Cain Components manufactures and distributes various plumbing products used in homes and other buildings. Over time, the production staff has noticed that products they considered easy to make were difficult to sell at margins considered reasonable, while products that seemed to take a lot of staff time were selling well despite recent price increases. A summer intern has suggested that the cost system might be providing misleading information. The controller decided that a good summer project for the intern would be to develop, in one self-contained area of the plant, an alternative cost system with which to compare the current system. The intern identified the following cost pools and, after discussion with some plant personnel, appropriate cost drivers for each pool. There were: Cost Pools Costs Activity Drivers Receiving $ 600,000 Direct material cost Manufacturing 5,500,000 Machine-hours Machine setup 900,000 Production runs Shipping 1,000,000 Units shipped In this particular area, Cain produces two of its many products: Standard and Deluxe. The following are data for production for the latest full year of operations. Products Standard Deluxe Total direct material costs $ 165,000 $ 235,000 Total direct labor costs $ 650,000 $ 410,000 Total machine-hours 118,000 132,000 Total number of setups 155 45 Total pounds of material 10,000 17,000 Total direct labor-hours 6,800 4,550 Number of units produced and shipped 16,000 9,000
Cain Components manufactures and distributes various plumbing products used in homes and other buildings. Over time, the production staff has noticed that products they considered easy to make were difficult to sell at margins considered reasonable, while products that seemed to take a lot of staff time were selling well despite recent price increases. A summer intern has suggested that the cost system might be providing misleading information.
The controller decided that a good summer project for the intern would be to develop, in one self-contained area of the plant, an alternative cost system with which to compare the current system. The intern identified the following cost pools and, after discussion with some plant personnel, appropriate cost drivers for each pool. There were:
Cost Pools | Costs | Activity Drivers | |
Receiving | $ | 600,000 | Direct material cost |
Manufacturing | 5,500,000 | Machine-hours | |
Machine setup | 900,000 | Production runs | |
Shipping | 1,000,000 | Units shipped | |
In this particular area, Cain produces two of its many products: Standard and Deluxe. The following are data for production for the latest full year of operations.
Products | ||||||
Standard | Deluxe | |||||
Total direct material costs | $ | 165,000 | $ | 235,000 | ||
Total direct labor costs | $ | 650,000 | $ | 410,000 | ||
Total machine-hours | 118,000 | 132,000 | ||||
Total number of setups | 155 | 45 | ||||
Total pounds of material | 10,000 | 17,000 | ||||
Total direct labor-hours | 6,800 | 4,550 | ||||
Number of units produced and shipped | 16,000 | 9,000 | ||||
The costs attributed to production are $13,020,000 and the costs attributed to engineering are $5,796,000. After discussion with plant engineers, the intern decides that the best cost driver for engineering is setups, because most of the work arises from changes in the way the product is run.
Required:
a-1. Compute the totals of the cost driver rates shown below.
a-2. What unit product costs will be reported for the two products if the revised ABC system is used?

Trending now
This is a popular solution!
Step by step
Solved in 3 steps

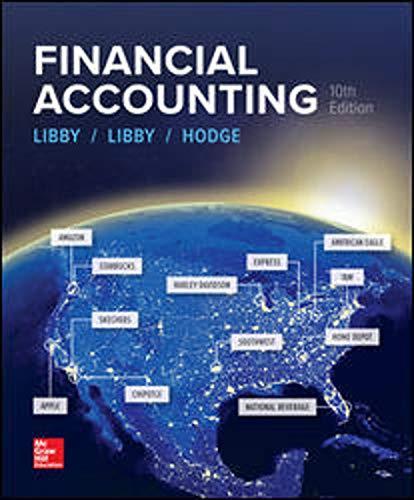
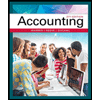
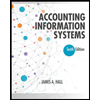
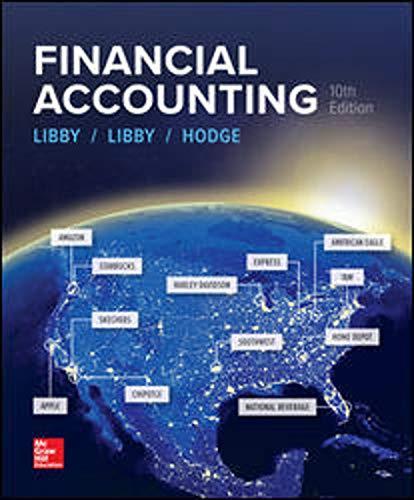
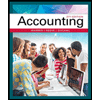
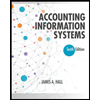
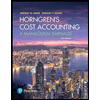
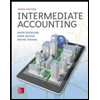
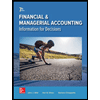