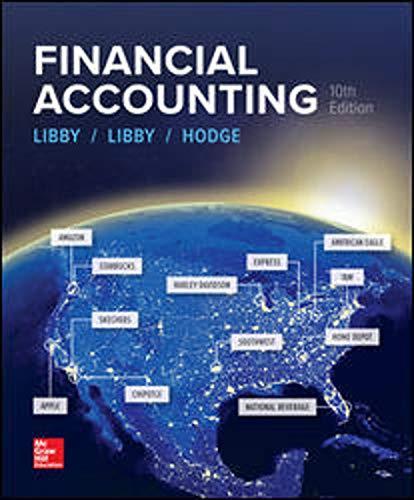
FINANCIAL ACCOUNTING
10th Edition
ISBN: 9781259964947
Author: Libby
Publisher: MCG
expand_more
expand_more
format_list_bulleted
Question
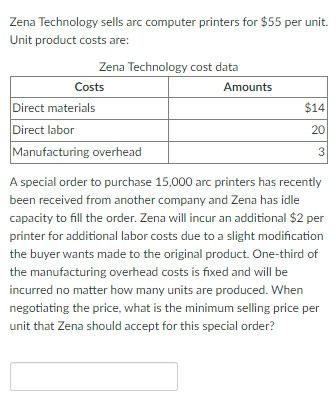
Transcribed Image Text:Zena Technology sells arc computer printers for $55 per unit. Unit product costs are:
**Zena Technology cost data**
| Costs | Amounts |
|---------------------------|---------|
| Direct materials | $14 |
| Direct labor | $20 |
| Manufacturing overhead | $3 |
A special order to purchase 15,000 arc printers has recently been received from another company, and Zena has idle capacity to fill the order. Zena will incur an additional $2 per printer for additional labor costs due to a slight modification the buyer wants made to the original product. One-third of the manufacturing overhead cost is fixed and will be incurred no matter how many units are produced. When negotiating the price, what is the minimum selling price per unit that Zena should accept for this special order?
Expert Solution

This question has been solved!
Explore an expertly crafted, step-by-step solution for a thorough understanding of key concepts.
This is a popular solution
Trending nowThis is a popular solution!
Step by stepSolved in 2 steps

Knowledge Booster
Similar questions
- Cypress Inc. manufactures wooden canoes. Cypress normally sells the canoes for $2,700 per unit. A major distributor has offered to buy 1,000 units at a reduced price. At its budgeted annual production level of 18,000 units, Cypress' per-unit manufacturing costs are as follows: Direct materials Direct labor Variable manufacturing overhead Fixed manufacturing overhead $950 $200 $330 $450 Cypress would have to produce the special order on an overtime shift, which would increase the direct labor costs to $300 per unit. The special order would not impact Cypress' fixed costs. However, if Cypress accepts the special order, it will also incur $60,000 in additional, one-time costs in connection with the order. What is the minimum per-unit selling price that Cypress must charge to break even on the special order? Round to the nearest whole dollar and do not enter a dollar sign or a decimal point (e.g., enter 89, not $89.00).arrow_forwardScootz could sell its scooters to retailers either assembled or unassembled. The cost of an unassembled scooters is as follows. Direct materials $150 Direct labor 70 Variable overhead (0.70 of direct labor) 49 Fixed overhead (0.30 of direct labor) 21 Manufacturing cost per unit $290 The unassembled scooters are sold to retailers at $450 each. Scootz currently has unused productive capacity that is expected to continue indefinitely; management has concluded that some of this capacity can be used to assemble the scooters and sell them at $495 each. Assembling the scooters will increase direct materials by $5 per scooter, and direct labor by $10 per scooter. Additional variable overhead will be incurred at the normal rates, but there will be no additional fixed overhead as a result of assembling the scooters. You are required to: (a) Prepare an incremental analysis for the sell-or-process-further decision. (b) Should Speedy sell unassembled or process further?arrow_forwardCarver Company manufactures a component used in the production of one of its main products. The following cost information is available: Direct materials $420 Direct labor (variable) 110 Variable manufacturing overhead Fixed manufacturing overhead 90 30 A supplier has offered to sell the component to Carver for $650 per unit. If Carver buys the component from the supplier, the released facilities can be used to manufacture a product that would generate a contribution margin of $20,000 annually. Assuming that Carver needs 3,000 components annually and that the fixed manufacturing overhead is unavoidable, what would be the impact on operating income if Carver outsources? A. Operating income would decrease by $70,000. B. Operating income would increase by $20,000. C. Operating income would decrease by $20,000. O D. Operating income would increase by $90,000.arrow_forward
- Wings Incorporated manufactures machine parts for aircraft engines. The CEO, Chucky Valters, was considering an offer from a subcontractor that would provide 2,400 units of product PQ107 for Valters for a price of $150,000. If Wings does not purchase these parts from the subcontractor it must produce them in-house with the following unit costs: Direct materials Direct labor Variable overhead Cost per Unit $31 19 8 In addition to the above costs, if Wings produces part PQ107, it would have a retooling and design cost of $9,800. The relevant costs of producing 2,400 units of product PQ107 internally are:arrow_forwardChip Jones ahoy manufactures the cloth for sails. The company has the capacity to produce 36,000 sails per year and is currently producing and selling 25,000 sails per year. The following information relates to current production: $175 Sales price per unit Variable costs per unit: Manufacturing Selling and administrative Total fixed costs: Manufacturing Selling and administrative LEFE $62 $20 $700,000 $250,000 Assume that a special pricing order is accepted for 5600 sails at a sales price of $150 per unit. This special order requires both variable manufacturing and variable selling and administrative costs, as well as incremental fixed costs of $400,000. What will be the impact on operating income? Operating income decreases by $380,800.arrow_forwardNikularrow_forward
- Bramble Company manufactures widgets. Blossom Company has approached Bramble with a proposal to sell the company widgets at a price of $60500 for 100,000 units. Bramble is currently making these components in its own factory. The following costs are associated with this part of the process when 100,000 units are produced: Direct material $22700 Direct labour 23000 Manufacturing overhead 29000 Total $74700 The manufacturing overhead consists of $12300 of costs that will be eliminated if the components are no longer produced by Bramble. From Bramble’s point of view, how much is the incremental cost or savings if the widgets are bought instead of made? $14200 incremental savings $2500 incremental savings $2500 incremental cost $14200 incremental costarrow_forwardEvery year Marigold Industries manufactures 6,100 units of part 231 for use in its production cycle. The per unit costs of part 231 are as follows: Direct materials Direct labor Variable manufacturing overhead Fixed manufacturing overhead Total (a) Total relevant cost to make $ $4.00 Net relevant cost to buy 10.00 Carla Vista, Inc., has offered to sell 6,100 units of part 231 to Marigold for $34 per unit. If Marigold accepts Carla Vista's offer, its freed-up facilities could be used to earn $10,700 in contribution margin by manufacturing part 240. In addition, Marigold would eliminate 40% of the fixed overhead applied to part 231. $ 6.00 10.00 Calculate total relevant cost to make and net cost to buy. $30.00arrow_forwardBeta makes a component used in its engine. Monthly production costs for 1,000 component units are as follows: Direct materials $46,000 Direct labor 11,500 Variable overhead costs 34,500 Fixed overhead costs 23,000 Total costs $115,000 It is estimated that 8% of the fixed overhead costs will no longer be incurred if the company purchases the component from an outside supplier. Beta has the option of purchasing the component from an outside supplier at $97.75 per unit. 22) If Beta accepts the offer from the outside supplier, the monthly avoidable costs (costs that will no longer be incurred) total 23) If Beta purchases 1,000 units from the outside supplier per month, then what would be the change in operating income?arrow_forward
- Harvey Automobiles uses a standard part in the manufacture of several of its trucks. The cost of producing 40,000 parts is $130,000, which includes fixed costs of $90,000 and variable costs of $40,000. The company can buy the part from an outside supplier for $3.30 per unit, and avoid 30% of the fixed costs. Assume that factory space freed up by purchasing the part from an outside source can be used to manufacture another product that can be sold for $179,000 profit. If Harvey Automobiles makes the part, what will its operating income be? $179,000 greater than if the company bought the part $49,000 greater than if the company bought the part $49,000 less than if the company bought the part $79,000 greater than if the company bought the partarrow_forwardRoadside Inc. manufactures the Megalite, and is reviewing the product's cost structure. Accounting records show these costs:factory space: $250,000 per yearinsurance: $47,000 per yearsupervisor salaries: $125,000 per yearmaterials: $5.00 per lampdirect labor: $2.69 per lamprecycling charge: $0.37 per lampRoadside Inc sells the Megalite to wholesalers for $13.69 each. Calculate Roadside's contribution margin as percent of selling price on the Megalite. (Rounding: tenth of a percent. Report 25.3%, for example, as "25.3".)arrow_forwardMainstay Auto uses a standard part in the manufacture of several of its trucks. The cost of producing 40,000 parts is $120,000, which includes fixed costs of $60,000 and variable costs of $60,000. The company can buy the part from an outside supplier for $3.00 per unit, and avoid 30% of the fixed costs. Assume that factory space freed up by purchasing the part from an outside source can be used to manufacture another product that can be sold for $12,000 profit. If Mainstay Auto makes the part, what will its operating income be? Select one: a. $150,000 greater than if the company bought the part b. $30,000 greater than if the company bought the part c. $30,000 less than if the company bought the part d. $54,000 greater than if the company bought the part e. $54,000 less than if the company bought the partarrow_forward
arrow_back_ios
SEE MORE QUESTIONS
arrow_forward_ios
Recommended textbooks for you
- AccountingAccountingISBN:9781337272094Author:WARREN, Carl S., Reeve, James M., Duchac, Jonathan E.Publisher:Cengage Learning,Accounting Information SystemsAccountingISBN:9781337619202Author:Hall, James A.Publisher:Cengage Learning,
- Horngren's Cost Accounting: A Managerial Emphasis...AccountingISBN:9780134475585Author:Srikant M. Datar, Madhav V. RajanPublisher:PEARSONIntermediate AccountingAccountingISBN:9781259722660Author:J. David Spiceland, Mark W. Nelson, Wayne M ThomasPublisher:McGraw-Hill EducationFinancial and Managerial AccountingAccountingISBN:9781259726705Author:John J Wild, Ken W. Shaw, Barbara Chiappetta Fundamental Accounting PrinciplesPublisher:McGraw-Hill Education
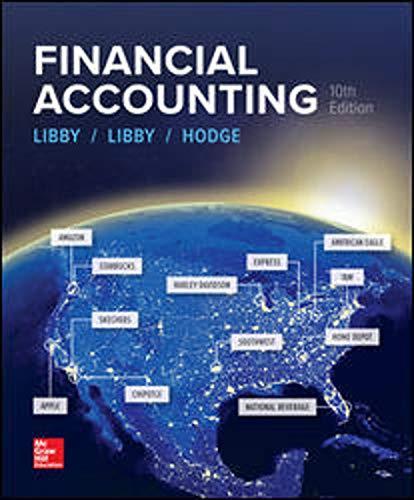
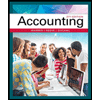
Accounting
Accounting
ISBN:9781337272094
Author:WARREN, Carl S., Reeve, James M., Duchac, Jonathan E.
Publisher:Cengage Learning,
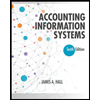
Accounting Information Systems
Accounting
ISBN:9781337619202
Author:Hall, James A.
Publisher:Cengage Learning,
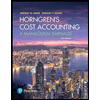
Horngren's Cost Accounting: A Managerial Emphasis...
Accounting
ISBN:9780134475585
Author:Srikant M. Datar, Madhav V. Rajan
Publisher:PEARSON
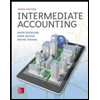
Intermediate Accounting
Accounting
ISBN:9781259722660
Author:J. David Spiceland, Mark W. Nelson, Wayne M Thomas
Publisher:McGraw-Hill Education
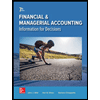
Financial and Managerial Accounting
Accounting
ISBN:9781259726705
Author:John J Wild, Ken W. Shaw, Barbara Chiappetta Fundamental Accounting Principles
Publisher:McGraw-Hill Education