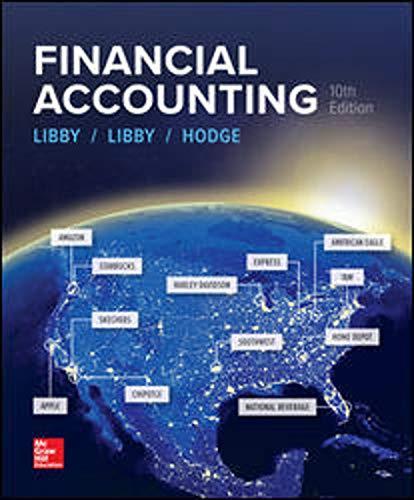
FINANCIAL ACCOUNTING
10th Edition
ISBN: 9781259964947
Author: Libby
Publisher: MCG
expand_more
expand_more
format_list_bulleted
Question
Mighty Safe Fire Alarm is currently buying 61,000 motherboards from MotherBoard, Inc. at a price of $63 per board. Mighty Safe is considering making its own motherboards. The costs to make the motherboards are as follows: direct materials, $34 per unit; direct labor, $11 per unit; and variable factory
a.make, $244,000 increase in profits
b.buy, $164,090 more in profits
c.buy, $80,000 more in profits
d.make, $164,090 increase in profits
Expert Solution

This question has been solved!
Explore an expertly crafted, step-by-step solution for a thorough understanding of key concepts.
This is a popular solution
Trending nowThis is a popular solution!
Step by stepSolved in 2 steps

Knowledge Booster
Learn more about
Need a deep-dive on the concept behind this application? Look no further. Learn more about this topic, accounting and related others by exploring similar questions and additional content below.Similar questions
- Wilma Company must decide whether to make or buy some of its components. The costs of producing 64,400 switches for its generators are as follows. Direct materials $29,200 Variable overhead $45,600 Direct labor $31,404 Fixed overhead $81,200 Instead of making the switches at an average cost of $2.91 ($187,404 ÷ 64,400), the company has an opportunity to buy the switches at $2.67 per unit. If the company purchases the switches, all the variable costs and one-fourth of the fixed costs will be eliminated. (a) Prepare an incremental analysis showing whether the company should make or buy the switches. (Enter negative amounts using either a negative sign preceding the number e.g. -45 or parentheses e.g. (45).) Net Income Make Buy Increase (Decrease) Direct materials $4 $4 $ Direct labor Variable manufacturing costs Fixed manufacturing costs Purchase price Total cost $4 $1 Wilma Company will incur $ of additional costs if it the switches.arrow_forwardThe Mighty Music Company produces and sells a desktop speaker for $200. The company has the capacity to produce 60,000 speakers each period. At capacity, the costs assigned to each unit are as follows: Unit-level costs Product-level costs Facility-level costs The company has received a special order for 11,000 speakers. If this order is accepted, the company will have to spend $20,000 on additional costs. Assuming that no sales to regular customers will be lost if the order is accepted, at what selling price will the company be indifferent between accepting and rejecting the special order? Multiple Choice O O $96.82 $146.82 $104.32 $95 $25 $15 $107.32arrow_forwardThe Wood Division of Vaughn Manufacturing manufactures rubber moldings and sells them externally for $45. Its variable cost is $25 per unit, and its fixed cost per unit is $8. Vaughn’s president wants the Wood Division to transfer 4300 units to another company division at a price of $21.Assuming the Wood Division does not have any available capacity, the minimum transfer price it should accept is $45. $25. $21. $8.arrow_forward
- Paradise Manufacturing currently makes one of its parts for a total cost of $3.80 per unit. This cost is based on a normal capacity of 60,000 units. Variable cost are $2.50 per unit. Fixed cost related to making this part is $30,000. Allocated fixed cost are unavoidable and amount to $30,000. Paradise Manufacturing is considering buying the part for $2.80 per unit. Should the company continue making the part or should they buy the part from the outside supplier? Give a numerical justification for your answer.arrow_forwardWilma Company must decide whether to make or buy some of its components. The costs of producing 60,000 switches for its generators are as follows. Direct materials $30,000 Variable overhead $45,000 Direct labor $42,000 Fixed overhead $60,000 Instead of making the switches at an average cost of $2.95 ($177,000 ÷ 60,000), the company has an opportunity to buy the switches at $2.7 per unit. If the company purchases the switches, all the variable costs and one-fourth of the fixed costs will be eliminated. (a) Prepare an incremental analysis showing whether the company should make or buy the switches. (Enter negative amounts using either a negative sign preceding the number e.g. -45 or parentheses e.g. (45).) Make Buy Net IncomeIncrease (Decrease) Direct materials $ $ $ Direct labor Variable manufacturing costs Fixed manufacturing costs Purchase price Total…arrow_forwardyntech makes digital cameras for drones. Their basic digital camera uses $80 in variable costs and requires $1,600 per month in fixed costs. Syntech sells 100 cameras per month. If they process the camera further to enhance its functionality, it will require an additional $50 per unit of variable costs, plus an increase in fixed costs of $1,200 per month. The current price of the camera is $170. The marketing manager is positive that they can sell more and charge a higher price for the improved version. At what price level would the upgraded camera begin to improve operational earnings?arrow_forward
- Answer the following questions. 1. Douglas Computers makes 5,900 units of a circuit board, CB76 at a cost of $220 each. Variable cost per unit is $170 and fixed cost per unit is $50. Peach Electronics offers to supply 5,900 units of CB76 for $200. If Douglas buys from Peach it will be able to save $20 per unit in fixed costs but continue to incur the remaining $30 per unit. Should Douglas accept Peach's offer? Explain. 1. Douglas Computers makes 5,900 units of a circuit board, CB76 at a cost of $220 each. Variable cost per unit is $170 and fixed cost per unit is $50. Peach Electronics offers to supply 5,900 units of CB76 for $200. If Douglas buys from Peach it will be able to save $20 per unit in fixed costs but continue to incur the remaining $30 per unit. Should Douglas accept Peach's offer? Explain. Begin by calculating the relevant cost per unit. (If a box is not used in the table, leave the box empty; do not enter a zero.) Make Buy Relevant costs: Unit relevant cost Douglas…arrow_forwardHelp pleasearrow_forwardA number of costs are listed below that may be relevant in a decision faced by the management of Bulacan Company. Bulacan normally runs at capacity and the old Model CY1000 machine is the company’s constraint. Management is considering purchasing a new machine, Model CZ4000 and the old one, CY1000 will be sold. The new machine is more efficient and can produce 20% more units than the old one. Demand for Bulacan’s product is greater than what they can supply. If the new machine is purchased, there should be a reduction in maintenance costs however the new machine is very costly and the company will need to borrow money in order to make the purchase. The increase in volume will be large enough to require increases in fixed selling expense, but general administrative expenses will remain unchanged. Required: For each cost listed determine whether the cost is relevant or irrelevant to the decision to replace the CY1000. a. Sales Revenue b. Direct materials c. Direct labor d. Variable…arrow_forward
- Lightning Semiconductors produces 100,000 hi – tech computer chips per month. Each chip uses a component that Lightning makes in - house. The variable costs to make the component are $1.40 per unit, and the fixed costs are $1,300,000 per month. The company has been approached by a foreign producer who can supply the component, within acceptable quality standards, for $1.20 each. The fixed costs are unavoidable, and Lightning would have no other use for the facilities currently employed in making the component. What would be the effect on operating income if the company decides to outsource? O A. Lightning Semiconductors could save $1,300,000 per month in costs. B. There would be no effect on operating income. O c. Lightning Semiconductor's costs would increase by $120,000 per month. O D. Lightning Semiconductors could save $20,000 per month in costs.arrow_forwardThe Knot manufactures men’s neckwear at its Spartanburg plant. The Knot is considering implementing a JIT production system. The following are the estimated costs and benefits of JIT production: a. Annual additional tooling costs $250,000 annually. b. Average inventory would decline by 80% from the current level of $1,000,000. c. Insurance, space, materials-handling, and setup costs, which currently total $400,000 annually, would decline by 20%. d. The emphasis on quality inherent in JIT production would reduce rework costs by 25%. The Knot currently incurs $160,000 in annual rework costs. e. Improved product quality under JIT production would enable The Knot to raise the price of its product by $2 per unit. The Knot sells 100,000 units each year. The Knot’s required rate of return on inventory investment is 15% per year. Q. Suppose The Knot implements JIT production at its Spartanburg plant. Give examples of performance measures The Knot could use to evaluate and control JIT…arrow_forwardA distributor of fasteners is opening a new plant and considering whether to use a mechanized process or a manual process to package the product. The manual process will have a fixed cost of $36,234 and a variable cost of $2.14 per bag. The mechanized process would have a fixed cost of $84,420 and a variable cost of $1.85 per bag. The company expects to sell each bag of fasteners for $2.75. a) What is the break-even point for the manual process (in units)? b) What is the break-even point for the mechanized process (in units)? c) A point of indifference for two processes is quantity at which each process generates the same amount of profit (review video). What is the point of indifference for the two processes? (Hint: 1) Use equations to set profit of manual process equal to mechanized process and solve for quantity; 2) (Excel) If you have a break-even for each process - have only one cell that represents quantity that be used to calculates costs/revenues for each process and use Goal…arrow_forward
arrow_back_ios
SEE MORE QUESTIONS
arrow_forward_ios
Recommended textbooks for you
- AccountingAccountingISBN:9781337272094Author:WARREN, Carl S., Reeve, James M., Duchac, Jonathan E.Publisher:Cengage Learning,Accounting Information SystemsAccountingISBN:9781337619202Author:Hall, James A.Publisher:Cengage Learning,
- Horngren's Cost Accounting: A Managerial Emphasis...AccountingISBN:9780134475585Author:Srikant M. Datar, Madhav V. RajanPublisher:PEARSONIntermediate AccountingAccountingISBN:9781259722660Author:J. David Spiceland, Mark W. Nelson, Wayne M ThomasPublisher:McGraw-Hill EducationFinancial and Managerial AccountingAccountingISBN:9781259726705Author:John J Wild, Ken W. Shaw, Barbara Chiappetta Fundamental Accounting PrinciplesPublisher:McGraw-Hill Education
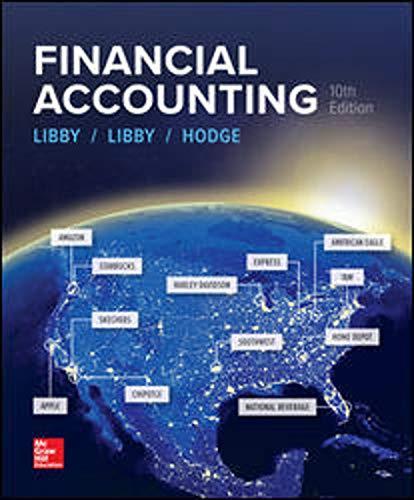
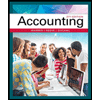
Accounting
Accounting
ISBN:9781337272094
Author:WARREN, Carl S., Reeve, James M., Duchac, Jonathan E.
Publisher:Cengage Learning,
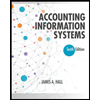
Accounting Information Systems
Accounting
ISBN:9781337619202
Author:Hall, James A.
Publisher:Cengage Learning,
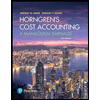
Horngren's Cost Accounting: A Managerial Emphasis...
Accounting
ISBN:9780134475585
Author:Srikant M. Datar, Madhav V. Rajan
Publisher:PEARSON
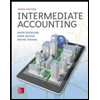
Intermediate Accounting
Accounting
ISBN:9781259722660
Author:J. David Spiceland, Mark W. Nelson, Wayne M Thomas
Publisher:McGraw-Hill Education
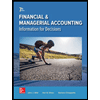
Financial and Managerial Accounting
Accounting
ISBN:9781259726705
Author:John J Wild, Ken W. Shaw, Barbara Chiappetta Fundamental Accounting Principles
Publisher:McGraw-Hill Education