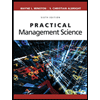
Concept explainers
Powered by Koffee (PBK) is a new campus coffee store. PBK uses 50 bags of whole bean coffee every month, and you may assume that demand is perfectly steady throughout the year. PBK has signed a year-long contract to purchase its coffee from a local supplier, Phish Roasters, for a price of $25 per bag and an $85 fixed cost for every delivery independent of the order size. The holding cost due to storage is $1 per bag per month. PBK managers figure their cost of capital is approximately 2 percent per month.
a. What is the optimal order size, in bags?
b. Given your answer in (a), how many times a year does PBK place orders?
c. Given your answer in (a), how many months of supply of coffee does PBK have on average?
d. On average, how many dollars per month does PBK spend to hold coffee (including cost of capital)? Suppose that a South American import/export company has offered PBK a deal for the next year. PBK can buy a year's worth of coffee directly from South America for $20 per bag and a fixed cost for delivery of $500. Assume the estimated cost for inspection and storage is $1 per bag per month and the cost of capital is approximately 2 percent per month.
e. Should PBK order from Phish Roasters or the South American import/export com- pany? Quantitatively justify your answer.

Trending nowThis is a popular solution!
Step by stepSolved in 2 steps with 2 images

Thanks and the cost of capital is not necessary to solve this problem?
I think there is an error with a when multiplying 12 by 600
Thanks and the cost of capital is not necessary to solve this problem?
I think there is an error with a when multiplying 12 by 600
- PART A Speedy Bicycle Company (SBC) is a wholesale distributor of a wide variety of bicycles and bicycle parts. The most popular model is the Dragonfly, which sells for $170. All manufacturing is done at a plant in China, and shipment takes a month (30 days) from the time an order is placed. The estimated order cost is $75, including customs clearance. SBC's cost per bicycle is 65% of retail price, and inventory carrying cost is 11% per year of SBC's cost. If the company cannot fulfill a retail order, the retailer will get the shipment from another distributor and SBC loses that business. SBC is planning inventory for 2023 based on forecasted demand and wants to maintain a 93% service level to minimize lost orders. The company has 300 working days per year. 2021 Forecasted Demand for the Dragonfly Bicycle Model: F A J 15 58 J 8 M 31 M 96 J 59 38 A 23 S 16 0 14 N 26 D 41arrow_forwardThe distribution manager for Putnam Corporation is trying to establish the most economic ordering policy for the standard model of its best-selling microwave oven. He has control of the finished goods warehouse for the factory and must satisfy wholesaler demand. The following information is available: Wholesale value $100 Annual demand 50,000 units Std. Deviation of Demand 30 units per day Working year 250 days Production lead time 9 days Ordering cost for production $1,800 Holding cost per unit per year 20% of value Desired service level 96 percent: If Putnam wishes to use the periodic review system, what should be the safety stock, reorder point? If the current on hand inventory is 1,000 units, how many units should be ordered?arrow_forwardGentle Ben's Bar and Restaurant uses 7,200 quart bottles of an imported wine each year. The effervescent wine costs $9 per bottle and is served only in whole bottles because it loses its bubbles quickly. Ben figures that it costs $25 each time an order is placed, and holding costs are 40 percent of the purchase price. It takes six weeks for an order to arrive. Weekly demand is 144 bottles (closed two weeks per year) with a standard deviation of 40 bottles. Ben would like to use an inventory system that minimizes inventory cost and will provide a 99 percent service probability. a. What is the economic quantity for Ben to order? b. At what inventory level should he place an order?arrow_forward
- Mr. Beautiful, an organization that sells weight training sets, has an ordering cost of $40 for the BB-1 set (BB-1 stands for Body Beautiful Number 1). The carrying cost for BB-1 is $5 per set per year. To meet demand, Mr. Beautiful orders large quantities of BB-1 7 times a year. The stockout cost for BB-1 is estimated to be $50 per set. Over the past several years, Mr. Beautiful has observed the following demand during the lead time for BB-1: Demand During Lead Time 40 50 60 70 80 90 The reorder point for BB-1 is 60 sets. What level of safety stock should be maintained for BB-1? The optimal quantity of safety stock which minimizes expected total cost is Probability 0.1 0.2 0.2 0.2 0.2 0.1 sets (enter your response as a whole number).arrow_forwardDouble T appliance is a retailer of small appliances in West Texas. Double T gets all of their merchandise from GE which it then sells to the people of the South Plains. Their annual demand is 10,000 units and the ordering cost is $100 per order. The carrying cost per unit is $50.00 What is their expected annual carrying cost (not including the costs of the goods) if the Economic Order Quantity is used and is equal to 200 units?arrow_forwardThe distribution manager for Divine Corporation is trying to establish the most economic ordering policy for the standard model of its best-selling microwave oven. He has control of the finished goods warehouse for the factory and must satisfy wholesaler demand. The following information is available: Wholesale Value $100 Annual Demand 50,000 units Standard Deviation of Demand 30 units per day Working Year 250 days Production Lead Time 9 days Ordering Cost for Production $1,800 Holding Cost per unit per year 20% of value Desired Service Level 96 percent If Divine decides to use a continuous review system, what should be economic order quantity, safety stock, and the reorder point? If on the other hand, Divine wishes to use the periodic review system, what should be the safety stock, reorder point? If the current on hand inventory is 1,000 units, how many units should be ordered?arrow_forward
- Alpha Products, Inc., is having a problem trying to control inventory. There is insufficient time to devote to all its items equally. The following is a sample of some items stocked, along with the annual usage of each item expressed in dollar volume. ITEM ANNUAL DOLLAR USAGE ITEM ANNUAL DOLLAR USAGE a S 30, 100 k S 1,700 b 27,000 120,000 c 93,000 m 111,000 d 1,400 n 3,000 e 1,800 o 500 f 30,000 p 114, 000 g 1,600 q 2,600 h 2,500 г 28,000 i 3, 200 s 2, 800 j 1,500 t 3, 100 a. Suggest a system for allocating control time? multiple choice ABC analysis Cycle counting b. Specify where each item from the list would be placed.arrow_forwardHaley Photocopying purchases paper from an out-of-state vendor. Average weekly demand for paper is 170 cartons per week for which Haley pays $25 per carton. Inbound shipments from the vendor average 950 cartons with an average lead time of 5 weeks. Haley operates 52 weeks per year; it carries a 6-week supply of inventory as safety stock and no anticipation inventory. The vendor has recently announced that they will be building a facility near Haley Photocopying that will reduce lead time to to week. Further, they will be able to reduce shipments to 300 cartons. Haley believes that they will be able to reduce safety stock to a 1-week supply. What impact will these changes make to Haley's average inventory level and its average aggregate inventory value?arrow_forwardMichigan State figurines Inc. sells Crystal figurines to spartan fans. They buy the figurines from the manufacture for $19 per unit. They send orders electronically to the manufacturer, cost and $33 per order and they experience an average sleep time of six days for each order to arrive from the manufacture. Their inventory Karen cost is 20%. The average daily demand for the figurines is two units per day. They are open for business 250 days a year. Answer the following questions. I am struggling with the last two.arrow_forward
- A bookstore stocks a limited-edition series of collectible comic books, which are considered perishable due to their limited availability and potential for damage if not stored properly. This particular comic book series is highly sought after by collectors and sells for $50 per issue. It comes with a high annual inventory holding cost rate of 30% of its SKU value. The estimated ordering cost is $100 per order. The store anticipates an annual demand of 500 issues for the upcoming year. The lead time for orders is four weeks, assuming 52 weeks in a year. a) Set up a fixed-order-quantity system computing: the EOQ and the reorder point (r). b) Set up a fixed-period system computing: the review period (T) and the replenishment level (M). Round the review period to the next highest number. c) How much more does it cost to hold inventory in an FPS vs. an FQS?arrow_forwardThe annual demand for the Super Thrive brand plant food manufactured by Cumberbatch and Dunst Indoor Plants Company is 120,000 pounds. The annual holding cost (also known as carrying charge) is $0.05 per pound, and Operations Manager Kirsten Benedict has calculated the cost of setting up machinery for making the plant food to be $20. 1) What is the annual holding (carrying) cost for the EOQ that you calculated ? plz send answer fast.arrow_forwardsniparrow_forward
- Practical Management ScienceOperations ManagementISBN:9781337406659Author:WINSTON, Wayne L.Publisher:Cengage,Operations ManagementOperations ManagementISBN:9781259667473Author:William J StevensonPublisher:McGraw-Hill EducationOperations and Supply Chain Management (Mcgraw-hi...Operations ManagementISBN:9781259666100Author:F. Robert Jacobs, Richard B ChasePublisher:McGraw-Hill Education
- Purchasing and Supply Chain ManagementOperations ManagementISBN:9781285869681Author:Robert M. Monczka, Robert B. Handfield, Larry C. Giunipero, James L. PattersonPublisher:Cengage LearningProduction and Operations Analysis, Seventh Editi...Operations ManagementISBN:9781478623069Author:Steven Nahmias, Tava Lennon OlsenPublisher:Waveland Press, Inc.
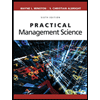
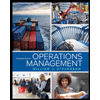
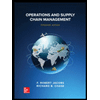
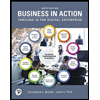
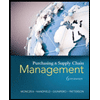
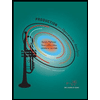