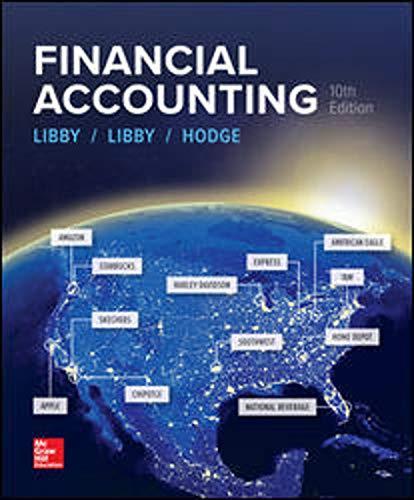
Concept explainers
(Appendix 6A) First-In, First-Out Method
Benson Pharmaceuticals uses a process-costing system to compute the unit costs of the overthe- counter cold remedies that it produces. It has three departments: mixing, encapsulating, and bottling. In mixing, the ingredients for the cold capsules are measured, sifted, and blended (with materials assumed to be uniformly added throughout the process). The mix is transferred out in gallon containers. The encapsulating department takes the powdered mix and places it in capsules (which are necessarily added at the beginning of the process). One gallon of powdered mix converts into 1,500 capsules. After the capsules are filled and polished, they are transferred to bottling, where they are placed in bottles that are then affixed with a safety seal, lid, and label. Each bottle receives 50 capsules.
During March, the following results are available for the first two departments:
Mixing | Encapsulating | ||||
Beginning inventories: | |||||
Physical units | 10 gallons | 4,000 | |||
Costs: | |||||
Materials | $252 | $32 | |||
Labor | $282 | $20 | |||
? | ? | ||||
Transferred in | $140 | ||||
Current production: | |||||
Transferred out | 140 gallons | 208,000 | |||
Ending inventory | 20 gallons | 6,000 | |||
Costs: | |||||
Materials | $3,636 | $1,573 | |||
Transferred in | — | ? | |||
Labor | $4,618 | $1,944 | |||
Overhead | ? | ? | |||
Percentage of completion: | |||||
Beginning inventory | 40% | 50% | |||
Ending inventory | 50% | 40% |
Overhead in both departments is applied as a percentage of direct labor costs. In the mixing department, overhead is 200% of direct labor. In the encapsulating department, the overhead rate is 150% of direct labor.
Required:
1. Prepare a production report for the mixing department using the FIFO method. Round the unit cost to four decimal places. If required, round final answers (except for unit costs) to the nearest dollar or unit.
Benson Pharmaceuticals | |||
Mixing Department Production Report | |||
For the Month of March (FIFO Method) | |||
Unit Information | |||
Units accounted for: | |||
Units in beginning WIP | |||
Units started | |||
Total units | |||
Units accounted for: | |||
Physical Flow | Equivalent Units | ||
Units started and completed | |||
Units in BWIP (to complete) | |||
Units in EWIP | |||
Total units accounted for | |||
Cost Information | |||
Costs to account for: | |||
Materials | Conversion | Total | |
Beginning WIP | $ | $ | $ |
Incurred during March | |||
Total costs to account for | $ | $ | $ |
Equivalent units | — | — | |
Cost per equivalent unit | — | — | $ |
Costs accounted for: | |||
Transferred Out | Ending Work in Process | Total | |
Units started and completed | $ | $ | |
Units in beginning WIP: | |||
From prior period | |||
From current period | |||
Ending work in process | $ | ||
Total costs accounted for | $ | $ | $ |
2. Prepare a production report for the encapsulating department using the FIFO method. Round the unit cost to four decimal places. If required, round final answers (except for unit costs) to the nearest dollar or unit. Hint: For this department you must convert gallons to capsules. Note: "Total costs to account for" and "Total costs to account for" would be different due to rounding.
Benson Pharmaceuticals | ||||
Encapsulating Department Production Report | ||||
For the Month of March (FIFO Method) | ||||
Unit Information | ||||
Units to account for: | ||||
Units in beginning WIP | ||||
Units started | ||||
Total units accounted for | ||||
Units to account for: | ||||
Equivalent Units | ||||
Physical Flow | Transferred In | Materials | Conversion | |
Units started and completed | ||||
Units in BWIP (to complete) | — | — | ||
Units in EWIP | ||||
Total units accounted for | ||||
Cost Information | ||||
Costs to account for: | ||||
Transferred In | Materials | Conversion | Total | |
Beginning WIP | $ | $ | $ | $ |
Incurred during March | ||||
Total costs to account for | $ | $ | $ | $ |
Equivalent units | — | |||
Cost per equivalent unit | $ | $ | $ | $ |
Costs accounted for: | ||||
Transferred Out | Ending WIP: | Total | ||
Units started and completed | $ | $ | ||
Units in BWIP from prior period | ||||
Current period | ||||
Ending work in process: | ||||
Transferred in | $ | |||
Materials | ||||
Conversion | ||||
Total costs accounted for | $ | $ | $ |

Trending nowThis is a popular solution!
Step by stepSolved in 3 steps with 4 images

- The cost per equivalent unit of direct materials and conversion in the Bottling Department of Beverages on Jolt Company is $0.50 and $0.20, respectively. The equivalent units to be assigned costs are as follows: Inventory in process, beginning of period Started and completed during the period Transferred out of Bottling (completed) Inventory in process, end of period Total units to be assigned costs Direct Materials 52,120 0 52,120 3,010 55,130 LA LA Conversion The beginning work in process inventory had a cost of $3,020. Determine the cost of completed and transferred-out production and the ending work in process inventory. When required, round your answers to the nearest dollar. Completed and transferred out production Inventory in process, ending 3,110 52,120 55,230 2,700 57,930arrow_forwardChristie's Co. manufactures cookies. The company has two departments, Mixing and Baking. For the Baking Department, material is added at the beginning of the process. Work happens evenly throughout the process, so Conversion Costs are added evenly to the product. Once mixing is complete, the cookies pieces are immediately transferred to the Baking Department. Once the baking is complete, the final product is transferred to Finished Goods Inventory. Data for the Baking Department is as follows: Units Transfer $ DirectMaterials $ % Complete Conv Costs % Complete Opening WIP 550 $3,500 $2,800 100% $2,100 30% New units & Costs 2,000 $12,300 $8,100 $14,000 Ending WIP 680 ??? 65% Calculate the physical and equivalent units for Transferred-In, Direct Materials and Conversion Costsarrow_forwardGladden Dock Company manufactures boat docks on an assembly line. Its costing system uses two cost categories, direct materials and conversion costs. Each product must pass through the Assembly Department and the Finishing Department. This problem focuses on the Assembly Department. Direct materials are added at the beginning of the production process. Conversion costs are allocated evenly throughout production. The firm uses FIFO method and the controller prepared the following (correct) equivalent unit calculation. Unitscompleted Physical Units Direct Materials Conversion WIP, beginning 70 0 52.5 Started and completed 30 30 30 WIP, ending 10 10 5 Totals 110 40 87.5 Cost per Equiv Unit $4,000 $16,000 Work in process, beginning inventory: Current Costs:Direct materials $140,000 Direct materials $ 160,000Conversion costs $260,000 Conversion…arrow_forward
- The Calgary Company is a food processing company based in Aberta. It operates under the weighted average method of process costing and has two departments: cleaning and cleaning department, conversion costs are added evenly during the process, and direct materials are added at the beginning of the process Spoiled units are detected upon insp and are disposed of at zero net disposal value. All completed work is transferred to the packaging department Summary data for May follow (Click the icon to Required For the deaning deg process Carry unit For each cost categ Enter the physical u Fl Work in process, be Started during cum To account for Completed and tran Normal spolage Abnormal spolage Work in process, ending Accounted for Data table The Calgary Company: Cleaning Dept. Work in process, beginning inventory (May 1) Degree of completion of beginning work in process Started during May Good units completed and transferred out during May Work in process, ending inventory (May 31) Degree…arrow_forwardQualCo manufactures a single product in two departments: Cutting and Assembly. Information for the Cutting department for May follows. Beginning work in process inventory Units started and completed Units completed and transferred out Ending work in process inventory Beginning work in process inventory Direct materials Conversion Costs added this period Direct materials Conversion Total costs to account for Equivalent units of production (EUP) Cost per equivalent unit of production + Equivalent units of production Cost per equivalent unit of production Cost assignment Beginning work in process To complete beginning work in process Direct materials Conversion Started and completed Direct materials Conversion Completed and transferred out Ending work in process Direct materials Conversion Total costs accounted for Units EUP Units 37,500 150,000 187,500 51, 250 Required: 1-3. Using the FIFO method, assign May's costs to the units transferred out and assign costs to its ending work in…arrow_forwardBlue Water Company produces premium bottled water. In the second department, the Bottling Department, conversion costs are incurred evenly throughout the bottling process, but packaging materials are not added until the end of the process. Costs in beginning Work-in-Process Inventory include transferred in costs of $1,200, direct labor of $600, and manufacturing overhead of $530 March data for the Bottling Department follow (Click the icon to view the data.) Read the requirements Divided by: Total EUP Cost per equivalent unit Costs accounted for Mar. 31 $ Finished Goods Inventory Work-in-Process Inventory-Bottling $ 180,000 $ 0.77 $ Completed and transferred out Ending work-in-process Total costs accounted for Requirement 2. Prepare the journal entry to record the cost of units completed and transferred out. (Record debits first, th Date Accounts Credit Debit 203,050 119,350 $ 19,250 138,600 S 155,000 0.18 S Work-in-Process Inventory-Bottling 172,500 0 36 27,900 S 0 27,900 S 55,800 $…arrow_forward
- Muskoge Company uses a process-costing system. The company manufactures a product that isprocessed in two departments: Molding and Assembly. In the Molding Department, directmaterials are added at the beginning of the process; in the Assembly Department, additionaldirect materials are added at the end of the process. In both departments, conversion costs areincurred uniformly throughout the process. As work is completed, it is transferred out. Thefollowing table summarizes the production activity and costs for February: Molding AssemblyBeginning inventories: Physical units 10,000 8,000 Costs: Transferred in — $ 45,400 Direct materials $22,000 — Conversion costs $13,800 $ 16,700Current production: Units started 25,000 ? Units transferred out 30,000 35,000 Costs: Transferred in — ? Direct materials $ 56,250 $ 40,250 Conversion costs $103,500 $142,845 Percentage of completion: Beginning inventory 40% 55% Ending inventory 80 50Required:3. Using the FIFO method, prepare the following for…arrow_forwardManjiarrow_forwardDevereaux Cycles makes three models of scooter: Commuter, Sport, and X-treme. The scooters are produced in four departments: Assembly, Detailing, Customization, and Packaging. All three models are started in Assembly, where all materials are assembled. The Commuter is then sent to Packaging, where it is packaged and transferred to finished goods inventory. The Sport is then transferred to Detailing. Once the detailing process is completed, the Sport models are transferred to Packaging and then finished goods. The X- Treme model is assembled and then transferred to Customization, and then Packaging. When packaged, it is transferred to finished goods. Data for February are shown in the following table. Conversion costs are allocated based on the number of units processed in each department. No work-in-process inventories are maintained in any department. Materials Conversion costs: Assembly Detailing Customization Packaging Total conversion costs Commuter Sport X-Treme Total $ 3,694,000…arrow_forward
- AccountingAccountingISBN:9781337272094Author:WARREN, Carl S., Reeve, James M., Duchac, Jonathan E.Publisher:Cengage Learning,Accounting Information SystemsAccountingISBN:9781337619202Author:Hall, James A.Publisher:Cengage Learning,
- Horngren's Cost Accounting: A Managerial Emphasis...AccountingISBN:9780134475585Author:Srikant M. Datar, Madhav V. RajanPublisher:PEARSONIntermediate AccountingAccountingISBN:9781259722660Author:J. David Spiceland, Mark W. Nelson, Wayne M ThomasPublisher:McGraw-Hill EducationFinancial and Managerial AccountingAccountingISBN:9781259726705Author:John J Wild, Ken W. Shaw, Barbara Chiappetta Fundamental Accounting PrinciplesPublisher:McGraw-Hill Education
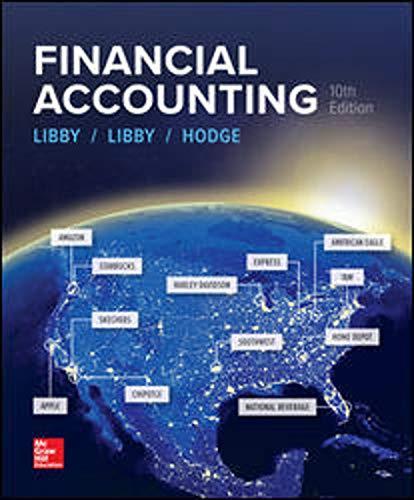
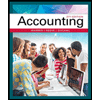
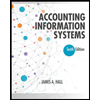
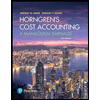
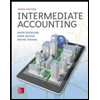
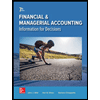