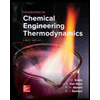
A gas mixture contains 0.03mole/mole of contaminant A. The solute free gas flow rate is 48.5 lbmole/(ft2 hr). We need to remove 85% of this contaminant from the gas stream. Liquid solvent is fed to the absorber in a countercurrent operational mode. Also the solvent being sent to this unit does not contain the contaminant
The equilibrium plot is given below and it is also attached as a file. The tabular data is also presented if you prefer to construct your own plot. Using this information answer the questions below.
Is this process gas absorption or liquid stripping?
Calculate minimum flow rate of liquid solvent.
If the actual solvent rate is 50% higher than the minimum solvent flow rate, determine the actual solvent flow rate and the fraction of solute A in the liquid solvent effluent stream.
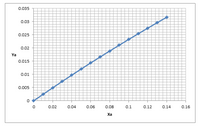

Step by stepSolved in 2 steps with 2 images

- An evaporation-crystallization process (as shown below) is used to obtain solid potassium sulfate from an aqueous salt solution. The feed contains 18.7 wt% K2SO4. The wet filter cake contains solid sulfate crystals and a 40.0 wt% salt solution. The filtrate is recycled to mix with the feed. The evaporator has a capacity of 175 kg of water evaporated per second. The filtrate has 40.0 wt% salt solution, as well, and from the water entering the evaporator, 45.0% is evaporated. In the wet filter cake, there is 10 kg of the solid crystals for every 1 kg of the salt solution. a.) Calculate the fresh feed rate. (Include units) b.) Determine the production rate of crystal. (Include units) c.) Calculate the recycle ratio. (kg recycle/kg feed) Include unitsarrow_forwardIn a counter-current absorption tower, a process gas containing 0.04 (mole fraction) ammonia is scrubbed with pure water. The exit gas contains 0.002 (mole fraction) ammonia.The diameter of the tower is 1m, and the packing has a large area per volume of 200 m2m–3. The overall mass transfer coefficient based on the liquid side driving force, KL, is 1.5×10−5ms–1. The total gas and liquid concentrations are 0.6kmolm–3and 20 kmolm–3respectively and the gas flowrateis 0.03kmols–1. The actual liquid to gas ratio is 1.5 times that of the minimum liquid to gas ratio. The equilibrium for ammonia between the air and water is given by y* = 1.04x. What is the mol fraction of ammonia in the liquid?arrow_forwardHydrogen sulfide (H2S) gas in petroleum refinery is to be removed from a 984 kg/h gas mixture consist of 25 % w.w H2S into air, using counter current absorption column. Water is used as solvent in the absorption column. The water flow rate is 1.81 times the gas mixture flow rate. The air mole percent at the top of the column is 96.5%. The air consists of 21.9% oxygen and 78.1% nitrogen. Calculate; The mole flow rate and mole fraction of H2S in the gas stream leaving at the top of the tower? Note; Don’t round numbers; Minimum 4 decimals (0.0000) Given A) The air consists of 21.9% oxygen and 78.1% nitrogen. B) The atomic weight of; 1. The hydrogen atom is 1 2. The Oxygen atom is 16 3. The sulfur atom is 32 4. 1The nitrogen atom is 14arrow_forward
- SEPERATIONS Absorption: Contaminant in a Gas Effluent We are going to absorb 90% of a contaminant in a gas stream containing 15.0 mole of the contaminant by absorntion into a water phase. The total inlet gas flow to the absorption column is 100.0 kgmole/hr and the total water flow is 200 kgmole/hr. Inlet water is NOT pure but contains 0.5% of the contaminant. I he process operates isothermally at 300k and a pressure of 1 atm. The equilibrium for this system is effectively characterized by either a Henry's Law relationship or Raoult's Law (using partial pressure), a general equilibrium relationship that can be used is ya=1.60*xa. plot the operating line and determine the minimum number of stages (graphically) for the equilibrium relationship provided. Confirm the results of part (a) using the analytical Kremser equation.arrow_forwardA cooling tower works with the amount of cooling water 1 ton/hour. Conditions of cooling water in the cooling tower has a solid content of 1350 ppm. The cooling water entering the cooling tower is processed in such a way that the solids content is a maximum of 225 ppm. If the cooling water evaporated rate is assumed to be 2.5% the cooling water inlet rate, calculate the concentration cycle, the added water rate, and the blowdown water rate!arrow_forwardA reverse-osmosis unit is used to obtain pure water from saline water. The coefficient of water permeation is 0.1 mol/cm2 s atm. The pressure differential across the membrane is 0.2 atm, and the osmotic pressure differential is 0.05 atm. The water flux across the membrane is most nearly (A) 0.0050 mol/cm2·s (B) 0.015 mol/cm2·s (C) 0.050 mol/cm2·s (D) 0.15 mol/cm² ·sarrow_forward
- An evaporation-crystallization process (as shown below) is used to obtain solid potassium sulfate from an aqueous salt solution. The feed contains 18.7 wt% K2SO4. The wet filter cake contains solid sulfate crystals and a 40.0 wt% salt solution. The filtrate is recycled to mix with the feed. The evaporator has a capacity of 175 kg of water evaporated per second. The filtrate has 40.0 wt% salt solution, as well, and from the water entering the evaporator, 45.0% is evaporated. In the wet filter cake, there is 10 kg of the solid crystals for every 1 kg of the salt solution. a.) Calculate the fresh feed rate. (Include units) b.) Determine the production rate of crystal. (Include units) c.) Calculate the recycle ratio. (kg recycle/kg feed) Include unitsarrow_forwardA// Fick's first diffusion law states that: Mass flux = -D Where mass flux = the quantity of mass (g/cm²/s), D a diffusion coefficient (1.6×10-6 cm²/s), c concentration, and x = distance (cm). An environmental engineer measures the following concentration of a pollutant in the sediments underlying a lake as the following: 0 2 6 0.12×10-6 0.64x10-6 1.20×10-6 Use a suitable Newton's interpolation formula available to estimate the derivative at x = 0 and then calculate the mass flux of pollutant. X, cm C, g/cm³ de dx =arrow_forwardProvide basis, find, Process flow diagram and show step-by-step solution for the process. Topic: Material Balance with multiple units An aqueous solution containing 30mol% NaCl is used to produce NaOH by electrolysis. At the anode, the chloride ion is oxidized to chlorine gas; at the cathode, water is reduced to hydroxide and hydrogen gas. The chlorine gas and hydrogen gas exit the electrolysis system while the remaining solution is concentrated in an evaporator to produce a product containing 50mol% NaOH, 7mol% NaCl, and 43mol% H2O.a. What is the percent conversion of salt to sodium hydroxide?b. How much chlorine gas (in kg) is produced per kg of the product?c. How much water (in kg) must be evaporated in the evaporator per kg of the product?arrow_forward
- a double effect evaporator is fed by 31896 lbm/hr of 9% potassium chloride solution. At the end of evaporation a 41% KCl solution is obtained. The water evaporated in the second effect is 1.5 times the water evaporated in the first effect. Determine:a) The amount of 41% concentrated solutionb) The amount of water evaporated in the first and second effectsc) The amount of solution fed into the second effect, as well as its compositionarrow_forwardIn a counter-current absorption tower, a process gas containing 0.04 (mole fraction) ammonia is scrubbed with pure water. The exit gas contains 0.002 (mole fraction) ammonia.The diameter of the tower is 1m, and the packing has a large area per volume of 200 m2m–3. The overall mass transfer coefficient based on the liquid side driving force, KL, is 1.5×10−5ms–1. The total gas and liquid concentrations are 0.6kmolm–3and 20 kmolm–3respectively and the gas flowrateis 0.03kmols–1. The actual liquid to gas ratio is 1.5 times that of the minimum liquid to gas ratio. The equilibrium for ammonia between the air and water is given by y* = 1.04x. If the operator increases the gas flow by 20% while keeping the liquid flow and the entering gas and liquid compositions constant,what are the new mole fractions of ammonia in the exit gas and the exit liquid? Assume that the overall mass transfer coefficient does not change with the gas flow.arrow_forward
- Introduction to Chemical Engineering Thermodynami...Chemical EngineeringISBN:9781259696527Author:J.M. Smith Termodinamica en ingenieria quimica, Hendrick C Van Ness, Michael Abbott, Mark SwihartPublisher:McGraw-Hill EducationElementary Principles of Chemical Processes, Bind...Chemical EngineeringISBN:9781118431221Author:Richard M. Felder, Ronald W. Rousseau, Lisa G. BullardPublisher:WILEYElements of Chemical Reaction Engineering (5th Ed...Chemical EngineeringISBN:9780133887518Author:H. Scott FoglerPublisher:Prentice Hall
- Industrial Plastics: Theory and ApplicationsChemical EngineeringISBN:9781285061238Author:Lokensgard, ErikPublisher:Delmar Cengage LearningUnit Operations of Chemical EngineeringChemical EngineeringISBN:9780072848236Author:Warren McCabe, Julian C. Smith, Peter HarriottPublisher:McGraw-Hill Companies, The
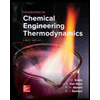
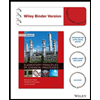
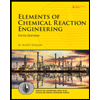
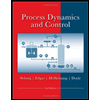
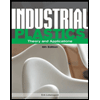
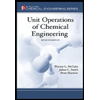