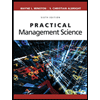
Practical Management Science
6th Edition
ISBN: 9781337406659
Author: WINSTON, Wayne L.
Publisher: Cengage,
expand_more
expand_more
format_list_bulleted
Question

Transcribed Image Text:**9.4** A florist carries an average inventory of $12,000 in cut flowers. The flowers require special storage and are highly perishable. The florist estimates capital costs at 10%, storage costs at 20%, and risk costs at 50%. What is the annual carrying cost?
**Explanation for an Educational Website:**
To calculate the annual carrying cost of the florist's inventory, you need to consider the total percentage of costs applied to the average inventory value. The capital, storage, and risk costs are given as percentages:
- Capital Costs: 10%
- Storage Costs: 20%
- Risk Costs: 50%
**Calculation Steps:**
1. **Total Percentage of Carrying Costs:**
- Capital Costs = 10%
- Storage Costs = 20%
- Risk Costs = 50%
- Total Percentage = 10% + 20% + 50% = 80%
2. **Annual Carrying Cost:**
- Multiply the total percentage by the average inventory value:
- Annual Carrying Cost = 80% of $12,000 = 0.80 * $12,000 = $9,600
Thus, the annual carrying cost for the florist's inventory is $9,600. This involves the costs associated with capital tied up, storage needs, and risks due to the perishable nature of the flowers.
Expert Solution

arrow_forward
INTRODUCTION
A firm's numerous expenses for keeping goods on hand are known as carrying costs. Taxes, insurance, personnel costs, and opportunity costs are some examples of carrying costs. By using effective warehouse architecture and employing computerized inventory management systems to monitor inventory levels, businesses may lower their carrying costs.
Step by stepSolved in 2 steps

Knowledge Booster
Similar questions
- Double T appliance is a retailer of small appliances in West Texas. Double T gets all of their merchandise from GE which it then sells to the people of the South Plains. Their annual demand is 10,000 units and the ordering cost is $100 per order. The carrying cost per unit is $50.00 What is their expected annual carrying cost (not including the costs of the goods) if the Economic Order Quantity is used and is equal to 200 units?arrow_forwardEOQ, reorder point, and safety stock Alexis Company uses 937units of a product per year on a continuous basis. The product has a fixed cost of $44 per order, and its carrying cost is $4 per unit per year. It takes 5 days to receive a shipment after an order is placed, and the firm wishes to hold 10 days' usage in inventory as a safety stock. a. Calculate the EOQ. b. Determine the average level of inventory. (Note: Use a 365-day year to calculate daily usage.) c. Determine the reorder point. d. Indicate which of the following variables change if the firm does not hold the safety stock: (1) order cost, (2) carrying cost, (3) total inventory cost, (4) reorder point, (5) economic order quantity.arrow_forwardThe Mcdonald’s fast-food restaurant on campus sells an average of 7,200 quarter pound hamburgers a week. Hamburger patties are resupplied twice a week, and on average the store has 740 pounds of hamburger in stock. Assume that hamburger patties cost $3 a pound and there are 52 weeks in a year. What is the inventory turnover for the hamburger patties? (Round 2 decimal places) On average how many days of supply are on hand? (Round 2 Decimal places)arrow_forward
- 7. Sam's Cat Hotel operates 52 weeks per year, 5 days per week, and uses a continuous review inventory system. It purchases kitty litter for $11.00 per bag. The following information is available about these bags. Refer to the standard normal table for z-values. ≻Demand = 95 bags/week ≻Order cost = $57/order ≻Annual holding cost = 30 percent of cost ≻Desired cycle-service level=98 percent ≻Lead time = 1 week(s) (5 working days) ≻Standard deviation of weekly demand = 20 bags ≻Current on-hand inventory is 350 bags, with no open orders or backorders. d. The store currently uses a lot size of 490 bags (i.e., Q=490). What is the annual holding cost of this policy? (Enter your response rounded to two decimal places.) and (Enter your response rounded to two decimal places.) **select the correct multiple choice answer** e. What would be the annual cost saved by shifting from the 490-bag lot size to the EOQ? (Enter your responses rounded to two decimal places.)arrow_forwardes Garden Variety Flower Shop uses 930 clay pots a month. The pots are purchased at $3.90 each. Annual carrying costs per pot are estimated to be 10 percent of cost, and ordering costs are $10 per order. The manager has been using an order size of 2,000 flower pots. a.What additional annual cost is the shop incurring by staying with this order size? (Round your optimal order quantity to the nearest whole number. Round all other intermediate calculations and your final answer to 2 decimal places.) Additional annual cost b.Other than cost savings, what benefit would using the optimal order quantity yield (relative to the order size of 2,000)? (Use the rounded order quantity from Part a. Round your final answer to the nearest whole percent.) About % of the storage space would be needed. Check myarrow_forwardA produce distributor uses 790 packing crates a month, which it purchases at a cost of $10 each. The manager has assigned an annual carrying cost of 39 percent of the purchase price per crate. Ordering costs are $31. Currently the manager orders once a month. How much could the firm save annually in ordering and carrying costs by using the EOQ? (Round intermediate calculations and final answer to 2 decimal places.) Savings per yeararrow_forward
- The annual demand for the Super Thrive brand plant food manufactured by Cumberbatch and Dunst Indoor Plants Company is 120,000 pounds. The annual holding cost (also known as carrying charge) is $0.05 per pound, and Operations Manager Kirsten Benedict has calculated the cost of setting up machinery for making the plant food to be $20. 1) What is the annual holding (carrying) cost for the EOQ that you calculated ? plz send answer fast.arrow_forwardDiscuss how inventory expenses must be balanced and kept to q minimum through inventory controlarrow_forwardJoe Henry's machine shop uses 2,450 brackets during the course of a year. These brackets are purchased from a supplier 90 miles away. The following information is known about the brackets: Annual demand 2,450 Holding cost per bracket per year $1.65 Order cost per order $18.50 Lead time 2 days Working days per year 250 a) What is the EOQ? __units (round your response to two decimal places). b) What is the average inventory if the EOQ is used?__ units (round your response to two decimal places). What would be the annual inventory holding cost? $__ (round your response to two decimal places). c) Given the EOQ, how many orders will be made annually?__orders (round your response to two decimal places). What would be the annual order cost? $__ (round your response to two decimal places). d) Given the EOQ, what is the total annual cost of managing (ordering and holding) the inventory? __ $ (round your response to two decimal places). d)…arrow_forward
- Joe Henry's machine shop uses 2,460 brackets during the course of a year. These brackets are purchased from a supplier 90 miles away. The following information is known about the brackets: Annual demand 2,460 Holding cost per bracket per year $ 1.65 Order cost per order $20.00 Lead time 22 days Working days per year 250 a) What is the EOQ? b) What is the average inventory if the EOQ is used? What would be the annual inventory holding cost? c) Given the EOQ, how many orders would be made each year? What would be the annual order cost? d) Given the EOQ, what is the total annual cost of managing (ordering and holding) the inventory? e) What is the time between orders? f) What is the reorder point (ROP)?arrow_forwardThe total inventory carrying cost = $enter your response here. (Enter your response as a whole number.)arrow_forwardManipulation Manufacturing Company uses 1,000 units of Chip annually in its production. Order costs consist of P10 for placing a long-distance call to make the order and P40 for delivering the order by truck to the company warehouse. Each Chip costs P100 and the carrying costs are estimated at 15.625% of the inventory cost. If the EOQ for Chip is 80 and the total ordering cost is P625. Compute for the Total Carrying Costs.arrow_forward
arrow_back_ios
SEE MORE QUESTIONS
arrow_forward_ios
Recommended textbooks for you
- Practical Management ScienceOperations ManagementISBN:9781337406659Author:WINSTON, Wayne L.Publisher:Cengage,Operations ManagementOperations ManagementISBN:9781259667473Author:William J StevensonPublisher:McGraw-Hill EducationOperations and Supply Chain Management (Mcgraw-hi...Operations ManagementISBN:9781259666100Author:F. Robert Jacobs, Richard B ChasePublisher:McGraw-Hill Education
- Purchasing and Supply Chain ManagementOperations ManagementISBN:9781285869681Author:Robert M. Monczka, Robert B. Handfield, Larry C. Giunipero, James L. PattersonPublisher:Cengage LearningProduction and Operations Analysis, Seventh Editi...Operations ManagementISBN:9781478623069Author:Steven Nahmias, Tava Lennon OlsenPublisher:Waveland Press, Inc.
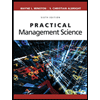
Practical Management Science
Operations Management
ISBN:9781337406659
Author:WINSTON, Wayne L.
Publisher:Cengage,
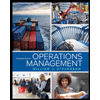
Operations Management
Operations Management
ISBN:9781259667473
Author:William J Stevenson
Publisher:McGraw-Hill Education
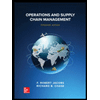
Operations and Supply Chain Management (Mcgraw-hi...
Operations Management
ISBN:9781259666100
Author:F. Robert Jacobs, Richard B Chase
Publisher:McGraw-Hill Education
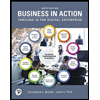
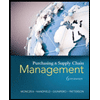
Purchasing and Supply Chain Management
Operations Management
ISBN:9781285869681
Author:Robert M. Monczka, Robert B. Handfield, Larry C. Giunipero, James L. Patterson
Publisher:Cengage Learning
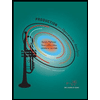
Production and Operations Analysis, Seventh Editi...
Operations Management
ISBN:9781478623069
Author:Steven Nahmias, Tava Lennon Olsen
Publisher:Waveland Press, Inc.