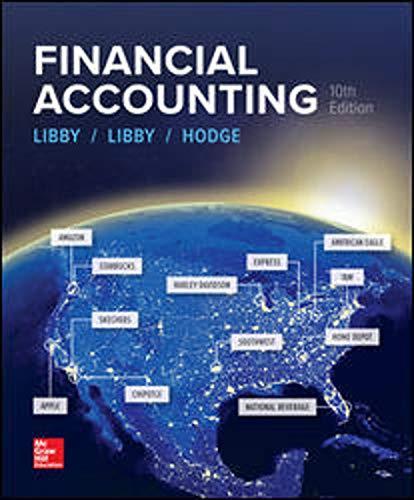
Concept explainers
Gourmet Master, Inc., uses activity-based costing to determine the cost of its stainless steel ovens. Activity-based product cost information is as follows:
Activity |
Activity-Base |
x | Activity Rate per Hour |
= |
Activity Cost |
Fabrication | 0.75 | $24.00 | $18.00 | ||
Assembly | 1.50 | 20.00 | 30.00 | ||
Inspection | 0.30 | 25.00 | 7.50 | ||
Moving | 0.25 | 12.00 | 3.00 | ||
Total activity cost per unit | $58.50 |
These activities only include the labor portion of the cost. Fabrication is the cutting and shaping of metal to be used in the assembly of the ovens. If the metal is not fabricated properly, additional time is required during final assembly to trim and adjust the metal pieces to fit properly. This has been a problem in Assembly. Management proposes improvements in Fabrication requiring the fabrication work to be done slower, but more accurately. As a result, the time in fabrication will increase to an hour per unit. However, because of the additional care, the parts are expected to fit better during assembly, thus reducing assembly time to 1.10 hours per unit.
a. Determine the revised activity-based cost per unit under the new fabrication plan.
b. Does this plan reduce the activity cost per unit of the oven?
Please show your work.

Trending nowThis is a popular solution!
Step by stepSolved in 2 steps with 1 images

- Time Clock Shop manufactures clocks on an automated assembly line. It utilizes two cost categories: direct materials and conversion costs. Each product must pass through the Assembly Department and the Testing Department. Direct materials are added at the beginning of production, while conversion costs are allocated evenly throughout production. The company uses weighted-average costing. Data for the Assembly Department are given in the table. (Click the icon to view the table.) What is the total amount debited to the work-in-process account during the month of June at Time Clock Shop? A. $450,000 B. $2,270,000 C. $3,250,000 D. $2,000,000 E. $2,450,000 Table Work in process, beginning inventory Direct materials (100% complete) Conversion costs (50% complete) Units started during June Work in process, ending inventory Direct materials (100% complete) Conversion costs (75% complete) Work in process, beginning inventory Direct materials Conversion costs Direct materials costs added during…arrow_forwardThe following table presents the activities and activity drivers that LampPlus uses in manufacturing Product 1 and Product 2. Complete the table: Activity Design Preparation Machining Finishing Inspection Packaging Shipping Cost Activity Driver $ 39,060 Design time $ 67,650 Labor hours 105,200 Machine hours $ Batches Units Orders $ 12,720 Packages Driver Usage Prod. 1 840 3,130 209 76 Prod. 2 1,330 hours hours 300 56 Activity Rate $ $ $ $ /hour /hour 20 /hour 50 /batch 17 /unit 302 /order /package Activity Cost:Prod. 1 $ $ $ $ 34,430 31,200 Activity Cost:Prod. 2 9,690 $ 12,986 $ 19,720 3,600arrow_forwardHaresharrow_forward
- Drilling Company uses activity-based costing and provides this information: Driver Rate Manufacturing Activity Materials handling Machinery Assembly Inspection Cost Driver Drilling has just completed 74 units of a component for a customer. Each unit required 94 parts and 2.70 machine hours. The prime cost is $1,240 per finished unit. All other manufacturing costs are classified as manufacturing overhead. Required 1 Number of parts Number of machine hours Number of parts Number of finished units Required: 1. Compute the total manufacturing costs and the unit costs of the 74 units just completed using ABC costing. 2. In addition to the manufacturing costs, the firm has determined that the total cost of upstream activities, including research and development and product design, is $174 per unit. The total cost of downstream activities, such as distribution, marketing, and customer service, is $294 per unit. Compute the full product cost per unit, including upstream, manufacturing, and…arrow_forwardonly typed solutionarrow_forwardShalom Company uses three activity pools to apply overhead to its products. Each activity has a cost driver used to allocate the overhead costs to the product. The activities and related overhead costs are as follows: product design P40,000; machining P300,000; and material handling P100,000. The cost drivers and estimated use are as follows: Activity Cost Pools Activities Product design Number of product changes Machining Machine hours Material handling Number of set-ups X Estimated Use of Cost Driver Per Activity Amounts must be in whole numbers. Example: 88,000 or (88,000) Unit costs be in whole numbers. Example: 88 Format of percentages: 88% Words must be in capital letters. 10 150,000 100 What is the activity-based overhead rate for material handling? Jarrow_forward
- Please help me with show all calculation thankuarrow_forwardPlease refer to the pictures for parts A and B. Part C is below: Cost assignment—Weighted average EUP Cost per EUP Total cost Completed and transferred out Direct materials Conversion Total Completed and transferred out Ending work in process Direct materials Conversion Total ending work in process Total costs accounted for HI-T Company.arrow_forwardplease give answer step by steparrow_forward
- Rex Industries has identified three different activities as cost drivers: machine setups, machine hours, and inspections. The overhead and estimated usage are: Compute the overhead rate for each activity. Round your answers to two decimal places. Overhead Overhead Annual Rate per Activity per Activity Usage Activity Machine Setups $157,850 4,100 $ Machine Hours 324,622 14,114 2$ Inspections 119,000 3,400arrow_forwardMultiple Choice $9,907.97 $89,171.73 $5,173.02 $136.51arrow_forwardCan someone help me with the second part?arrow_forward
- AccountingAccountingISBN:9781337272094Author:WARREN, Carl S., Reeve, James M., Duchac, Jonathan E.Publisher:Cengage Learning,Accounting Information SystemsAccountingISBN:9781337619202Author:Hall, James A.Publisher:Cengage Learning,
- Horngren's Cost Accounting: A Managerial Emphasis...AccountingISBN:9780134475585Author:Srikant M. Datar, Madhav V. RajanPublisher:PEARSONIntermediate AccountingAccountingISBN:9781259722660Author:J. David Spiceland, Mark W. Nelson, Wayne M ThomasPublisher:McGraw-Hill EducationFinancial and Managerial AccountingAccountingISBN:9781259726705Author:John J Wild, Ken W. Shaw, Barbara Chiappetta Fundamental Accounting PrinciplesPublisher:McGraw-Hill Education
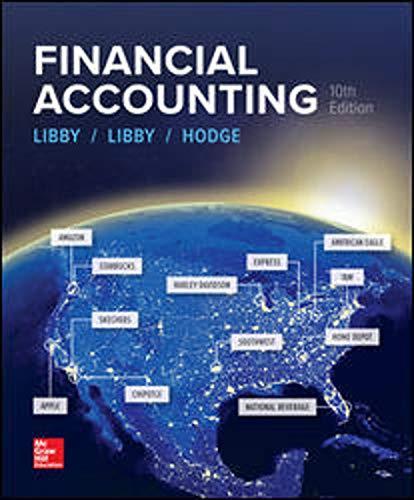
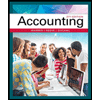
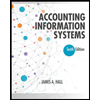
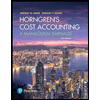
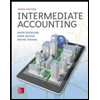
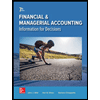