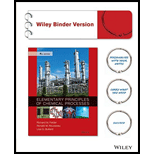
Freeze drying is a technique for dehydrating substances at low temperatures, thereby avoiding the degradation that may accompany heating. The material to be dried is cooled to a temperature at which all of the water present turns to ice. The frozen substance is then placed in a vacuum chamber and may also be subjected to radiant or microwave heating; the ice in the food sublimes, and the vapor is carried off by the vacuum pump.
Steaks are to be freeze-dried in a heated chamber at 1 torr (1 mm Hg). The steaks, which contain 72% water by mass, enter the chamber at —26°C at a rate of 50 kg/min. Of the water entering with the steaks, 96% leaves as a vapor at 60°C; the remainder leaves as a liquid with the steaks at 50°C.
- Use the heat capacity data given below and additional tabulated data for water to calculate the required heat input in kilowatts.
- When large temperature changes are not involved in a phase-change operation, a reasonable estimate of the required heat transfer rate may be obtained by neglecting contributions of temperature changes to die overall process enthalpy change (i.e., by taking only phase changes into account). Moreover, it is often reasonable to use any available values of latent heats, neglecting their dependence on temperature and pressure. In the case of the freeze-drying process, the approximation might be to calculate only the heat needed to melt all die water and vaporize 96% of it, using latent heats at the normal melting and boiling points (Table B.l) and neglecting the heat required to raise the temperature of the meat and water. What percentage error in the calculated value of Q would result from this approximation? Take the value determined in Part (a) to be exact. (c) Many substances, such as food and drugs, spoil if exposed too long to high temperatures (which accelerate rates of degradation) or to liquid water (which provides an environment for growth of microbial species that cause degradation). Also, rates of evaporation and sublimation increase as
temperature increases and pressure decreases. Use those observations to construct a one- paragraph explanation of how freeze-drying works and the reason for each step of the process. (For example, why is the sublimation done in a vacuum chamber?) Your explanation should be clear to someone with a nontechnical or nonscientific background.

Want to see the full answer?
Check out a sample textbook solution
Chapter 8 Solutions
Elementary Principles of Chemical Processes, Binder Ready Version
Additional Engineering Textbook Solutions
Elementary Surveying: An Introduction To Geomatics (15th Edition)
Modern Database Management
Starting Out with Java: From Control Structures through Data Structures (4th Edition) (What's New in Computer Science)
Database Concepts (8th Edition)
Degarmo's Materials And Processes In Manufacturing
Electric Circuits. (11th Edition)
- (30) 6. In a process design, the following process streams must be cooled or heated: Stream No mCp Temperature In Temperature Out °C °C kW/°C 1 5 350 270 2 9 270 120 3 3 100 320 4 5 120 288 Use the MUMNE algorithm for heat exchanger networks with a minimum approach temperature of 20°C. (5) a. Determine the temperature interval diagram. (3) (2) (10) (10) b. Determine the cascade diagram, the pinch temperatures, and the minimum hot and cold utilities. c. Determine the minimum number of heat exchangers above and below the pinch. d. Determine a valid heat exchange network above the pinch. e. Determine a valid heat exchange network below the pinch.arrow_forwardUse this equation to solve it.arrow_forwardQ1: Consider the following transfer function G(s) 5e-s 15s +1 1. What is the study state gain 2. What is the time constant 3. What is the value of the output at the end if the input is a unit step 4. What is the output value if the input is an impulse function with amplitude equals to 3, at t=7 5. When the output will be 3.5 if the input is a unit steparrow_forward
- give me solution math not explinarrow_forwardExample (6): An evaporator is concentrating F kg/h at 311K of a 20wt% solution of NaOH to 50wt %. The saturated steam used for heating is at 399.3K. The pressure in the vapor space of the evaporator is 13.3 KPa abs. The 5:48 O Transcribed Image Text: Example (7): Determine thearrow_forward14.9. A forward feed double-effect vertical evaporator, with equal heating areas in each effect, is fed with 5 kg/s of a liquor of specific heat capacity of 4.18 kJ/kg K. and with no boiling point rise, so that 50 per cent of the feed liquor is evaporated. The overall heat transfer coefficient in the second effect is 75 per cent of that in the first effect. Steam is fed at 395 K and the boiling point in the second effect is 373 K. The feed is heated by an external heater to the boiling point in the first effect. It is decided to bleed off 0.25 kg/s of vapour from the vapour line to the second effect for use in another process. If the feed is still heated to the boiling point of the first effect by external means, what will be the change in steam consumption of the evaporator unit? For the purpose of calculation, the latent heat of the vapours and of the steam may both be taken as 2230 kJ/kgarrow_forward
- Example(3): It is desired to design a double effect evaporator for concentrating a certain caustic soda solution from 12.5wt% to 40wt%. The feed at 50°C enters the first evaporator at a rate of 2500kg/h. Steam at atmospheric pressure is being used for the said purpose. The second effect is operated under 600mmHg vacuum. If the overall heat transfer coefficients of the two stages are 1952 and 1220kcal/ m2.h.°C. respectively, determine the heat transfer area of each effect. The BPR will be considered and present for the both effect 5:49arrow_forwardالعنوان ose only Q Example (7): Determine the heating surface area 개 required for the production of 2.5kg/s of 50wt% NaOH solution from 15 wt% NaOH feed solution which entering at 100 oC to a single effect evaporator. The steam is available as saturated at 451.5K and the boiling point rise (boiling point evaluation) of 50wt% solution is 35K. the overall heat transfer coefficient is 2000 w/m²K. The pressure in the vapor space of the evaporator at atmospheric pressure. The solution has a specific heat of 4.18kJ/ kg.K. The enthalpy of vaporization under these condition is 2257kJ/kg Example (6): 5:48 An evaporator is concentrating F kg/h at 311K of a 20wt% solution of NaOH to 50wt %. The saturated steam used for heating is at 399.3K. The pressure in the vapor space of the evaporator is 13.3 KPa abs. The 5:48 1 J ۲/۱ ostrarrow_forwardExample 8: 900 Kg dry solid per hour is dried in a counter current continues dryer from 0.4 to 0.04 Kg H20/Kg wet solid moisture content. The wet solid enters the dryer at 25 °C and leaves at 55 °C. Fresh air at 25 °C and 0.01Kg vapor/Kg dry air is mixed with a part of the moist air leaving the dryer and heated to a temperature of 130 °C in a finned air heater and enters the dryer with 0.025 Kg/Kg alry air. Air leaving the dryer at 85 °C and have a humidity 0.055 Kg vaper/Kg dry air. At equilibrium the wet solid weight is 908 Kg solid per hour. *=0.0088 Calculate:- Heat loss from the dryer and the rate of fresh air. Take the specific heat of the solid and moisture are 980 and 4.18J/Kg.K respectively, A. =2500 KJ/Kg. Humid heat at 0.01 Kg vap/Kg dry=1.0238 KJ/Kg. "C. Humid heat at 0.055 Kg/Kg 1.1084 KJ/Kg. "C 5:42 Oarrow_forward
- Introduction to Chemical Engineering Thermodynami...Chemical EngineeringISBN:9781259696527Author:J.M. Smith Termodinamica en ingenieria quimica, Hendrick C Van Ness, Michael Abbott, Mark SwihartPublisher:McGraw-Hill EducationElementary Principles of Chemical Processes, Bind...Chemical EngineeringISBN:9781118431221Author:Richard M. Felder, Ronald W. Rousseau, Lisa G. BullardPublisher:WILEYElements of Chemical Reaction Engineering (5th Ed...Chemical EngineeringISBN:9780133887518Author:H. Scott FoglerPublisher:Prentice Hall
- Industrial Plastics: Theory and ApplicationsChemical EngineeringISBN:9781285061238Author:Lokensgard, ErikPublisher:Delmar Cengage LearningUnit Operations of Chemical EngineeringChemical EngineeringISBN:9780072848236Author:Warren McCabe, Julian C. Smith, Peter HarriottPublisher:McGraw-Hill Companies, The
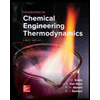
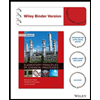
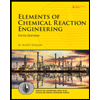
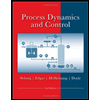
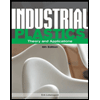
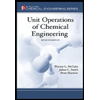