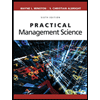
Practical Management Science
6th Edition
ISBN: 9781337406659
Author: WINSTON, Wayne L.
Publisher: Cengage,
expand_more
expand_more
format_list_bulleted
Concept explainers
Topic Video
Question
Which of the following is the planned order receipts using an MRP program with lot-for-lot policy if the inventory on hand is 0,
Expert Solution

This question has been solved!
Explore an expertly crafted, step-by-step solution for a thorough understanding of key concepts.
Step by stepSolved in 5 steps

Knowledge Booster
Learn more about
Need a deep-dive on the concept behind this application? Look no further. Learn more about this topic, operations-management and related others by exploring similar questions and additional content below.Similar questions
- Assume material A calls out material B (qty per = 1). Material A has a stock quantity of 10. Material A has a demand for 100 due on 7/1 and there is an order for 90 with a due date of 7/1 and start date of 6/15. What is the requirement QUANTITY that will be generated for product B?arrow_forwardPlease do not give solution in image format thankuarrow_forwardFind MPS start as wellarrow_forward
- Subject: Logistic management The following information is given to you D = 19,000 units/yr; H = $4/unit/year; S=$25/order. Calculate the EOQ, Annual holding cost and annual ordering cost.arrow_forward10.5 An SKU has an annual demand of 10,000 units, each costing $20, ordering costs are $80 per order, and the cost of carrying inventory is 25%. Calculate the EOQ in units and then convert to dollars.arrow_forwardDevelop a lot-for-lot solution and calculate total relevant costs for the gross requirements in the following table*. 5 6 7 30 70 30 9 10 11 12 60 10 70 Period 1 Gross requirements 20 2 Period Gross requirements On-hand at beginning of period 40 On-hand at end of period Order receipt Order release 3 40 1 20 4 *Holding cost = $3.50/unit/week; setup cost = $200; lead time = 1 week; beginning inventory = 40. Develop a lot-for-lot solution (enter your responses as whole numbers). 2 3 40 4 8 5 6 30 7 70 30 8 9 10 11 12 10 70 60 cornarrow_forward
- If no safety stock is required, what would the re-order point be?arrow_forwardDevelop a lot-for-lot solution and calculate total relevant costs for the gross requirements in the following table*. Period Gross requirements Develop a lot-for-lot solution (enter your responses as whole numbers). Period Gross requirements On-hand at beginning of period On-hand at end of period 1 Order receipt Order release 30 2 3 30 1 30 40 || 4 5 2 6 7 40 70 20 *Holding cost = $3.50/unit/week; setup cost = $150; lead time = 1 week; beginning inventory = 40. 3 4 30 8 9 10 11 12 5 6 7 40 70 20 20 80 8 60 9 10 20 80 11 12 60arrow_forwardFull stepsarrow_forward
- In reference to the attached image: What would be the impact of a scheduled receipt of 200 units for item B in week 3 (and allother data remained the same) on your calculated planned order receipts and releases?arrow_forwardExercise 11.8 We Care Associates (WCA), a local physician practice group, orders supplies from various distributors. Order quantities of fifteen items have been determined based on the past five years of usage. Other relevant information from the practice’s inventory records is depicted in Table EX 11.8. The practice is functional for fifty-two weeks a year. Item No. Weekly Demand (Unit/Week) Unit Cost ($) Yearly Carrying Rate of Each Item Ordering Cost ($) 1 400 2.50 15% 12.00 2 1,600 0.50 16% 6.00 3 175 37.50 20% 32.00 4 250 3.5 12% 50.00 5 250 1.75 18% 12.00 6 32 2,300.00 2% 35.00 7 1,500 1.25 14% 10.00 8 2,200 0.65 17% 6.00 9 1,270 0.95 21% 5.00 10 120 12.50 12% 12.00 11 220 2.00 15% 28.00 12 350 1.50 14% 18.00 13 18 5,000.00 2% 25.00 14 6 6,700.00 2% 50.00 15 1,250 2.60 22% 19.00…arrow_forwardUsing the gross requirements schedule below*, prepare an alternative ordering system that orders every 3 weeks for 3 weeks ahead (a periodic order quantity). What is the cost of this ordering system? Period 1 2 3 4 5 6 7 Gross requirements 25 20 40 0 10 50 30 The cost of this ordering system is $ Prepare a net requirements plan (enter your responses as whole numbers). *Holding cost = $1/unit/week; setup cost = $200; lead time = 1 week; beginning inventory = 25 units. Period Gross requirements On-hand at beginning of period On-hand at end of period Net requirements Order receipt Order release (enter your response as a whole number). 25 1 25 2 20 3 40 4 5 0 10 8 0 6 50 9 10 30 65 7 30 8 9 10 0 30 65arrow_forward
arrow_back_ios
arrow_forward_ios
Recommended textbooks for you
- Practical Management ScienceOperations ManagementISBN:9781337406659Author:WINSTON, Wayne L.Publisher:Cengage,Operations ManagementOperations ManagementISBN:9781259667473Author:William J StevensonPublisher:McGraw-Hill EducationOperations and Supply Chain Management (Mcgraw-hi...Operations ManagementISBN:9781259666100Author:F. Robert Jacobs, Richard B ChasePublisher:McGraw-Hill Education
- Purchasing and Supply Chain ManagementOperations ManagementISBN:9781285869681Author:Robert M. Monczka, Robert B. Handfield, Larry C. Giunipero, James L. PattersonPublisher:Cengage LearningProduction and Operations Analysis, Seventh Editi...Operations ManagementISBN:9781478623069Author:Steven Nahmias, Tava Lennon OlsenPublisher:Waveland Press, Inc.
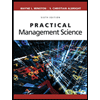
Practical Management Science
Operations Management
ISBN:9781337406659
Author:WINSTON, Wayne L.
Publisher:Cengage,
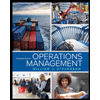
Operations Management
Operations Management
ISBN:9781259667473
Author:William J Stevenson
Publisher:McGraw-Hill Education
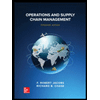
Operations and Supply Chain Management (Mcgraw-hi...
Operations Management
ISBN:9781259666100
Author:F. Robert Jacobs, Richard B Chase
Publisher:McGraw-Hill Education
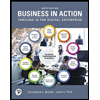
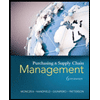
Purchasing and Supply Chain Management
Operations Management
ISBN:9781285869681
Author:Robert M. Monczka, Robert B. Handfield, Larry C. Giunipero, James L. Patterson
Publisher:Cengage Learning
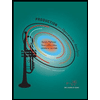
Production and Operations Analysis, Seventh Editi...
Operations Management
ISBN:9781478623069
Author:Steven Nahmias, Tava Lennon Olsen
Publisher:Waveland Press, Inc.