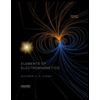
Concept explainers
Your factory produces cryogenic refrigerators, and your task is to design a control system for the fridge, but, using the same sensor, you must also supply the end-user with temperature monitoring. The cryogenic freezer is controlled in a tight band around minus 85°C, therefore in controlling the fridge you need to have the most accurate information available regarding the operating range of the fridge (nominally at -85°C, but it can be colder and it can defrost if faulty and reach a maximum ambient temperature of say 50°C to be safe).
Due to the economy of RTD sensors, it is decided by management to use a PT100 RTD sensor (range -400°F to 1200°F) with a smart transmitter which needs to be set up correctly to a 4-20mA input on the PLC controlling the fridge. Taking the above conditions into account, the measuring range should be -100°C to 50°C (which should cater for the worst ambient temperature).
a) Make sure the RTD is the correct choice b) Set the smart transmitter up correctly (type, offset and span) c) Find the straight-line equation (in the form y = ax+b, where y in mA, and x in °C) for the temperature in °C to mA output of the smart transmitter d) Test your equation at the extremes (-85°C to 50°C) |

Step by stepSolved in 4 steps with 2 images

- The figure below shows a schematic of a dual-duct system For design purposes, suppose the zones shown are two of five zones, each having identical operating design conditions. The only exhaust is the main system exhaust. The zones are to held at 75 °F db / 50% RH when the total heat gain of each one is 200,000 BTUH and the sensible heat ratio is 0.6. Outside air (OA) is 95 °F db / 40% RH and the system is designed to operate with a mass flow rate of dry air that contains 25% OA & 75% RA (return air). The hot deck provides sensible heating only, and the air exits the heating coil at 105 °F db. The cold deck is designed such that air exits the cooling coil at 50 °F db / 90 % RH. Take the pressure to be one standard atmosphere. a. Accurately sketch and label the state points on an electronic psych chart (in particular make sure that the coil is represented as a collie on the TRANE pscyh chart software you can input a coil process) b. Compute the mass flow rate (lbma/hr) through…arrow_forwardAn induction machine, inverter, and control were implemented experimentally to validate the model shown in Fig. 3. To protect the experimental setup without significantly affecting the model, two factors were considered. The first factor is to avoid injecting faults that could cause severe failures or trigger the protection circuitry as predicted from simulations. The second factor is to use a tight external closed-loop torque control in experiments to avoid sudden overload conditions on the dynamometer and the motor shaft. Design a fault tree analysis (FTA) for induction motor failure in Fig. 3 if the rotational speed of the rotor failed to be controlled. fan cover cooling end fan bell wiring box lifting eye cast-iron frame nameplate stator coils squirrel- cage rotor Fig. 3 bearing seal ball bearing 0arrow_forwardHow do motion-sensing input devices like accelerometers and gyroscopes work, and where are they commonly used?arrow_forward
- Elements Of ElectromagneticsMechanical EngineeringISBN:9780190698614Author:Sadiku, Matthew N. O.Publisher:Oxford University PressMechanics of Materials (10th Edition)Mechanical EngineeringISBN:9780134319650Author:Russell C. HibbelerPublisher:PEARSONThermodynamics: An Engineering ApproachMechanical EngineeringISBN:9781259822674Author:Yunus A. Cengel Dr., Michael A. BolesPublisher:McGraw-Hill Education
- Control Systems EngineeringMechanical EngineeringISBN:9781118170519Author:Norman S. NisePublisher:WILEYMechanics of Materials (MindTap Course List)Mechanical EngineeringISBN:9781337093347Author:Barry J. Goodno, James M. GerePublisher:Cengage LearningEngineering Mechanics: StaticsMechanical EngineeringISBN:9781118807330Author:James L. Meriam, L. G. Kraige, J. N. BoltonPublisher:WILEY
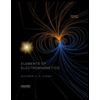
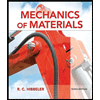
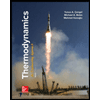
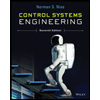
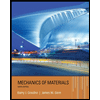
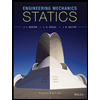