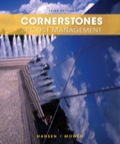
Concept explainers
1 a.
Ascertain the productivity profile for 2014 using actual inputs.
1 a.

Explanation of Solution
Productivity measurement: The productivity measurement refers to the quantitative assessment of the changes in the productivity.
Profile measurement and analysis: The profile measurement and analysis refers to the computation of a set of operational partial productivity measures and their comparison to the corresponding set of base period, for the assessment of the nature of changes in productivity.
Compute the productivity profile for 2014:
Compute the Material Productivity Profile for 2014:
Compute the Labor Productivity Profile for 2014:
The Material Productivity Profile is 1.67 and Labor Productivity Profile is 0.83.
1 b.
Ascertain the productivity profile for 2015 for the proposed process changes.
1 b.

Explanation of Solution
Compute the productivity profile for 2015 Change 1:
Compute the Material Productivity Profile for 2015 Change 1:
Compute the Labor Productivity Profile for 2015 Change 1:
The Material Productivity Profile is 1.43 and Labor Productivity Profile is 1.25.
Compute the productivity profile for 2015 Change 2:
Compute the Material Productivity Profile for 2015 Change 2:
Compute the Labor Productivity Profile for 2015 Change 2:
The Material Productivity Profile is 2.00 and Labor Productivity Profile is 1.00.
There is an overall improvement in the output input ratio from 2014 to 2015.
1 c.
Ascertain the productivity profile for optimal input combination and recommend the most productive profile.
1 c.

Explanation of Solution
Compute the productivity profile for optimal input combination:
Compute the Material Productivity Profile for optimal input combination:
Compute the Labor Productivity Profile for optimal input combination:
The Material Productivity Profile is 2.50 and Labor Productivity Profile is 1.25.
There is an overall improvement in the output input ratio from 2014 to 2015. The change 1 in 2015 has the optimum labor productivity, however the material productivity is very low. In the Change 2 of 2015, both material and labor productivity are good. Now for the decision regarding the implementation of the productivity profile, this depends on the productivity trade-offs of the inputs.
2.
Ascertain the productive inefficiency among the given combinations and compare the improvement along with the changes in the technical and
2.

Explanation of Solution
Total productive efficiency: The total productive efficiency refers to the point where the maximum technical and allocative efficiency is achieved. This is the point where the production of a new product may compromise the production of another product, as the optimum quantity of inputs is being used to get the desired output.
The technical efficiency ensures no more units of input than the required number is used for any mix of inputs.
The allocative efficiency ensures the use of an inexpensive and most technically efficient mix.
Compute the total cost of productive efficiency:
Particulars | Number of Units (A) | Cost per Unit (B) | |
2014 | |||
Cost of materials | 33,000 | $ 60 | $ 1,980,000 |
Cost of labor | 66,000 | $ 15 | $ 990,000 |
Total Cost | $ 2,970,000 | ||
2015 Change 1 | |||
Cost of materials | 38,500 | $ 60 | $ 2,310,000 |
Cost of labor | 44,000 | $ 15 | $ 660,000 |
Total Cost | $ 2,970,000 | ||
2015 Change 2 | |||
Cost of materials | 27,500 | $ 60 | $ 1,650,000 |
Cost of labor | 55,000 | $ 15 | $ 825,000 |
Total Cost | $ 2,475,000 | ||
Optimal Input | |||
Cost of materials | 22,000 | $ 60 | $ 1,320,000 |
Cost of labor | 44,000 | $ 15 | $ 660,000 |
Total Cost | $ 1,980,000 |
Table (1)
Compute the total cost of productive inefficiency:
Compute the cost of productive inefficiency for 2014:
Compute the cost of productive inefficiency for 2015 Change 1:
Compute the cost of productive inefficiency for 2015 Change 2:
Compute the potential improvement:
Compute the potential improvement for 2015 Change 1:
Compute the potential improvement for 2015 Change 2:
The Change 1 has greater technical efficiency but the allocative efficiency is reduced, on the other hand Change 2 is able to attain both technical and allocative efficiency.
3.
Compute and describe the price recovery component.
3.

Explanation of Solution
Profit-linked productivity measurement and analysis: The profit-linked productivity measurement and analysis is the ascertainment of the amount of change in profit, from the base period to the current period, due to the various changes in the productivity.
Compute the profit-linked productivity measurement:
Compute the profit-linked productivity measurement for 2015 Change 1:
Compute the profit-linked productivity measurement for 2015 Change 2:
The profit-linked productivity measurement takes into consideration only the changes in the input with no regards to the base or optimal combination.
Want to see more full solutions like this?
Chapter 15 Solutions
EBK CORNERSTONES OF COST MANAGEMENT
- A process control manager is considering two robots to improve materials-handling capacity in the production of rigid shaft couplings that make dissimilar drive components. Robot X has a first cost of $92,000, an annual M&O cost of $31,000, and $40,000 salvage value, and it will improve revenues by $96,000 per year. Robot Y has a first cost of $146,000, an annual M&O cost of $28,000, and $47,000 salvage value, and it will increase revenues by $124,000 per year. The company's MARR is 37% per year, and it uses a 3-year study period for economic evaluations. Calculate the incremental ROR, and identify the robot the manager should select. The incremental ROR is %. The manager should select robot: (Click to select) (Click to select) Yarrow_forwardBooster Company has been researching into new ways of manufacturing their products. The costs and results of a recent project are as follows: Period 2010 2011 January to June 2011 July to December 2012 Costs P 6,000,000 9,000,000 14,000,000 nil Description General research Development stage 1 Development stage 2 New process adopted in the factory Development began in January 2011, but it was only in July 2011 that it became apparent that the process would be successful and that it would save the company a lot of money. The new process will probably be used for ten years from January 2012, saving about P4,000,000 per annum. The process is protected by patent for seven years, after which time most of Booster’s rivals will adopt the process. What is the carrying value of the development expenditure on December 31, 2012? a. P 23,000,000 b. P 29,000,000 c. P 9,000,000 d. P 14,000,000 need asap thanksarrow_forwardA large electronics manufacturer is considering outsourcing the manufacturing of a diaphragm used in its large speaker. The company estimates that annual fixed costs of manufacturing the part in-house, which include equipment, maintenance, and management, amounts to$6.9million. The variable costs of labor and material are$7per unit. The company has an offer from a major subcontractor to produce the part for \$12 per unit. However, the subcontractor wants the company to share in the costs of the equipment. The electronics company estimates that the total cost would be$3.4million, which also includes management oversight for the new supply contact. The company must consume more than diaphragms to make the manufacturing the part in-house option least costly. (Enter your response rounded up to the nearest whole number.).arrow_forward
- COLORADO INC. is a chemical manufacturer that supplies various products to industrial users. The company plans to introduce a new chemical solution, called Nysap, for which it needs to develop a standard product cost. The following information is available on the production of Nysap: Nysap is made by combining a chemical compound (nyclyn) and a solution (salex), and boiling the mixture. A 20% loss in volume occurs for both the salex and the nyclyn during boiling. After boiling, the mixture consists of 9.6 liters of salex and 12 kilograms of nyclyn per 10-liter batch of Nysap. After the boiling process is complete, the solution is cooled slightly before 5 kilograms of protet are added per 10-liter batch of Nysap. The addition of the protet does not affect the total liquid volume. The resulting solution is then bottled in 10-liter containers. The finished product is highly unstable, and one10-liter batch out of six is rejected at final inspection. Rejected batches have no commercial…arrow_forwardMSI is considering outsourcing the production of the handheld control module used with some of its products. The company has received a bid from Monte Legend Company (MLC) to produce 10,000 units of the module per year for $16 each. The following information pertains to MSI’s production of the control modules: Direct materials $ 9 Direct labor 4 Variable manufacturing overhead 2 Fixed manufacturing overhead 3 Total cost per unit $ 18 MSI has determined it could eliminate all variable costs if the control modules were produced externally, but none of the fixed overhead is avoidable. At this time, MSI has no specific use in mind for the space that is currently dedicated to the control module production. Required: 1. Compute the difference in cost between making and buying the control module. 2. Should MSI buy the modules from MLC or continue to make them? 3-a. Suppose the MSI space currently used for the modules could be utilized by a new product line that would generate…arrow_forwardAlderon Enterprises is evaluating a special order it has received for a ceramic fixture to be used in aircraft engines. Alderon has recently been operating at less than full capacity, so the firm's management will accept the order if the price offered exceeds the costs that will be incurred in producing it. You have been asked for advice on how to determine the cost of two raw materials that would be required to produce the order. A) The special order will require 800 gallons of Endor, a highly perishable material that is purchased as needed. Alderon currently has 1,200 gallons of Endor on hand, since the material is used in virtually all of the company's products. The last time endor was purchased, Alderon paid $5.00 per gallon. However, the average price paid for the endor in stock was only $4.75. The market price for the Endor is quite volatile, with the current price at $5.50. If the special order is accepted, Alderon will have to place a new order next week to replace the…arrow_forward
- A company is analyzing a make-versus-purchase situation for a component used in several products, and the engineering department has developed these data:Option A: Purchase 10,000 items per year at a fixed price of $8.50 per item. The cost of placing the order is negligible according to the present cost accounting procedure. Option B: Manufacture 10,000 items per year, using available capacity in the factory. Cost estimates are direct materials = $5.00 per item and direct labor = $1.50 per item. Manufacturing overhead is $3.00 per item. Based on these data, should the item be purchased or manufactured?arrow_forwardHudson Corporation is considering three options for managing its data warehouse: continuing with its own staff, hiring an outside vendor to do the managing, or using a combination of its own staff and an outside vendor. The cost of the operation depends on future demand. The annual cost of each option (in thousands of dollars) depends on demand as follows: If the demand probabilities are 0.2, 0.5, and 0.3, which decision alternative will minimize the expected cost of the data warehouse? What is the expected annual cost associated with that recommendation? Construct a risk profile for the optimal decision in part (a). What is the probability of the cost exceeding $700,000?arrow_forwardCleanTech manufactures equipment to mitigate the environmental effects of waste. (a) If Product A has fixed expenses of $15,000 per year and each unit of product has a $0.20 variable cost, and Product B has fixed expenses of $5000 per year and a $0.50 variable cost, at what number of units of annual production will A have the same overall cost as B? (b) As a manager at CleanTech what other data would you need to evaluate these two products?arrow_forward
- Crane Company has decided to introduce a new product. The new product can be manufactured by either a capital-intensive method or a labor-intensive method. The manufacturing method will not affect the quality of the product. The estimated manufacturing costs by the two methods are as follows. Direct materials Direct labor Variable overhead Fixed manufacturing costs (a) Crane' market research department has recommended an introductory unit sales price of $40.00. The selling expenses are estimated to be $622,000 annually plus $2.00 for each unit sold, regardless of manufacturing method. (b) Capital-Intensive $6.00 per unit $7.00 per unit $4.00 per unit Your answer is correct. $3,200,000 Calculate the estimated break-even point in annual unit sales of the new product if Crane Company uses the: 1. Capital-intensive manufacturing method. 2. Labor-intensive manufacturing method. Break-even point in units eTextbook and Media Labor-Intensive $7.00 per unit $10.00 per unit $5.50 per unit…arrow_forwardLakeside Incorporated produces a product that currently sells for $40 per unit. Current production costs per unit include direct materials, $11; direct labor, $13; variable overhead, $6; and fixed overhead, $6. Product engineering has determined that certain production changes could refine the product quality and functionality. These new production changes would increase material and labor costs by 20% per unit. Required: a. What would be the incremental profit or loss if Lakeside could sell the refined version of its product for $44 per unit? Note: Do not round your intermediate calculations. Round your final answer to 2 decimal places. Loss amounts should be indicated with a minus sign.arrow_forwardA process control manager is considering two robots to improve materials handling capacity in the production of rigid shaft couplings that mate dissimilar drive components. Robot X has a first cost of $84,000, an annual M&O cost of $31,000, a $40,000 salvage value, and will improve revenues by $96,000 per year. Robot Y has a first cost of $146,000, an annual M&O cost of $28,000, a $47,000 salvage value, and will increase revenues by $119,000 per year. The company’s MARR is 15% per year and it uses a 3-year study period for economic evaluations. Which one should the manager select (a) on the basis of ROR values, and (b) on the basis of the incremental ROR value? (c) Which is the correct selection basis? Perform the analysis by hand or spreadsheet, as instructed.arrow_forward
- Cornerstones of Cost Management (Cornerstones Ser...AccountingISBN:9781305970663Author:Don R. Hansen, Maryanne M. MowenPublisher:Cengage LearningEssentials of Business Analytics (MindTap Course ...StatisticsISBN:9781305627734Author:Jeffrey D. Camm, James J. Cochran, Michael J. Fry, Jeffrey W. Ohlmann, David R. AndersonPublisher:Cengage LearningManagerial AccountingAccountingISBN:9781337912020Author:Carl Warren, Ph.d. Cma William B. TaylerPublisher:South-Western College Pub
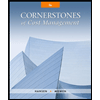
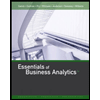
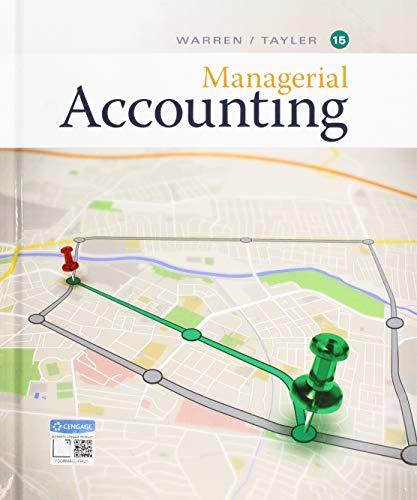