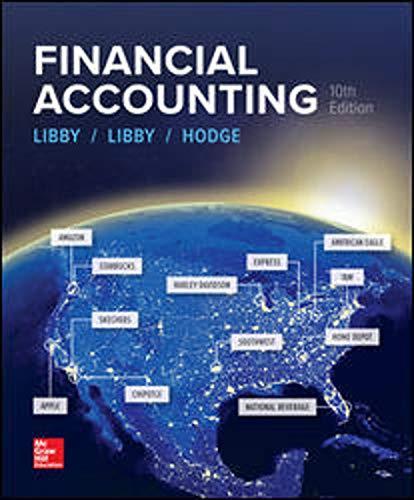
FINANCIAL ACCOUNTING
10th Edition
ISBN: 9781259964947
Author: Libby
Publisher: MCG
expand_more
expand_more
format_list_bulleted
Concept explainers
Topic Video
Question
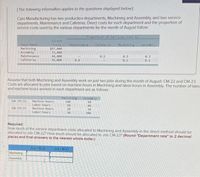
Transcribed Image Text:[The following information applies to the questions displayed beiow.)
Caro Manufacturing has two production departments, Machining and Assembly, and two service
departments, Maintenance and Cafeteria. Direct costs for each department and the proportion of
service costs used by the various departments for the month of August follow:
Proportion of Services Used by
Direct
Costs
Maintenance
Cafeteria
Machining
Assembly
Depantment
Machining
Assembly
$97,000
72,400
44, 800
36,000
Maintenance
0.2
0.5
0.3
Cafeteria
0.8
0.1
0.1
Assume that both Machining and Assembly work on just two jobs during the month of August: CM-22 and CM-23.
Costs are allocated to jobs based on machine-hours in Machining and labor-hours in Assembly. The number of labo.
and machine-hours worked in each department are as follows:
Machining
360
Assembly
Job CM-22: Machine-hours
60
Labor-hours
Machine-hours
Labor-hours
se
40
30
Job CM-23:
20
30
340
Required:
How much of the service department costs allocated to Machining and Assembly in the direct method should be
allocated to Job CM-22? How much should be allocated to Job CM-23? (Round "Department rate" to 2 decimal
places and final answers to the nearest whole doller.)
Job CM-22
Job CM-23
Machining
Assembly
Expert Solution

This question has been solved!
Explore an expertly crafted, step-by-step solution for a thorough understanding of key concepts.
This is a popular solution
Trending nowThis is a popular solution!
Step by stepSolved in 3 steps

Knowledge Booster
Learn more about
Need a deep-dive on the concept behind this application? Look no further. Learn more about this topic, accounting and related others by exploring similar questions and additional content below.Similar questions
- Hanshabenarrow_forwardDawson Company manufactures small table lamps and desk lamps. The following shows the activities per product and the total overhead information: Units Setups Inspections Assembly (dlh) 2,700 4,000 8,000 8,000 Small table lamps Desk lamps Activity Setups 9,150 15,250 44,400 44,400 Total Activity-Base Usage Budgeted Activity Cost 12,000 $102,000 24,400 129,320 77,700 310,800 Inspections Assembly (dlh) The total factory overhead to be allocated to desk lamps is Oa. $456,995 Ob. $228,498 Oc. $587,565 Od. $326,425arrow_forwardRiverbed Manufacturing has five activity cost pools and two products (a budget tape vacuum and a deluxe tape vacuum). Information is presented below: Activity Cost Pools Ordering and Receiving Machine Setup Machining Assembly Inspection Budget $ Cost Driver Orders Setups Machine hours Deluxe $ Parts Inspections Overhead cost per unit Est. Overhead $144,000 311,400 1,023,000 1,624,000 314,000 per unit Est. Use of Cost Drivers Budget per unit 600 500 150,000 1.200,000 550 Deluxe 400 Compute the overhead cost per unit for each product. Production is 700.000 units of Budget and 200.000 units of Deluxe. (Round per machine hour and per part values to 3 decimal places, eg 52.711. Round overhead cost per unit to 2 decimal places, e.g. 12.25 and cost assigned to 0 decimal places, eg. 2,500.) 400 100,000 800,000 450arrow_forward
- answer in text form please (without image)arrow_forwardSupport department cost allocation-direct method Becker Tabletops has two support departments (Janitorial and Cafeteria) and two production departments (Cutting and Assembly). Relevant details for these departments are as follows: Support Department Janitorial Department Cafeteria Department Cost Driver Square footage to be serviced Number of employees Janitorial Department $320,000 Janitorial Department cost allocation Cafeteria Department cost allocation Cafeteria Department $170,000 4,500 3 44 10 Department costs Square feet Number of employees Allocate the support department costs to the production departments using the direct method. Cutting Department $ Cutting Department $1,510,000 $ 700 27 Assembly Department $680,000 6,300 3 Assembly Departmentarrow_forwardUsing the sequential method, Pone Hill Company allocates Janitorial Department costs based on square footage serviced. It allocates Cafeteria Department costs based on the number of employees served. It has determined to allocate Janitorial costs before Cafeteria costs. It has the following information about its two service departments and two production departments, Cutting and Assembly: Line Item Description Costs Square Feet Number ofEmployees Janitorial Department $450,000 100 20 Cafeteria Department 200,000 10,000 10 Cutting Department 1,500,000 2,000 60 Assembly Department 3,000,000 8,000 20 The percentage (proportional) usage of the Janitorial Department by the Cutting Department is a. 80% b. 9% c. 10% d. 20%arrow_forward
- Dhapaarrow_forwardMervon Company has two operating departments: Mixing and Bottling. Mixing occupies 24,660 square feet. Bottling occupies 16,440 square feet. Indirect factory costs include maintenance costs of $234,000. If maintenance costs are allocated to operating departments based on square footage occupied, determine the amount of maintenance costs allocated to each operating department.arrow_forwardMack Precision Tool and Die has two production departments, Fabricating and Finishing, and two service departments, Repair and Quality Control. Direct costs for each department and the proportion of service costs used by the various departments for the month of March follow: Proportion of Services Used by Department Fabricating Direct Costs Repair $ 134,600 Quality Control Fabricating Finishing Finishing 98,200 Repair Quality Control 42,000 78,400 0 0.2 0.5 0.3 0.6 0 0.2 0.2 Required: Use the step method to allocate the service costs, using the following: a. The order of allocation starts with Repair. b. The allocations are made in the reverse order (starting with Quality Control). Complete this question by entering your answers in the tabs below. Required A Required B Use the step method to allocate the service costs, using the following: The allocations are made in the reverse order (starting with Quality Control). Note: Amounts to be deducted should be indicated by a minus sign. Do…arrow_forward
- 1.Smith Manufacturing has five activity cost pools and two products (a budget toaster oven and a deluxe toaster oven). Information is presented below: Activity. Cost Pool Ordering and Receiving Machine Setup Machining Assembly Inspection Cost Driver Orders Setups Machine hours Parts Inspections Est. Overhead $ 130,000 297,000 1,000,000 1,600,000 300,000 Cost Drivers by Product Budget 600 500 150,000 1,200,000 550 Deluxe 400 400 100,000 800,000 450 Instructions Compute the overhead cost per unit for each product. Production is 700,000 units of Budget and 200,000 units of Deluxe. Round your answer to the nearest cent.arrow_forwardMack Precision Tool and Die has two production departments, Fabricating and Finishing, and two service departments, Repair and Quality Control. Direct costs for each department and the proportion of service costs used by the various departments for the month of March follow: Department Fabricating Finishing Repair Quality Control Required A Required B Direct Costs Repair $ 136,600 102, 200 43,800 81,800 Required: Use the step method to allocate the service costs, using the following: From: a. The order of allocation starts with Repair. b. The allocations are made in the reverse order (starting with Quality Control). Service department costs Repair Quality control Total costs allocated Complete this question by entering your answers in the tabs below. $ $ Repair Proportion of Services Used by Quality Control 0 0.8 Use the step method to allocate the service costs, using the following: The order of allocation starts with Repair. Note: Amounts to be deducted should be indicated by a minus…arrow_forwardTidwell Industries has the following overhead costs and cost drivers. Direct labor hours are estimated at 100,000 for the year. Activity Cost Pool Ordering and Receiving Machine Setup Machining Assembly I Inspection ( Cost Driver $1.20 per direct labor hour. $240 per order. $0.12 per part. $6,834 per order. Orders Setups Machine hours Parts Inspections Est. Overhead $ 120,000 297,000 1,500,000 1,200,000 MA 300,000 Cost Driver Activity W 500 orders 450 setups If overhead is applied using activity-based costing, the overhead application rate for ordering and receiving is 125,000 MH 1,000,000 parts 500 inspections P s 240arrow_forward
arrow_back_ios
SEE MORE QUESTIONS
arrow_forward_ios
Recommended textbooks for you
- AccountingAccountingISBN:9781337272094Author:WARREN, Carl S., Reeve, James M., Duchac, Jonathan E.Publisher:Cengage Learning,Accounting Information SystemsAccountingISBN:9781337619202Author:Hall, James A.Publisher:Cengage Learning,
- Horngren's Cost Accounting: A Managerial Emphasis...AccountingISBN:9780134475585Author:Srikant M. Datar, Madhav V. RajanPublisher:PEARSONIntermediate AccountingAccountingISBN:9781259722660Author:J. David Spiceland, Mark W. Nelson, Wayne M ThomasPublisher:McGraw-Hill EducationFinancial and Managerial AccountingAccountingISBN:9781259726705Author:John J Wild, Ken W. Shaw, Barbara Chiappetta Fundamental Accounting PrinciplesPublisher:McGraw-Hill Education
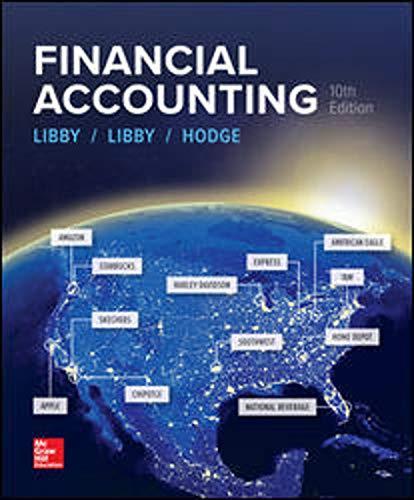
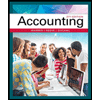
Accounting
Accounting
ISBN:9781337272094
Author:WARREN, Carl S., Reeve, James M., Duchac, Jonathan E.
Publisher:Cengage Learning,
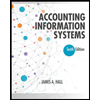
Accounting Information Systems
Accounting
ISBN:9781337619202
Author:Hall, James A.
Publisher:Cengage Learning,
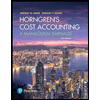
Horngren's Cost Accounting: A Managerial Emphasis...
Accounting
ISBN:9780134475585
Author:Srikant M. Datar, Madhav V. Rajan
Publisher:PEARSON
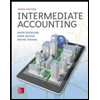
Intermediate Accounting
Accounting
ISBN:9781259722660
Author:J. David Spiceland, Mark W. Nelson, Wayne M Thomas
Publisher:McGraw-Hill Education
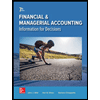
Financial and Managerial Accounting
Accounting
ISBN:9781259726705
Author:John J Wild, Ken W. Shaw, Barbara Chiappetta Fundamental Accounting Principles
Publisher:McGraw-Hill Education