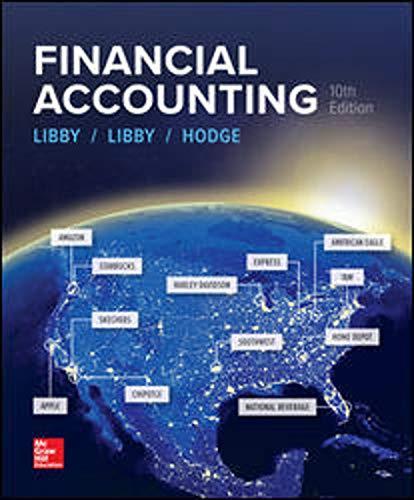
FINANCIAL ACCOUNTING
10th Edition
ISBN: 9781259964947
Author: Libby
Publisher: MCG
expand_more
expand_more
format_list_bulleted
Concept explainers
Question
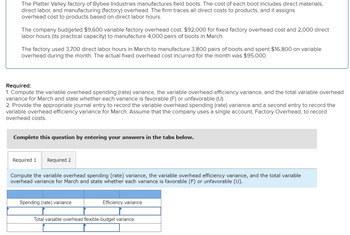
Transcribed Image Text:The Platter Valley factory of Bybee Industries manufactures field boots. The cost of each boot includes direct materials,
direct labor, and manufacturing (factory) overhead. The firm traces all direct costs to products, and it assigns
overhead cost to products based on direct labor hours.
The company budgeted $9,600 variable factory overhead cost, $92,000 for fixed factory overhead cost and 2,000 direct
labor hours (its practical capacity) to manufacture 4,000 pairs of boots in March.
The factory used 3,700 direct labor hours in March to manufacture 3,800 pairs of boots and spent $16,800 on variable
overhead during the month. The actual fixed overhead cost incurred for the month was $95,000.
Required:
1. Compute the variable overhead spending (rate) variance, the variable overhead efficiency variance, and the total variable overhead
variance for March and state whether each variance is favorable (F) or unfavorable (U).
2. Provide the appropriate journal entry to record the variable overhead spending (rate) variance and a second entry to record the
variable overhead efficiency variance for March. Assume that the company uses a single account, Factory Overhead, to record
overhead costs.
Complete this question by entering your answers in the tabs below.
Required 1 Required 2
Compute the variable overhead spending (rate) variance, the variable overhead efficiency variance, and the total variable
overhead variance for March and state whether each variance is favorable (F) or unfavorable (U).
Spending (rate) variance
Efficiency variance
Total variable overhead flexible-budget variance
Expert Solution

This question has been solved!
Explore an expertly crafted, step-by-step solution for a thorough understanding of key concepts.
Step by stepSolved in 4 steps with 3 images

Knowledge Booster
Learn more about
Need a deep-dive on the concept behind this application? Look no further. Learn more about this topic, accounting and related others by exploring similar questions and additional content below.Similar questions
- Power company manufactures a variety of drill bits. The company's plant is partially automated. The budget for the year includes $492,000 payroll for 5400 direct labor-hours. Listed below is cost driver information use in the product-costing system:arrow_forwardThe Shoe For You Company manufactures two types of shoes; dress and casual shoes. For the month of May, the company plans to produce 21,000 pairs of dress shoes and 17,500 pairs of casual shoes. Both types of shoes are produced in the assembling and finishing departments. The direct labor rates for assembling and finishing departments are $13.00 per hour and $17.50 per hour, respectively. The following table indicates the amount of direct labor hours required for each type of shoe: Assembling Finishing Dress shoes 15 minutes per pair 30 minutes per pair Casual shoes 12 minutes per pair 15 minutes per pair Calculate the budgeted direct labor cost for dress shoes.arrow_forwardThe Gilster Company, a machine tooling firm, has several plants. One plant, located in St. Cloud, Minnesota, uses a job order costing system for its batch production processes. The St. Cloud plant has two departments through which most jobs pass. Plant-wide overhead, which includes the plant manager’s salary, accounting personnel, cafeteria, and human resources, is budgeted at $400,000. During the past year, actual plantwide overhead was $385,000. Each department’s overhead consists primarily of depreciation and other machine-related expenses. Selected budgeted and actual data from the St. Cloud plant for the past year are as follows. Department A Department B Budgeted department overhead (excludes plantwide overhead) $ 153,000 $ 439,900 Actual department overhead 170,000 459,900 Expected total activity: Direct labor hours 50,000 25,000 Machine-hours 15,000 53,000 Actual activity:…arrow_forward
- i need the answer quicklyarrow_forwardKaumajet Factory produces two products: table lamps and desk lamps. It has two separate departments: Fabrication and Assembly. The factory overhead budget for the Fabrication Department is $324,156, using 272,400 direct labor hours. The factory overhead budget for the Assembly Department is $295,263, using 61,900 direct labor hours. If a desk lamp requires 2 hours of fabrication and 5 hours of assembly, the amount of factory overhead that Kaumajet Factory will allocate to each unit of desk lamp using the multiple production department factory overhead rate method with an allocation base of direct labor hours is a.$4.77 b.$10.01 c.$70.05 d.$26.23arrow_forwardCarter Company manufactures two products, Deluxe and Regular, and uses a traditional two-stage cost allocation system. The first stage assigns all factory overhead costs to two production departments, A and B. based on machine hours. The second stage uses direct labor hours to allocate overhead to individual products. For the current year, the firm budgeted $1,550,000 total factory overhead cost. The $1,550,000 was for the planned levels of machine and direct labor hours shown in the following table. Machine hours Direct labor hours Units produced and sold Unit cost of direct materials The following information relates to the firm's operations for the month of January: Hourly direct labor wage rate Direct labor hours in Department A per unit Direct labor hours in Department B per unit Activity Material movement Machine setups Inspections Shipment Production Production Department A Department B 6,200 31,000 1. Deluxe unit cost Regular unit cost 2. Deluxe unit overhead Regular unit…arrow_forward
- Coronado Company produces high-quality microscopes for education and health care uses. The company uses a job order costing system. Because the microscopes’ optics require significant manual labor to ensure adherence to strict manufacturing specifications, the company applies overhead on the basis of direct labor hours. At the beginning of 2021, the company estimated its manufacturing overhead would be $1,960,000 and that employees would work a total of 49,000 direct labor hours. During March, the company worked on the following five jobs: Job BeginningBalance Direct Materialsadded duringMarch Direct Laboradded duringMarch Direct Labor Hoursadded duringMarch 134 $120,600 $6,000 $9,400 140 158 125,450 3,500 12,160 450 212 21,800 88,400 36,650 3,500 287 36,350 71,800 31,850 2,550 301 18,990 21,845 1,400 Total $304,200 $188,690 $111,905 8,040 Jobs 134 and 158 were started in January,…arrow_forwardThe Gidget Company produces a variety of styles of gidgets, and measures total output as the standard hours allowed for actual output. Gidget Company's manufacturing overhead budget calls for $50,000 of fixed overhead for the year plus $10 per direct labor hour. Last year the Gidget Company produced 11,000 standard hours of output. Actual manufacturing overhead for the year amounted to $53,000 of fixed overhead and the Gidget Company used 8,000 direct labor hours. The Gidget Company uses standard direct labor hours allowed as a basis for allocating overhead and uses 10,000 direct labor hours as its denominator volume. Calculate the production volume variance:arrow_forwardCozy, Inc., manufactures small and large blankets. It estimates $350,000 in overhead during the manufacturing of 75,000 small blankets and 25,000 large blankets. What is the predetermined overhead rate if a small blanket takes 1 machine hour and a large blanket takes 2 machine hours?arrow_forward
- Marvel Parts, Incorporated, manufactures auto accessories including a set of seat covers that can be adjusted to fit most cars. According to its standards, the factory should work 1,015 hours each month to produce 2,030 sets of seat covers. The standard costs associated with this level of production are: Direct materials Direct labor Variable manufacturing overhead (based on direct labor-hours) Direct materials (8,400 yards) Direct labor Variable manufacturing overhead Total $ 59,276 $ 8,120 $ 3,857 1. Materials price vanance 1. Materials quantity variance 2. Labor rate variance 2 Labor efficiency variance 3. Vanable overhead rate variance 3. Variable overhead efficiency variance Per Set of Covers During August, the factory worked 700 direct labor-hours and produced 1,500 sets of covers. The following actual costs were recorded during the month: Total $ 42,000 $ 6,300 $3,150 $ 29.20 4.00 1.90 $ 35.10 Per Set of Covers $28.00 4.20 2.10 $34.30 At standard, each set of covers should…arrow_forwardRequired Information [The following information applies to the questions displayed below.] The Platter Valley factory of Bybee Industries manufactures field boots. The cost of each boot includes direct materials, direct labor, and manufacturing (factory) overhead. The firm traces all direct costs to products, and it assigns overhead cost to products based on direct labor hours. The company budgeted $15,000 variable factory overhead cost, $90,000 for fixed factory overhead cost and 2,500 direct labor hours (its practical capacity) to manufacture 5,000 pairs of boots in March. The factory used 2,700 direct labor hours in March to manufacture 4,800 pairs of boots and spent $15,600 on variable overhead during the month. The actual fixed overhead cost incurred for the month was $92,000. The Platter Valley factory of Bybee Industries uses a two-variance analysis of the total factory overhead variance. Required: 1. Compute the total flexible-budget variance for overhead and the production…arrow_forwardSifton Electronics Corporation manufactures and assembles electronic motor drives for video cameras. The company assembles the motor drives for several accounts. The process consists of a lean cell for each customer. The following information relates to only one customer's lean cell for the coming year. For the year, projected labor and overhead was $5,154,500 and materials costs were $34 per unit. Planned production included 5,408 hours to produce 16,900 motor drives. Actual production for August was 1,820 units, and motor drives shipped amounted to 1,400 units. Conversion costs are applied based on units of production From the foregoing information, determine the amount of the conversion costs charged to Raw and In Process Inventory during August. Oa. $555,100 Ob. $556,954 Oc. $235,349 Od. $128,100arrow_forward
arrow_back_ios
SEE MORE QUESTIONS
arrow_forward_ios
Recommended textbooks for you
- AccountingAccountingISBN:9781337272094Author:WARREN, Carl S., Reeve, James M., Duchac, Jonathan E.Publisher:Cengage Learning,Accounting Information SystemsAccountingISBN:9781337619202Author:Hall, James A.Publisher:Cengage Learning,
- Horngren's Cost Accounting: A Managerial Emphasis...AccountingISBN:9780134475585Author:Srikant M. Datar, Madhav V. RajanPublisher:PEARSONIntermediate AccountingAccountingISBN:9781259722660Author:J. David Spiceland, Mark W. Nelson, Wayne M ThomasPublisher:McGraw-Hill EducationFinancial and Managerial AccountingAccountingISBN:9781259726705Author:John J Wild, Ken W. Shaw, Barbara Chiappetta Fundamental Accounting PrinciplesPublisher:McGraw-Hill Education
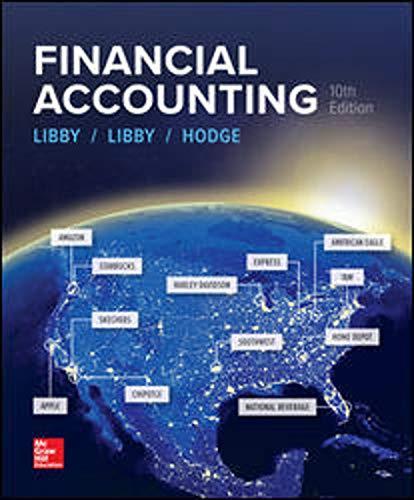
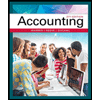
Accounting
Accounting
ISBN:9781337272094
Author:WARREN, Carl S., Reeve, James M., Duchac, Jonathan E.
Publisher:Cengage Learning,
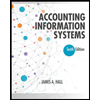
Accounting Information Systems
Accounting
ISBN:9781337619202
Author:Hall, James A.
Publisher:Cengage Learning,
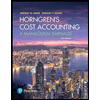
Horngren's Cost Accounting: A Managerial Emphasis...
Accounting
ISBN:9780134475585
Author:Srikant M. Datar, Madhav V. Rajan
Publisher:PEARSON
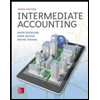
Intermediate Accounting
Accounting
ISBN:9781259722660
Author:J. David Spiceland, Mark W. Nelson, Wayne M Thomas
Publisher:McGraw-Hill Education
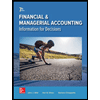
Financial and Managerial Accounting
Accounting
ISBN:9781259726705
Author:John J Wild, Ken W. Shaw, Barbara Chiappetta Fundamental Accounting Principles
Publisher:McGraw-Hill Education