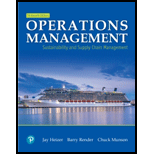
Mylab Operations Management With Pearson Etext -- Access Card -- For Operations Management: Sustainability And Supply Chain Management (13th Edition)
13th Edition
ISBN: 9780135225899
Author: Jay Heizer, Barry Render, Chuck Munson
Publisher: PEARSON
expand_more
expand_more
format_list_bulleted
Concept explainers
Question
Chapter 13, Problem 1CS
Summary Introduction
Case summary:
Company AC is a distributor and producer of outdoor lighting fixtures. It operates three different plants to produce outdoor lighting fixtures and has five distribution centers. The capacity of distribution centers is as follows:
Warehouse | Capacity (units) |
Warehouse 1 | 9,000 |
Warehouse 2 | 13,000 |
Warehouse 3 | 11,000 |
Warehouse 4 | 15,000 |
Warehouse 5 | 8,000 |
Capacity of the three plants is given as follows:
Plants | Capacity (units) |
Plant 1, regular time | 27,000 |
Plant 1, overtime | 7,000 |
Plant 2, regular time | 20,000 |
Plant 2, overtime | 5,000 |
Plant 3, regular time | 25,000 |
Plant 3, overtime | 6,000 |
Variable cost and fixed cost of each plant are given as follows:
Plant | Variable cost per unit | Fixed cost per unit | |
Operating | Not operating | ||
Plant 1, regular time | $2.80 | $14,000 | $6,000 |
Plant 1, overtime | $3.52 | ||
Plant 2, regular time | $2.78 | $12,000 | $5,000 |
Plant 2, overtime | $3.48 | ||
Plant 3, regular time | $2.72 | $15,000 | $7,500 |
Plant 3, overtime | $3.42 |
Distribution cost per unit is given as follows:
From plants | Warehouse 1 | Warehouse 2 | Warehouse 3 | Warehouse 4 | Warehouse 5 |
Plant 1 | $0.50 | $0.44 | $0.49 | $0.46 | $0.56 |
Plant 2 | $0.40 | $0.52 | $0.50 | $0.56 | $0.57 |
Plant 3 | $0.56 | $0.53 | $0.51 | $0.54 | $0.35 |
To determine: The various configurations of operating and closed plants and the configuration that would minimize the total cost.
Expert Solution & Answer

Want to see the full answer?
Check out a sample textbook solution
Students have asked these similar questions
QUESTION THREE
Mulungushi textiles during its peak days used to manufacture gowns on a produce-to-order
basis. The company manufactured three models of gowns on the same final assembly line. The
final assembly had 20,000 hours of weekly capacity. The 6-week MPS and the final assembly
standard for each model are shown below:
Final Assembly Standard
Weekly Production (Gowns)
Product
(hours per gown)
| 2
4
|5
1
3
6
200 150
200
| 250 150 250
A
25
B.
30
100 200
350
250
150
250
35
|150 150 150
250
|250
200
a) Compute the actual final assembly hours required at the plant in each week and for
the total 6 weeks to produce the MPS. Compare the load to the labour-hours
capacity in each week and for the total 6-weeks.
b) Does enough production capacity exist to produce the MPS?
c) What changes to the MPS would you recommend?
Build New plant option=
Question 4
Cost-benefit-tradeoff problems are linear programming problems involving the allocation of limited resources to activities.
O True
O False
Chapter 13 Solutions
Mylab Operations Management With Pearson Etext -- Access Card -- For Operations Management: Sustainability And Supply Chain Management (13th Edition)
Ch. 13 - Prob. 1DQCh. 13 - Why are SOP teams typically cross-functional?Ch. 13 - Prob. 3DQCh. 13 - Prob. 4DQCh. 13 - Prob. 5DQCh. 13 - Prob. 6DQCh. 13 - Question: 7. What is level scheduling? What is the...Ch. 13 - Question: 8. Define mixed strategy. Why would a...Ch. 13 - Prob. 9DQCh. 13 - Prob. 10DQ
Ch. 13 - Question: 11. What is the relationship between the...Ch. 13 - Prob. 12DQCh. 13 - Question: 13. What are major limitations of using...Ch. 13 - Prob. 14DQCh. 13 - Question: 13.1 Prepare a graph of the monthly...Ch. 13 - Prob. 2PCh. 13 - The president of Hill Enterprises, Terri Hill,...Ch. 13 - Prob. 4PCh. 13 - Prob. 5PCh. 13 - Prob. 6PCh. 13 - Prob. 7PCh. 13 - Prob. 8PCh. 13 - Prob. 9PCh. 13 - Question: 13.10 The SOP team (see Problem 13.9)...Ch. 13 - Prob. 11PCh. 13 - Prob. 12PCh. 13 - Prob. 13PCh. 13 - Question: 13.14 Jerusalem Medical Ltd., an...Ch. 13 - Prob. 15PCh. 13 - Prob. 16PCh. 13 - Prob. 17PCh. 13 - Question: 13.18 Jose Martinez of El Paso has...Ch. 13 - Prob. 19PCh. 13 - Prob. 23PCh. 13 - Prob. 24PCh. 13 - Prob. 25PCh. 13 - Prob. 26PCh. 13 - Prob. 1CSCh. 13 - Prob. 2CSCh. 13 - Prob. 1.1VCCh. 13 - Prob. 1.2VCCh. 13 - Question: 3. What are some concerns the team needs...
Knowledge Booster
Learn more about
Need a deep-dive on the concept behind this application? Look no further. Learn more about this topic, operations-management and related others by exploring similar questions and additional content below.Similar questions
- Question 34 The term "soft constraints" is associated with which of the following? Goal Programming Expected Monetary Value Network Models Integer Programmingarrow_forwardQUESTION 2 NAK Consult Ltd is a construction company with many contracts being executed concurrently. A large number of workers are on various construction sites. NAK Consult Ltd has an internal audit department and the team is currently reviewing cash wages systems within the company. The following information is available concerning the wages systems: • Workers on each site are controlled by a foreman. The foreman has a record of all employee numbers and can issue temporary numbers for new employees. • Any overtime is calculated by the computerized wages system and added to the standard pay. • The two staff in the wages department make amendments to the computerized wages system in respect of employee leave, illness, as well as setting up and maintaining all employee records. • The computerized wages system calculates deductions from gross pay, such as employee taxes (PAYE), and other statutory deductions. • Finally, a list of net cash payments for each employee is produced. Cash is…arrow_forwardPlease help with the conclusion question.arrow_forward
- Practice 19. Please show solutionarrow_forwardQuestion 3 Heman Company has three production plants in P1, P2, and P3 and two warehouses W1 and W2. The capacities of the three production plants during the next year are 450, 600, and 380. The demands at the two warehouses are 650 and 780 cars. The cost chart between the production plants and the warehouses is given: COST Chart W1 W2 P1 $6 $4 P2 $3 $6 P3 S7 $8 Formulate an initial feasible solution to Heman Company's problem using the Northwest- Corner Rule. Then evaluate each unused shipping route by computing all improvement indices using Stepping-Stone Method. Is the solution optimal?arrow_forwardWhat descriptive term is used to refer to Coca Cola and Campbell’s soup high number of product items in their product line? Question 2 options: a) Depth b) Width c) Mix d) Grouparrow_forward
- Question and Observe: At what level of demand (number of units) per year would these two alternatives be equal? Graphically represent these two alternatives and their tradeoff point.arrow_forwardThe Millers are traveling with their three children under the age of 10. After four days, they need to use the hotel guest laundry service. This service represents which of the following for the hotel? Question 10 options: a) Additional revenue b) Work for housekeepers c) Club-level service d) Children’s servicearrow_forwardBaton Rouge Company is considering purchasing new equipment which will cost $950,000. This equipment is expected to have a useful life of 12 years, have a salvage value of $50,000 and is expected to have an annual net cash inflow (before taxes) of $80,000. Assume the company is in the 34% tax bracket. What is Baton Rouge's annual net cash inflow (after taxes)? Question 12 options: $13,200 $73,200 $78,300 $112,800 $52,800arrow_forward
- Question 4: A Chemical Company LLC is unable to satisfy customer demand for one of their products. The ratios for mixing the outputs from processes C, D and E are 2, 1 and 1 respectively. The ratio for the departments F and G is 3 and 1, and the ratio for departments H and I is 4 and 1. Using Table Q4, Determine the following; (1) The system capacity and bottleneck; (ii) How much system capacity can be gained by adding capacity to the bottleneck Table Q4 Capacity (liters/hour) 350 Department Predecessors A В 400 A C 350 В 250 E 200 F 750 C, D and E G 300 H 850 F, and G 350 J 1100 H and I K 1350 Jarrow_forwardQuestion 1. Hoverboards and the Factory Market Area: Suppose there is a single shoe factory in the region. The factory competes with homemade shoes and will sell shoes to any household for which the net price of factory shoes is less than the cost of homemade shoes. The cost of a homemade shoe is the opportunity cost of the time required to make the shoe at home, that is, the one gallon of milk that could be produced instead. Suppose the higher cost of living and commuting requires compensation of 0.80 gallons of milk per hour. Each worker produces 10 shoes per hour, so the average labor and capital cost are 0.18 gallons of milk and 0.12 gallons of milk respectively. The factory price of shoe (equal to the average production cost, sum of the average labor cost and the average capital cost) is 0.30 gallons of milk. A round-trip mile involves one mile of travel to a location and one mile back, for a total distance of two miles. Linear travel cost 20 miles /hour. Therefore, the…arrow_forwardQuestion R .Create a BPMN diagram to represent the supply chain management process for BMW. The solution should include the following Actors. • Buyer • BMW dealership • BMW parts manufacturer • Raw material manufacturer Full explain this question and text typing work only We should answer our question within 2 hours takes more time then we will reduce Rating Dont ignore this linearrow_forward
arrow_back_ios
SEE MORE QUESTIONS
arrow_forward_ios
Recommended textbooks for you
- Practical Management ScienceOperations ManagementISBN:9781337406659Author:WINSTON, Wayne L.Publisher:Cengage,Operations ManagementOperations ManagementISBN:9781259667473Author:William J StevensonPublisher:McGraw-Hill EducationOperations and Supply Chain Management (Mcgraw-hi...Operations ManagementISBN:9781259666100Author:F. Robert Jacobs, Richard B ChasePublisher:McGraw-Hill Education
- Purchasing and Supply Chain ManagementOperations ManagementISBN:9781285869681Author:Robert M. Monczka, Robert B. Handfield, Larry C. Giunipero, James L. PattersonPublisher:Cengage LearningProduction and Operations Analysis, Seventh Editi...Operations ManagementISBN:9781478623069Author:Steven Nahmias, Tava Lennon OlsenPublisher:Waveland Press, Inc.
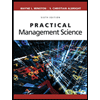
Practical Management Science
Operations Management
ISBN:9781337406659
Author:WINSTON, Wayne L.
Publisher:Cengage,
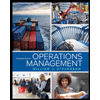
Operations Management
Operations Management
ISBN:9781259667473
Author:William J Stevenson
Publisher:McGraw-Hill Education
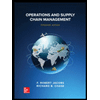
Operations and Supply Chain Management (Mcgraw-hi...
Operations Management
ISBN:9781259666100
Author:F. Robert Jacobs, Richard B Chase
Publisher:McGraw-Hill Education
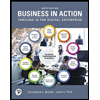
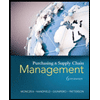
Purchasing and Supply Chain Management
Operations Management
ISBN:9781285869681
Author:Robert M. Monczka, Robert B. Handfield, Larry C. Giunipero, James L. Patterson
Publisher:Cengage Learning
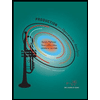
Production and Operations Analysis, Seventh Editi...
Operations Management
ISBN:9781478623069
Author:Steven Nahmias, Tava Lennon Olsen
Publisher:Waveland Press, Inc.