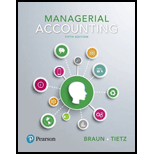
Sustainability and budgeting (Learning Objective 1)
Liller Beverages manufactures its own soda pop bottles. The bottles are made from polyethylene terephthalate (PET), a lightweight yet strong plastic. The company uses as much PET recycled resin pellets in its bottles as it can, both because using recycled PET helps the company to meet its sustainability goals and because recycled PET is less expensive than virgin PET.
Liller is continuing to search for ways to reduce its costs and its impact on the environment. PET plastic is melted and blown over soda bottle molds to produce the bottles. One idea Liller’s engineers have suggested is to retrofit the soda bottle molds and change the plastic formulation slightly so that 25% less PET plastic is used for each bottle. The average kilograms of PET per soda bottle before any redesign is 0.004 kg. The cost of retrofitting the soda bottle molds will result in a one-time charge of $35,947, while the plastic reformulation will cause the average cost per kilogram of PET plastic to change from $4.00 to $4.30.
Liller’s management is analyzing whether the change to the bottle molds to reduce PET plastic usage should be made. Management expects the following number of soda bottles to be used in the upcoming year:
For the upcoming year, management expects the beginning inventory of PET to be 1,280 kilograms, while ending inventory is expected to be 1,690 kilograms. During the first three quarters of the year, management wants to keep the ending inventory of PET a1 the end of each quarter equal to 10% of the following quarter’s PET needs.
Requirements
- 1. Using the original data (before any redesign of soda bottles), prepare a direct materials budget to calculate the cost of PET purchases in each quarter for the upcoming year and for the year in total.
- 2. Assume that the company retrofits the soda bottle molds and changes the plastic formulation slightly so that less PET plastic is used in each bottle. Now prepare a direct materials budget to calculate the cost of PET purchases in each quarter for the upcoming year and for the year in total for this possible scenario.
- 3. Compare the cost of PET plastic for Requirement 1 (original data) and for Requirement 2 (making change to using less PET). What is the direct material cost savings from making the change to using less PET? Compare the total of those savings to the cost of retrofitting the soda bottle molds. Should the company make the change? Explain your rationale.

Want to see the full answer?
Check out a sample textbook solution
Chapter 15 Solutions
Managerial Accounting (5th Edition)
- Please give answer step by steparrow_forwardWhat role should the precautionary principle play in the development and application of accounting standards? Discuss the potential tensions that may arise between the need for financial transparency and the desire to mitigate against excessive risk-taking or overly optimistic reporting.arrow_forwardThe Tin company uses the straight-line method to depreciate its equipment. On May 1, 2018, the company purchased some equipment for $200,000. The equipment is estimated to have a useful life of ten years and a salvage value of $20,000. How much depreciation expense should Tin record for the equipment in the adjusting entry on December 31, 2018?arrow_forward
- Kindly help me with accounting questionsarrow_forwardPlease given answer general Accountingarrow_forwardQuestions:-General Account - On March 1, 2019, Alpha Company's beginning work-in-process inventory had 8,000 units. This is its only production department. Beginning WIP units were 50% completed to conversion costs. Alpha introduces direct materials at the beginning of the production process. During March, a total of 15,000 units were started and a total of 20,000 units were completed. Alpha's ending WIP inventory had 3,000 units which were 70% completed to conversion costs. Alpha uses the weighted average method. Use this information to determine for March 2019 the equivalent units of production for conversion costsarrow_forward
- Managerial Accounting: The Cornerstone of Busines...AccountingISBN:9781337115773Author:Maryanne M. Mowen, Don R. Hansen, Dan L. HeitgerPublisher:Cengage LearningManagerial AccountingAccountingISBN:9781337912020Author:Carl Warren, Ph.d. Cma William B. TaylerPublisher:South-Western College Pub
- Financial And Managerial AccountingAccountingISBN:9781337902663Author:WARREN, Carl S.Publisher:Cengage Learning,Cornerstones of Cost Management (Cornerstones Ser...AccountingISBN:9781305970663Author:Don R. Hansen, Maryanne M. MowenPublisher:Cengage LearningPrinciples of Accounting Volume 2AccountingISBN:9781947172609Author:OpenStaxPublisher:OpenStax College
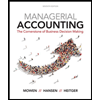
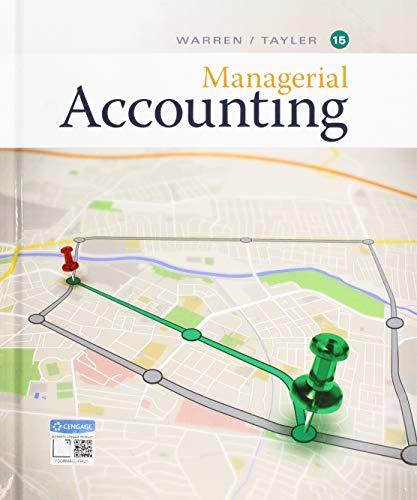
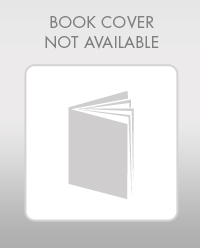
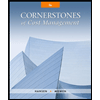