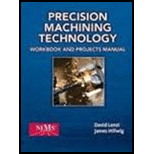
Precision Machining Technology (MindTap Course List)
2nd Edition
ISBN: 9781285444543
Author: Peter J. Hoffman, Eric S. Hopewell, Brian Janes
Publisher: Cengage Learning
expand_more
expand_more
format_list_bulleted
Concept explainers
Textbook Question
Chapter 8.2, Problem 4RQ
Name three major collet styles used in toolholding.
- a. ________________________
- b. ________________________
- c. ________________________
Expert Solution & Answer

Trending nowThis is a popular solution!

Students have asked these similar questions
I have a machine theory assignment and I am adding the conditions of this assignment here as a picture. You choose the mechanism and write the necessary solutions for this mechanism.
Q41 (20 Marks)
An ideal steam power plant works on regenerative cycle. Some steam
(y1) is bled out between first and second stage and another portion (y2)
is bled between second and third stages and feed the feed water heaters
as shown in the following figures. In terms of enthalpies determine
(1) y1 (2) y2 (3)the work at the first turbine (4) the work at the second
turbine (5) the work at the third turbine (6) the work at the pump (FP1)
(7) the work at the pump (FP2) (8) the work at the pump (CEP) (9)
the heat received at the boiler (10) the rejected heat
Boiler
NY
ST1
ST2
ST3
TI
52
Condenser
CFWH
OFWH
11
www
12
10
CEP
FP
FP
DONT USE ARTIFICIAL INTELLIGENCE
Chapter 8 Solutions
Precision Machining Technology (MindTap Course List)
Ch. 8.1 - What is an ATC?Ch. 8.1 - What is an MCU and what is its function?Ch. 8.1 - Briefly describe a ball screw and a linear guide.Ch. 8.1 - Explain the benefits of using the absolute...Ch. 8.1 - Explain the benefits of using the incremental...Ch. 8.1 - Which coordinate system uses an angle and a...Ch. 8.1 - What is the name for the type of motor used to...Ch. 8.1 - Supposing a programmer, using absolute mode,...Ch. 8.1 - What is a modal code?Ch. 8.1 - What is another name for the Cartesian coordinate...
Ch. 8.1 - List four G-codes and describe their functions. a....Ch. 8.1 - List four M-codes and describe their functions. a....Ch. 8.1 - What is the name of the character that ends each...Ch. 8.1 - Explain the purpose of the safe-start portion of a...Ch. 8.2 - Name the two primary machine axes on most CNC...Ch. 8.2 - Explain the difference between a turning center...Ch. 8.2 - List the three common types of live toolholders....Ch. 8.2 - Name three major collet styles used in...Ch. 8.2 - Name three types of workholding devices for...Ch. 8.2 - Name three major styles of turning machines....Ch. 8.2 - Explain why some workholding devices can be run at...Ch. 8.2 - Explain the difference between an OD grooving tool...Ch. 8.2 - When machining workpieces made from bar stock,...Ch. 8.2 - Describe how a sub-spindle can be used to increase...Ch. 8.2 - How does a Swiss turning center differ from a...Ch. 8.3 - Write the X- and Z-axis coordinates for the part...Ch. 8.3 - To perform a facing cut using a tool with a nose...Ch. 8.3 - Explain the difference between rigid tapping and...Ch. 8.3 - How must the feed rate for tapping using a...Ch. 8.3 - Describe what happens to a concave radius (fillet)...Ch. 8.3 - Describe what happens to an outside chamfer when...Ch. 8.3 - If a G1 code command is programmed partway through...Ch. 8.3 - List and briefly describe the two methods for...Ch. 8.3 - Explain in your own words the difference between...Ch. 8.3 - In your own words, describe a canned cycle.Ch. 8.3 - List two types of canned cycles besides roughing...Ch. 8.4 - What machine mode is generally used to manually...Ch. 8.4 - MDI stands for _________ ___________ ________.Ch. 8.4 - Which must be set first, the tool geometry offset...Ch. 8.4 - What is the process called where a program is sent...Ch. 8.4 - Explain the purpose of homing.Ch. 8.4 - What is the process called when a new program is...Ch. 8.4 - When setting up a machine to run a program that...Ch. 8.4 - What does MCS stand for?Ch. 8.4 - What is used to adjust the clamping pressure of...Ch. 8.4 - What does MCS stand for?Ch. 8.4 - What does WCS stand for?Ch. 8.4 - A workpiece offset is the distance from __________...Ch. 8.5 - Explain the difference between a machining center...Ch. 8.5 - Name the two major types of ATCs and briefly...Ch. 8.5 - What are the two basic types of tapping...Ch. 8.5 - What are the three most common styles of collets...Ch. 8.5 - What are the two basic types of tapping...Ch. 8.5 - Prob. 6RQCh. 8.5 - A programmable indexing fixture creates a fourth...Ch. 8.5 - A _______ ________ uses interchangeable tooling...Ch. 8.5 - Briefly describe a tombstone used for CNC...Ch. 8.5 - A custom ______ can be designed and built to hold...Ch. 8.5 - The combination of the machining operations...Ch. 8.6 - What are the three major axes used during CNC mill...Ch. 8.6 - What command would be given to turn on the spindle...Ch. 8.6 - What G-code designates IPM feed rate mode? IPR...Ch. 8.6 - What is the purpose of a clearance plane in CNC...Ch. 8.6 - What is the purpose of work coordinate systems?Ch. 8.6 - Briefly define linear interpolation.Ch. 8.6 - If during the last operation on a part, a G1 code...Ch. 8.6 - Briefly describe the use of I and J for the arc...Ch. 8.6 - Write two blocks of code that could be used to...Ch. 8.6 - Briefly explain the difference between rigid and...Ch. 8.6 - Define the initial plane for a canned drilling or...Ch. 8.6 - A G98 in a canned cycle sets the return point to...Ch. 8.6 - A _____ code is used to cancel a canned cycle.Ch. 8.6 - What two codes are used to activate automatic...Ch. 8.6 - What two codes are used to activate automatic...Ch. 8.6 - What code is used to cancel automatic cutter...Ch. 8.7 - Which must be set first, a work offset or a tool...Ch. 8.7 - What mode is used to manually enter programs into...Ch. 8.7 - What is the process called when a program is sent...Ch. 8.7 - Explain what may occur that makes it necessary to...Ch. 8.7 - Explain the purpose of homing.Ch. 8.7 - What is the process called when a new program is...Ch. 8.7 - What are two actions that can be taken during the...Ch. 8.7 - When automatic cutter radius compensation is used...Ch. 8.7 - Which machine mode allows short, temporary program...Ch. 8.7 - Which machine mode is used to run the machine...Ch. 8.7 - What are the two controls on the machine's control...Ch. 8.7 - What control panel feature can be used to slow a...Ch. 8.8 - Prob. 1RQCh. 8.8 - Prob. 2RQCh. 8.8 - What are the three primary steps in creating a CNC...Ch. 8.8 - Prob. 4RQCh. 8.8 - What is the definition of entity?Ch. 8.8 - Why should a toolpath be verified on the screen of...Ch. 8.8 - What is a post-processor used for?Ch. 8.8 - What is it called when mutiple touching entities...Ch. 8.8 - What type of cutting tool is usually used for...
Knowledge Booster
Learn more about
Need a deep-dive on the concept behind this application? Look no further. Learn more about this topic, mechanical-engineering and related others by exploring similar questions and additional content below.Similar questions
- Q2] (20 Marks) A steam turbine with one open feed water heater (OFWH) as shown in the following figure. In terms of enthalpies and y determine: 1- Work of HPT 2- Work of LPT 3- Work at Pump1 4- Work at Pump2 5-The heat added at the boiler 6- The quantity (y) in terms of enthalpies 7-Heat extracted from condenser 5 Boiler 2岁 3 OFWH 9 Pump2 HPT LPT 8 Pump1 O Condenserarrow_forward11.2 Boxes A and B are at rest on a conveyer belt that is initially at rest. The belt suddenly starts in an upward direction so that slipping instantly occurs between the belt and the boxes. The kinetic friction coefficients between the belt and the boxes are μk,A = 0.3 and μk,B = 0.32. Determine the initial acceleration of each box. Will the blocks stay together, or separate? 80 lb 100 lb A B 15° Hint: to see if the boxes stay together or separate, first assume they separate, and see if their resulting motion (acceleration) validates that assumption. If the their motion is not consistent with the assumption of separation, then they must stay together.arrow_forwardAn ideal gas is enclosed in a cylinder which has a movable piston. The gas is heated, resulting in an increase in temperature of the gas, and work is done by the gas on the piston so that the pressure remains constant. a) Is the work done by the gas negative, positive or zero? b) From a microscopic view, how is the internal energy of the gas molecules affected? c) Is the heat less than, greater than or equal to the work? Explain you answer.arrow_forward
- I need to adapt a real-life system to this assignment. It doesn't need to be a very complicated system. I am a senior mechanical engineering student. I need help with my mechanical theory homeworkarrow_forwardstate all the formulae associated with adiabatic processarrow_forwardDesign a Moore type synchronous state machine with three external inputs A1, A2, A3 and one output signal F. The output F goes to 1 when A1.A2.-A3 = 1 at the next system timing event. The output F stays at 1 as long as A3=0; otherwise, the output goes to 0. (Note: use a positive edge-triggered D flip-flop in the design) Write a VHDL code to describe the implementation of one-digit decimal counter using PROCESS.arrow_forward
- State all the formulae associated with the Isothermal Process.arrow_forward: +0 العنوان solle не Am 4 A pump draws water through a 300-mm diameter cast iron pipe, 15m long from a reservoir in which the water surface is 4.5 m higher than the pump and discharges through a 250- mm diameter cast iron, 75 m long, to an elevated tank in which the water surface is 60 m higher than the pump. Q=0.25 m³/s. Considering f-0.02 and the coefficients for minor head losses (k entrance 0.5, k bend 0.35, and K exit -0.5), compute the power of the pump. ۳/۱ ۲/۱ 4.5 m Kentrance 300 mm dia. 15 m Length 250 mm dia. 75 m Length kpend kexit 60 m ostlararrow_forwardA 100 m length of a smooth horizontal pipe is attached to a large reservoir. A attached to the end of the pipe to pump water into the reservoir at a volume flow rate of 0.01 m³/s. What pressure (gage) must the pump produce at the pipe to generate this flow rate? The inside diameter of the smooth pipe is 150mm. Dynamic Viscosity of water is 1*103 Kg/(m.s). K at the exit of the pipe is 1. pump 10 m D=150mm L= 100 m- Pumparrow_forward
- : +0 العنوان solle не A 4 A numn drawe water through 200 ۳/۱ ۲/۱ A heavy car plunges into a lake during an accident and lands at the bottom of the lake on its wheels as shown in figure. The door is 1.2 m high and 1 m wide, and the top edge of the door is 8 m below the free surface of the water. Determine the hydrostatic force on the door if it is located at the center of the door, and discuss if the driver can open the door, if not; suggest a way for him to open it. Assume a strong person can lift 100 kg, the passenger cabin is well-sealed so that no water leaks inside. The door can be approximated as a vertical rectangular plate. 8 m E ✓ Lakearrow_forwardTwo concentric plain helical springs of the same length are wound out of the samewire circular in cross section and supports a compressive load P. The inner springmean diameter 200 mm. Calculate the maximum stress induced in the spring if theconsists of 20 turns of mean dimeter 160 mm and the outer spring has 18 turns ofdiameter of wire is equal to 10 mm and Pis equal to 1000 N. (Take Ks=1)arrow_forwardt 1+2\xi pu +962гz P 1 A heavy car plunges into a lake during an accident and lands at the bottom of the lake on its wheels as shown in figure. The door is 1.2 m high and I m wide, and the top edge of the door is 8 m below the free surface of the water. Determine the hydrostatic force on the door if it is located at the center of the door, and discuss if the driver can open the door, if not; suggest a way for him to open it. Assume a strong person can lift 100 kg, the passenger cabin is well-sealed so that no water leaks inside. The door can be approximated as a vertical rectangular plate. 加 8 m 1.2 m Lake -20125 DI 750 x2.01 5 P 165 Xarrow_forward
arrow_back_ios
SEE MORE QUESTIONS
arrow_forward_ios
Recommended textbooks for you
- Precision Machining Technology (MindTap Course Li...Mechanical EngineeringISBN:9781285444543Author:Peter J. Hoffman, Eric S. Hopewell, Brian JanesPublisher:Cengage Learning
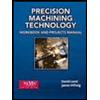
Precision Machining Technology (MindTap Course Li...
Mechanical Engineering
ISBN:9781285444543
Author:Peter J. Hoffman, Eric S. Hopewell, Brian Janes
Publisher:Cengage Learning
Fluid Mechanics - Viscosity and Shear Strain Rate in 9 Minutes!; Author: Less Boring Lectures;https://www.youtube.com/watch?v=_0aaRDAdPTY;License: Standard youtube license