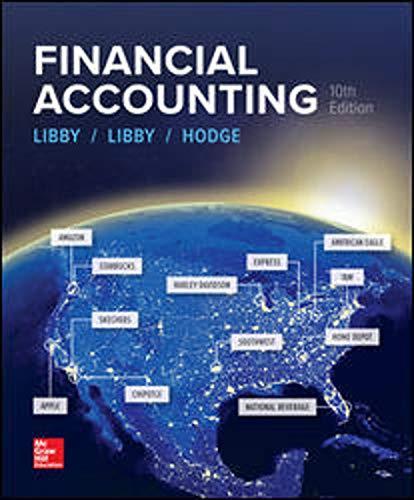
Concept explainers
Fisher Fixtures manufactures three types of lighting fixtures, with model names of Silver, Gold, and Platinum. It applies all indirect costs according to an annual predetermined rate based on direct labor-hours. The plant controller has recommended that the company switch to an activity-based costing system. The controller's staff prepared the following cost estimates for next year (year 2) for the recommended cost drivers.
Activity | Recommended Cost Driver | Estimated Cost | Estimated Cost Driver Activity | |
---|---|---|---|---|
Purchasing material | Number of purchase orders | $ 130,800 | 240 | purchase orders |
Receiving material | Direct materials cost | 238,400 | $ 2,980,000 | |
Setting up equipment | Number of production runs | 231,840 | 120 | runs |
Machine |
Machine-hours | 80,260 | 16,052 | hours |
Ensuring regulatory compliance | Number of inspections | 459,000 | 54 | inspections |
Shipping | Number of units shipped | 1,087,200 | 604,000 | units |
Total estimated cost | $ 2,227,500 |
In addition, management estimated 45,000 direct labor-hours for year 2.
Assume that the following cost-driver volumes occurred in January, year 2:
Silver | Gold | Platinum | |
---|---|---|---|
Number of units produced | 32,000 | 10,000 | 3,000 |
Direct labor-hours | 2,000 | 1,200 | 400 |
Number of purchase orders | 7 | 6 | 3 |
Direct materials costs | $ 97,500 | $ 60,000 | $ 37,500 |
Number of production runs | 2 | 3 | 5 |
Machine-hours | 700 | 175 | 100 |
Number of inspections | 0 | 2 | 3 |
Units shipped | 32,000 | 10,000 | 3,000 |
Labor costs are based on the contractual rate of $25 per hour.
Required:
-
Compute the predetermined rate for year 2 for use in the current product-costing system using direct labor-hours as the allocation base.
-
Compute the per-unit production costs for each model for January using direct labor-hours as the allocation base and the predetermined rate computed in requirement (a).
-
Compute the predetermined
overhead rate for year 2 for each cost driver using the estimated costs and estimated cost driver units prepared by the controller's staff to be used in an ABC system. -
Compute the per unit production costs for each product for January using the cost drivers recommended by the consultant and the predetermined rates computed in requirement (c). (Note: Do not assume that total overhead applied to products in January will be the same for activity-based costing as it was for the labor-hour-based allocation.)
Compute the predetermined rate for year 2 for use in the current product-costing system using direct labor-hours as the allocation base.
Account
|
Silver
|
Gold
|
Platinum
|
Total
|
Direct materials
|
$
97,500 |
$
60,000 |
$
37,500 |
$
195,000 |
Direct labor
|
??? | ??? | ???? |
0
|
Indirect costs
|
??? | ??? | ??? |
0
|
Total cost
|
$
97,500 |
$
60,000 |
$
37,500 |
$
195,000 |
Units produced
|
??? | ??? | ??? | |
Unit cost (rounded)
|
??? | ??? | ??? |
REQUIRED C.
Activity
|
Rate
|
|
Purchasing material
|
?? |
per order
|
Receiving material
|
?? |
%
|
Setting up equipment
|
?? |
per run
|
Machine maintenance
|
?? |
per machine hour
|
Ensuring compliance
|
?? |
per inspection
|
Shipping
|
?? |
per unit
|
REQUIRED D
Account
|
Silver
|
Gold
|
Platinum
|
Total
|
Direct materials
|
$
97,500 |
$
60,000 |
$
37,500 |
$
195,000 |
Direct labor
|
0
|
|||
Indirect costs
|
||||
Purchasing material
|
0
|
|||
Receiving material
|
0
|
|||
Setting up equipment
|
0
|
|||
Machine maintenance
|
0
|
|||
Ensuring compliance
|
0
|
|||
Shipping
|
0
|
|||
Total indirect costs
|
$
76,579 |
$
49,741 |
$
45,695 |
$
172,015 |
Total cost
|
$
97,500 |
$
60,000 |
$
37,500 |
$
195,000 |
Units produced
|
||||
Unit cost (rounded)
|
Need help please, I'm stuck.

Trending nowThis is a popular solution!
Step by stepSolved in 3 steps

Excellent job! For PART B the unit cost row is wrong for some reason.
(8.00 , 15.00, & 22.00) for some reason they are not correct
and I don't know why.
Also for PART D
the last 2 on the unit cost is wrong.
(14.00 & 31.00) I wonder why that is . Can you still help?
Excellent job! For PART B the unit cost row is wrong for some reason.
(8.00 , 15.00, & 22.00) for some reason they are not correct
and I don't know why.
Also for PART D
the last 2 on the unit cost is wrong.
(14.00 & 31.00) I wonder why that is . Can you still help?
- Saratoga Company manufactures jobs to customer specifications. The company is conducting a time-driven activity-based costing study in Its Purchasing Department to better understand how Purchasing Department labor costs are consumed by Individual jobs. To ald the study, the company provided the following data regarding its Purchasing Department and three of its many jobs: Number of employees Average salary per employee Weeks of employment per year Hours worked per week Practical capacity percentage $ 30,000 52 40 85% Requisition Processing 15 Bid Evaluation Inspection 45 30 Minutes per unit of the activity Job X Job Y Job Z Number of requisitions processed Number of bid evaluations 6 3 2 2 1 3 Number of inspections 5 1 5 Now assume that Saratoga Company would like to answer the following "what if" question using its time-driven activity-based costing system: Assuming our estimated activity demands for all jobs in the next period will be as shown below, how will this affect our job…arrow_forwardSilven Company has identified the following overhead activities, costs, and activity drivers for the coming year: Activity Expected Cost Activity Driver Activity Capacity $138,000 Number of setups 10,200 Number of orders 92,400 Machine hours 18,480 Receiving hours phones with the following expected activity demands: Setting up equipment Ordering materials Machining Receiving Silven produces two models of cell Model X 5,000 80 200 6,600 385 Units completed Number of setups Number of orders Machine hours Receiving hours Required: Model Y 10,000 40 400 4,950 770 120 600 11,550 1,155arrow_forwardSultan Company uses an activity-based costing system. At the beginning of the year, the company made the following estimates of cost and activity for its five activity cost pools: Activity Cost Pool Activity Measure Expected Overhead Cost Expected Activity Labor-related Direct labor-hours $ 184,800 30,800 DLHs Purchase orders Number of orders $ 6,900 230 orders Parts management Number of part types $ 81,120 104 part types Board etching Number of boards $ 45,000 1,800 boards General factory Machine-hours $ 150,300 16,700 MHs Required: 1. Compute the activity rate for each of the activity cost pools. 2. The expected activity for the year was distributed among the company’s four products as follows: Activity Cost Pool Expected Activity Product A Product B Product C Product D Labor-related (DLHs) 7,000 14,300 4,400 5,100 Purchase orders (orders) 58 26 46 100 Parts management (part types) 30 18 37 19 Board etching (boards) 500 720 580 0 General factory…arrow_forward
- Collin Company manufactures small appliances and uses an activity-based costing system. Information from its system for the year for all products follows: Activity cost pool Total cost Total activity. Assembly Inspection Packaging $460,000 $298,500 $19,700 A. $139,977.76 B. $115,566.24 C. $23,187.50 D. $26.50 20,000 8,500 1,800 machine - hours inspection - hours order The company makes 875 of its stand mixers a year, which requires a total of 27 machine hours, 15 inspection hours, and 9 orders. The stand mixer requires $16.00 in direct materials per unit and $10.50 in direct labor per unit. The stand mixer sells for $160 per unit. What is the profit margin in total for the stand mixer? (Do not round intermediary calculations and round your final answer to the nearest cent.)arrow_forwardXie Company identified the following activities, costs, and activity drivers for this year. The company manufactures two types of go- karts: Deluxe and Basic. Activity Handling materials Inspecting product Processing purchase orders Paying suppliers Insuring the factory. Designing packaging Activity Required: Compute the activity rate for each activity, assuming the company uses activity-based costing. (Round activity rate answers to 2 decimal places.) Handling material Inspecting product Processing orders Paying suppliers Insuring factory Designing packaging Expected Costs $700,000 975,000 180,000 250,000 375,000 150,000 Expected Costs $ $ Expected Activity 100,000 parts 1,500 batches 700 orders 500 invoices 40,000 square feet 2 models. 700,000 975,000 180,000 250,000 375,000 150,000 2,630,000 Activity Driver 100,000 parts 1,500 batches 700 orders 500 invoices 40,000 square feet 2 models Activity Ratearrow_forwardDate + + + + + I + ī + ||| I General Journal Account/Explanation Page G2 PR Debit Creditarrow_forward
- AccountingAccountingISBN:9781337272094Author:WARREN, Carl S., Reeve, James M., Duchac, Jonathan E.Publisher:Cengage Learning,Accounting Information SystemsAccountingISBN:9781337619202Author:Hall, James A.Publisher:Cengage Learning,
- Horngren's Cost Accounting: A Managerial Emphasis...AccountingISBN:9780134475585Author:Srikant M. Datar, Madhav V. RajanPublisher:PEARSONIntermediate AccountingAccountingISBN:9781259722660Author:J. David Spiceland, Mark W. Nelson, Wayne M ThomasPublisher:McGraw-Hill EducationFinancial and Managerial AccountingAccountingISBN:9781259726705Author:John J Wild, Ken W. Shaw, Barbara Chiappetta Fundamental Accounting PrinciplesPublisher:McGraw-Hill Education
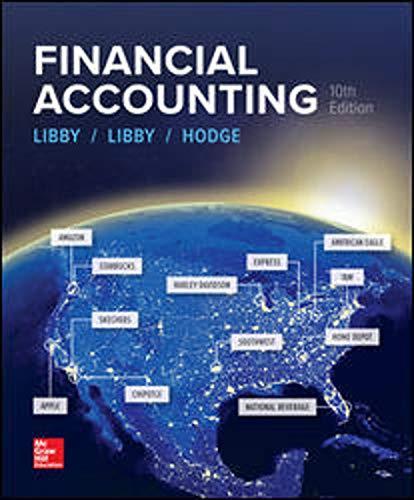
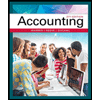
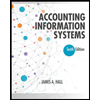
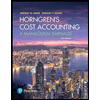
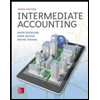
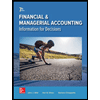