Why is the strengthening of the alloys required?
Strengthening of the alloys is required as metals become weak due to various lattice defects, metal bonding phenomena. The strength of the metals is not enough for any mechanical work. The internal dislocations of any metals arise due to forming processes. Due to the movement of these dislocations, the metals are plastically deformed.
To prevent these types of dislocations in the metals and intermetallics, strengthening of alloys is required.
What is the strengthening of the alloys?
The strengthening can improve the mechanical properties of metals. The mechanical properties include ductility, strength, toughness, and yield strength. These metals are then required for various applications. Types of strengthening methods are work hardening , precipitation hardening, grain boundary, solid solution, dispersion strengthening, etc.
Metal forming mechanism
The variation of mechanical properties with the grain size is shown below:
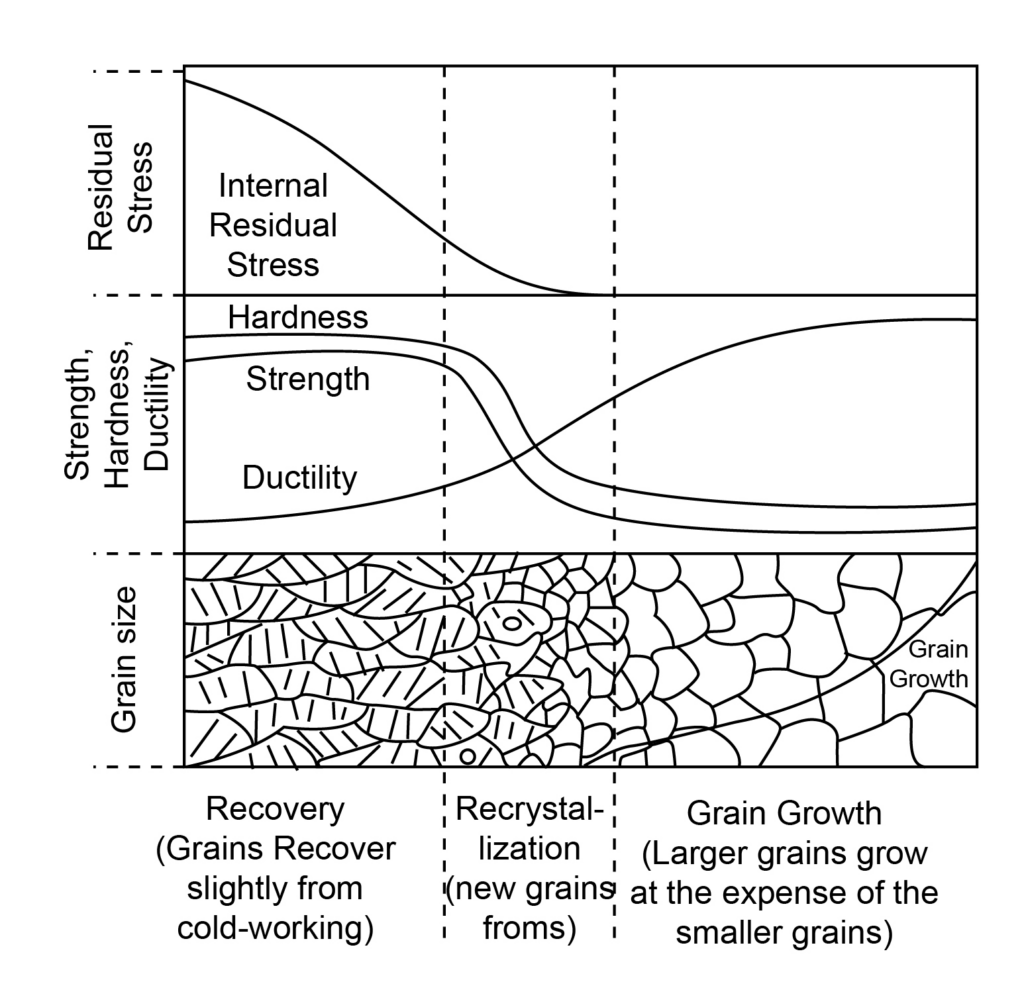
Recovery
In the recovery stage, the internal stresses will be relieved with the increase in temperature. The grains become soft. The hardness and strength of the materials are high. But the ductility is less. There is little change in the grains sizes.
Recrystallization
In this stage, the grains start transforming, and grain refinement takes place. At 0.5 times melting temperature, the grains will be completely transformed. The range of recrystallization temperature is between 0.3 to 0.5 of the melting temperature. Here, internal stress decreases and is significantly less present in the material. Ductility starts increasing, but the hardness and the strength start decreasing.
Grain growth
In the grain growth, the grain sizes increases. The ductility of the material increases but the hardness and strength both decrease and become significantly less.
Grain boundary strengthening
The grains and their boundaries act as strengtheners in the metal and alloys. The grain size can be varied by various techniques like the controlled type of micro-alloying elements introduction, and then they will undergo thermomechanical type processing. The grain growth takes place in fine grains, and they are stable in multiple alloys and steels. They increase the strength of the alloys up to a specific temperature.
The grain and its boundaries can be shown as,
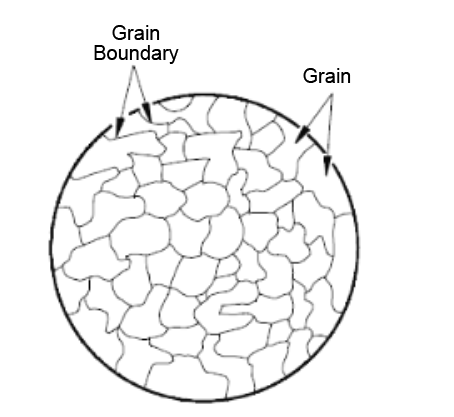
The grains have various crystallographic structures. They also have grain boundaries. When deformation due to forming and other processes take place then slip, phenomenon comes into the picture. Grain boundaries provide a barrier to the motion of dislocations. The grains sizes can be reduced and thus increasing the grain numbers and grain boundaries. Thus, the barrier numbers also increase, and the dislocation motion reduces as a result of this.
From the Hall-Petch equation relationship, the yield strength can be expressed as,
Here, is the initial yield stress, k is the constant, d is the average diameter of the grain.
From the above relation also, it can be observed that by reducing the grain diameter, the yield strength will be increased.
Solid solution strengthening
In this method, the interstitial or substitution defects arise due to the addition of one solute atom of any element with the other elements in the crystalline lattice structure, which will form a solid solution. The motion of dislocations can be obstructed by the lattice distortions of the solid atoms. This will increase the yield strength. These solid atoms apply tensile or compressive stresses into the crystal lattice structures. These solid atoms act as a barrier and interact with the dislocations.
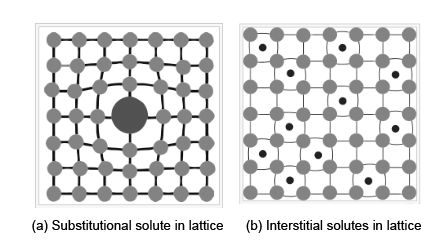
In figure (a), the solid atom makes a stress field around it and obstructs the dislocation. Due to this addition of a substitutional solid atom, the lattice structure will be strained. The impurity is approximately similar to the size of parent atoms. In this form, the ductility of the metal is enhanced. In figure (b), the interstitial solute will be added to the crystal lattice structure, strain-induced in the material.
Smaller and larger substitutional Impurities
The small atoms (impurity) applies the tensile strains. This can be shown in the figure below as,
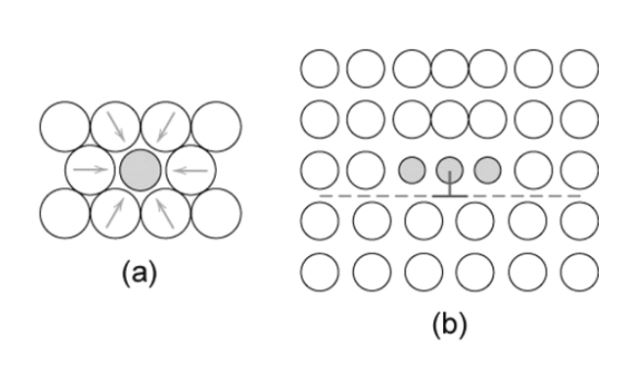
Here, the solute atoms concentrate around the dislocations and try to decrease the strain energy. These impurities resist the motion of the dislocations and cancel out most of the strains in the lattice.
The larger substitutional atom applies compressive strains. In the same way, like smaller impurities, they also behave in the lattice. This can be represented as,
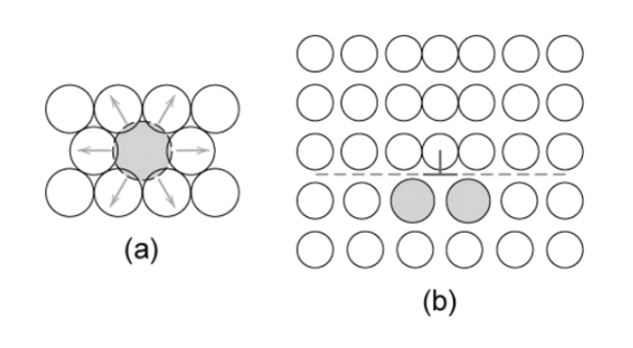
Variation of tensile strength with nickel content (%)
The tensile strength versus nickel content curve can be shown as,
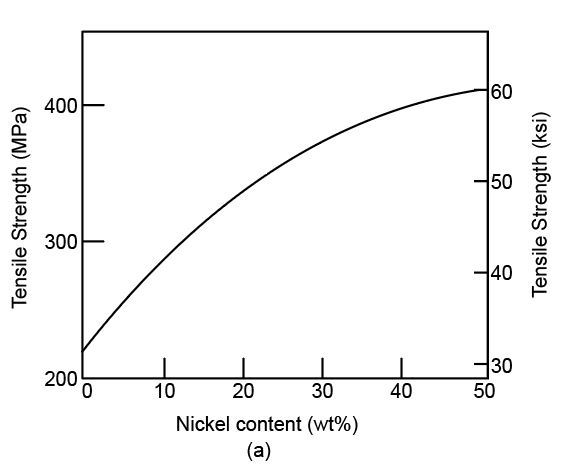
Due to the addition of solute in the other element, the movement of dislocation decreases, and the yield stress increases. Likewise, nickel is added to the copper, the tensile strength and yield strength increase. Thus, the ductility will decrease.
Variation of yield strength with nickel content (%)
The tensile strength versus nickel content curve can be shown as,
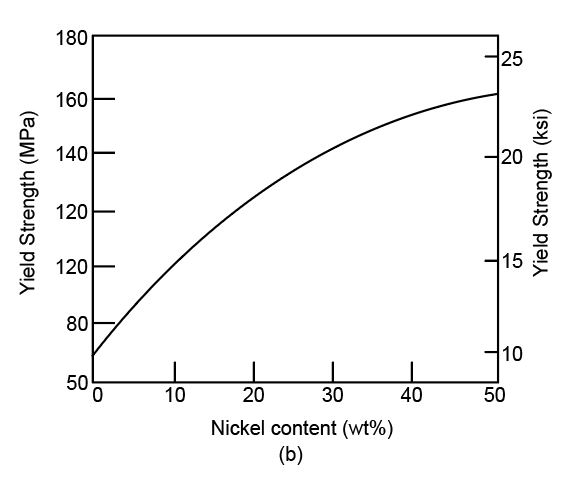
Here, with the addition of nickel into the copper in nickel-copper alloys, the strength of alloys increases.
Change in yield strength with alloy content (weight%)
The yield strength versus alloy weight % curve can be shown as,
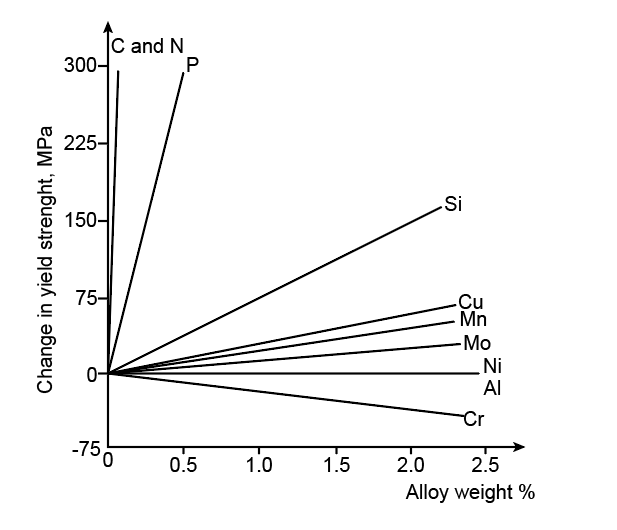
Here, due to the addition of the alloy into the ferrite and perlite steel, the yield strength of the steel varies. Like silicon is added into the steel, then the yield strength varies uniformly with alloy addition. When nickel and aluminum are added to the steel, the yield strength remains constant. Similarly, others can be interpreted.
Strain hardening
By performing cold working operations, the mechanical properties of any metals can be enhanced. When the material deforms, the elongation of the material takes place. Then strain of the material is obtained. Due to this strain, the material gets hardened. On increasing the stress on the material, it further deforms. The deformed part of the material also applies back stress in the opposite direction of the applied stress.
Due to this, extra stress is needed to deform the material further. And the workpiece gets hardened. In the initial deformation, a small amount of stress is required, but a greater amount of stress is required to deform the material further. And each strain makes the specific material hard and difficult for further stains in the material to take place. This process can be considered as strain hardening.
As a result of the plastic deformation, the dislocation in the material increases, and hence stress increases. With the strain hardening, the ductility of the material increases as the strength and hardness of the material increases.
The stress required for the movement of dislocation can be expressed as,
Here, is the initial stress needed for the dislocation movement at zero dislocation, is a constant, is the shear modulus, and is the burger vector, is the matrix density.
Precipitation hardening
The alloys like aluminum, copper, nickel, tin, etc., show an increment in hardness concerning temperature. Hardness also increases at higher temperatures post-heating. Conditions of the precipitations like the decrease in the temperature, solubility of the solute concentration in the solvent concentration should decrease. Also, the precipitate must be coherent for the hardening of the material. The precipitation hardening includes the processes like heating, quenching then aging or age-hardening.
Dispersion hardening
The hardness of the material can be increased by the interaction of the stresses of the nearby particles with the stresses of the dislocation density movement. The hardness also increases by the obstruction created by the hard particles in the dislocation movement.
The hardness can be improved by inducing fine hard (second phase) particles into the softer type of matrix. The limit up to which the hardening or strengthening can be obtained depends on the factors like the amount, shape, size, and properties of hard particles. Application of these types of strengthening mechanisms is sintered aluminum powder, powder metallurgy, etc.
The increment in the yield strength for the hard particles can be given as,
Here, C is the shear modulus, b is the burger vector, l is the mean spacing distance between two particles.
Particulate hardening
This is similar to dispersion strengthening. The only difference between both is the size of the particles. The dispersion hardening includes the size of the particles in between 1 micrometer or more than this. But in the particulate hardening, the size of the particles is 0.1 micrometer. Here, the particles should be very small and uniform in nature. Applications are powder metallurgy.
Phase transition hardening
The variation or transformation of phases of alloys takes place in these types of hardening mechanisms. For example, the austenite steel structure is converted into martensite. This transformation comes under the heat treatment process. This transformation is because of the fast cooling of the austenite (FCC) phase to room temperature for getting converted into the martensitic (BCT) phase. Here, FCC is the face-centered cubic structure, and BCT is the body-centered tetragonal structure.
Common Mistakes
- It is a misconception that dispersion and precipitate hardening are the same mechanisms. But both are different due to variations in the sizes of the particles.
- Sometimes students get confused that the strength and ductility of the material show similar variation. But in the cold working process, the ductility will decrease with the increase in strength.
- Students get confused that in the cold working process, the surface finish will be poor. But in the cold working method, the surface finish will be improved.
- Students get confused that in the cold working process achieved above recrystallization temperature. But it can be achieved before recrystallization temperature.
- It is a misconception that internal stress relief occurs in all heat treatment processes, but internal stresses are relieved in the annealing process.
Context and Applications
The topic strengthening of the alloys is significant in many technical as well as professional exams, graduation courses, post-graduation, Doctor of Philosophy, and others. For example:
- Bachelor of Technology in Mechanical Engineering
- Bachelor of Technology in Production Engineering
- Master of Technology in Mechanical Engineering
- Doctor of Philosophy in Material Science and Engineering
- Doctor of Philosophy in Metallurgical and Material Engineering
Related Concept
- Metal forming
- Cold forming
- Grain and Grain boundaries
- Grain refinement
- Strain hardening
- Precipitation Hardening
- Solid Solution Strengthening
Practice problems
Q1: Which one of the following is the correct SI unit of yield strength?
(a)
(b)
(c)
(d)
Correct option: (a)
Explanation: In the standard international system, the yield strength is measured in the units of Newton per meter square.
Q2: What is the range of temperature in the recrystallization phase of grain growth in terms of melting temperature?
(a)
(b)
(c)
(d)
Correct option: (b)
Explanation: In terms of melting temperature, the range of temperature in the recrystallization phase of grain growth is to .
Q3: What is the following is correct about the cold working process in metal forming?
(a) Surface finish poor
(b) Strength low
(c) Ductility decreases
(d) operate above the recrystallization temperature
Correct option: (c)
Explanation: In the cold working process, the component is strengthened through plastic deformation. The ductility reduces in this process because of the metallurgical variations.
Q4: What is the sequential mechanism of grain structure in the metal forming?
(a) Recovery<grain growth<recrystallization
(b) Grain growth<recrystallization<recovery
(c) Recrystallization<recovery<grain growth
(d) Recovery<recrystallization<grain growth
Correct option: (d)
Explanation: In the metal forming of grain structure, the microstructural changes that take place are recovery, recrystallization, and grain growth. The recovery helps the equipments by reducing internal stresses.
Q5: What is the following is correct regarding grain boundary strengthening when the grain size increases?
(a) Yield strength decreases
(b) Strength increases
(c) Yield strength constant
(d) Yield strength unchanged
Correct option: (a)
Explanation: According to the Hall-Petch relation, it is obtained that if the grain size rises, the yield strength will reduce because of the inverse square root correlation between the grain size and yield strength.
Want more help with your mechanical engineering homework?
*Response times may vary by subject and question complexity. Median response time is 34 minutes for paid subscribers and may be longer for promotional offers.
Search. Solve. Succeed!
Study smarter access to millions of step-by step textbook solutions, our Q&A library, and AI powered Math Solver. Plus, you get 30 questions to ask an expert each month.
Materials Science and Engineering
Metals and Alloys
Strengthening of Alloys
Strengthening of Alloys Homework Questions from Fellow Students
Browse our recently answered Strengthening of Alloys homework questions.
Search. Solve. Succeed!
Study smarter access to millions of step-by step textbook solutions, our Q&A library, and AI powered Math Solver. Plus, you get 30 questions to ask an expert each month.