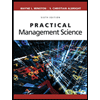
Practical Management Science
6th Edition
ISBN: 9781337406659
Author: WINSTON, Wayne L.
Publisher: Cengage,
expand_more
expand_more
format_list_bulleted
Question
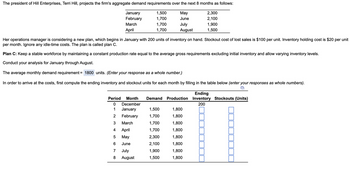
Transcribed Image Text:The president of Hill Enterprises, Terri Hill, projects the firm's aggregate demand requirements over the next 8 months as follows:
May
1,500
1,700
1,700
June
1,700
January
February
March
April
Her operations manager is considering a new plan, which begins in January with 200 units of inventory on hand. Stockout cost of lost sales is $100 per unit. Inventory holding cost is $20 per unit
per month. Ignore any idle-time costs. The plan is called plan C.
Plan C: Keep a stable workforce by maintaining a constant production rate equal to the average gross requirements excluding initial inventory and allow varying inventory levels.
Conduct your analysis for January through August.
The average monthly demand requirement = 1800 units. (Enter your response as a whole number.)
In order to arrive at the costs, first compute the ending inventory and stockout units for each month by filling in the table below (enter your responses as whole numbers).
D₂₁
0 December
1
January
2
February
3
March
4
April
5
May
June
July
August
6
7
8
July
August
Ending
Period Month Demand Production Inventory Stockouts (Units)
200
1,500
1,700
1,700
1,700
2,300
2,100
1,900
1,500
2,300
2,100
1,900
1,500
1,800
1,800
1,800
1,800
1,800
1,800
1,800
1,800
Expert Solution

This question has been solved!
Explore an expertly crafted, step-by-step solution for a thorough understanding of key concepts.
This is a popular solution
Trending nowThis is a popular solution!
Step by stepSolved in 3 steps with 4 images

Follow-up Questions
Read through expert solutions to related follow-up questions below.
Follow-up Question
I completed those steps and it is saying my answer is incorrect
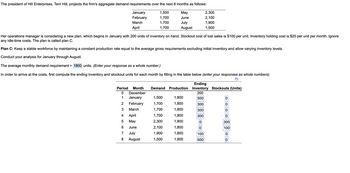
Transcribed Image Text:The president of Hill Enterprises, Terri Hill, projects the firm's aggregate demand requirements over the next 8 months as follows:
May
January
February
1,500
1,700
1,700
June
July
March
April
1,700
August
Her operations manager is considering a new plan, which begins in January with 200 units of inventory on hand. Stockout cost of lost sales is $100 per unit. Inventory holding cost is $20 per unit per month. Ignore
any idle-time costs. The plan is called plan C.
Plan C: Keep a stable workforce by maintaining a constant production rate equal to the average gross requirements excluding initial inventory and allow varying inventory levels.
Conduct your analysis for January through August.
The average monthly demand requirement = 1800 units. (Enter your response as a whole number.)
In order to arrive at the costs, first compute the ending inventory and stockout units for each month by filling in the table below (enter your responses as whole numbers).
D
2,300
2,100
1,900
1,500
Ending
Period Month Demand Production Inventory Stockouts (Units)
0 December
200
1 January
1,500
500
2 February
1,700
300
M
3 March
1,700
300
4 April
1,700
300
5 May
2,300
0
6 June
2,100
0
7
July
1,900
100
8 August
500
1,500
1,800
1,800
1,800
1,800
1,800
1,800
1,800
1,800
ܘ ܘ ܘ ܘ
300
100
0
0
Solution
by Bartleby Expert
Follow-up Questions
Read through expert solutions to related follow-up questions below.
Follow-up Question
I completed those steps and it is saying my answer is incorrect
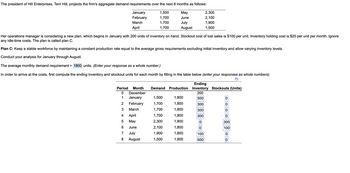
Transcribed Image Text:The president of Hill Enterprises, Terri Hill, projects the firm's aggregate demand requirements over the next 8 months as follows:
May
January
February
1,500
1,700
1,700
June
July
March
April
1,700
August
Her operations manager is considering a new plan, which begins in January with 200 units of inventory on hand. Stockout cost of lost sales is $100 per unit. Inventory holding cost is $20 per unit per month. Ignore
any idle-time costs. The plan is called plan C.
Plan C: Keep a stable workforce by maintaining a constant production rate equal to the average gross requirements excluding initial inventory and allow varying inventory levels.
Conduct your analysis for January through August.
The average monthly demand requirement = 1800 units. (Enter your response as a whole number.)
In order to arrive at the costs, first compute the ending inventory and stockout units for each month by filling in the table below (enter your responses as whole numbers).
D
2,300
2,100
1,900
1,500
Ending
Period Month Demand Production Inventory Stockouts (Units)
0 December
200
1 January
1,500
500
2 February
1,700
300
M
3 March
1,700
300
4 April
1,700
300
5 May
2,300
0
6 June
2,100
0
7
July
1,900
100
8 August
500
1,500
1,800
1,800
1,800
1,800
1,800
1,800
1,800
1,800
ܘ ܘ ܘ ܘ
300
100
0
0
Solution
by Bartleby Expert
Knowledge Booster
Similar questions
- Deb Bishop Health and Beauty Products has developed a new shampoo and you need to develop its aggregate schedule. The cost accounting department has supplied you the cost relevant to the aggregate plan and the marketing department has provided a four-quarter forecast. the four-quarter forecast. Quarter Forecast 1 1,400 2 1,100 3 1,700 4 1,300 aggregate plan. Costs Previous quarter's output 1,600 units Beginning inventory 0 units Stockout cost for backorders $55 per unit Inventory holding cost $11 per unit for every unit held at the end of the quarter Hiring workers $50 per unit Layoff workers $75 per unit Unit cost $35 per unit Overtime $20 extra per unit Subcontracting Not available Your job is to develop an aggregate plan for the next four quarters. Part 2 a) Try hiring and layoffs (to meet the forecast) as necessary (enter your responses as whole…arrow_forwardAn X product is composed of A, B, C items. The aggregate plan for February and some of the information are provided as follows. Prepare the master production schedule.arrow_forwardPlease help me answer this question. Please provide solution/computation.arrow_forward
- Id-6c An aggregate plan provides justification for: Select one: a. the budget amount requested b. demand for individual products c. demand for product families d. the demand for the parts of each product and. number of customersarrow_forwardDevelop a production plan and calculate the annual cost for a firm whose demand forecast is fall, 11,000; winter, 8,000; spring, 6,000; summer, 13,000. Inventory at the beginning of fall is 500 units. At the beginning of fall you currently have 30 workers, but you plan to hire temporary workers at the beginning of summer and lay them off at the end of summer. In addition, you have negotiated with the union an option to use the regular workforce on overtime during winter or spring if overtime is necessary to prevent stockouts at the end of those quarters. Overtime is not available during the fall. Relevant costs are hiring, $100 for each temp; layoff $200 for each worker laid off; inventory holding, $5 per unit-quarter; backorder, $10 per unit; straight time, $5 per hour; overtime, $8 per hour. Assume that the productivity is 0.5 unit per worker hour, with eight hours per day and 60 days per season. a. What is the total cost for this plan?arrow_forwardDevelop a production schedule to produce the exact production requirements by varying the workforce size for the following problem. The monthly forecasts for Product X for January, February, and March are 940, 1,520, and 1,230, respectively. Safety stock policy recommends that half of the forecast for that month be defined as safety stock. There are 22 working days in January, 19 in February, and 21 in March. Beginning inventory is 570 units. Manufacturing cost is $170 per unit, storage cost is $5 per unit per month, standard pay rate is $8 per hour, overtime rate is $12 per hour, cost of stock-out is $9 per unit per month, marginal cost of subcontracting is $8 per unit, hiring and training cost is $160 per worker, layoff cost is $260 per worker, and worker productivity is 0.1 unit per hour. Assume that you start off with 44 workers and that they work 8 hours per day. (Leave the cells blank, whenever zero (0) is required. Input all values as positive values. Round up "Workers Required"…arrow_forward
- The president of Hill Enterprises, Terri Hill, projects the firm's aggregate demand requirements over the next 8 months as follows: January 1,400 May 2,300 February 1,700 June 2,100 March 1,600 July 1,900 April 1,700 August 1,300 Her operations manager is considering a new plan, which begins in January with 200units on hand and ends with zero inventory. Stockout cost of lost sales is $125per unit. Inventory holding cost is $25per unit per month. Ignore any idle-time costs. The plan is called plan B. Plan B: Produce at a constant rate of 1,300units per month, which will meet minimum demands. Then use subcontracting, with additional units at a premium price of $75per unit. Subcontracting capacity is limited to 1,000units per month. Evaluate this plan by computing the costs for January through August. Part 2 In order to arrive at the costs, first compute the ending inventory and subcontracting units for each month by…arrow_forwarda) GOT7 Soda Pop, Inc., has a new fruits drink. The production planner has assembled the following cost data and demand forecast as follow: [GOT7 Soda Pop, Inc., mempunyai minuman buah-buahan yang baru, Perancang pengeluaran telah mengumpul data tentang kos dan ramalan permintaan seperti berikut:] Quarter Demand 1,800 First Second 1,200 Third 1,600 Fourth 1,300 Table 1: Cost and demand forecast [Jadual 1: Kos dan ramalan permintaan] Previous quater's output 1,300 cases Beginning inventory 0 cases Stockout cost Inventory holding cost Hiring employees Terminating employees Subcontracting cost Unit cost on regular time Overtime cost RM150 RM40 per case at the end of quater RM40 per case RM80 per case RM60 per case RM30 per case RM15 extra per case You as the production planner need to develop an aggregate planning. You are required to: [Anda sebagai perancang pengeluaran perlu membangunkan perancangan agregat Anda dikehendaki untuk:] i) Assess plan A: strategy that hires and fires…arrow_forwarda. Produce utilizing a level strategy at 180 units in which the company incurs regular time production costs, inventory charges and any costs due to the change in the production level from the previous output level. What is the cost of this strategy? [Select] b. Was there a need to back-order? If so, how many units? [Select] c. Produce utilizing a mixed strategy by producing 160 units every month. Then, utilize overtime, and subcontracting to meet demand. (Don't forget the capacity limitations on overtime and subcontracting.) What is the cost of this strategy? [Select] d. Based on the mixed strategy, what was the cost of utilizing overtime [Select] e. Based on a strategy of varying the workforce (Chase), what is the total cost? [Select] f. Which strategy provides the lowest cost solution? [Select]arrow_forward
- I do not understand this. Please help me get the answer. Please provide the solution/computation.arrow_forwardDemand for stereo headphones and MP3 players for joggers has caused Nina Industries to grow almost 50 percent over the past year. The number of joggers continues to expand, so Nina expects demand for headsets to also expand, because, as yet, no safety laws have been passed to prevent joggers from wearing them. Demand for the players for last year was as follows: MONTH DEMAND (UNITS) January 4,240 February 4,340 March 4,040 April 4,440 May 5,040 June 4,740 July 5,340 August 4,940 September 5,440 October 5,740 November 6,335 December 6,030 a. Using linear regression analysis, what would you estimate demand to be for each month next year? (Do not round intermediate calculations. Round your answers to 2 decimal places.) b. To be reasonably confident of meeting demand, Nina decides to use 4 standard errors of estimate for safety. How many additional units should be held to meet this level of confidence? (Do not round intermediate calculations. Round…arrow_forwardPrepare a master schedule based on the following information: Week 1 2 3 4 5 6 7 8 Forecast 500 500 600 600 750 750 900 800 Orders 540 470 325 200 105 45 10 0 Currently there are 700 units in inventory. Policy calls for a fixed order quantity of 1250 units. Can you receive another order for 250 items in week 1? Why? How many orders can be received in each period without altering the plan. If there are 1250 items in stock, what would be the answer of questions 2 and 3?arrow_forward
arrow_back_ios
SEE MORE QUESTIONS
arrow_forward_ios
Recommended textbooks for you
- Practical Management ScienceOperations ManagementISBN:9781337406659Author:WINSTON, Wayne L.Publisher:Cengage,Operations ManagementOperations ManagementISBN:9781259667473Author:William J StevensonPublisher:McGraw-Hill EducationOperations and Supply Chain Management (Mcgraw-hi...Operations ManagementISBN:9781259666100Author:F. Robert Jacobs, Richard B ChasePublisher:McGraw-Hill Education
- Purchasing and Supply Chain ManagementOperations ManagementISBN:9781285869681Author:Robert M. Monczka, Robert B. Handfield, Larry C. Giunipero, James L. PattersonPublisher:Cengage LearningProduction and Operations Analysis, Seventh Editi...Operations ManagementISBN:9781478623069Author:Steven Nahmias, Tava Lennon OlsenPublisher:Waveland Press, Inc.
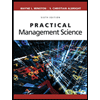
Practical Management Science
Operations Management
ISBN:9781337406659
Author:WINSTON, Wayne L.
Publisher:Cengage,
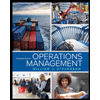
Operations Management
Operations Management
ISBN:9781259667473
Author:William J Stevenson
Publisher:McGraw-Hill Education
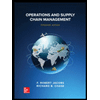
Operations and Supply Chain Management (Mcgraw-hi...
Operations Management
ISBN:9781259666100
Author:F. Robert Jacobs, Richard B Chase
Publisher:McGraw-Hill Education
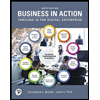
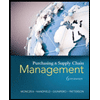
Purchasing and Supply Chain Management
Operations Management
ISBN:9781285869681
Author:Robert M. Monczka, Robert B. Handfield, Larry C. Giunipero, James L. Patterson
Publisher:Cengage Learning
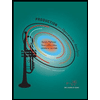
Production and Operations Analysis, Seventh Editi...
Operations Management
ISBN:9781478623069
Author:Steven Nahmias, Tava Lennon Olsen
Publisher:Waveland Press, Inc.