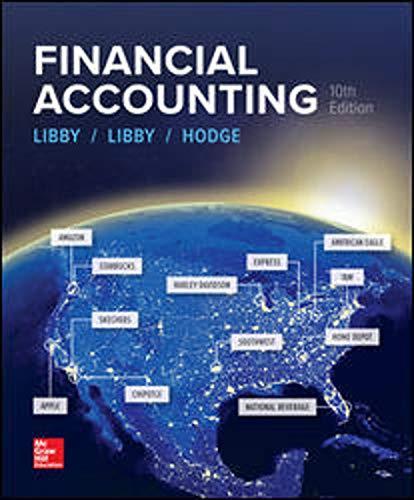
Woodruff Company is currently producing a snowmobile that uses five specialized parts. Engineering has proposed replacing these specialized parts with commodity parts, which will cost less and can be purchased in larger order quantities. Current activity capacity and demand (with specialized parts required) and expected activity demand (with only commodity parts required) are provided.
Activities | Activity Driver | Activity Capacity |
Current Activity Demand |
Expected Activity Demand |
Material usage | Number of parts | 192,000 | 192,000 | 192,000 |
Installing parts | Direct labor hours | 90,000 | 90,000 | 72,000 |
Purchasing parts | Number of orders | 20,000 | 17,100 | 10,500 |
Additionally, the following activity cost data are provided:
Material usage: $20 per specialized part used; $16 per commodity part; no fixed activity cost.
Installing parts: $14 per direct labor hour; no fixed activity cost.
Purchasing parts: Four salaried clerks, each earning a $45,000 annual salary; each clerk is capable of processing 5,000 purchase orders. Variable activity costs: $0.80 per purchase order processed for forms, postage, etc.
Required:
1. Calculate the cost reduction produced by using commodity parts instead of specialized parts. Enter your answers as positive amounts.
Material usage cost reduction | $fill in the blank 1 |
Labor usage cost reduction | fill in the blank 2 |
Purchasing cost reduction | fill in the blank 3 |
Total savings | $fill in the blank 4 |
2. Suppose that 50,000 units are being produced and sold for $8,800 per unit and that the price per unit will be reduced by the per-unit savings. What is the new price for the configured product? If required, round your intermediate calculations and final answer to the nearest cent.
$fill in the blank 5
3. What if the expected activity demand for purchase orders was 8,500? How would this affect the answers to Requirements 1 and 2? If required, round your intermediate calculations and final answers to the nearest cent.
Total savings | by | $fill in the blank 7 | to | $fill in the blank 8 | |
New price | by | $fill in the blank 10 | to | $fill in the blank 11 |

Trending nowThis is a popular solution!
Step by stepSolved in 2 steps

- Problem 08.023- Determine which robot to select based on incremental rate of return A process control manager is considering two robots to improve materials-handling capacity in the production of rigid shaft couplings that make dissimilar drive components. Robot X has a first cost of $84,000, an annual M&O cost of $31,000, and $40,000 salvage value, and it will improve revenues by $96,000 per year. Robot Y has a first cost of $146,000, an annual M&O cost of $28,000, and $47,000 salvage value, and it will increase revenues by $125,000 per year. The company's MARR is 25.00% per year, and it uses a 3- year study period for economic evaluations. Calculate the incremental ROR, and identify the robot the manager should select. (Round the final answer to three decimal places.) The incremental ROR is 26.598 %. The manager should select robot Yarrow_forwardWindu Enterprises uses a manufacturing process that is very labor intensive to manufacture its multicolored laser vegetable slicers. Windu is considering a change to a more automated manufacturing process. The cost structure information for Windu's options are listed below. Windu sells its only product for $25 per unit. Costs Fixed Manufacturing Costs Variable Manufacturing Cost per unit Current Method $180,000 $15 Automated Method $240,000 $13 Required. 1. Compute the breakeven points for both production methods 2. Compute the point of indifference for these two production methods (i.e. at what number of units of production will income be equal for both methods?) 3. Calculate the Operating Leverage Factor for both methods at the point of indifference + 4. If Windu's management intends to produce and sell 35,000 units, which production method should they use? 5. By how much per unit (nearest $.01) would the current method's variable cost need to decrease in order for management to be…arrow_forwardAn operations manager is deciding on the level of automation for a new process. The fixed cost for automation includes the equipment purchase price, installation, and initial spare parts. The variable costs per unit for each level of automation are primarily labor related. Each unit can be sold for $81. As in many cases, you have the default alternative of doing nothing ($0 fixed cost, $0 variable costs). Hint: For these questions, also consider the “Do Nothing” option as a viable option when making your decision. Alternative Fixed Costs Variable Costs per Unit A $100,000 $54 B $272,000 $31 C $560,000 $20 Recommended: graph each alternative with units on the x-axis and $ on the y-axis. Also, include revenue on the chart. Identify the break-even points and points of indifference.arrow_forward
- Preparing a Standard Cost Card -Redwing EXO-7 Industries manufactures a Redwing reconnaissance drone. The following information pertains to its manufacturing costs. To make one redwing unit it takes 2 pounds of titanium and 0.5 pounds of carbon fiber. The company expects 0.01 pounds of waste for titanium and 0.02 waste for the carbon fiber materials. Titanium costs are anticipated at $10.25 per pound and carbon fiber costs are anticipated at $5.25 per pound. A 1% discount is offered to EXO-7 Industries from its suppliers. The redwing unit requires two labor processes to complete it -assembly and programming. Assembly laborers are paid $17 per hour and programming laborers are paid $27 per hour. Fringe benefits and payroll taxes for assembly and programming laborers amount to $1.75 and $5.25 per hour, respectively. Based on the company’s experience and research, it expects to use 5.0 hours of assembly and 10 hours of programming. The company uses direct labor hours as…arrow_forwardi need the answer quicklyarrow_forward>>>>_____arrow_forward
- The Quality Athletics Company produces a wide variety of outdoor sports equipment. Its newest division, Golf Technology, manufactures and sells a single product: AccuDriver, a golf club that uses global positioning satellite technology to improve the accuracy of golfers' shots. The demand for AccuDriver is relatively insensitive to price changes. The following data are available for Golf TechnoloTotal annual fixed costs $30,000,000 Variable cost per AccuDriver $440 Number of AccuDrivers sold each year 155,000 Average operating assets invested in the division $ 50,000,0001. Compute Golf Technology's ROI if the selling price of AccuDrivers is $ 740 per club. 2. If management requires an ROI of at least 20% from the division, what is the minimum selling price that the Golf Technology Division should charge per AccuDriver club? 3. Assume that Quality Athletics judges the performance of its investment centres on the basis of RI rather than ROI. What is the minimum selling price that Golf…arrow_forwardIndustrial Robots does not manufacture its own motors or computer chips. Its premium product differs from its standard product in having heavier-duty motors and more computer chips for greater flexibility. As a result, Industrial Robots manufactures a higher fraction of the standard product’s value itself, and it purchases a higher fraction of the premium product’s value. Use the following data to allocate $850,000 in overhead on the basis of labor cost and materials cosarrow_forwardThe Gargus Company, which manufactures projection equipment, is ready to introduce a new line of portable projectors. The following data are available for a proposed model: Variable manufacturing costs Applied fixed manufacturing overhead Variable selling and administrative costs Applied fixed selling and administrative costs $ 380 190 145 160 What price will the company charge if the firm uses cost-plus pricing based on total variable cost and a markup percentage of 205%?arrow_forward
- The Chopin Company has decided to introduce a new product. The new product can be manufactured by either a computer-assisted manufacturing (CAM) or a labor-intensive production (LIP) system. The manufacturing method will not affect the quality of the product. The estimated manufacturing costs for each of the two methods are as follows. CAM System: Direct Material = $5.0 Direct Labor (DLH) = 0.5 DLH X $12 = $6 Variable Overhead = 0.5DLHx$6 = $3 Fixed Iverhead* = $ 2,440,000 LIP System: Direct Material = $5.6 Direct Labor (DLH) = 0.8 DLH X $9 = $7.2 Variable Overhead = 0.8 DLH X $6 = $4.8 Fixed Overhead* = $1,320,000 *These costs are directly traceable to the new product line. They would not be incurred if the new product were not produced. The company’s marketing research department has recommended an introductory unit sales price of $30. Selling expenses are estimated to be $500,000 annually plus $2 for each unit sold. (Ignore income taxes.) Required: Calculate the estimated…arrow_forwardWoodruff Company is currently producing a snowmobile that uses five specialized parts. Engineering has proposed replacing these specialized parts with commodity parts, which will cost less and can be purchased in larger order quantities. Current activity capacity and demand (with specialized parts required) and expected activity demand (with only commodity parts required) are provided. Activities Activity Driver ActivityCapacity Current ActivityDemand Expected ActivityDemand Material usage Number of parts 200,000 200,000 200,000 Installing parts Direct labor hours 20,000 20,000 16,000 Purchasing parts Number of orders 7,600 6,498 3,990 Additionally, the following activity cost data are provided: Material usage: $11 per specialized part used; $27 per commodity part; no fixed activity cost. Installing parts: $21 per direct labor hour; no fixed activity cost. Purchasing parts: Four salaried clerks, each earning a $47,000 annual salary; each clerk is capable of processing 1,900…arrow_forwardHall, Incorporated manufactures two components, Standard and Ultra, that are designed for the same function, but are made of different metals for operational performance reasons. The metal used in Standard is easy to work with and there are few quality issues or reworking required on the machines. The metal used in Ultra is more difficult to work with and often needs additional machine time and rework. Data on expected operations and direct costs for the next fiscal year follow: Account Administration Engineering Machine operation and maintenance Standard Miscellaneous Supervision Total 48,000 144,000 24,000 Ultral $ 3,384,000 2,520,000 Units produced Direct labor-hours used Machine-hours used Direct materials costs $5,163,000 Direct labor costs 855,000 The planning process team at Hall, Incorporated has estimated the following manufacturing overhead costs for the next fiscal year: 16,500 22,500 22,500 Total Amount $ 825,400 5,699,500 875,000 540,100 884,500 $8,824,500. 64,500 166,500…arrow_forward
- AccountingAccountingISBN:9781337272094Author:WARREN, Carl S., Reeve, James M., Duchac, Jonathan E.Publisher:Cengage Learning,Accounting Information SystemsAccountingISBN:9781337619202Author:Hall, James A.Publisher:Cengage Learning,
- Horngren's Cost Accounting: A Managerial Emphasis...AccountingISBN:9780134475585Author:Srikant M. Datar, Madhav V. RajanPublisher:PEARSONIntermediate AccountingAccountingISBN:9781259722660Author:J. David Spiceland, Mark W. Nelson, Wayne M ThomasPublisher:McGraw-Hill EducationFinancial and Managerial AccountingAccountingISBN:9781259726705Author:John J Wild, Ken W. Shaw, Barbara Chiappetta Fundamental Accounting PrinciplesPublisher:McGraw-Hill Education
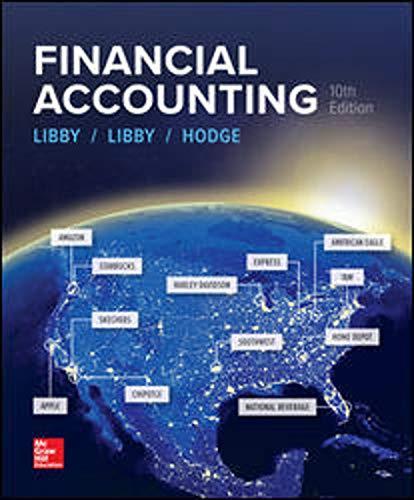
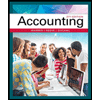
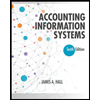
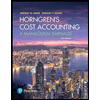
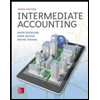
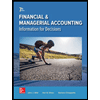