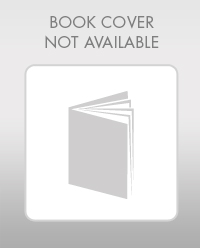
Essentials Of Investments
11th Edition
ISBN: 9781260013924
Author: Bodie, Zvi, Kane, Alex, MARCUS, Alan J.
Publisher: Mcgraw-hill Education,
expand_more
expand_more
format_list_bulleted
Question

Transcribed Image Text:Use Excel or a similar spreadsheet application to calculate the new machine's internal rate of return. (Round answer to 2 decimal
places, eg. 1.25%)
Internal rate of return
%
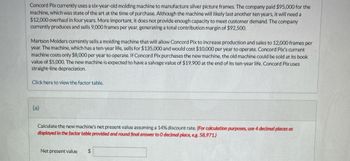
Transcribed Image Text:Concord Pix currently uses a six-year-old molding machine to manufacture silver picture frames. The company paid $95,000 for the
machine, which was state of the art at the time of purchase. Although the machine will likely last another ten years, it will need a
$12,000 overhaul in four years. More important, it does not provide enough capacity to meet customer demand. The company
currently produces and sells 9.000 frames per year, generating a total contribution margin of $92,500.
Martson Molders currently sells a molding machine that will allow Concord Pix to increase production and sales to 12,000 frames per
year. The machine, which has a ten-year life, sells for $135,000 and would cost $10,000 per year to operate. Concord Pix's current
machine costs only $8,000 per year to operate. If Concord Pix purchases the new machine, the old machine could be sold at its book
value of $5,000. The new machine is expected to have a salvage value of $19,900 at the end of its ten-year life. Concord Pix uses
straight-line depreciation.
Click here to view the factor table.
(a)
Calculate the new machine's net present value assuming a 14% discount rate. (For calculation purposes, use 4 decimal places as
displayed in the factor table provided and round final answer to O decimal place, e.g. 58,971)
Net present value $
Expert Solution

This question has been solved!
Explore an expertly crafted, step-by-step solution for a thorough understanding of key concepts.
Step by stepSolved in 3 steps with 2 images

Knowledge Booster
Similar questions
- Teal Mountain Company has been a retailer of audio systems for the past 3 years. However, after a thorough survey of audio system markets, Teal Mountain decided to turn its retail store into an audio equipment factory. Production began October 1, 2022. Direct materials costs for an audio system total $77 per unit. Workers on the production lines are paid $13 per hour. An audio system takes 6 labor hours to complete. In addition, the rent on the equipment used to assemble audio systems amounts to $5,070 per month. Indirect materials cost $5 per system. A supervisor was hired to oversee production; her monthly salary is $3,700. Factory janitorial costs are $2,030 monthly. Advertising costs for the audio system will be $9,030 per month. The factory building depreciation is $6,360 per year. Property taxes on the factory building will be $8,520 per year. Assuming that Teal Mountain manufactures, on average, 1,400 audio systems per month, enter each cost item on your answer sheet, placing…arrow_forwardJupiter Game Company manufactures pocket electronic games. Last year Jupiter sold 25,000 games at $25 each. Total costs amounted to $525,000, of which $150,000 were considered fixed costs. In an attempt to improve its product, the company is considering replacing a component part that has a cost of $2.50 with a new and better part costing $4.50 per unit in the coming year. A new machine also would be needed to increase plant capacity. The machine would cost $18,000 with a useful life of six years and no salvage value. The company uses straight-line depreciation on all plant assets. (Ignore income taxes). 1) If the firm holds the sales price constant and makes the suggested changes, how many units of product will the company have to sell to make the same net income as last year?arrow_forwardIPort Products makes cases for portable music players in two processes, cutting and sewing. The cutting process has a capacity of 115,000 units per year; sewing has a capacity of 150,000 units per year. Cost information follows. Inspection and testing costs $ 47,500 Scrap costs (all in the cutting dept.) 147,500 Demand is very strong. At a sales price of $15.00 per case, the company can sell whatever output it can produce. IPort Products can start only 115,000 units into production in the Cutting Department because of capacity constraints. Defective units are detected at the end of production in the Cutting Department. At that point, defective units are scrapped. Of the 115,000 units started at the cutting operation, 17,250 units are scrapped. Unit costs in the Cutting Department for both good and defective units equal $11.30 per unit, including an allocation of the total fixed manufacturing costs of $264,500 per year to units. Direct…arrow_forward
- HH Co. uses corrugated cardboard to ship its product to customers. Currently, the company’s returns department incurs annual overhead costs of $126,000 and forecasts 6,000 returns per year. Management believes it has found a better way to package its products. As a result, the company expects to reduce the number of shipments that are returned due to damage by 3%. In addition, the initiative is expected to reduce the department’s annual overhead by $14,000.Compute the returns department’s standard overhead rate per return (a) before the sustainability improvement and (b) after the sustainability improvement.arrow_forward“I’m not sure we should lay out $350,000 for that automated welding machine,” said Jim Alder, president of the Superior Equipment Company. “That’s a lot of money, and it would cost us $94,000 for software and installation, and another $60,000 per year just to maintain the thing. In addition, the manufacturer admits it would cost $57,000 more at the end of three years to replace worn-out parts.” “I admit it’s a lot of money,” said Franci Rogers, the controller. “But you know the turnover problem we’ve had with the welding crew. This machine would replace six welders at a cost savings of $124,000 per year. And we would save another $8,500 per year in reduced material waste. When you figure that the automated welder would last for six years, I’m sure the return would be greater than our 15% required rate of return.” “I’m still not convinced,” countered Mr. Alder. “We can only get $22,000 scrap value out of our old welding equipment if we sell it now, and in six years the new machine…arrow_forwardWaterways is considering the replacement of an antiquated machine that has been slowing down production because of breakdowns and added maintenance. The operations manager estimates that this machine still has 2 more years of possible use. The machine produces an average of 60.00 units per day at a unit cost of $6.80, whereas other similar machines are producing twice that much. The units sell for $9.00. Sales are equal to production on these units, and production runs for 260 days each year. The replacement machine would cost $71,940 and have a 2-year life. Given the information above, what are the consequences of Waterways replacing the machine that is slowing down production because of breakdowns? Replacing the machine will result in a net loss of $ . Waterways should keep the old iarrow_forward
- hello, can someone help me out with this ?arrow_forwardDomesticarrow_forwardArtisan Metalworks has a bottleneck in their production that occurs within the engraving department. Jamal Moore, the COO, is considering hiring an extra worker, whose salary will be $54,000 per year, to solve the problem. With this extra worker, the company could produce and sell 2,900 more units per year. Currently, the selling price per unit is $25.00 and the cost per unit is $7.50. Direct materials $3.40 Direct labor Variable overhead Fixed overhead (primarily depreciation of equipment) Total 1.00 0.40 2.70 $7.50 Using the Information provided, calculate the annual financial Impact of hiring the extra worker. Profit $ ✓ Increasearrow_forward
- Futura Company purchases the 60,000 starters that it installs in its standard line of farm tractors from a supplier for the price of $10.40 per unit. Due to a reduction in output, the company now has idle capacity that could be used to produce the starters rather than buying them from an outside supplier. However, the company’s chief engineer is opposed to making the starters because the production cost per unit is $11.20 as shown below: Per Unit Total Direct materials $ 5.00 Direct labor 2.50 Supervision 1.70 $ 102,000 Depreciation 1.10 $ 66,000 Variable manufacturing overhead 0.40 Rent 0.50 $ 30,000 Total product cost $ 11.20 If Futura decides to make the starters, a supervisor would have to be hired (at a salary of $102,000) to oversee production. However, the company has sufficient idle tools and machinery such that no new equipment would have to be purchased. The rent charge above is based on space utilized in the plant. The total rent on the…arrow_forwardOriole Inc. manufactures snowsuits. Oriole is considering purchasing a new sewing machine at a cost of $2.45 million. Its existing machine was purchased 5 years ago at a price of $1.8 million; six months ago, Oriole spent $55,000 to keep it operational. The existing sewing machine can be sold today for $211,855. The new sewing machine would require a one-time, $85,000 training cost. Operating costs would decrease by the following amounts for years 1 to 7: Year 1 2 3 4 5 6 7 $390,600 399,400 411,000 425.900 432,000 434,600 436,400 The new sewing machine would be depreciated according to the declining-balance method at a rate of 20%. The salvage value is expected to be $379,400. This new equipment would require maintenance costs of $94,200 at the end of the fifth year. The cost of capital is 9%. Click here to view PV tablearrow_forwardA machine that produces a certain piece must be turned off by the operator after each piece is completed. The machine "coasts" for 15 seconds after it is turned off, thus preventing the operator from removing the piece quickly before producing the next piece. An engineer has suggested installing a brake that would reduce the coasting time to 3 seconds. The machine produces 50,000 pieces a year. The time to produce one piece is 1 minute 45 seconds, excluding coastint time. The operator earns $13 an hour and direct costs for operation are $2 an hour. The direct costs are incurred whenever the operator has to work. The brake will require servicing every 587 hours of operation. It will take the operator 30 minutes to perform the necessary maintenance and will require $60 in parts and material. The brake is expected to last 7,500 hours of operation (with proper maintenance) and will have no salvage value. How much could be spent for the brake if the Minimum Attractive Rate of Return is 10%…arrow_forward
arrow_back_ios
SEE MORE QUESTIONS
arrow_forward_ios
Recommended textbooks for you
- Essentials Of InvestmentsFinanceISBN:9781260013924Author:Bodie, Zvi, Kane, Alex, MARCUS, Alan J.Publisher:Mcgraw-hill Education,
- Foundations Of FinanceFinanceISBN:9780134897264Author:KEOWN, Arthur J., Martin, John D., PETTY, J. WilliamPublisher:Pearson,Fundamentals of Financial Management (MindTap Cou...FinanceISBN:9781337395250Author:Eugene F. Brigham, Joel F. HoustonPublisher:Cengage LearningCorporate Finance (The Mcgraw-hill/Irwin Series i...FinanceISBN:9780077861759Author:Stephen A. Ross Franco Modigliani Professor of Financial Economics Professor, Randolph W Westerfield Robert R. Dockson Deans Chair in Bus. Admin., Jeffrey Jaffe, Bradford D Jordan ProfessorPublisher:McGraw-Hill Education
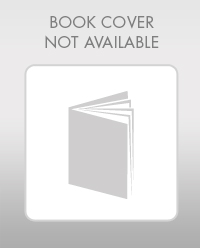
Essentials Of Investments
Finance
ISBN:9781260013924
Author:Bodie, Zvi, Kane, Alex, MARCUS, Alan J.
Publisher:Mcgraw-hill Education,
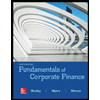
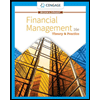
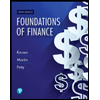
Foundations Of Finance
Finance
ISBN:9780134897264
Author:KEOWN, Arthur J., Martin, John D., PETTY, J. William
Publisher:Pearson,
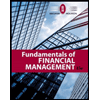
Fundamentals of Financial Management (MindTap Cou...
Finance
ISBN:9781337395250
Author:Eugene F. Brigham, Joel F. Houston
Publisher:Cengage Learning
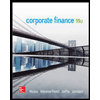
Corporate Finance (The Mcgraw-hill/Irwin Series i...
Finance
ISBN:9780077861759
Author:Stephen A. Ross Franco Modigliani Professor of Financial Economics Professor, Randolph W Westerfield Robert R. Dockson Deans Chair in Bus. Admin., Jeffrey Jaffe, Bradford D Jordan Professor
Publisher:McGraw-Hill Education