Yacama Shades supplies sun-blocking shades to home remodeling supply stores such as Home Depot and Lowes as well as discounters such as Walmart. The CFO is worried about inflation and the effect on Yacama Shades' financial results. The variable production costs are $150, and fixed costs amount to $2 million. Production engineers have advised management that they expect unit labor costs to rise by 20 percent and unit materials costs to rise by 15 percent in the coming year. Of the $150 variable costs, 50 percent are from labor and 20 percent are from materials. Variable
Presently, the company sells 33,000 units for $400 per unit.
The company wishes to maintain the same level of profit in real dollar terms. It is expected that to accomplish this objective, profits must increase by 10 percent during the year.
Required:
- Compute the volume in units and the dollar sales level necessary to maintain the present profit level, assuming that the maximum price increase is implemented.
- Compute the volume of sales and the dollar sales level necessary to provide the 10 percent increase in profits, assuming that the maximum price increase is implemented.
- If the volume of sales were to remain at 33,000 units, calculate the new price that would be required to attain the 10 percent increase in profits.
A) Volume In Units?
A) Sales?
B) Volume In Units?
B) Sales?
C)If the volume of sales were to remain at 33,000 units, calculate the new price that would be required to attain the 10 percent increase in profits.
New Price?

Step by stepSolved in 2 steps

- Artisan Metalworks has a bottleneck in their production that occurs within the engraving department. Jamal Moore, the COO, is considering hiring an extra worker, whose salary will be $55,000 per year, to solve the problem. With this extra worker, the company could produce and sell 3,000 more units per year. Currently, the selling price per unit is $25 and the cost per unit is $7.85. Using the information provided, calculate the annual financial impact of hiring the extra worker.arrow_forwardVariety Artisans has a bottleneck in their production that occurs within the engraving department. Arjun Naipul, the COO, is considering hiring an extra worker, whose salary will be $45,000 per year, to solve the problem. With this extra worker, the company could produce and sell 3,500 more units per year. Currently, the selling price per unit is $18 and the cost per unit is $5.85. Using the information provided, calculate the annual financial impact of hiring the extra worker.arrow_forwardKimball Company has developed the following cost formulas: Materialusage:Ym=80X;r=0.95Laborusage(direct):Yl=20X;r=0.96Overheadactivity:Yo=350,000+100X;r=0.75Sellingactivity:Ys=50,000+10X;r=0.93 where X=Directlaborhours The company has a policy of producing on demand and keeps very little, if any, finished goods inventory (thus, units produced equals units sold). Each unit uses one direct labor hour for production. The president of Kimball Company has recently implemented a policy that any special orders will be accepted if they cover the costs that the orders cause. This policy was implemented because Kimballs industry is in a recession and the company is producing well below capacity (and expects to continue doing so for the coming year). The president is willing to accept orders that minimally cover their variable costs so that the company can keep its employees and avoid layoffs. Also, any orders above variable costs will increase overall profitability of the company. Required: 1. Compute the total unit variable cost. Suppose that Kimball has an opportunity to accept an order for 20,000 units at 220 per unit. Should Kimball accept the order? (The order would not displace any of Kimballs regular orders.) 2. Explain the significance of the coefficient of correlation measures for the cost formulas. Did these measures have a bearing on your answer in Requirement 1? Should they have a bearing? Why or why not? 3. Suppose that a multiple regression equation is developed for overhead costs: Y = 100,000 + 100X1 + 5,000X2 + 300X3, where X1 = direct labor hours, X2 = number of setups, and X3 = engineering hours. The coefficient of determination for the equation is 0.94. Assume that the order of 20,000 units requires 12 setups and 600 engineering hours. Given this new information, should the company accept the special order referred to in Requirement 1? Is there any other information about cost behavior that you would like to have? Explain.arrow_forward
- Yacama Shades supplies sun-blocking shades to home remodeling supply stores such as Home Depot and Lowes as well as discounters such as Walmart. The CFO is worried about Inflation and the effect on Yacama Shades financial results. The variable production costs are $150, and fixed costs amount to $2 million. Production engineers have advised management that they expect unit labor costs to rise by 10 percent and unit materials costs to rise by 25 percent in the coming year. Of the $150 variable costs, 50 percent are from labor and 20 percent are from materials. Variable overhead costs are expected to Increase by 20 percent. Sales prices cannot Increase more than 6 percent. It is also expected that fixed costs will rise by 13.0 percent as a result of Increased taxes and other miscellaneous fixed charges. Presently, the company sells 30,000 units for $400 per unit. The company wishes to maintain the same level of profit in real dollar terms. It is expected that to accomplish this…arrow_forwardScholes Systems supplies a particular type of office chair to large retailers such as Target, Costco, and Office Max. Scholes is concerned about the possible effects of inflation on its operations. Presently, the company sells 81,000 units for $65 per unit. The variable production costs are $35, and fixed costs amount to $1,410,000. Production engineers have advised management that they expect unit labor costs to rise by 15 percent and unit materials costs to rise by 10 percent in the coming year. Of the $35 variable costs, 40 percent are from labor and 20 percent are from materials. Variable overhead costs are expected to increase by 20 percent. Sales prices cannot increase more than 10 percent. It is also expected that fixed costs will rise by 5 percent as a result of increased taxes and other miscellaneous fixed charges. The company wishes to maintain the same level of profit in real dollar terms. It is expected that to accomplish this objective, profits must increase by 7 percent…arrow_forwardScholes Systems supplies a particular type of office chair to large retailer such as Target, Costco, and Office Max. Scholes is concerned about the possible effects of inflation on its operations. Presently, the company sells 85,000 units for $80 per unit. The variable production costs are $50, and fixed costs amount to $1,450,000. Production engineers have advised management that they expect unit labor costs to rise by 20 prevent and unit materials costs to rise by 10 percent in the coming year. Of the $50 variable costs, 45 percent are from labor and 25 percent are from materials. Variable overhead costs are expected to increase 25 percent. Sales prices cannot increase more than 10 percent. It is also expected that fixed costs will rise by 6 percent as a result of increased taxes and other miscellaneous fixed charges. The company wishes to maintain the same level of profit in real dollar terms. It is expected that to accomplish this objective, profits must increase by 7 percent…arrow_forward
- HH Co. uses corrugated cardboard to ship its product to customers. Currently, the company’s returns department incurs annual overhead costs of $72,000 and forecasts 2,000 returns per year. Management believes it has found a better way to package its products. As a result, the company expects to reduce the number of shipments that are returned due to damage by 5%. In addition, the initiative is expected to reduce the department’s annual overhead by $12,000. Compute the returns department’s standard overhead rate per return (a) before the sustainability improvement and (b) after the sustainability improvement. Round to the nearest cent.arrow_forwardHH Co. uses corrugated cardboard to ship its product to customers. Currently, the company’s returns department incurs annual overhead costs of $126,000 and forecasts 6,000 returns per year. Management believes it has found a better way to package its products. As a result, the company expects to reduce the number of shipments that are returned due to damage by 3%. In addition, the initiative is expected to reduce the department’s annual overhead by $14,000.Compute the returns department’s standard overhead rate per return (a) before the sustainability improvement and (b) after the sustainability improvement.arrow_forwardThe Knot manufactures men’s neckwear at its Spartanburg plant. The Knot is considering implementing a JIT production system. The following are the estimated costs and benefits of JIT production: a. Annual additional tooling costs $250,000 annually. b. Average inventory would decline by 80% from the current level of $1,000,000. c. Insurance, space, materials-handling, and setup costs, which currently total $400,000 annually, would decline by 20%. d. The emphasis on quality inherent in JIT production would reduce rework costs by 25%. The Knot currently incurs $160,000 in annual rework costs. e. Improved product quality under JIT production would enable The Knot to raise the price of its product by $2 per unit. The Knot sells 100,000 units each year. The Knot’s required rate of return on inventory investment is 15% per year. Q. What nonfinancial and qualitative factors should The Knot consider when making the decision to adopt JIT production?arrow_forward
- The Knot manufactures men’s neckwear at its Spartanburg plant. The Knot is considering implementing a JIT production system. The following are the estimated costs and benefits of JIT production: a. Annual additional tooling costs $250,000 annually. b. Average inventory would decline by 80% from the current level of $1,000,000. c. Insurance, space, materials-handling, and setup costs, which currently total $400,000 annually, would decline by 20%. d. The emphasis on quality inherent in JIT production would reduce rework costs by 25%. The Knot currently incurs $160,000 in annual rework costs. e. Improved product quality under JIT production would enable The Knot to raise the price of its product by $2 per unit. The Knot sells 100,000 units each year. The Knot’s required rate of return on inventory investment is 15% per year. Q. Suppose The Knot implements JIT production at its Spartanburg plant. Give examples of performance measures The Knot could use to evaluate and control JIT…arrow_forwardThe Colin Division of Crane Company sells its product for $30.00 per unit. Variable costs per unit include: manufacturing, $13.80; and selling and administrative, $4.00. Fixed costs are: $322000 manufacturing overhead, and $54000 selling and administrative. There was no beginning inventory. Expected sales for next year are 46000 units. Matthew Young, the manager of the Colin Division, is under pressure to improve the performance of the Division. As part of the planning process, he has to decide whether to produce 46000 units or 54000 units next year. What would the manufacturing cost per unit be under variable costing for each alternative? 46000 units 54000 units $13.80 $13.80 $17.80 $17.80 $19.55 $20.80 $20.80 $19.55arrow_forwardArtisan Metalworks has a bottleneck in their production that occurs within the engraving department. Jamal Moore, the COO, is considering hiring an extra worker, whose salary will be $54,000 per year, to solve the problem. With this extra worker, the company could produce and sell 2,900 more units per year. Currently, the selling price per unit is $25.00 and the cost per unit is $7.50. Direct materials $3.40 Direct labor Variable overhead Fixed overhead (primarily depreciation of equipment) Total 1.00 0.40 2.70 $7.50 Using the Information provided, calculate the annual financial Impact of hiring the extra worker. Profit $ ✓ Increasearrow_forward
- Principles of Accounting Volume 2AccountingISBN:9781947172609Author:OpenStaxPublisher:OpenStax CollegeCornerstones of Cost Management (Cornerstones Ser...AccountingISBN:9781305970663Author:Don R. Hansen, Maryanne M. MowenPublisher:Cengage LearningEBK CONTEMPORARY FINANCIAL MANAGEMENTFinanceISBN:9781337514835Author:MOYERPublisher:CENGAGE LEARNING - CONSIGNMENT
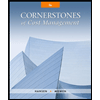
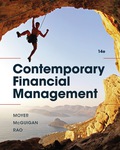