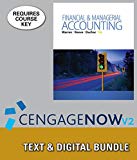
Concept explainers
Activity-based and department rate product costing and product cost distortions
Black and Blue Sports Inc. manufactures two products: snowboards and skis. The factory
Indirect labor | $507,000 |
Cutting Department | 156,000 |
Finishing Department | 192,000 |
Total | $855,000 |
The activity hase associated with the two production departments is direct labor hours. The indirect labor can be assigned to two different activities as follows:
Activity | Budgeted Activity Cost | Activity Base |
Production control | $237,000 | Number of production runs |
Materials handling | 270,000 | Number of moves |
Total | $507,000 |
The activity-base usage quantities and units produced for the two products follow:
Number o Production Runs |
Number of Moves |
Direct Labor Hours—Cutting |
Direct Labor Hours—Finishing |
Units Produced |
|
Snowboards | 430 | 5,000 | 4,000 | 2,000 | 6,000 |
Skis | _70 | 2,500 | 2,000 | 4,000 | 6,000 |
Total | 500 | 7,500 | 6,000 | 6,000 | 12,000 |
Instructions
- 1. Determine the factory overhead rates under the multiple production department rate method. Assume that indirect labor is associated with the production departments, so that the total factory overhead is $315,000 and $540,000 for the Cutting and finishing departments, respectively.
- 2. Determine the total and per-unit
factory overhead costs allocated to each product, using the multiple production department overhead rates in (1). - 3. Determine the activity rates, assuming that the indirect labor is associated with activities rather than with the production departments.
- 4. Determine the total and per-unit cost assigned to each product under activity-based costing.
- 5. Explain the difference in the per-unit overhead allocated to each product under the multiple production department factory overhead rate and activity-based costing methods.
1.

Multiple production department factory overhead rate: This allocation method identifies different departments in the process of production. The factory overheads are allocated to products based on the overhead rate for each of the production departments.
Formula to compute multiple production department overhead rate:
Activity-based costing (ABC) method: The costing method which allocates overheads to the products based on factory overhead rate for each activity or cost object, according to the cost pooled for the cost drivers (allocation base).
Formula to compute activity-based overhead rate:
To compute: The multiple production department overhead rate for both departments
Explanation of Solution
Compute multiple production department overhead rate for cutting department.
Compute multiple production department overhead rate for finishing department.
2.

To compute: The factory overhead allocated to total and per unit of each product
Explanation of Solution
Compute total factory overhead and per unit overhead allocated for snowboards.
Production Department | Multiple Production Department Overhead Rate | × | Total Number of Budgeted DLH | = | Factory Overhead |
Cutting | $52.50 per DLH | × | 4,000 DLH | = | $210,000 |
Finishing | $90 per DLH | × | 2,000 DLH | = | 180,000 |
Total factory overhead costs allocated for snowboards | $390,000 | ||||
Number of units of snowboards | ÷ 6,000 units | ||||
Factory overhead cost per unit of snowboard | $65.00 |
Table (1)
Note: Refer to part (A) for value and computation of multiple production department overhead rate.
Compute total factory overhead and per unit overhead allocated for skis.
Production Department | Multiple Production Department Overhead Rate | × | Total Number of Budgeted DLH | = | Factory Overhead |
Cutting | $52.50 per DLH | × | 2,000 DLH | = | $105,000 |
Finishing | $90 per DLH | × | 4,000 DLH | = | 360,000 |
Total factory overhead costs allocated for skis | $465,000 | ||||
Number of units of skis | ÷ 6,000 units | ||||
Factory overhead cost per unit of ski | $77.50 |
Table (2)
Note: Refer to part (A) for value and computation of multiple production department overhead rate.
3.

To compute: The activity-based overhead rate for each of the given activities
Explanation of Solution
Compute activity-based overhead rates.
Computation of Activity-Based Overhead Rates | |||||
Activity | Activity Cost | ÷ | Total Activity-Base Usage | = | Activity-Based Overhead Rates |
Production control | $237,000 | ÷ | 500 production runs | = | $474 per run |
Materials handling | 270,000 | ÷ | 7,500 moves | = | $36 per move |
Cutting | 156,000 | ÷ | 6,000 DLH | = | $26 per DLH |
Finishing | 192,000 | ÷ | 6,000 DLH | = | $32 per DLH |
Table (3)
4.

To compute: The activity-cost per unit of the products
Explanation of Solution
Compute activity cost allocated per unit of snowboards.
Activity | Activity-Based Overhead Rates | × | Actual Use of Activity-Base (Cost Driver) | = | Activity Cost Allocated |
Production control | $474 per run | × | 430 runs | = | $203,820 |
Materials handling | 36 per move | × | 5,000 moves | = | 180,000 |
Cutting | 26 per DLH | × | 4,000 DLH | = | 104,000 |
Finishing | 32 per DLH | × | 2,000 DLH | = | 64,000 |
Total activity costs allocated to snowboards | $551,820 | ||||
Number of units of snowboard | ÷ 6,000 units | ||||
Activity-based overhead cost per unit of snowboards | $91.97 |
Table (4)
Note: Refer to Table (3) for the value and computation of activity allocation rates.
Compute activity cost allocated per unit of snowboards.
Activity | Activity-Based Overhead Rates | × | Actual Use of Activity-Base (Cost Driver) | = | Activity Cost Allocated |
Production control | $474 per run | × | 70 runs | = | $33,180 |
Materials handling | 36 per move | × | 2,500 moves | = | 90,000 |
Cutting | 26 per DLH | × | 2,000 DLH | = | 52,000 |
Finishing | 32 per DLH | × | 4,000 DLH | = | 128,000 |
Total activity costs allocated to skis | $303,180 | ||||
Number of units of skis | ÷ 6,000 units | ||||
Activity-based overhead cost per unit of ski | $50.53 |
Table (5)
Note: Refer to Table (3) for the value and computation of activity allocation rates.
5.

To discuss: The product cost distortion due to multiple production department overhead rate
Explanation of Solution
The product cost under multiple production department overhead rate approach and ABC approach are different. The product cost is distorted in multiple production department overhead rate approach. Although the time spent for cutting and finishing for snowboards and skis is in the same ratio, but the production control department and materials handling department are not accounted for in multiple department overhead rate method.
Want to see more full solutions like this?
Chapter 26 Solutions
Bundle: Financial & Managerial Accounting, 13th + Working Papers, Volume 1, Chapters 1-15 For Warren/reeve/duchac’s Corporate Financial Accounting, ... 13th + Cengagenow™v2, 2 Terms Access Code
- HELP!!!arrow_forwardCan you answer this general accounting question?arrow_forwardAdidas, Evans and Merrelle are partners who share profit and loss in the ratio 30%, 25%, 25% and 20%. Capital balances before division of Net loss of P30,000 and withdrawals of P10,000 each, were as follows: 120,000.00 - Adidas 150,000.00 - Evans 130,000.00 - Merrelle 100,000.00- Converse 1. Converse is to retire from the partnership and will be paid P84,000 2. Converse is to retire and will be paid P100,000. Use the Bonus method 3. Converse is to retire and will be paid P70,000. Use the Revaluation of asset method 4. Converse is to retire and will be purchased by Merrelle paying P90,000 5. Converse is to retire from the partnership and will have an increase share of P10,000 in the revaluation of asset 6 Converse is to retire from the partnership and will be paid P90,000 Which method would Evans would prefer assuming the partners divide the P/L equally after the retirement of Converse?arrow_forward
- ansarrow_forwardElle Corporation has the following standards for its direct materials: 1. Standard Cost: $3.80 per pound 2. Standard Quantity: 6.00 pounds per product. During the most recent month, the company purchased and used 33,900 pounds of material in manufacturing 5,600 products, at a total cost of $131,900. Compute the materials quantity variance.arrow_forward?arrow_forward
- What is the firm's return on equity on these general accounting question?arrow_forwardAnalyze the role of the accounting function in supporting corporate governance and risk management processes. Consider the ways in which accountants can contribute to the identification, assessment, and mitigation of organizational risks, beyond their traditional financial reporting responsibilities.arrow_forwardPlease provide answer the general accounting questionarrow_forward
- Managerial AccountingAccountingISBN:9781337912020Author:Carl Warren, Ph.d. Cma William B. TaylerPublisher:South-Western College PubPrinciples of Cost AccountingAccountingISBN:9781305087408Author:Edward J. Vanderbeck, Maria R. MitchellPublisher:Cengage LearningCornerstones of Cost Management (Cornerstones Ser...AccountingISBN:9781305970663Author:Don R. Hansen, Maryanne M. MowenPublisher:Cengage Learning
- Financial And Managerial AccountingAccountingISBN:9781337902663Author:WARREN, Carl S.Publisher:Cengage Learning,Managerial Accounting: The Cornerstone of Busines...AccountingISBN:9781337115773Author:Maryanne M. Mowen, Don R. Hansen, Dan L. HeitgerPublisher:Cengage LearningPrinciples of Accounting Volume 2AccountingISBN:9781947172609Author:OpenStaxPublisher:OpenStax College
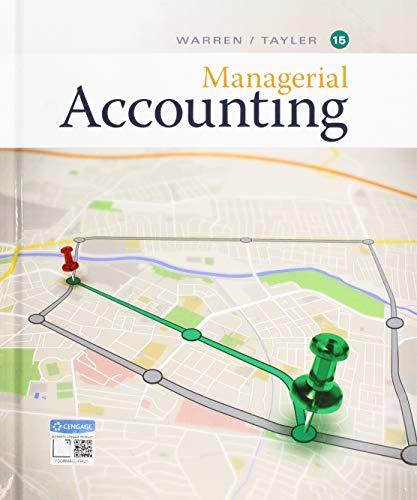
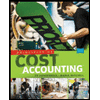
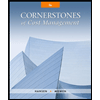
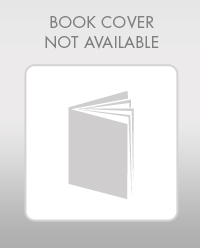
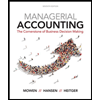