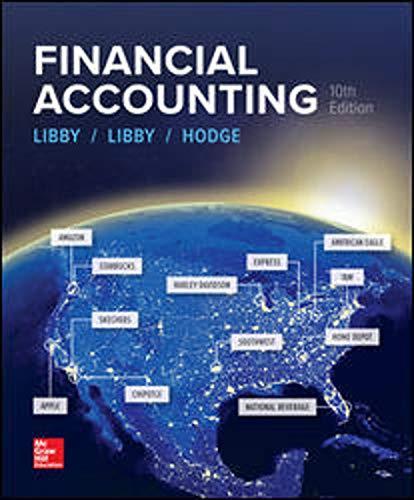
Problem 9
Comely Products manufactures three products R, S and T, in a joint Process. For every ten kilos of raw materials input, the output is five kilos of R, three kilos of S and two kilos of T. During August, 50,000 kilos of raw materials costing P120,000 were processed and completed, with joint conversion costs of P200,000. Conversion costs are to be allocated to the products on the basis of market values. To make the products saleable, further processing which does not require additional raw materials was done at the following costs:
|
Further processing cost |
Selling Price |
Product R |
P30,000 |
P10.00 |
Product S |
P20,000 |
P12.00 |
Product T |
P30,000 |
P15.00 |
Assuming that all units are sold, the gross margin on sales for Product S is

Step by stepSolved in 2 steps

- Question 8 Cost per Equivalent Unit The cost of direct materials transferred into the Filling Department of Eve Cosmetics Company is $128,400. The conversion cost for the period in the Filling Department is $140,740. The total equivalent units for direct materials and conversion are 42,800 ounces and 45,400 ounces, respectively. Determine the direct materials and conversion costs per equivalent unit. If required, round to the nearest cent. Direct materials cost per equivalent unit: $fill in the blank 1 per ounce Conversion costs per equivalent unit: $fill in the blank 2 per ouncearrow_forwardVikramarrow_forwardActivity Cost Driver Chosen asAllocation Base Conversion Cost Per Unit ofAllocation Base Materials handling Number of parts $1.00 Machining Machine hours 60.00 Packaging Number of finished units 2.00 Each windsock requires three parts and spends five minutes in the machining department. The total cost of direct materials and direct labor is $3.50 per windsock. Gale produces 20,000 windsocks each year and sells them at 140% of cost. The selling price per windsock is: Question 8 options: $13.50. $18.90. $16.10. $88.20.arrow_forward
- Question Content Area Prior to installing a JIT system, Grindstone Company used machine hours to assign maintenance costs to its three products of 4-inch, 6-inch, and 9-inch insulation. The maintenance costs totaled $432,000 per year. The machine hours used by each product and the quantity produced of each product are as follows: Machine Hours Quantity Produced 4-inch 5,000 15,000 rolls 6-inch 12,000 12,500 rolls 9-inch 7,000 11,200 rolls After installing JIT, three manufacturing cells were created, and the cell workers were trained to perform maintenance. Maintenance costs for the three cells still totaled $432,000; however, these costs are now traceable to each cell. Cell, 4-inch $125,000 Cell, 6-inch 175,000 Cell, 9-inch 165,000 The maintenance cost per roll of 9-inch insulation before JIT is installed would be a. $14.00. b. $11.25. c. $7.75. d. $30.00.arrow_forwardQUESTION 4 An organisation manufactures a single product. The following information with regard to the raw material needed in the production process is supplied to you: Normal delivery time: 2.5 weeksMaximum delivery time: 3.5 weeksNormal usage: 52 000 units per yearPurchase price per unit: R8.50Cost of placing an order: R18.00Interest rate: 2% per yearStoring cost per unit: R2.50 Required: Calculate the re-order point if the organisation has a policy to keep safety stock. Calculate the safety stock that should be kept by the organisation.arrow_forward1arrow_forward
- Activity Cost Driver Chosen asAllocation Base Conversion Cost Per Unit ofAllocation Base Materials handling Number of parts $1.00 Machining Machine hours 60.00 Packaging Number of finished units 2.00 Each windsock requires three parts and spends five minutes in the machining department. The total cost of direct materials and direct labor is $3.50 per windsock. Gale produces 20,000 windsocks each year and sells them at 140% of cost. The total cost of producing the 20,000 windsocks is: Question 7 options: $160,000. $230,000. $270,000. $1,260,000.arrow_forward4. PT Prahasta produces products through two departments with cost calculations using the weighted average method. In early March 2022, the department 1 has 25 units of product in progress with a completion rate of 100% cost raw materials and 50% conversion costs. Products added in the month process this is 100 units, while the finished ones are processed and transferred to the department 2 as many as 110 units. At the end of the month, unfinished products are already processed absorbs 100% raw material costs and 75% conversion costs. Department 2 completes production and transfers 120 units to the warehouse and at the end of the month, there are still 10 units left with a completion rate of 30% labor costs and 70% factory overhead costs. At the beginning of the month the product in process in this department has absorbed 30% labor costs and 50% factory overhead costs. It is known that the cost of goods in the process at the beginning of the month in department 1 is Rp. 15,000 for raw…arrow_forwardBarrett Chemicals manufactures four chemicals, Chem-1, Chem-2, Chem-3, and Chem-4, from a joint process. The total joint costs in May were $594,000. Additional information follows: Product Units Produced Sales Value at Split-Off If Processed Further Additional Costs Sales Values Chem-1 264,000 $ 200,640 $ 29,040 $ 237,600 Chem-2 176,000 264,000 28,160 288,640 Chem-3 200,000 156,000 24,000 187,500 Chem-4 160,000 272,000 28,800 300,000 800,000 $ 892,640 $ 110,000 $ 1,013,740 Required: Barrett Chemicals uses the physical quantities method to allocate joint costs. What joint costs would be allocated to each product in May?arrow_forward
- am.1234.arrow_forwardBarrett Chemicals manufactures four chemicals, Chem-1, Chem-2, Chem-3, and Chem-4, from a joint process. The total joint costs in May were $564,000. Additional information follows: Product Chem-1 Chem-2 Chem-3 Chem-4 Units Produced 288,000 176,000 192,000 144,000 800,000 Chem-1 Chem-2 Chem-3 If Processed Further Required: Which, if any, of the four products would you recommend Barrett Chemicals sell at split-off (and not process further)? Note: You may select more than one answer. Single click the box with the question mark to produce a check mark for a correct answer and double click the box with the question mark to empty the box for a wrong answer. Any boxes left with a question mark will be automatically graded as incorrect. Chem-4 Sales Value at Additional Split-Off Costs $ 220,000 264,000 149,600 246,400 $ 880,000 $ 32,700 29,400 24,900 26,300 $ 113,300 Sales Values $ 260,000 290,000 180,000 270,000 $ 1,000,000 harrow_forwardChem Manufacturing Company processes direct materials up to the splitoff point where two products (X and Y) are obtained and sold. The following information was collected for the month of November: Production: X 3000 gallons, Y 2000 gallons . Sales: X 2600 at $15 per gallon ,Y 1700 at $10 per gallon. The joint cost was $20000. No beginning inventories of X and Y. --- Using the physical-volume method, joint cost allocated for X : Select one: O a. $20000 O b. $8000 c. $12000 O d. $10000arrow_forward
- AccountingAccountingISBN:9781337272094Author:WARREN, Carl S., Reeve, James M., Duchac, Jonathan E.Publisher:Cengage Learning,Accounting Information SystemsAccountingISBN:9781337619202Author:Hall, James A.Publisher:Cengage Learning,
- Horngren's Cost Accounting: A Managerial Emphasis...AccountingISBN:9780134475585Author:Srikant M. Datar, Madhav V. RajanPublisher:PEARSONIntermediate AccountingAccountingISBN:9781259722660Author:J. David Spiceland, Mark W. Nelson, Wayne M ThomasPublisher:McGraw-Hill EducationFinancial and Managerial AccountingAccountingISBN:9781259726705Author:John J Wild, Ken W. Shaw, Barbara Chiappetta Fundamental Accounting PrinciplesPublisher:McGraw-Hill Education
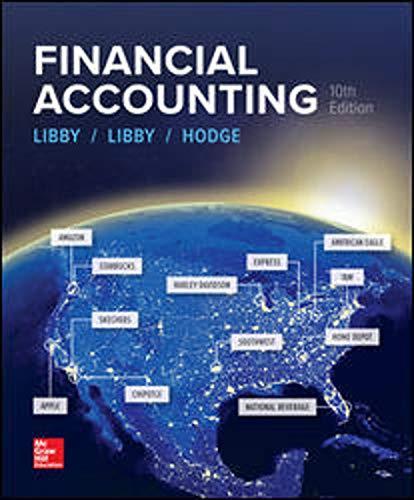
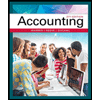
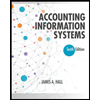
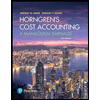
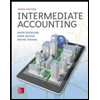
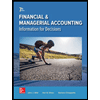