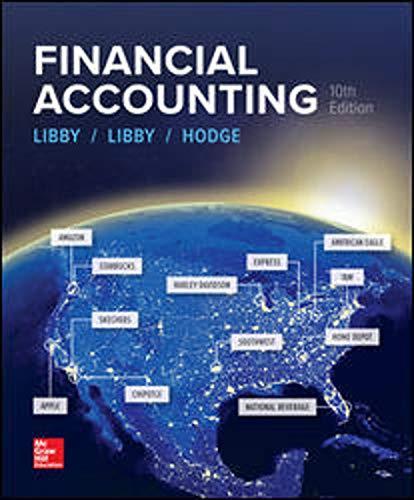
FINANCIAL ACCOUNTING
10th Edition
ISBN: 9781259964947
Author: Libby
Publisher: MCG
expand_more
expand_more
format_list_bulleted
Concept explainers
Question
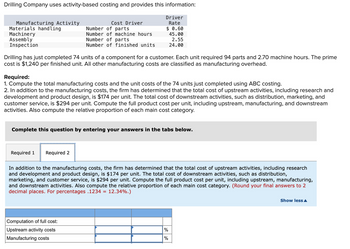
Transcribed Image Text:Drilling Company uses activity-based costing and provides this information:
Driver
Rate
Manufacturing Activity
Materials handling
Machinery
Assembly
Inspection
Cost Driver
Drilling has just completed 74 units of a component for a customer. Each unit required 94 parts and 2.70 machine hours. The prime
cost is $1,240 per finished unit. All other manufacturing costs are classified as manufacturing overhead.
Required 1
Number of parts
Number of machine hours
Number of parts
Number of finished units
Required:
1. Compute the total manufacturing costs and the unit costs of the 74 units just completed using ABC costing.
2. In addition to the manufacturing costs, the firm has determined that the total cost of upstream activities, including research and
development and product design, is $174 per unit. The total cost of downstream activities, such as distribution, marketing, and
customer service, is $294 per unit. Compute the full product cost per unit, including upstream, manufacturing, and downstream
activities. Also compute the relative proportion of each main cost category.
Required 2
$ 0.60
45.00
2.55
24.00
Complete this question by entering your answers in the tabs below.
Computation of full cost:
Upstream activity costs
Manufacturing costs
In addition to the manufacturing costs, the firm has determined that the total cost of upstream activities, including research
and development and product design, is $174 per unit. The total cost of downstream activities, such as distribution,
marketing, and customer service, is $294 per unit. Compute the full product cost per unit, including upstream, manufacturing,
and downstream activities. Also compute the relative proportion of each main cost category. (Round your final answers to 2
decimal places. For percentages.1234 = 12.34%.)
do do
%
%
Show less ▲
Expert Solution

This question has been solved!
Explore an expertly crafted, step-by-step solution for a thorough understanding of key concepts.
Step by stepSolved in 4 steps

Knowledge Booster
Learn more about
Need a deep-dive on the concept behind this application? Look no further. Learn more about this topic, accounting and related others by exploring similar questions and additional content below.Similar questions
- Wykes Metal Working uses a special lathe to shape components. Data on the lathe and its usage follow: Resources used Energy Repairs Resources supplied Energy Repairs Energy Repairs Cost Driver Rate Unused Resource Capacity $ 2.45 per machine-hour $ 5.45 per job $ 6,400 $ 5,250 Cost Driver Volume Required: Compute the cost of unused resource capacity in energy and repairs for Wykes Metal Working. 2,140 machine-hours 720 jobsarrow_forwardHayward Industries manufactures dining chairs and tables. The following information is available: Dining Chairs Tables Total Cost Machine setups 200 Inspections Labor hours 250 600 $48,000 470 $72,000 2,600 2,400 Hayward is considering switching from one overhead rate based on labor hours to activity-based costing. Perform the following analyses for these two components of overhead: Compute total machine setups and inspection costs assigned to each product, using a single overhead rate. Total Costs Dining chairs $_ $_ Tables Compute total machine setups and inspection costs assigned to each product, using activity-based costing. Total Costs Dining chairs $_ Tables $_arrow_forwardH1. Accountarrow_forward
- Use the following information to answer questions. (Algo) The following information is available for ADT Company, which produces special-order security products and uses a job order costing system. Overhead is applied using a predetermined overhead rate of 55% of direct labor cost. Inventories [The following information applies to the questions displayed below.] Raw materials Work in process Finished goods Beginning of period $ 48,000 9,000 65,000 Cost incurred for the period Raw materials purchases Factory payroll Factory overhead (actual) Indirect materials used Indirect labor used Other overhead costs End of Period $ 43,000 20,700 34,900 $ 179,000 250,000 12,000 57,500 114,500arrow_forward2.A company makes two products 1 and 2. The finishing activity pool has estimated manufacuring costs of $82,749 and the cost drivers for Product 1 is 359 and 282 for Product 2. The assembling activity pool has estimated costs of $63,039 and the cost drivers for Product 1 is 200 and 300 for Product 2. Direct labor hours for Product 1 is 497and 303 for Product 2. What is the total manufacturing overhead cost to be assigned to Product 1 using a single overhead rate as under tradional cost accounting? Round your final answer to the nearest whole dollar and do not put a dollar sign in your answer.arrow_forward6arrow_forward
- A company has traditionally allocated its overhead based on machine hours but had collected this information to change to activity-based costing: Estimated Activity Activity Center Product 1 Product 2 Estimated Cost Machine Setups 15 45 $11,400 Assembly Parts 4,500 4,500 217,800 Packaging Pieces 250 200 27,450 Machine Hours per Unit 4 3 Production Volume 750 1,500 A. How much overhead would be allocated to each unit under the traditional allocation method? Round your answers to two decimal places. Product 1 Product 2 Allocation per unit ? ? B. How much overhead would be allocated to each unit under activity-based costing? Round your answers to two decimal places. Product 1 Product 2 Allocation per unit ? ?arrow_forwardTelecom uses activity - based costing to allocate all manufacturing conversion costs. Telecom produces cellular telephones; each phone has $20.00 of direct materials, includes 50 parts and requires 3 hours of machine time. Additional information follows: Activity Materials handling Machining Assembling Packaging What is the cost of machining per phone? A. $6 B. $9 C. $200 O D. $175 Allocation Base Number of parts Machine hours Number of parts Number of finished units Cost Allocation Rate $3.50 per part $2.00 per machine hour $4.00 per part $3.00 per finished unitarrow_forwardRequired information Skip to question Greenwood Company manufactures two products—15,000 units of Product Y and 7,000 units of Product Z. The company uses a plantwide overhead rate based on direct labor-hours. It is considering implementing an activity-based costing (ABC) system that allocates all of its manufacturing overhead to four cost pools. The following additional information is available for the company as a whole and for Products Y and Z: Activity Cost Pool Activity Measure Estimated Overhead Cost Expected Activity Machining Machine-hours $ 227,700 11,000 MHs Machine setups Number of setups $ 153,900 270 setups Production design Number of products $ 91,000 2 products General factory Direct labor-hours $ 257,000 10,000 DLHs Activity Measure Product Y Product Z Machining 8,700 2,300 Number of setups 60 210 Number of products 1 1 Direct labor-hours 8,700 1,300 2. Using the plantwide overhead rate, how much manufacturing overhead cost is…arrow_forward
- Give me correct answer with explanation.farrow_forwardConcord Company manufactures two products, Mini A and Maxi B. Concord's overhead costs consist of setting up machines- $860000; machining- $2020000; and inspecting- $570000. Information on the two products is: Direct labour hours Machine setups Machine hours Inspections Mini A Maxi B $1324000. $1660400. $1690400. O $2542105. 10000 600 24000 800 28000 400 26000 700 Overhead applied to Maxi B using activity-based costing isarrow_forwardCompute the cost that is assigned to the car wheels and truck wheels product lines using an activity-based costing system, given the following information. Use of Cost Drivers per Product Car Truck Number of setups 200 800 Direct labor hours 43,000 45,000 Number of inspections 100 1,100 Car Wheels Setting up machines SA $ Assembling $ Truck Wheels $ $ SA Inspection $ SA $ Total cost assigned $ SA $ SUPPORTarrow_forward
arrow_back_ios
SEE MORE QUESTIONS
arrow_forward_ios
Recommended textbooks for you
- AccountingAccountingISBN:9781337272094Author:WARREN, Carl S., Reeve, James M., Duchac, Jonathan E.Publisher:Cengage Learning,Accounting Information SystemsAccountingISBN:9781337619202Author:Hall, James A.Publisher:Cengage Learning,
- Horngren's Cost Accounting: A Managerial Emphasis...AccountingISBN:9780134475585Author:Srikant M. Datar, Madhav V. RajanPublisher:PEARSONIntermediate AccountingAccountingISBN:9781259722660Author:J. David Spiceland, Mark W. Nelson, Wayne M ThomasPublisher:McGraw-Hill EducationFinancial and Managerial AccountingAccountingISBN:9781259726705Author:John J Wild, Ken W. Shaw, Barbara Chiappetta Fundamental Accounting PrinciplesPublisher:McGraw-Hill Education
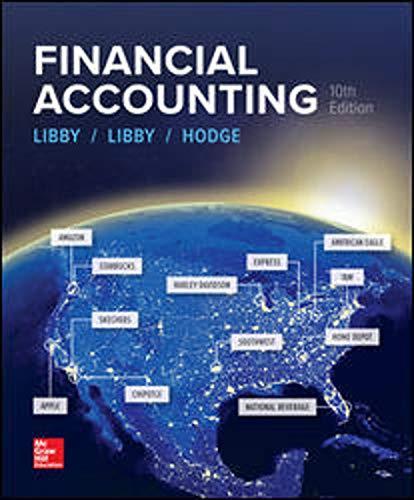
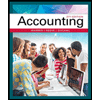
Accounting
Accounting
ISBN:9781337272094
Author:WARREN, Carl S., Reeve, James M., Duchac, Jonathan E.
Publisher:Cengage Learning,
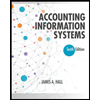
Accounting Information Systems
Accounting
ISBN:9781337619202
Author:Hall, James A.
Publisher:Cengage Learning,
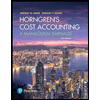
Horngren's Cost Accounting: A Managerial Emphasis...
Accounting
ISBN:9780134475585
Author:Srikant M. Datar, Madhav V. Rajan
Publisher:PEARSON
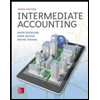
Intermediate Accounting
Accounting
ISBN:9781259722660
Author:J. David Spiceland, Mark W. Nelson, Wayne M Thomas
Publisher:McGraw-Hill Education
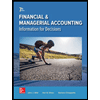
Financial and Managerial Accounting
Accounting
ISBN:9781259726705
Author:John J Wild, Ken W. Shaw, Barbara Chiappetta Fundamental Accounting Principles
Publisher:McGraw-Hill Education