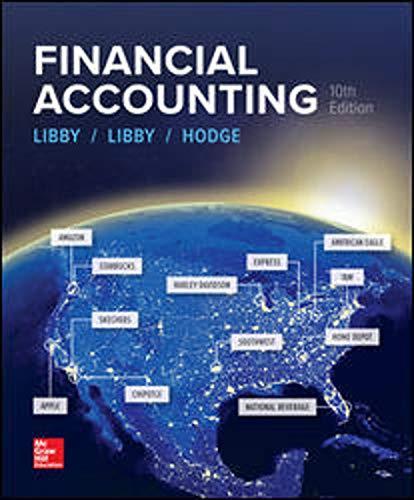
Concept explainers
Chocolate Bars, Inc. (CBI), manufactures creamy deluxe chocolate candy bars. The firm has developed three distinct products: Almond Dream, Krispy Krackle, and Creamy Crunch.
CBI is profitable, but management is quite concerned about the profitability of each product and the product costing methods currently employed. In particular, management questions whether the
In reviewing cost reports with the marketing manager, Steve Hoffman, who is the cost accountant, notices that Creamy Crunch appears exceptionally profitable and that Almond Dream appears to be produced at a loss. This surprises both him and the manager, and after much discussion, they are convinced that the cost accounting system is at fault and that Almond Dream is performing very well at the current market price.
Steve decides to hire Jean Sharpe, a management consultant, to study the firm’s cost system over the next month and present her findings and recommendations to senior management. Her objective is to identify and demonstrate how the cost accounting system might be distorting the firm’s product costs.
Jean begins her study by gathering information and documenting the existing cost accounting system. It is rather simplistic, using a single overhead allocation base—direct labor-hours—to calculate and apply overhead rates to all products. The rate is calculated by summing variable and fixed overhead costs and then dividing the result by the number of direct labor-hours. The product cost is determined by multiplying the number of direct labor-hours required to manufacture the product by the overhead rate and adding this amount to the direct labor and direct material costs.
CBI engages in two distinct production processes for each product. Process 1 is labor intensive, using a high proportion of direct materials and labor. Process 2 uses special packing equipment that wraps each individual candy bar and then packs it into a box of 24 bars. The boxes are then packaged into cases, each of which has six boxes. Special packing equipment is used on all three products and has a monthly capacity of 3,000 cases, each containing 144 candy bars (= 6 boxes × 24 bars).
To illustrate the source of the distortions to senior management, Jean collects the cost data for the three products, Almond Dream, Krispy Krackle, and Creamy Crunch.
Almond Dream | Krispy Krackle | Creamy Crunch | ||||
Product costs | ||||||
Labor-hours per case | 8.1 | 4.1 | 1.0 | |||
Total cases produced | 1,000 | 1,000 | 1,000 | |||
Material cost per case | $ | 9.10 | $ | 3.10 | $ | 9.60 |
Direct labor cost per case | $ | 48.60 | $ | 24.60 | $ | 6.00 |
Labor-hours per product | 8,100 | 4,100 | 1,000 | |||
Total overhead = $75,000 | ||||||
Total labor-hours = 13,200 | ||||||
Direct labor costs per hour = $6.00 | ||||||
Allocation rate per labor-hour = (a). | ||||||
Costs of products | ||||||
Material cost per case | $ | 9.10 | $ | 3.10 | $ | 9.60 |
Direct labor cost per case | 48.60 | 24.60 | 6.00 | |||
Allocated overhead per case(to be computed) | (b) | (c) | (d) | |||
Product cost | (e) | (f) | (g) | |||
CBI recently adopted a general policy to discontinue all products whose gross profit margin percentages [(Gross margin ÷ Selling price) × 100] were less than 10 percent. By comparing the selling prices to the firm’s costs and then calculating the gross margin percentages, Jean could determine which products, under the current cost system, should be dropped. The current selling prices of Almond Dream, Krispy Krackle, and Creamy Crunch are $96.00, $60.00, and $28.00 per case, respectively. Overhead will remain $75,000 per month under all alternatives.
Required:
a-1. Complete the table under the current cost system.
a-2. Determine which product(s), if any, should be dropped.
Reg A1
Complete the table under the current cost system. (Round your intermediate calculations and final answers to 2 decimal places. Negative values should be indicated with a minus sign.)
|
|
- Reg A2
-
Determine which product(s), if any, should be dropped.
Almond Dreamradio button unchecked1 of 3 Krispy Krackleradio button unchecked2 of 3 Creamy Crunchradio button unchecked3 of 3

Trending nowThis is a popular solution!
Step by stepSolved in 2 steps

- Techno Instruments uses a manufacturing costing system with one direct-cost category (direct materials) and three indirect-cost categories: a. Setup, production-order, and materials-handling costs that vary with the number of batches b. Manufacturing-operations costs that vary with machine-hours c. Costs of engineering changes that vary with the number of engineering changes made In response to competitive pressures at the end of 2016, Techno Instruments used value-engineering techniques to reduce manufacturing costs. Actual information for 2016 and 2017 is as follows: 2016 2017 Setup, production-order, and materials-handling costs per batch $8,600 $7,800 Total manufacturing-operations cost per machine-hour $59 $53 Cost per engineering change $18,750 $14,000 The management of Techno Instruments wants to evaluate whether value engineering has succeeded in reducing the target manufacturing cost per unit of one…arrow_forwardChocolate Bars, Inc. (CBI), manufactures creamy deluxe chocolate candy bars. The firm has developed three distinct products: Almond Dream, Krispy Krackle, and Creamy Crunch. CBI is profitable, but management is quite concerned about the profitability of each product and the product costing methods currently employed. In particular, management questions whether the overhead allocation base of direct labor-hours accurately reflects the costs incurred during the production process of each product. In reviewing cost reports with the marketing manager, Steve Hoffman, who is the cost accountant, notices that Creamy Crunch appears exceptionally profitable and that Almond Dream appears to be produced at a loss. This surprises both him and the manager, and after much discussion, they are convinced that the cost accounting system is at fault and that Almond Dream is performing very well at the current market price. Steve decides to hire Jean Sharpe, a management consultant, to study the…arrow_forwardVishanuarrow_forward
- Maglie Company manufactures two video game consoles: handheld and home. The handheld consoles are smaller and less expensive than the home consoles. The company only recently began producing the home model. Since the introduction of the new product, profits have been steadily declining. Management believes that the accounting system is not accurately allocating costs to products, particularly because sales of the new product have been increasing. Management has asked you to investigate the cost allocation problem. You find that manufacturing overhead is currently assigned to products based on their direct labor costs. For your investigation, you have data from last year. Manufacturing overhead was $1,237,000 based on production of 290,000 handheld consoles and 100,000 home consoles. Direct labor and direct materials costs were as follows. Handheld Home Total Direct labor $ 1,135,250 $ 411,000 $ 1,546,250 Materials 700,000 671,000 1,371,000…arrow_forwardUtica Manufacturing (UM) was recently acquired by MegaMachines, Inc. (MM). and organized as a separate division within the company. Most manufacturing plants at MM use an ABC system, but UM has always used a traditional product costing system. Bob Miller, the plant controller at UM, has decided to experiment with ABC and has asked you to help develop a simple ABC system that would help him decide if it was useful. The controller's staff has identified costs for the first month in the four overhead cost pools along with appropriate cost drivers for each pool. Activity Drivers Direct material cost Costs 154, 000 1,600, 900 900, 000 450, 000 Cost Pools Incoming inspection Production Machine-hours Machine setup Shipping Setups Units shipped The company manufactures two basic products with model numbers 308 and 510. The following are data for production for the first month as part of MM. Products 308 510 $ 45,000 $173,800 50,000 $ 32,000 $283,809 118,800 Total direct material costs Total…arrow_forwardNote:- Do not provide handwritten solution. Maintain accuracy and quality in your answer. Take care of plagiarism. Answer completely. You will get up vote for sure.arrow_forward
- AccountingAccountingISBN:9781337272094Author:WARREN, Carl S., Reeve, James M., Duchac, Jonathan E.Publisher:Cengage Learning,Accounting Information SystemsAccountingISBN:9781337619202Author:Hall, James A.Publisher:Cengage Learning,
- Horngren's Cost Accounting: A Managerial Emphasis...AccountingISBN:9780134475585Author:Srikant M. Datar, Madhav V. RajanPublisher:PEARSONIntermediate AccountingAccountingISBN:9781259722660Author:J. David Spiceland, Mark W. Nelson, Wayne M ThomasPublisher:McGraw-Hill EducationFinancial and Managerial AccountingAccountingISBN:9781259726705Author:John J Wild, Ken W. Shaw, Barbara Chiappetta Fundamental Accounting PrinciplesPublisher:McGraw-Hill Education
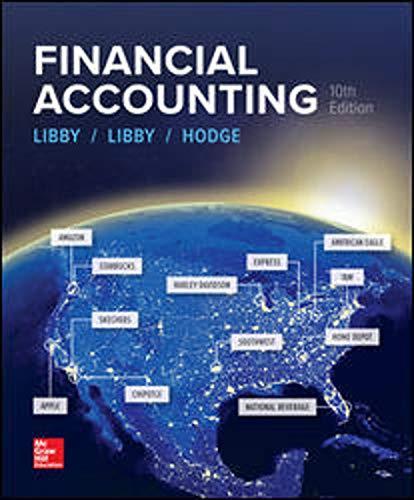
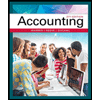
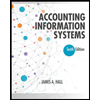
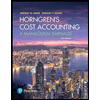
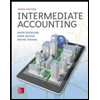
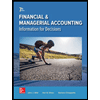