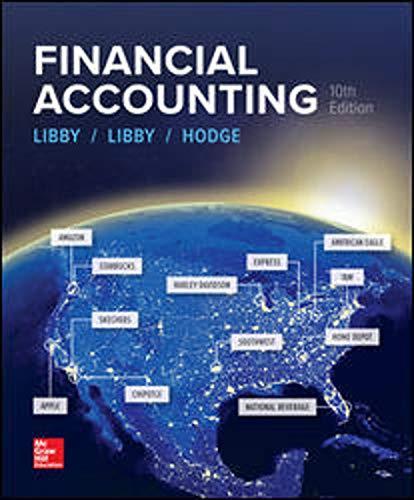
Concept explainers
Bouwens Corporation manufactures a solvent used in airplane maintenance shops. Bouwens sells the solvent to both U.S. military services and commercial airlines. The solvent is produced in a single plant in one of two buildings. Although the solvent sold to the military is chemically identical to that sold to the airlines, the company produces solvent for the two customer types in different buildings at the plant. The solvent sold to the military is manufactured in building 155 (B-155) and is labeled M-Solv. The solvent sold to the commercial airlines is manufactured in building 159 (B-159) and is labeled C-Solv.
B-155 is much newer and is considered a model work environment with climate control and other amenities. Workers at Bouwens, who all have roughly equal skills, bid on their job locations (the buildings they will work in) and are assigned based on bids and seniority. As workers gain seniority, they also receive higher pay.
The solvent sold to the two customers is essentially identical, but the military requires Bouwens to use a base chemical with a brand name, MX. The solvent for the commercial airlines is called CX. MX is required for military applications because it is sold by vendors on a preferred vendor list.
The company sells solvent for the market price to the airlines. Solvent sold to the military is sold based on cost plus a fixed fee. That is, the government pays Bouwens for the recorded cost of the solvent plus a fixed amount of profit. The cost can be computed according to "commonly used product cost methods, including
Currently, Bouwens uses a job costing system in which each month’s production for each customer type is considered a "job." Thus, every month, Bouwens starts and completes one job in B-155 and one job in B-159. (There is never any beginning or ending work in process at Bouwens.) Recently, a dispute arose between Jack, the product manager for the military solvent, and Jill, the product manager for the commercial solvent, over the proper costing system.
Jack: It is ridiculous to use job costing for this. We are producing solvent. Everyone knows that the chemicals are the same. The fact the B-155 has high-cost labor is because all the senior employees want to work there. We could produce the same product with the employees in B-159. We should be using process costing and consider all the production in both buildings for each month as the batch.
Jill: Jack, the fact is that the military requires us to use a special chemical, and their contracts require we keep track of the costs for their business. If we don’t separate the costing, we won’t know how profitable either business is.
The following is production and cost information for a typical month, July.
M-Solv (B-155) | C-Solv (B-159) | Total | |
---|---|---|---|
Units started | 2,000 | 10,000 | 12,000 |
Materials cost | $ 14,000 | $ 40,000 | $ 54,000 |
Conversion cost | 30,000 | 120,000 | 150,000 |
Total | $ 44,000 | $ 160,000 | $ 204,000 |
Required:
- Compute the unit costs of M-Solv and C-Solv for July using the current system (job costing) at Bouwens.
- Compute the costs of M-Solv and C-Solv for July if Bouwens were to treat all production as the same (combining B-155 and B-159 production).
- Recommend a costing method that best reflects the cost of producing M-Solv and C-Solv.
- For your recommended costing system, compute the cost of both M-Solv and C-Solv for July.
- Compute the unit costs for materials and conversion costs separately.
- Then compute conversion costs for the factory.
- Now, compute the unit product cost.
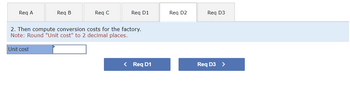
![**Instruction for Unit Product Cost Calculation:**
**3. Now, compute the unit product cost.**
*Note: Round your answers to 2 decimal places.*
---
**Cost Components Table:**
| | M-Solv (B-155) | C-Solv (B-159) |
|-----------------------|----------------|----------------|
| **Unit materials costs** | | |
| **Unit conversion costs** | | |
| **Total unit costs** | | |
---
**Navigation:**
- `< Req D2` (Previous Requirement)
- `Req D3 >` (Next Requirement) [Disabled]
---
In this exercise, you are required to compute the unit product costs for the products M-Solv (B-155) and C-Solv (B-159). Fill in the table with the accurate calculation of costs, considering both materials and conversion costs.](https://content.bartleby.com/qna-images/question/f00761e5-6ea2-4b64-9c87-d0591240e351/02b7908c-dfd9-4d31-b22d-ebd89fffc815/meu61s_thumbnail.png)

As per the Honor code of Bartleby we are bound to give the answer of the first three sub parts only, Please post the remaining sub part again Our other experts will assist you with that.
Job Costing: Accounting technique that tracks the cost of materials, labor, and overhead for a particular job. The main purpose of job costing is to determine the profit or loss of each job. Repetitive work or poorly allocated employees can be addressed for the upcoming project through job costs.
Process costing :
Operation costing method employed to determine the value of a product at each process or stage of the production process, applicable where goods produced from a series of continuous operations or procedures. Process costing is employed by businesses that manufacture goods and where production is in repetitive inflow.
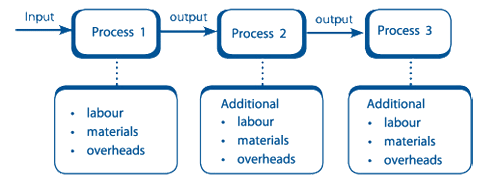
Operating costing : It combines the features of job costing and process costing wherein cost can be identified by preparing the cost sheet.
Step by stepSolved in 5 steps with 1 images

- Convert the accompanying database to an Excel table to find: a.The total cost of all orders. b.Thetotal quantity of airframe fasteners purchased. c. The total cost of all orders placed with Manley Valve. Question content area bottom Part 1 a. The total cost of all orders is $?????? enter your response here.arrow_forwardConvert the accompanying database to an excel table to find: a. The total cost of all orders b. The total quantity of airframe fasteners purchased. c. The total cost of all orders placed with Manley Valve.arrow_forwardsee enclosed jpeg please. Explain as clear as possible how you come to the solution.arrow_forward
- What I Know Before we begin this lesson, let us check first your prior knowledge on this module. After taking and checking this short test, take note of the items that you are not able to answer correctly and look for the right answer as you go through this module. Direction: Encircle the letter of the correct answer. 1. What type of cost includes product ingredients and materials? а. fixed b. revenue с. total d. variable 2. What type of cost includes the rental of space? а. fixed b. revenue c. total d. variable 3. What type of cost is the product of the price and the quantity sold? а. fixed b. revenue с. total d. variable 4. What concept is being described when the business will neither earn a profit nor suffer a loss? а. break-even b. loss с. profit d. summit 5. What type of analysis shows equal revenue and total cost? а. break-even b. cost of variable c. profit-loss d. volume of salesarrow_forwardCs Cases 1. Create a new Excel sheet in which you will find the delivery cost for each delivery. nal... a. Create a new sheet that has information for each delivery. Name this sheet "lookup." Rat... b. In this lookup sheet, look up the hourly rate for the driver for each delivery. Do not enter this information manually! Use the VLOOKUP function. c. For each delivery, calculate the delivery cost as hourly rate for the driver multiplied by time (hours). Fill in the table below for the first ten records. Date Delivery ID Driver Time (Hours) Hourly Rate Cost 20.00 X 1 George 1 1/1 25.00 X 2 Deanna 1.5 1/2 2 3 Ben 1/3 4 Caroline 2 1/3 < 5 Unknown 1 1/4 6 Elizabeth 2 1/5 7 Unknown 2.5 1/5 8 Unknown 1 1/6 9 Adam 2 1/8 10 Hannah 1.5 1/9 2. Create a new Excel sheet that aggregates the data contained in the lookup sheet to show each driver's activity analysis. a. Create a pivot table in a new sheet; name this new sheet "pivot table."arrow_forwardPlease see the pictures below for question details. Need help with this. Note that the pictures are the same, it is just showing what each part is asking for.arrow_forward
- darrow_forwardPlease help me with part a and part b thankuarrow_forward4. Change the estimated total amount of the allocation base back to 83,000 machine-hours, so that the data area of you workshe looks exactly the same as in Requirement 2. Now change the actual manufacturing overhead cost from $637,900 to $633,100. Th data area of your worksheet should now look like this: A в 1 Chapter 3: Applying Excel 2. Data Allocation base Estimated manufacturing overhead cost Estimated total amount of the allocation base Actual manufacturing overhead cost Actual total amount of the allocation base 4 Machine-hours 655,700 83,000 machine-hours 7 $ 633,100 78,000 machine-hours 8 (a) By how much is the manufacturing overhead underapplied or overapplied? manufacturing overhead 3. 5. 6.arrow_forward
- AccountingAccountingISBN:9781337272094Author:WARREN, Carl S., Reeve, James M., Duchac, Jonathan E.Publisher:Cengage Learning,Accounting Information SystemsAccountingISBN:9781337619202Author:Hall, James A.Publisher:Cengage Learning,
- Horngren's Cost Accounting: A Managerial Emphasis...AccountingISBN:9780134475585Author:Srikant M. Datar, Madhav V. RajanPublisher:PEARSONIntermediate AccountingAccountingISBN:9781259722660Author:J. David Spiceland, Mark W. Nelson, Wayne M ThomasPublisher:McGraw-Hill EducationFinancial and Managerial AccountingAccountingISBN:9781259726705Author:John J Wild, Ken W. Shaw, Barbara Chiappetta Fundamental Accounting PrinciplesPublisher:McGraw-Hill Education
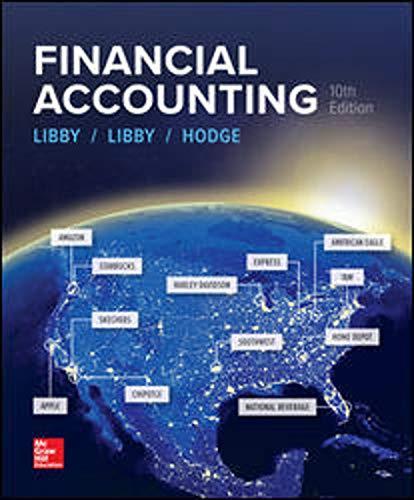
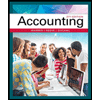
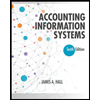
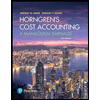
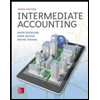
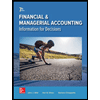