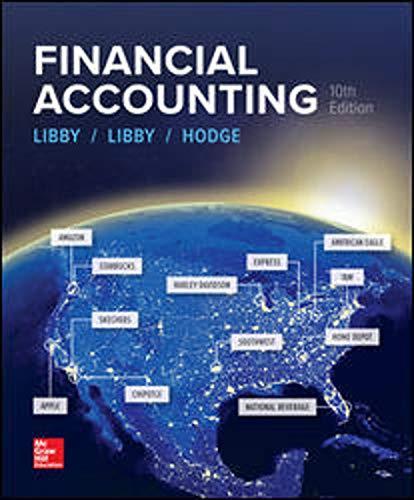
Concept explainers
Single Plantwide and Multiple Production Department Factory
The management of Firebolt Industries Inc. manufactures gasoline and diesel engines through two production departments, Fabrication and Assembly. Management needs accurate product cost information in order to guide product strategy. Presently, the company uses a single plantwide factory overhead rate for allocating factory overhead to the two products. However, management is considering the multiple production department factory overhead rate method. The following factory overhead was budgeted for Firebolt:
Fabrication Department factory overhead | $396,000 | ||
Assembly Department factory overhead | 180,000 | ||
Total | $576,000 |
Direct labor hours were estimated as follows:
Fabrication Department | 3,600 | hours | |
Assembly Department | 3,600 | ||
Total | 7,200 | hours |
In addition, the direct labor hours (dlh) used to produce a unit of each product in each department were determined from engineering records, as follows:
Production Departments | Gasoline Engine | Diesel Engine | ||
Fabrication Department | 1.30 | dlh | 3.00 | dlh |
Assembly Department | 2.70 | 1.00 | ||
Direct labor hours per unit | 4.00 | dlh | 4.00 | dlh |
a. Determine the per-unit factory overhead allocated to the gasoline and diesel engines under the single plantwide factory overhead rate method, using direct labor hours as the activity base.
Gasoline engine | $ per unit |
Diesel engine | $ per unit |
b. Determine the per-unit factory overhead allocated to the gasoline and diesel engines under the multiple production department factory overhead rate method, using direct labor hours as the activity base for each department.
Gasoline engine | $ per unit |
Diesel engine | $ per unit |

Trending nowThis is a popular solution!
Step by stepSolved in 3 steps with 3 images

- Helpful Division of X Company makes two products, Small and Large. The company has always used Conventional Costing (for financial reporting purposes), but this period wants to try using Activity-Based Costing to make better decisions. Information related to the current period is as follows: REQUIRED: (#1) Since the company has three activities, what are the three overhead application rates the company would use for activity-based costing? (ROUND EACH RATE TO THE NEAREST CENT and be sure to label the rates appropriately.) (#2) Using activity-based costing, what was the cost to manufacture one Small unit? (#3) Using activity-based costing, what was the cost to manufacture one Large unit? (#4) Based on what you learned about activity-based costing this week, how might Helpful Division managers use the new cost information from its activity-based costing system to better manage its operations? Helpful Resource: https://www.youtube.com/watch?v=PU3U_aMbKwsarrow_forwardFountain Water Products (FWP) manufacturers water bottles. They have historically used a traditional system that allocated the manufacturing overhead costs based on machine hours. FWP is looking at switching to an ABC system in order to ensure more accurate product costing. They first want to compare the traditional and ABC costing systems to determine if it is worth the effort and costs to implement and maintain. They estimate a total overhead cost of $459,000. Under the traditional system they identified machine hours as the cost driver, and estimated a total of 51,000 machine hours. They actually incurred 48,700 machine hours in production. The total applied MOH calculated under the more precise ABC system was $320,000. The ABC costing system will cost $50,000 to implement. FWP has determined that a benefit of more accurate costing by $80,000 is worth the $50,000 implementation cost. What is the difference between the ABC costing and traditional system? Enter your number as a…arrow_forwardChocolate Bars, Inc. (CBI), manufactures creamy deluxe chocolate candy bars. The firm has developed three distinct products: Almond Dream, Krispy Krackle, and Creamy Crunch. CBI is profitable, but management is quite concerned about the profitability of each product and the product costing methods currently employed. In particular, management questions whether the overhead allocation base of direct labor-hours accurately reflects the costs incurred during the production process of each product. In reviewing cost reports with the marketing manager, Steve Hoffman, who is the cost accountant, notices that Creamy Crunch appears exceptionally profitable and that Almond Dream appears to be produced at a loss. This surprises both him and the manager, and after much discussion, they are convinced that the cost accounting system is at fault and that Almond Dream is performing very well at the current market price. Steve decides to hire Jean Sharpe, a management consultant, to study the…arrow_forward
- Drippin' in Heat manufactures the finest formal wear west of the Mississippi. The company produces two main products: Suit Jackets and Sport Coats. Currently the company uses a traditional overhead rate in which Manufacturing Overhead is allocated to products based on direct labor hours logged. The projected production levels for the period are 1,200 Suit Jackets and 400 Sport Coats. Due to profitability concerns, management is considering switching to Activity-Based Costing (ABC). Management has divided manufacturing overhead costs into three activities and cost pools: Assembly $30,000; Machine Setup $20,000; and Product Movement $102,400. Management has identified the following cost drivers for each overhead activity: direct labor hours for assembly, number of setups for machine setup, and number of moves for product movement. The following information has been compiled for each product line: Direct Labor Requirements Machine Setup Requirements Product Movement Requirements Suit…arrow_forwardJulio produces two types of calculator, standard and deluxe. The company is currently using a traditional costing system with machine hours as the cost driver but is considering a move to activity-based costing. In preparing for the possible switch, Julio has identified two cost pools: materials handling and setup. The collected data follow: Number of machine hours Number of material moves Number of setups Total estimated overhead costs are $332,860, of which $158,400 is assigned to the material handling cost pool and $174,460 is assigned to the setup cost pool. Required: 1. Calculate the overhead assigned to each product using the traditional cost system. 2. Calculate the overhead assigned to each product using ABC. Required 1 Required 2 Standard Model Deluxe Model 30,400 870 520 Complete this question by entering your answers in the tabs below. Standard Model Deluxe Model 25,400 570 90 Calculate the overhead assigned to each product using the traditional cost system. (Round the…arrow_forwardLockTite Company produces two products, Pretty Safe (PS) and Virtually Impenetrable (VI). The following two tables give pertinent information about these products. Solve, a. What is the cost per unit of Pretty Safe if LockTite uses traditional overhead allocation based on number of units produced? b. What is the cost per unit of Pretty Safe if LockTite uses activity-based costing to allocate overhead?arrow_forward
- [The following information applies to the questions displayed below.] Benton Corporation manufactures computer microphones, which come in two models: Standard and Premium. Data for a representative quarter for the two models follow: Units produced Production runs per quarter Direct materials cost per unit Direct labor cost per unit Supervision Setup labor Incoming inspection Total overhead Manufacturing overhead in the plant has three main functions: supervision, setup labor, and incoming material inspection. Data on manufacturing overhead for a representative quarter follow: Standard 10,400 50 $ 30 50 $ 214,500 249,600 179,400 $ 643,500 a. Overhead rate b. Supervision b. Setup labor b. Incoming inspection Premium 2,600 25 $ 64 75 Required: a. Benton currently applies overhead on the basis of direct labor cost. What is the predetermined overhead rate for the quarter? b. The CFO and the plant controller at Benton are thinking of adopting an ABC system. They have tentatively chosen the…arrow_forwardNutterco, Inc., produces two types of nut butter: peanut butter and cashew butter. Of the two,peanut butter is the more popular. Cashew butter is a specialty line using smaller jars and fewerjars per case. Data concerning the two products follow: Annual overhead costs are listed below. These costs are classified as fixed or variable with respect to the appropriate activity driver. Required:1. Prepare a traditional segmented income statement, using a unit-level overhead rate based ondirect labor hours. Using this approach, determine whether the cashew butter product lineshould be kept or dropped.2. Prepare an activity-based segmented income statement. Repeat the keep-or-drop analysisusing an ABC approach.arrow_forwardCampbell Electronics produces video games in three market categories: commercial, home, and miniature. Campbell has traditionally allocated overhead costs to the three products using the companywide allocation base of direct labor hours. The company recently implemented an ABC system when it installed computer-controlled assembly stations that rendered the traditional costing system ineffective. In implementing the ABC system, the company identified the following activity cost pools and cost drivers: Category Unit Batch Product Facility Additional data for each of the product lines follow: Direct materials cost Direct labor cost Number of labor hours Number of machine hours Number of production orders Research and development time Number of units. Square footage Required Total Pooled Cost $ 376,000 206,400 109,600 304,000 Type of Product a. Commercial a. Home a. Miniature Combined total b. Commercial b. Home b. Miniature Combined total Types of Costs Indirect labor wages, supplies,…arrow_forward
- AccountingAccountingISBN:9781337272094Author:WARREN, Carl S., Reeve, James M., Duchac, Jonathan E.Publisher:Cengage Learning,Accounting Information SystemsAccountingISBN:9781337619202Author:Hall, James A.Publisher:Cengage Learning,
- Horngren's Cost Accounting: A Managerial Emphasis...AccountingISBN:9780134475585Author:Srikant M. Datar, Madhav V. RajanPublisher:PEARSONIntermediate AccountingAccountingISBN:9781259722660Author:J. David Spiceland, Mark W. Nelson, Wayne M ThomasPublisher:McGraw-Hill EducationFinancial and Managerial AccountingAccountingISBN:9781259726705Author:John J Wild, Ken W. Shaw, Barbara Chiappetta Fundamental Accounting PrinciplesPublisher:McGraw-Hill Education
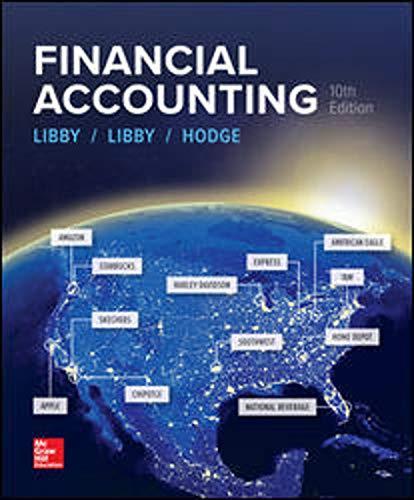
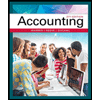
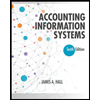
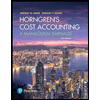
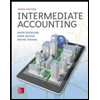
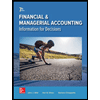