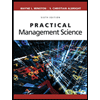
Practical Management Science
6th Edition
ISBN: 9781337406659
Author: WINSTON, Wayne L.
Publisher: Cengage,
expand_more
expand_more
format_list_bulleted
Concept explainers
Topic Video
Question
- The distribution manager for Divine Corporation is trying to establish the most economic ordering policy for the standard model of its best-selling microwave oven. He has control of the finished goods warehouse for the factory and must satisfy wholesaler demand. The following information is available:
Wholesale Value |
$100 |
Annual Demand |
50,000 units |
Standard Deviation of Demand |
30 units per day |
Working Year |
250 days |
Production Lead Time |
9 days |
Ordering Cost for Production |
$1,800 |
Holding Cost per unit per year |
20% of value |
Desired Service Level |
96 percent |
- If Divine decides to use a continuous review system, what should be economic order quantity, safety stock, and the reorder point?
- If on the other hand, Divine wishes to use the periodic review system, what should be the safety stock, reorder point? If the current on hand inventory is 1,000 units, how many units should be ordered?
Expert Solution

This question has been solved!
Explore an expertly crafted, step-by-step solution for a thorough understanding of key concepts.
This is a popular solution
Trending nowThis is a popular solution!
Step by stepSolved in 2 steps

Knowledge Booster
Learn more about
Need a deep-dive on the concept behind this application? Look no further. Learn more about this topic, operations-management and related others by exploring similar questions and additional content below.Similar questions
- 40) PLEASE HELP WITH THIS! Gentle Ben's Bar and Restaurant uses 5,000 quart bottles of an imported wine each year. The effervescent wine costs $3 per bottle and Is served only in whole bottles because it loses its bubbles quickly. Ben figures that it costs $10 each time an order is placed, and holding costs are 20 percent of the purchase price. It takes three weeks for an order to arrive. Weekly demand is 100 bottles (closed two weeks per year) with a standard devlation of 30 bottles. Ben would like to use an inventory system that minimizes inventory cost and will provide a 95 percent service probability. b. At what inventory level should he place an order? Note: Use Excel's NORM.S.IN( function to find the z value. Round z value to 2 decimal places and final answer to the nearest whole number.arrow_forwardSam's Pet Hotel operates 52 weeks per year, 6 days per week, and uses a continuous review inventory system. It purchases kitty litter for $13.00 per bag. The following information is available about these bags: ≻Demand=75 bags/week ≻Order cost=$55.00/order ≻Annual holding cost=25 percent of cost ≻Desired cycle-service level=80 percent ≻Lead time=4 weeks (24 working days) ≻Standard deviation of weekly demand=15 bags ≻Current on-hand inventory is 320 bags, with no open orders or backorders. Part 2 a. Suppose that the weekly demand forecast of 75 bags is incorrect and actual demand averages only 50 bags per week. How much higher will total costs be, owing to the distorted EOQ caused by this forecast error? The costs will be $enter your response here higher owing to the error in EOQ. (Enter your response rounded to two decimal places.) a. What is the EOQ? What would the average time between orders (in weeks)? b. What should R be? c. An inventory withdraw…arrow_forwardThe distribution manager for Putnam Corporation is trying to establish the most economic ordering policy for the standard model of its best-selling microwave oven. He has control of the finished goods warehouse for the factory and must satisfy wholesaler demand. The following information is available: Wholesale value $100 Annual demand 50,000 units Std. Deviation of Demand 30 units per day Working year 250 days Production lead time 9 days Ordering cost for production $1,800 Holding cost per unit per year 20% of value Desired service level 96 percent: If Putnam wishes to use the periodic review system, what should be the safety stock, reorder point? If the current on hand inventory is 1,000 units, how many units should be ordered?arrow_forward
- define the ABC approach to inventory management Several metrics can be used to identify an A-status:explain?arrow_forwardDefine each of the following terms: c. Economic Ordering Quantity (EOQ); EOQ model; EOQ rangearrow_forwardPlease do not give solution in image format thanku Prince Electronics, a manufacturer of consumer electronic goods, has five distribution centers in different regions of the country. For one of its products, a highspeed modem priced at $360 per unit, the average weekly demand at each distribution center is 85 units. Average shipment size to each distribution center is 450 units, and average lead time for delivery is 2 weeks. Each distribution center carries 2 weeks' supply as safety stock but holds no anticipation inventory. Part 2 a. On average, how many dollars of pipeline inventory will be in transit to each distribution center? $enter your response here. (Enter your response as an integer.)arrow_forward
- 13.37. Kelly's Tavern serves Shamrock draft beer to its customers. The daily demand for beer is normally distributed, with an average of 20 gallons and a standard deviation of 4 gallons. The lead time required to receive an order of beer from the local distributor is 12 days. Determinearrow_forwardFisk Corporation is trying to improve its inventory control system and has installed an online system at its retail stores. Fisk anticipates sales of 58,800 units per year, an ordering cost of $4 per order, and carrying costs of $1.50 per unit. In the second year, Fisk Corporation finds that it can reduce ordering costs to $1 per order, but carrying costs will stay the same at $1.50 per unit. a-1. What is the economic ordering quantity for the second year? Economic ordering quantity (EOQ) a-2. How many orders will be placed during the second year? Number of orders a-3. What will the average inventory be for the second year? Average inventory Total costs units units a-4. What is the total cost of ordering and carrying inventory for second year? LAarrow_forwardMaxantene Products buys 300,000 units of a crucial input per year from a supplier that fulfills its orders within two days after receiving them. Maxantene Product submits its orders directly to the supplier through a Web interface, so its lead time is the supplier two day turnaround time. Each order cost Maxantene Products about P500 to place, while carrying cost are about P60 per unit per year. The company seek to maintain a five day usage level in a safety stock. Assume a 365 day year. ------------- a.What is Maxantene Products economic order quantity for this input? b. What is Maxantene Products' carrying cost at the EOQ? * c. At what inventory level of this input should Maxantene re-order?arrow_forward
- What would be the relationship (one-to-one, one-to-many, or many-to-many) relationship between: Sales and inventory Inventory and Order form Order and Vendorarrow_forwardAndy's Job Shop buys two parts (Tegdiws and Widgets) for use in its production system from two different suppliers. The parts are needed throughout the entire 52-week year to assemble Uediracs for sale. Tegdiws are used at a relatively constant rate but the use of Widgets vary with demand. Andy wants to improve his inventory management system and use either a "P" system or a "Q" system. What are the advantages and disadvantages of each system in this application and what information is needed to choose between them?arrow_forwardBradley Solutions and Alexander Limited are two well-established suppliers of inexpensive tools. Weekend Projects is a national chain of retail outlets that caters to the occasional fixer-upper who would prefer to get the job done fast rather than investing in a well-appointed tool box. Weekend Projects wants to find a supplier for a particular tool set that promises to be a big seller. Expected annual sales are 100,000 units (D). Weekend's warehouses operate 50 weeks a year. Management collected data on the two suppliers, which are contained in the table below: Annual Price/Unit Holding Cost/Unit Lead Time (L) (p) (wks) Supplier 10,000 25,000 50,000 Bradley $40,000 $26,000 $19,000 Alexander $30,000 $28,000 $17,000 $7.15 $7.15 a. Which of the two suppliers would provide the lowest annual cost to Weekend Projects? What shipping quantity would you suggest? and a shipping quantity of Using Annual Freight Costs Shipping Quantity (Q) -w an example Get more help. (H) $1.43 $1.43 6 4 Annual…arrow_forward
arrow_back_ios
SEE MORE QUESTIONS
arrow_forward_ios
Recommended textbooks for you
- Practical Management ScienceOperations ManagementISBN:9781337406659Author:WINSTON, Wayne L.Publisher:Cengage,Operations ManagementOperations ManagementISBN:9781259667473Author:William J StevensonPublisher:McGraw-Hill EducationOperations and Supply Chain Management (Mcgraw-hi...Operations ManagementISBN:9781259666100Author:F. Robert Jacobs, Richard B ChasePublisher:McGraw-Hill Education
- Purchasing and Supply Chain ManagementOperations ManagementISBN:9781285869681Author:Robert M. Monczka, Robert B. Handfield, Larry C. Giunipero, James L. PattersonPublisher:Cengage LearningProduction and Operations Analysis, Seventh Editi...Operations ManagementISBN:9781478623069Author:Steven Nahmias, Tava Lennon OlsenPublisher:Waveland Press, Inc.
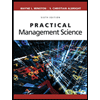
Practical Management Science
Operations Management
ISBN:9781337406659
Author:WINSTON, Wayne L.
Publisher:Cengage,
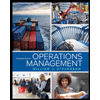
Operations Management
Operations Management
ISBN:9781259667473
Author:William J Stevenson
Publisher:McGraw-Hill Education
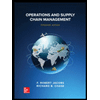
Operations and Supply Chain Management (Mcgraw-hi...
Operations Management
ISBN:9781259666100
Author:F. Robert Jacobs, Richard B Chase
Publisher:McGraw-Hill Education
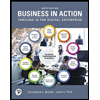
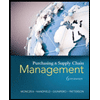
Purchasing and Supply Chain Management
Operations Management
ISBN:9781285869681
Author:Robert M. Monczka, Robert B. Handfield, Larry C. Giunipero, James L. Patterson
Publisher:Cengage Learning
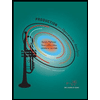
Production and Operations Analysis, Seventh Editi...
Operations Management
ISBN:9781478623069
Author:Steven Nahmias, Tava Lennon Olsen
Publisher:Waveland Press, Inc.