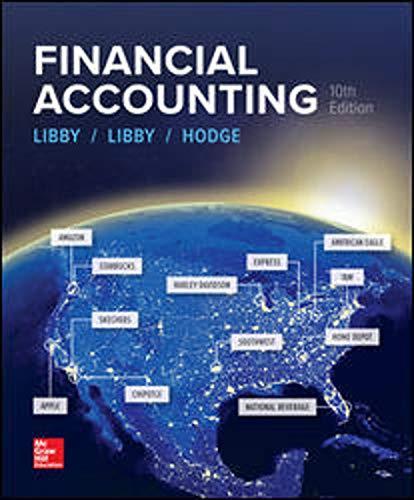
FINANCIAL ACCOUNTING
10th Edition
ISBN: 9781259964947
Author: Libby
Publisher: MCG
expand_more
expand_more
format_list_bulleted
Concept explainers
Question
Arcana Ltd has two support departments (information technology and engineering) and two production departments (assembly and finishing). The budgeted costs of the information technology and engineering departments are $90,000 and $50,000, respectively. The usage of the two support departments is as follows:
User of services | Information technology | Engineering |
Information technology | 5% | |
Engineering | 10% | |
Assembly | 60% | 40% |
Finishing | 30% | 55% |
Using the direct method, what is the information technology department cost allocated to the assembly department?
Expert Solution

This question has been solved!
Explore an expertly crafted, step-by-step solution for a thorough understanding of key concepts.
Step by stepSolved in 2 steps

Knowledge Booster
Learn more about
Need a deep-dive on the concept behind this application? Look no further. Learn more about this topic, accounting and related others by exploring similar questions and additional content below.Similar questions
- Fans Company has two service departments - product design and engineering support, and two production departments - assembly and finishing. The distribution of each service department's efforts to the other departments is shown below: SERVICE DEPARTMENT Product Design Engineering Support Product Design Engineering Support Assembly Finishing Multiple Choice O The direct operating costs of the departments (including both variable and fixed costs) were as follows: $1.057.333. O $1,970,000. O $712,667. O The total cost accumulated in the finishing department using the step method is (calculate all ratios and percentages to 4 decimal places, for example 33.3333 %, and round all dollar amounts to the nearest whole dollar assume that the engineering support department goes first): Design 0% 20% $664,792. $980,208. SERVICES PROVIDED TO $ 180,000 $ 160,000 $570,000 $ 860,000 Support 10% 0% Assembly 30% 45% Finishing 60% 35%arrow_forwardGeorgetown Metal Works produces two types of metal lamps. Georgetown manufactures 17,500 basic lamps and 6,160 designer lamps. Its activity-based costing system uses two indirect-cost pools. One cost pool is for setup costs and the other for general manufacturing overhead. Georgetown allocates setup costs to the two lamps based on setup labour-hours and general manufacturing overhead costs on the basis of direct manufacturing labour-hours. It provides the following budgeted cost information. (Click the icon to view the information.) Calculate the total budgeted costs of the basic and designer lamps using Georgetown' activity-based costing system. Begin by calculating the overhead rates for each of the two indirect-cost pools: setup costs and general manufacturing overhead. First select the formula; then enter the applicable amounts and calculate the rate. Begin with the overhead rate for set up costs. (Round the budgeted rate to the nearest dollar. Abbreviations used: MOH =…arrow_forwardnt Systems Corporation is estimating activity costs associated with producing disk drives, tapes drives, and wire drives. The indirect labor can be traced to five separate activity pools. The budgeted activity cost and activity base data by product are as follows: Procurement Scheduling Materials handling Activity Cost $370,000 Activity Base Number of purchase orders 250,000 Number of production orders 500,000 Number of moves Product development 730,000 Number of engineering changes Production 1,500,000 Machine hours Number of Purchase Number of Number Production Number of Number of Engineering Machine Orders Orders Moves Changes Hours of Units Disk drives 4,000 300 1,400 10 2,000 2,000 Tape drives 4,000 150 800 10 8,000 4,000 Wire drives 12,000 800 4,000 25 10,000 2,500 The activity-based cost (rounded to the nearest cent) for each wire drive unit is a. $204.13 b. $173.51 c. $744.06 d. $394.12 Previous Nextarrow_forward
- Panamint Systems Corporation is estimating activity costs associated with producing disk drives, tapes drives, and wire drives. The indirect labor can be traced to four separate activity pools. The budgeted activity cost and activity base data by product are provided below. Activity Cost Activity Base Procurement $356,700 Number of purchase orders Scheduling 245,900 Number of production orders Materials handling 481,200 Number of moves Product development 719,400 Number of engineering changes Production 1,487,000 Machine hours Number ofPurchaseOrders Number of ProductionOrders NumberofMoves Number ofEngineeringChanges MachineHours NumberofUnits Disk drives 3,940 270 1,350 12 1,600 1,800 Tape drives 1,900 185 590 6 9,600 4,400 Wire drives 11,300 880 3,600 28 11,300 2,000 The activity rate for the materials handling cost pool is a. $184.19 per move b. $20.81 per move c. $66.09 per…arrow_forwardHessel Corporation has two operating departments (Domestic and Global) and three service departments: Human Resources (HR), Legal, and Testing. In the most recent period, the following costs and service department usage ratios were recorded: Supplying Department Using Department Human Resources Legal Human Resources 0 10% 10% $ 264,500 Legal Testing Direct cost Costs Human resources Legal Testing Total Testing Global 15% 0 0 Domestic 10% 0 0 Global 25% 30% 45% 50% Required: Allocate the service department costs to the two operating departments using the reciprocal method. Note: Do not round intermediate calculations. From Allocated to: Domestic 60% 45% $ 190,000 $90,000 $538,000 $ 487,000arrow_forwardConsider the following data for two products of Vigano Manufacturing. Activity Budgeted Cost Activity Driver Machine setup $ 16,000 (20 machine setups) Parts handling 12,800 (16,000 parts) Quality inspections 19,200 (100 inspections) Total budgeted overhead $ 48,000 Unit Information Product A Product B Units produced 1,600 units 320 units Direct materials cost $ 26 per unit $ 36 per unit Direct labor cost $ 46 per unit $ 56 per unit Direct labor hours 2 per unit 2.50 per unit 1. Using a plantwide overhead rate based on 4,000 direct labor hours, compute the total product cost per unit for each product.2. Consider the following additional information about these two products. If activity-based costing is used to allocate overhead cost, (a) compute overhead activity rates, (b) allocate overhead cost to Product A and Product B and compute overhead cost per unit for each, and (c) compute product cost per unit for each. Actual Activity Usage Product A…arrow_forward
- Barstow Manufacturing Company has two service departments — product design and engineering support, and two production departments — assembly and finishing. The distribution of each service department's efforts to the other departments is shown below: FROM TO Design Support Assembly Finishing Design 0 % 20 % 10 % 70 % Support 10 % 0 % 30 % 60 % The direct operating costs of the departments (including both variable and fixed costs) were as follows: Design $ 110,000 Engineering Support $ 490,000 Assembly $ 440,000 Finishing $ 700,000 The total cost accumulated in the assembly department using the reciprocal method is (calculate all ratios and percentages to 4 decimal places, for example 33.3333%, and round all dollar amounts to the nearest whole dollar): Multiple Choice $2,009,592. $557,551. $612,959. $1,182,449. $1,127,041.arrow_forwardhekov Company has two support departments, Human Resources and General Factory, and two producing departments, Fabricating and Assembly. Support Departments Producing Departments HumanResources GeneralFactory Fabricating Assembly Direct costs $170,000 $330,000 $114,200 $94,000 Normal activity: Number of employees — 60 45 80 Square footage 1,500 — 6,000 14,000 The costs of the Human Resources Department are allocated on the basis of number of employees, and the costs of General Factory are allocated on the basis of square footage. Chekov Company uses the direct method of support department cost allocation. Required: 1. Calculate the allocation ratios for the four departments using the direct method. If an amount is zero, enter "0". Round your answer to the nearest cent. Proportion of Driver Used by Human Resources General Factory Fabricating Assembly Human Resources fill in the blank 1 fill in the blank 2 fill in the blank 3 fill in the blank 4…arrow_forwardPanamint Systems Corporation is estimating activity costs associated with producing disk drives, tapes drives, and wire drives. The indirect labor can be traced to four separate activity pools. The budgeted activity cost and activity base data by product are provided below. Activity Cost Activity Base Procurement $348,600 Number of purchase orders Scheduling 200,100 Number of production orders Materials handling 471,600 Number of moves Product development 741,200 Number of engineering changes Production 1,511,600 Machine hours Number of Number of Number Number of Number Purchase Production of Engineering Machine of Orders Orders Moves Changes Hours Units Disk drives 3,910 380 1,430 10 1,900 2,400 Tape drives 1,600 235 570 8,000 3,700 Wire drives 11,300 880 4,200 28 11,500 2,300 The activity rate for the procurement activity cost pool is Oa. $133.85 per purchase order Ob. $70.64 per purchase order Oc. S20.74 per purchase order Od. S233.18 per purchase order Previous Next Submit Test for…arrow_forward
- Panamint Systems Corporation is estimating activity costs associated with producing disk drives, tapes drives, and wire drives. The indirect labor can be traced to five separate activity pools. The budgeted activity cost and activity base data by product are provided below. Activity Cost Activity Base Procurement $370,000 Number of purchase orders Scheduling 250,000 Number of production orders Materials handling 500,000 Number of moves Product development 730,000 Number of engineering changes Production 1,500,000 Machine hours Number ofPurchaseOrders Number ofProductionOrders NumberofMoves Number ofEngineeringChanges MachineHours NumberofUnits Disk drives 4,000 300 1,400 10 2,000 2,000 Tape drives 4,000 150 800 10 8,000 4,000 Wire drives 12,000 800 4,000 25 10,000 2,500 The activity rate for the product development cost pool is a.$16,222 per engineering change b.$30,417 per…arrow_forwardOrange, Inc. has identified the following cost drivers for its expected overhead costs for the year: Overhead Item Expected Cost Cost Driver Expected Quantity Setup costs $ 59,500 Number of setups 250 Ordering costs 49,000 Number of orders 1,500 Maintenance 138,000 Machine hours 2,000 Power 29,500 Kilowatt hours 4,000 Total Overhead $ 276,000 Total direct labor hours budgeted = 2,000 hours. The following actual data applies to one of the products completed during the year: Product X Direct materials $ 6,900 Number of setups 5 Direct labor $ 4,900 Number of orders 50 Units completed 100 Machine hours 50 Direct labor hours 100 Kilowatt hours 500 If Orange, Inc. uses machine hours to allocate overhead cost, the unit product cost of Product X will be: Multiple Choice $117.00. $137.00 $147.00 $167.00. $187.00.arrow_forwardFans Company has two service departments-product design and engineering support, and two production departments-assembly and finishing. The distribution of each service department's efforts to the other departments is shown below: SERVICE DEPARTMENT Product Design Engineering Support The direct operating costs of the departments (including both variable and fixed costs) were as follows: Product Design Engineering Support Assembly Finishing Multiple Choice $631,492 Design 0% 20% $1,018.633. SERVICES PROVIDED TO $ 162,000 $ 142,000 $ 552,000 $ 842,000 Support 10% 0% The total cost accumulated in the assembly department using the step method is (calculate all ratios and percentages to 4 decimal places, for example 33.3333%, and round all dollar amounts to the nearest whole dollar. Assume that the engineering support department goes first): Assembly 30% 45% Finishing. 60% 35%arrow_forward
arrow_back_ios
SEE MORE QUESTIONS
arrow_forward_ios
Recommended textbooks for you
- AccountingAccountingISBN:9781337272094Author:WARREN, Carl S., Reeve, James M., Duchac, Jonathan E.Publisher:Cengage Learning,Accounting Information SystemsAccountingISBN:9781337619202Author:Hall, James A.Publisher:Cengage Learning,
- Horngren's Cost Accounting: A Managerial Emphasis...AccountingISBN:9780134475585Author:Srikant M. Datar, Madhav V. RajanPublisher:PEARSONIntermediate AccountingAccountingISBN:9781259722660Author:J. David Spiceland, Mark W. Nelson, Wayne M ThomasPublisher:McGraw-Hill EducationFinancial and Managerial AccountingAccountingISBN:9781259726705Author:John J Wild, Ken W. Shaw, Barbara Chiappetta Fundamental Accounting PrinciplesPublisher:McGraw-Hill Education
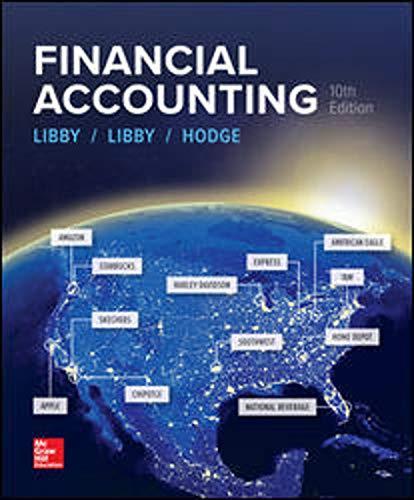
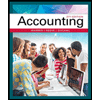
Accounting
Accounting
ISBN:9781337272094
Author:WARREN, Carl S., Reeve, James M., Duchac, Jonathan E.
Publisher:Cengage Learning,
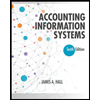
Accounting Information Systems
Accounting
ISBN:9781337619202
Author:Hall, James A.
Publisher:Cengage Learning,
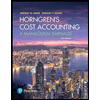
Horngren's Cost Accounting: A Managerial Emphasis...
Accounting
ISBN:9780134475585
Author:Srikant M. Datar, Madhav V. Rajan
Publisher:PEARSON
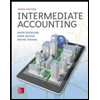
Intermediate Accounting
Accounting
ISBN:9781259722660
Author:J. David Spiceland, Mark W. Nelson, Wayne M Thomas
Publisher:McGraw-Hill Education
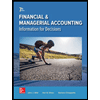
Financial and Managerial Accounting
Accounting
ISBN:9781259726705
Author:John J Wild, Ken W. Shaw, Barbara Chiappetta Fundamental Accounting Principles
Publisher:McGraw-Hill Education