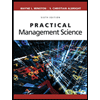
Concept explainers
The Donald Fertilizer Company produces industrial chemical fertilizers. The projected manufacturing requirements (in thousands of gallons) for the next four quarters are 80, 50, 80, and 130, respectively. A level workforce is desired, relying only on anticipation inventory as a supply option. Stockouts and backorders are to be avoided, as are overtime and undertime.
a. Determine the quarterly production rate required to meet total demand for the year, and minimize the anticipation inventory that would be left over at the end of the year. Beginning inventory is zero.
b. Specify the anticipation inventory that will be produced.
c. Suppose that the requirements for the next four quarters are revised to 80, 130, 50, and 80, respectively. If total demand is the same, what level of production rate is needed now, using the same strategy as part (a)?

Trending nowThis is a popular solution!
Step by stepSolved in 3 steps with 6 images

- Complete the MPS record below for a single item. (Enter your responses as integers. A response of "0" is equivalent to being not applicable.) Item: A Quantity on Hand: 80 Forecast Customer orders (booked) Projected on-hand inventory MPS quantity 1 70 40 ☐☐ January 2 70 65 80 Order Policy: 100 units Lead Time: 1 week February Week 4 40 0 5 45 35 50 70 45 0 8 50 0arrow_forwardOQ18arrow_forwardDevelop a production plan and calculate the annual cost for a firm whose demand forecast is fall, 11,000; winter, 8,000; spring, 6,000; summer, 13,000. Inventory at the beginning of fall is 500 units. At the beginning of fall you currently have 30 workers, but you plan to hire temporary workers at the beginning of summer and lay them off at the end of summer. In addition, you have negotiated with the union an option to use the regular workforce on overtime during winter or spring if overtime is necessary to prevent stockouts at the end of those quarters. Overtime is not available during the fall. Relevant costs are hiring, $100 for each temp; layoff $200 for each worker laid off; inventory holding, $5 per unit-quarter; backorder, $10 per unit; straight time, $5 per hour; overtime, $8 per hour. Assume that the productivity is 0.5 unit per worker hour, with eight hours per day and 60 days per season. a. What is the total cost for this plan?arrow_forward
- Using the cut-and-try method for aggregate operations planning, as described in the textbook, we can calculate the production requirement in units of output. If beginning inventory = 500 units, demand forecast is 1,000 units and safety stock is set at 10% of the demand forecast, then the production requirement equals: a) 600 b) 100 c) 550 d) 1,000 e) 450arrow_forwardThe total planned expenditures is called as aggregate demand Select one: True Falsearrow_forwardAssume an initial starting Ft of 200 units, a trend (Tt ) of 8 units, an alpha of 0.30, and a delta of 0.40. If actual demand turned out to be 288, calculate the forecast including trend for the next period.arrow_forward
- A small textile company makes several types of sweat-ers. Demand is very seasonal, as shown by the follow-ing quarterly demand estimates. Demand is estimated interms of standard hours of production required.An hour of regular time costs the company $12. Employees are paid $18 per hour on overtime, andlabor can be subcontracted from the outside at $14per hour. A maximum of 1000 overtime hours isavailable in any month. A change in the regular level of production (increase or decrease) incurs a one-time cost of $5 per hour for adding or subtracting anhour of labor. It costs 2 percent per month to carry an hour of finished work in inventory. Materials and overhead costs in inventory are equal to the directlabor costs. At the beginning of the fall quarter,there are 5000 standard hours in inventory and theworkforce level is equivalent to 10,000 standardhours.a. Suppose management sets the level of regular work-ers for the year equal to the average demand andsubcontracts out the rest. What is…arrow_forwardevelop a production plan and calculate the annual cost for a firm whose demand forecast is fall, 9,700; winter, 8,000; spring, 7,000; summer, 11,700. Inventory at the beginning of fall is 485 units. At the beginning of fall you currently have 35 workers, but you plan to hire temporary workers at the beginning of summer and lay them off at the end of summer. In addition, you have negotiated with the union an option to use the regular workforce on overtime during winter or spring only if overtime is necessary to prevent stockouts at the end of those quarters. Overtime is not available during the fall. Relevant costs are hiring, $80 for each temp; layoff, $160 for each worker laid off; inventory holding, $5 per unit-quarter; backorder, $10 per unit; straight time, $5 per hour; overtime, $8 per hour. Assume that the productivity is 0.5 unit per worker hour, with eight hours per day and 60 days per season. In each quarter, produce to the full output of your regular workforce, even if that…arrow_forwardCalculate MPS for all periodsarrow_forward
- 4. Terminator, Inc., manufactures a motorcycle part in lots of 250 units. The raw materials cost for the part is $170, and the value added in manufacturing 1 unit from its components is $320, for a total cost per completed unit of $490. The lead time to make the part is 4 weeks, and the annual demand is 4,200 units. Assume 50 working weeks per year. a. How many units of the part are held, on average, as cycle inventory? ___ units. (Enter your response as an integer.) What is its value? $______ (Enter your response as an integer.) b. How many units of the part are held, on average, as pipeline inventory? _____units. (Enter your response as an integer.) What is its value? $______ (Enter your response as an integer.)arrow_forwardQ7. The president of Rose Bowl Enterprises, Desmond Howard, projects the firms aggregate DEMAND requirements over the next 8 months as follows: These are the monthly DEMAND, not production. MONTH JAN FEB MAR APR MAY JUN JULY AUG DEMAND 1,400 1,600 1,800 1,800 2,200 2,200 1,800 1,800 PRODUCTION 1,600 from December INVENTORY 200 from Dec plus 200 His operations manager is considering a new plan, which begins in January with 200 units on hand. Stockout cost of lost sales is $100 per unit. Inventory holding cost is $20 per unit per month. Ignore any idle time costs. The plan is called plan A. Plan A: Vary the workforce level to execute a strategy that produces the quantity demanded in the prior month. The December demand was given as 1,600 units per month. Therefore, the production for JAN will be 1,600. However, only 1,400 are needed. Therefore, the extra 200 produced go into inventory and there is a holding cost for inventory. Also, per the above, you already have 200 units in inventory…arrow_forward
- Practical Management ScienceOperations ManagementISBN:9781337406659Author:WINSTON, Wayne L.Publisher:Cengage,Operations ManagementOperations ManagementISBN:9781259667473Author:William J StevensonPublisher:McGraw-Hill EducationOperations and Supply Chain Management (Mcgraw-hi...Operations ManagementISBN:9781259666100Author:F. Robert Jacobs, Richard B ChasePublisher:McGraw-Hill Education
- Purchasing and Supply Chain ManagementOperations ManagementISBN:9781285869681Author:Robert M. Monczka, Robert B. Handfield, Larry C. Giunipero, James L. PattersonPublisher:Cengage LearningProduction and Operations Analysis, Seventh Editi...Operations ManagementISBN:9781478623069Author:Steven Nahmias, Tava Lennon OlsenPublisher:Waveland Press, Inc.
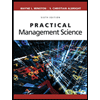
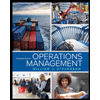
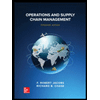
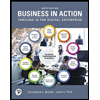
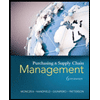
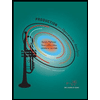