. The equipment will be put into use in year 1 and depreciated to zero using the 7-year MACRS schedule. You plan to sell the equipment for book value at the end of year 3. Your current level of working capital is $310,000. The new product will require the working capital to increase to a level of $450,000 immediately, then to $465,000 in year 1, in year 2 the level will be $320,000, and finally in year 3 the level will return to $310,000. Your tax rate is 21%. The discount rate for this project is 10%. Do the capital budgeting analysis for this project and calculate its NPV.arrow_forwardYour company has been doing well, reaching $1.02 million in earnings, and is considering launching a new product. Designing the new product has already cost $510,000. The company estimates that it will sell 773,000 units per year for $3.05 per unit and variable non-labor costs will be $1.09 per unit. Production will end after year 3. New equipment costing $1.01 million will be required. The equipment will be depreciated to zero using the 7-year MACRS schedule. You plan to sell the equipment for book value at the end of year 3. Your current level of working capital is $302,000. The new product will require the working capital to increase to a level of $387,000 immediately, then to $399,000 in year 1, in year 2 the level will be $341,000, and finally in year 3 the level will return to $302,000. Your tax rate is 21%. The discount rate for this project is 9.7%. Do the capital budgeting analysis for this project and calculate its NPV. Note: Assume that the equipment is put into use in year…arrow_forward5. Your company has been doing well, reaching $1.15 million in earnings, and is considering launching a new product. Designing the new product has already cost $466,000. The company estimates that it will sell 756,000 units per year for $2.94 per unit and variable non-labor costs will be $1.03 per unit. Production will end after year 3. New equipment costing $1.07 million will be required. The equipment will be depreciated to zero using the 7-year MACRS schedule. You plan to sell the equipment for book value at the end of year 3. Your current level of working capital is $306,000. The new product will require the working capital to increase to a level of $378,000 immediately, then to $396,000 in year 1, in year 2 the level will be $354,000, and finally in year 3 the level will return to $306,000. Your tax rate is 21%. The discount rate for this project is 9.8%. Do the capital budgeting analysis for this project and calculate its NPV. Note: Assume that the equipment is put into use in…arrow_forward
- Nikularrow_forwardVandalay industries is considering the purchase of a new machine for the production of latex. Machine A cost $2,270,000 and will last for 4 years. Variable cost are 38 percent of sales, and fixed cost are $145,000 per year. Machine B cost $4,290,000 and will last for 8 years. Variable costs for this machine are 29 percent of sales and fixed costs are $84,000 per year. The sales for each machine will be $8.58 million per year. The required return is 10 percent and the tax rate is 35 percent. Both machines will be depreciated on a straight line basis. A.Required: if the company plans to replace the machine when it wears out on a perpetual basis, what is the EAC for machine A? Do not round your intermediate calculations. B. If the company plans to replace the machine when it wears out on a perpetual basis, what is the EAC for machine B? Do not round your intermediate calculations.arrow_forwardBeacon Company is considering automating its production facility. The initial investment in automation would be $6.46 million, and the equipment has a useful life of 5 years with a residual value of $1,060,000. The company will use straight-line depreciation. Beacon could expect a production increase of 43,000 units per year and a reduction of 20 percent in the labor cost per unit. Production and sales volume Sales revenue Variable costs Direct materials Direct labor Variable manufacturing overhead Total variable manufacturing costs Contribution margin Fixed manufacturing costs Net operating income. Per Unit $ 98 Net present value $18 25 11 54 $44 Current (no automation) 76,000 units Total $ ? ? $1,220,000 ? Proposed (automation) 119,000 units Per Unit $98 $18 ? 11 ? $49 Total $? ? $ 2,190,000 ? Check my we 5. Recalculate the NPV using a 10 percent discount rate. (Future Value of $1, Present Value of $1, Future Value Annuity of $1, Present Value Annuity of $1.) (Use appropriate…arrow_forward
arrow_back_ios
SEE MORE QUESTIONS
arrow_forward_ios
Recommended textbooks for you
- Principles of Accounting Volume 2AccountingISBN:9781947172609Author:OpenStaxPublisher:OpenStax CollegeEBK CONTEMPORARY FINANCIAL MANAGEMENTFinanceISBN:9781337514835Author:MOYERPublisher:CENGAGE LEARNING - CONSIGNMENT
- Intermediate Financial Management (MindTap Course...FinanceISBN:9781337395083Author:Eugene F. Brigham, Phillip R. DavesPublisher:Cengage LearningCornerstones of Cost Management (Cornerstones Ser...AccountingISBN:9781305970663Author:Don R. Hansen, Maryanne M. MowenPublisher:Cengage Learning
Principles of Accounting Volume 2
Accounting
ISBN:9781947172609
Author:OpenStax
Publisher:OpenStax College
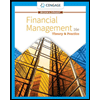
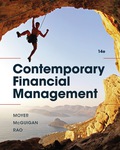
EBK CONTEMPORARY FINANCIAL MANAGEMENT
Finance
ISBN:9781337514835
Author:MOYER
Publisher:CENGAGE LEARNING - CONSIGNMENT
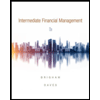
Intermediate Financial Management (MindTap Course...
Finance
ISBN:9781337395083
Author:Eugene F. Brigham, Phillip R. Daves
Publisher:Cengage Learning
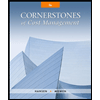
Cornerstones of Cost Management (Cornerstones Ser...
Accounting
ISBN:9781305970663
Author:Don R. Hansen, Maryanne M. Mowen
Publisher:Cengage Learning