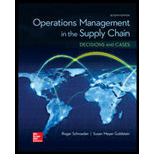
Concept explainers
a)
To determine: The total cost of supplying the product to Country P.
Introduction:
Supplier selection is the process of evaluating the performance of each supplier and comparing it with in-house production to choose the capable supplier to support the output of the organization.
b)
To determine: The risk associated with Country P’s supplier.
Introduction:
Supplier selection is the process of evaluating the performance of each supplier and comparing it with in-house production to choose the capable supplier to support the output of the organization.
c)
To determine: Whether the firm should outsource or not.
Introduction:
Supplier selection is the process of evaluating the performance of each supplier and comparing it with in-house production to choose the capable supplier to support the output of the organization.

Want to see the full answer?
Check out a sample textbook solution
Chapter 17 Solutions
OPERATIONS MANAGEMENT IN THE SUPPLY CHAIN: DECISIONS & CASES (Mcgraw-hill Series Operations and Decision Sciences)
- Analyse one specific and current issue (or “gap”) in service delivery, why has this arisen and what is one strategy that has been developed to address the issue.arrow_forwardAt Hewlett-Packard (HP), billions of dollars of product are being shipped - from computers and diagnostic devices to toner cartridges each year. Customer orders come in 24 hours a day, 365 days a year. Nearly 16,000 different products are requested daily and have to be shipped from six different warehouses which are located 30 or more miles apart. It often takes weeks to get the products into the customer’s hand. This is a serious problem if customers have contracts with HP stating deliveries are to be made in three (3) business days, or less. That means that from the time a customer calls the HP customer service line, they will have their replacement part and be back in operation within 72 hours or less, no matter where that customer is located. On average, delivery to customers takes 6+ days. It is imperative that HP guarantee for delivery of products and services are followed to protect their image, secure its position in the market place, increase its competitive advantage and its…arrow_forwardDiscuss the concept of service orchestration and its importance in coordinating complex business processes.arrow_forward
- Mark Hopper owns Dane Champions, a dog kennel that raises champion Great Danes for showing and breeding. His vision is to be the best-known breeder of Great Danes globally. His strategy is to breed and sell dogs from outstanding lineage from the standpoint of both physical health and good-natured temperaments. Following is information about operations over the last year. Number of breedings Ac€¦Ac€¦Ac€¦Ac€¦Ac€¦Ac€¦Ac€¦Ac€¦Ac€¦Ac€¦Ac€¦Ac€¦Ac€¦Ac€¦Ac€¦.. 10 Number of puppies Ac€¦Ac€¦Ac€¦Ac€¦Ac€¦Ac€¦Ac€¦Ac€¦Ac€¦Ac€¦Ac€¦Ac€¦Ac€¦Ac€¦Ac€¦Ac€¦.. 45 Number of puppies sold…arrow_forwardOutline the five gaps that can cause problems in service delivery as described in the Gap Model of Service Delivery. Please define each gap.arrow_forwardUber is an international company that faced an ethical problem. The problem is many passengers were harassed and assaulted sexually. Q: The proposed solutions with an explanation of each solutionarrow_forward
- As a response to COVID -19 issue, Kurmitola General Hospital, Dhaka, has started treating coronavirus patients since last month. Healthcare workers are on the frontline toward the COVID-19 response. Two volunteers from North South University intend to join in Kurmitola General Hospital to assist the medical team. Since they do not have any technical knowledge, they will be helping the team with activities like registering the patients, providing initial information about treatment, collecting samples, etc. As the manager of this hospital, you must arrange training for these volunteers to enhance their skills and willingness to work. Therefore, list and briefly explain the steps you will follow to train these individuals. How would you measure the effectiveness of the provided training?arrow_forwardThe capacity of the Internet to accommodate two distinct types of application support services remains uncertain. These services exhibit variations in several significant aspects?arrow_forwardFor nearly 20 years, Cullumber Coatings has provided painting and galvanizing services for manufacturers in its region. Manufacturers of various metal products have relied on the quality and quick turnaround time provided by Cullumber Coatings and its 20 skilled employees. During the past year, as a result of a sharp upturn in the economy, the company’s sales have increased by 30% relative to the previous year. The company has not been able to increase its capacity fast enough, so Cullumber Coatings has had to turn work away because it cannot keep up with customer requests.Top management is considering the purchase of a sophisticated robotic painting booth. The booth would represent a considerable move in the direction of automation versus manual labour. If Cullumber Coatings purchases the booth, it would most likely lay off 15 of its skilled painters. To analyze the decision, the company compiled production information from the most recent year and then prepared a parallel compilation…arrow_forward
- Can you give me some ideas for research questions about logistics in the philippinesarrow_forwardDiscuss the application of technology and service delivery process within Marriott hotels in London.arrow_forwardSouth Africa is experiencing an increase in investment pertaining to logistics and logistical infrastructure. you have been recruited by Patrice Motsepe, a mining billionaire businessman to head up the supply chain department at one of his new commissioned logistics companies. As the supply chain head, you are tasked with answering the following questions. Mr Motsepe is extremely busy and doesn’t have the time to get involved with the operations of this new company hence he has hired you. Assist Mr Motsepe to understand this new venture by differentiating between the concept of logistics management and supply chain management with a practical example of each.arrow_forward
- Purchasing and Supply Chain ManagementOperations ManagementISBN:9781285869681Author:Robert M. Monczka, Robert B. Handfield, Larry C. Giunipero, James L. PattersonPublisher:Cengage Learning
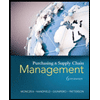