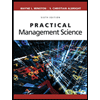
Practical Management Science
6th Edition
ISBN: 9781337406659
Author: WINSTON, Wayne L.
Publisher: Cengage,
expand_more
expand_more
format_list_bulleted
Concept explainers
Question
A. What are some sources of demand variation
B. Describe three classical strategies for capacity and demand planning and management
Expert Solution

This question has been solved!
Explore an expertly crafted, step-by-step solution for a thorough understanding of key concepts.
Step by stepSolved in 2 steps

Knowledge Booster
Learn more about
Need a deep-dive on the concept behind this application? Look no further. Learn more about this topic, operations-management and related others by exploring similar questions and additional content below.Similar questions
- A B с D E F G H J 1234567 FCB Inc. has the following aggregate demand requirements and other data for the upcoming four quarters: Production Data (in units) Previous quarter's output 6 Beginning inventory 8 Cost Data (per unit) Stockout cost 1500 0 9 10 Inventory holding cost (at the end of the quarter) $ 11 Hiring workers 12 Firing workers $ 13 Unit cost 14 15 Overtime $ sssss es ese $ 50.00 10.00 $ 40.00 80.00 $ 30.00 15.00 16 Quarter Demand 17 18 19 20 21 31 222222 23456782033 29 1 2 3 4 1,400 1,200 1,500 1,300 Time period Demand Regular Overtime Production Production Ending Inventory Available inventory Lost sale Backorder/ Change in production/workers Increase in produciton (Hire Previous Plan Q1 Q2 Q3 Q4 Total: Cost: Total cost of plan:arrow_forwardWhat role does demand variability play in the Wilson Approach, and how can it be managed effectively?arrow_forwardHau Lee Furniture, Inc., spends 45% of its sales dollars in the supply chain and finds its current profit of $15,000 inadequate. The bank is insisting on an improved profit picture prior to approval of a loan for some new equipment. Hau would like to improve the profit line to $20,000 so he can obtain the bank's approval for the loan. Sales Cost of material Current Situation $100,000 $45,000 (45%) Production costs Fixed cost Profit $25,000 (25%) $15,000 (15%) $15,000 (15%) a) What percentage improvement is needed in the supply chain strategy for profit to improve to $20,000? What is the cost of material with a $20,000 profit? A decrease of ☐ % in material (supply-chain) costs is required to yield a profit of $20,000, for a new material cost of (Enter your response for the percentage decrease to one decimal place and enter your response for the new material cost as a whole number.)arrow_forward
- Q1) Evaluate each plan and find out which one is better in terms of total costs - Plan 1: for the manufacturer is to maintain a constant workforce throughout the 6-month period. we assume that the production per day is average requirements ( average production per day) and that we have a constant workforce, no overtime or idle time, no safety stock, and no subcontractors. The firm accumulates inventory during the slack period of demand, January through March, and depletes it during the higher-demand warm season, April through June. We assume beginning inventory = 0 and planned ending inventory = 0. - Plan 2: is to maintain a constant workforce at a level necessary to meet the lowest demand month ( February ) and to meet all demand above this level by subcontracting. Please use the following information : Inventory carrying cost $ 3 per unit per month Subcontracting cost per unit $17 per unit Average pay rate $10 per hour ($80 per day - 8 working hours per day)…arrow_forwardWal Mart, although they are not a manufacturing company, uses sophisticated computer software to forecast sales and order products to be stocked in their stores so that they do not run out of the things shoppers are looking for. What kind of software system does Wal Mart likely use? Group of answer choices a) Inventory control b) Just-in-time ordering c) E-procurement d) Materials Requirement Planning (MRP)arrow_forwardHelp please.arrow_forward
- 12arrow_forwardLMNO Gaskets has formulated a production plan for a product to meet demand over the upcoming four quarters. Demand in each of the four quarters and production, overtime, and subcontracting capacities are reported in the table below, in addition to the feasible production plan. The relevant costs are: • Regular time production cost is $10/unit. Overtime production cost is $14/unit. Subcontracting cost is $18/unit Inventory is held at a cost of $1/unit/quarter. • Units may be backordered at a cost of $4/unit/quarter. Production Resource Regular Time Q1 Overtime Q1 Subcontract Q1 Regular Time Q2 Overtime Q2 Subcontract Q2 Regular Time Q3 Overtime Q3 Subcontract Q3 Demand in Quarter Demand in Quarter Q2 0 20 0 550 Q1 550 230 0 0 0 0 40 40 0 860 250 470 0 40 0 1330 What is the inventory cost for the year? What is the backorder cost for the year? What is the total cost for the year? Q3 0 0 0 0 0 30 510 160 0 700 What is the total overtime production cost for the year? Capacity 550 250 500…arrow_forwardThe planner at a company that makes garden tractors is about to prepare an aggregate production plan that will cover the next 6 months. She has collected the following information: Month Demand Forecast Above the available capacity through permanent workforce 1 1,000 2 1,000 3 2,000 4 3,000 5 4,000 6 1,000 Total: 12,000 Production per month = 20 units per worker Initial inventory = 500 units Desired ending inventory (at the end of month 6) = 0 units Cost: Hire cost = $500 per temporary worker Inventory = $10 per tractor per month Backorder = $150 per tractor per month The optimum aggregate plan is: Month 1 2 3 4 5 6 Total Forecast Demand above regular capacity 1,000 1,000 2,000 3,000 4,000 1,000 12,000 # of temporary workers required 50 50 100 150 200 50 Temp. Workers hired 25 25 50 75 0 0 Temp. workers laid off 0…arrow_forward
- 5. Formulate a level sales and operations plan for a company with the following predicted demand: Month Demand 6,300 2 9,000 3 6,000 4 9,000 5 15,000 6 6,000 Total 51,300 The beginning workforce is 125 employees. The monthly output per employee is 150 units. The costs to hire and lay off a worker are $2,500 and $4,000, respectively. The cost to carry an item in inventory for one month is estimated at $10, and the stockout cost is $25 per unit. Show the production schedule, the inventory levels, and the changes in workforce from period to period. Compute the plan's cost.arrow_forwardHau Lee Fumiture, Inc., spends 45% of its sales dollars in the supply chain and finds its current profit of $24,000 inadequate. The bank is insisting on an improved profit picture prior to approval of a loan for some new equipment. Hau would like to improve the profit line to $29,000 so he can obtain the bank's approval for the loan. Sales Cost of material Production costs Fixed cost Profit Current Situation $80,000 $36,000 (45%) $16,000 (20%) $4,000 (5%) $24,000 (30%) a) What percentage improvement is needed in the supply chain strategy for profit to improve to $29,000? What is the cost of material with a $29,000 profit? A decrease of % in material (supply-chain) costs is required to yield a profit of $29,000, for a new material cost of $ cost as a whole number.) (Enter your response for the percentage decrease to one decimal place and enter your response for the new materialarrow_forwardLet’s say that Glass For Sale, Inc. manufacturers replacement glass for the home remodelingindustry. In January, the company produces fifteen-thousand windows and ended the monthwith nine-thousand windows in inventory. Glass For Sale’s management team would like to develop a production schedule for the next three months. A smooth production schedule is obviously desirable due to the fact that it maintains the current workforce and provides a similar month-to-month operation. However, given the sales forecasts, the production capacities, and the storage capabilities as shown in Table two, the management teamdoes not think a smooth production schedule with the same production quantity each month is possible. The company’s cost accounting department estimates that increasing production by one window from one month to the next will increase total costs by one dollar for each unit increase in the production level. In addition, decreasing production by one unit from one month to the next…arrow_forward
arrow_back_ios
SEE MORE QUESTIONS
arrow_forward_ios
Recommended textbooks for you
- Practical Management ScienceOperations ManagementISBN:9781337406659Author:WINSTON, Wayne L.Publisher:Cengage,Operations ManagementOperations ManagementISBN:9781259667473Author:William J StevensonPublisher:McGraw-Hill EducationOperations and Supply Chain Management (Mcgraw-hi...Operations ManagementISBN:9781259666100Author:F. Robert Jacobs, Richard B ChasePublisher:McGraw-Hill Education
- Purchasing and Supply Chain ManagementOperations ManagementISBN:9781285869681Author:Robert M. Monczka, Robert B. Handfield, Larry C. Giunipero, James L. PattersonPublisher:Cengage LearningProduction and Operations Analysis, Seventh Editi...Operations ManagementISBN:9781478623069Author:Steven Nahmias, Tava Lennon OlsenPublisher:Waveland Press, Inc.
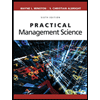
Practical Management Science
Operations Management
ISBN:9781337406659
Author:WINSTON, Wayne L.
Publisher:Cengage,
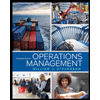
Operations Management
Operations Management
ISBN:9781259667473
Author:William J Stevenson
Publisher:McGraw-Hill Education
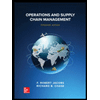
Operations and Supply Chain Management (Mcgraw-hi...
Operations Management
ISBN:9781259666100
Author:F. Robert Jacobs, Richard B Chase
Publisher:McGraw-Hill Education
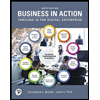
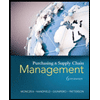
Purchasing and Supply Chain Management
Operations Management
ISBN:9781285869681
Author:Robert M. Monczka, Robert B. Handfield, Larry C. Giunipero, James L. Patterson
Publisher:Cengage Learning
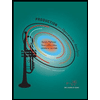
Production and Operations Analysis, Seventh Editi...
Operations Management
ISBN:9781478623069
Author:Steven Nahmias, Tava Lennon Olsen
Publisher:Waveland Press, Inc.