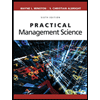
Concept explainers
Lunar Co.Ltd's estimated demand for the next 6 months in 2021 is as follows:
Month | Demand |
July | 1500 |
August | 1700 |
September | 2000 |
October | 1800 |
November | 2200 |
December | 1500 |
Management considers 2 aggregate plans as follows:
a. Perform variations in the number of workers according to the level of demand. The current average production is 1500 units/month. Labor procurement costs $500,000 per 100 units,
while the cost of reducing labor is $750,000 per 100 units.
b. Keeping production levels constant at an average of 1500 units/month (to meet minimum demand) and to meet demand shortages through subcontracting at a marginal cost of $5,000 per unit. Subcontracting can only be done in a number of 500 units. Demand that cannot be met by production and subcontracting is a loss of sales and calculated at $5,000 per unit.
In your opinion, as the company's operational manager, which plan should the company take (from points a & b above) so that the company can achieve production efficiency? Explain, why?

Trending nowThis is a popular solution!
Step by stepSolved in 2 steps with 2 images

- DAT, Inc., needs to develop an aggregate plan for its product line. Relevant data are Management prefers to keep a constant workforce and production level, absorbingvariations in demand through inventory excesses and shortages. Demand not met is carriedover to the following month.Develop an aggregate plan that will meet the demand and other conditions of theproblem. Do not try to i nd the optimum; just i nd a good solution and state the procedureyou might use to test for a better solution. Make any necessary assumptions.arrow_forwardLMNO Gaskets has formulated a production plan for a product to meet demand over the upcoming four quarters. Demand in each of the four quarters and production, overtime, and subcontracting capacities are reported in the table below, in addition to the feasible production plan. The relevant costs are: • Regular time production cost is $10/unit. Overtime production cost is $14/unit. Subcontracting cost is $18/unit Inventory is held at a cost of $1/unit/quarter. • Units may be backordered at a cost of $4/unit/quarter. Production Resource Regular Time Q1 Overtime Q1 Subcontract Q1 Regular Time Q2 Overtime Q2 Subcontract Q2 Regular Time Q3 Overtime Q3 Subcontract Q3 Demand in Quarter Demand in Quarter Q2 0 20 0 550 Q1 550 230 0 0 0 0 40 40 0 860 250 470 0 40 0 1330 What is the inventory cost for the year? What is the backorder cost for the year? What is the total cost for the year? Q3 0 0 0 0 0 30 510 160 0 700 What is the total overtime production cost for the year? Capacity 550 250 500…arrow_forward5. Formulate a level sales and operations plan for a company with the following predicted demand: Month Demand 6,300 2 9,000 3 6,000 4 9,000 5 15,000 6 6,000 Total 51,300 The beginning workforce is 125 employees. The monthly output per employee is 150 units. The costs to hire and lay off a worker are $2,500 and $4,000, respectively. The cost to carry an item in inventory for one month is estimated at $10, and the stockout cost is $25 per unit. Show the production schedule, the inventory levels, and the changes in workforce from period to period. Compute the plan's cost.arrow_forward
- Shoney Video Concepts produces a line of video streaming servers that are linked to personal computers for storing movies. These devices have very fast access and large storage capacity. Shoney is trying to determine a production plan for the next 12 months. The main criterion for this plan is that the employment level is to be held constant over the period. Shoney is continuing in its R&D efforts to develop new applications and prefers not to cause any adverse feelings with the local workforce. For the same reason, all employees should put in full workweeks, even if that is not the lowest-cost alternative. The forecast for the next 12 months is MONTH FORECAST DEMAND January 550 February 750 March 850 April 550 May 350 June 250 July 150 August 150 September 250 October 650 November 750 December 830 Manufacturing cost is $200 per server, equally divided between materials and labor. Inventory storage cost is $4 per unit per month and is assigned based…arrow_forwardOnly typed explanation otherwise leave itarrow_forwardDirections Select one of these concepts: How the Aggregate Operations Plan combines required materials, capacity, and staffing. Inputs and application of the different Production Planning Strategies: Chase strategy, level strategy, Stable workforce Aggregate planning techniques that minimize the costs of operations. Application of Materials Requirement Planning methods as a manufacturing scheduling tool Use of Bills of Materials and Lot Sizing in MRP systemsarrow_forward
- The S&OP team at Kansas Furniture, led by David Angelow, has received estimates of demand requirements as shown in the table. Assuming one-time stockout costs for lost sales of $125 per unit, Kinventory carrying costs of $25 per unit per month, and zero beginning and ending inventory, evaluate the following plan on an incremental cost basis: Plan B: Vary the workforce to produce the prior month's demand. Demand was 1,300 units in June. The cost of hiring additional workers is $30 per unit produced. The cost of layoffs is $65 per unit cut back. (Enter all responses as whole numbers.) Note: Both hiring and layoff costs are incurred in the month of the change (i.e., going from production of 1,300 in July to 1200 in August requires a layoff (and related costs) of 100 units in August). Stockouts (Units) Month 1 July Demand 1200 Hire Production (Units) Layoff Ending (Units) Inventory 2 August 1300 3 September 1200 4 October 1700 5 November 1650 6 December 1650arrow_forwardc7 need urgent in 15 minutesarrow_forwardCalculate the turnover for the Fall season if the sales are planned at $215,800 and the average inventory is $189,180.arrow_forward
- JAYB, manager of a Fabrication company, has the following aggregate demand requirements and other data for the upcoming four quarters. Table 5: Forecast and cost information [Jadual 5: Maklumat Ramalan dan kos] Quarter [Suku] Demand [Permintaan] Previous quarter's output [Keluaran suku sebelumnya] 1,500 units 1 1,400 Beginning inventory [Inventori awal] 200 units 2 1,000 Hiring workers [Pengambilan pekerja] RM6 per unit 3 1,500 Laying off workers [Pembuangan pekerja] RM11 per unit 4 1,300 Unit cost [Kos unit] RM30 per unit With the information given, JAYB wants you to calculate the total cost of using chase strategy by hiring and layoff workers.arrow_forwardc6 need urgent in 15 minutesarrow_forwardJataarrow_forward
- Practical Management ScienceOperations ManagementISBN:9781337406659Author:WINSTON, Wayne L.Publisher:Cengage,Operations ManagementOperations ManagementISBN:9781259667473Author:William J StevensonPublisher:McGraw-Hill EducationOperations and Supply Chain Management (Mcgraw-hi...Operations ManagementISBN:9781259666100Author:F. Robert Jacobs, Richard B ChasePublisher:McGraw-Hill Education
- Purchasing and Supply Chain ManagementOperations ManagementISBN:9781285869681Author:Robert M. Monczka, Robert B. Handfield, Larry C. Giunipero, James L. PattersonPublisher:Cengage LearningProduction and Operations Analysis, Seventh Editi...Operations ManagementISBN:9781478623069Author:Steven Nahmias, Tava Lennon OlsenPublisher:Waveland Press, Inc.
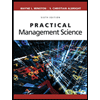
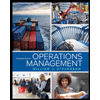
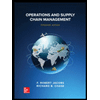
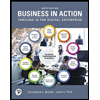
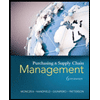
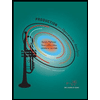