What are the main points of this case?
Chapter1: Taking Risks And Making Profits Within The Dynamic Business Environment
Section: Chapter Questions
Problem 1CE
Related questions
Question
What are the main points of this case?

Transcribed Image Text:SEX
e
1
2
3
2
- 3-
Machine Tools
research and the country organizations worked to develop and apply new
production methods. Moto employed the company's own equipment, such as
numerical controls and minicomputers, and had developed unique software and
automation techniques.
584-074
THE NUMERICAL CONTROL INDUSTRY
Machine tools were power-driven equipment for shaping metal,
either by cutting (over 80%) or forming. They were made primarily in
Europe, the U.S. and Japan by original equipment manufacturers (OEMs) who
took great pride in machine precision and reliability. West Germany
accounted for 40% of machine tools made in Europe.
OEMS sold to end users, ranging from large, sophisticated
aircraft and automotive manufacturers, that shaped metal parts on assembly
lines to "job shops" that fabricated workpieces in small batches or single
units. Until the introduction of NCs, all machine tools were controlled
manually by highly skilled operators who followed a pattern drawn by a
design engineer. The operator used dials and handles to move the workpiece
and tool.
Numerical Controls
NCs were devices that, following a program, electronically
directed the movements of the workpiece and tools, freeing the operator
from manual control. Early NCs were programmed through a paper tape, on
which a production engineer punched a program using special tape writing
machines. The operator installed the proper tool (such as a drill bit),
secured the workpiece, and then fed the tape through the NC.
These early NCs doubled the capacity of a machine tool, ensured
that all pieces met the same precise specifications, and increased labor
productivity; however, they were expensive, needed engineers who knew how
to develop the programs, and required trained operators. During the 1950s
and 1960s few machine tools were numerically controlled. The few end users
tended to be large innovative manufacturers. U.S. defense contractors, in
particular, were compelled to use them, by the insistence of the U.S. Air
Force. NC demand did not grow widely until the mid-1970s, when techno-
logical innovations lowered costs and improved performance.
Technological Advances
The key technological advance was the computerization of NCs
enabling the writing and storage of "software." Software was a general.
program which an NC programmer used to write specific "workpiece programs"
that were different but of the same general form. Early computerized NCs
used minicomputers and were expensive, but in the mid-1970s the micro-
computer allowed costs to drop and capacity and reliability to increase.
By 1983 only a few minicomputer NCs were still produced; Moto made only
microcomputer NCS.
584-074
As NC computer hardware grew in capacity, software was developed
to handle more complex and precise machine tool functions. Although some
NC manufacturers licensed third party software houses, most wrote their own
software for their units, and the writing of software grew to dominate
development efforts. In 1982, 80% of ICD's NC development cost was for
software; development, in turn, accounted for 30% of total NC costs. ICD
worked closely with its largest customers on software; but like other
makers, it used knowledge obtained from all its customers to develop
software that could handle increasingly numerous and complex machine tool.
functions. By 1983, software could automatically compensate tool speed for
tool wear, increasing the "up time" of the machine. New "user friendly"
software allowed machine tool operators to program a workpiece or batch,
often in only a few minutes, without the help of a computer programmer.
New software also enhanced the precision and quality of the workpieces.
OEMS were developing machine tools that performed new and more
sophisticated functions. A major advance was the introduction of machining
centers, greatly expanded machine tools with multiple tools that
automatically changed tools according to an NC program. These new tools
necessitated more powerful NCs and new software. Moto made an NC that had
capacity and software to control a machining center with up to 5 axes, 32
tools, high power functions, and close tolerance.
The early NC machine tools could not easily interface with other
machinery or outside operations. In the mid-1970s, programmable
controllers (PCs) were developed. PCs were integrated with an NC and
provided data and signals to link the machine tool to other equipment. ICD
marketed a line of PCs separately from its NCs, because many OEMs bought
NCs and PCs from different suppliers. A PC required its own software, and
the PC's capacity and software determined how complex the interface between
the machine tool and other automated equipment could be.
The first important use of PCs was loading and unloading.
Conveyor belts moved a batch of workpieces one by one to be secured
automatically to the machine tool. The PC signaled the belt to move; as
each successive workpiece was secured, the PC checked alignment and
signaled the NC to start the program again. An operator could load a batch.
of workpieces and let the machine tool run, tremendously enhancing
productivity.
Although these advances made NC machine tools applicable to more
end-user operations and demand grew, in 1983 many end users still found
that the programs did not adequately solve their manufacturing problems.
Motofabrikwerk's Role
Moto entered the NC business in 1962 and worked only with
European machine tool OEMS. European OEMs, numbering less than 500 with
some building only a few specialized machines a year, proved reluctant to
adopt NCs. Moto soon became the third largest NC vendor in Europe, behind
Siemens and Philips. Siemens, based in Munich, gained the dominant share
in West Germany. In 1983, Moto sold to 21 European OEMs, only 6 of whom
bought more than 50 units in 1982. Some machine tool builders, such as

Transcribed Image Text:1
2
3
DOZ
Harvard Business School
MOTOFABRIKWERK S.A. (A)
9-584-074
Rev. 6/85
In August 1983, Mr. Hans Overmeyer, marketing vice president of
the Industrial Controls Division (ICD) of Motofabrikwerk S.A. in Zurich,
Switzerland, was reviewing his numerical control business. Numerical
controls (NCs) were computerized devices which directed machine tools.
Motofabrikwerk (Moto) sold NCs to machine tool builders who sold
numerically controlled machine tools to diverse end users.
Moto entered the NC business in 1962 and by 1983 was the third
largest merchant supplier of NCs in Europe. ICD, however, reported a loss.
of 5% of sales in 1982 and again for the first six months of 1983.
Overmeyer attributed the losses to the sharp drop in worldwide demand for
machine tools, caused by the most severe recession since the 1930s, and to
intensifying competition. ICD faced both steeply declining competitive
prices and substantial expenses for continuing research and development.
Overmeyer had to submit the 1984 development budget in early
September and wondered whether the $3 million needed to maintain the
business could be justified. Some experts considered the prospects of the
NC business as potentially enormous and others saw it offering a major
entry into the "factory of the future." Moto, with a strong position in
electronic equipment and internal expertise in manufacturing automation,
was among the few European concerns along with Siemens, Philips,
Olivetti, and ASEA- which might have the resources and knowledge to
compete effectively in the emerging factory automation business.
MOTOFABRIKWERK
Moto reported 1982 revenues of SFr. 19.4 billion ($9.7 billion), ¹
profits of SFr. 440 million ($220 million), assets of SFr. 20.3 billion
($10.15 billion), and a solid balance sheet.
In 1982, the Swiss franc (SFr.) exchanged for approximately $.50.
This case was prepared by Research Assistant Edward J. Hoff, under the
supervision of Professor Benson P. Shapiro as the basis for class
discussion rather than to illustrate either effective or ineffective
handling of an administrative situation. Assistant Professor Frank V.
Cespedes provided substantial editorial support.
Copyright © 1984 by the President and Fellows of Harvard College
means
No part of this publication may be reproduced, stored in a retrieval system, or transmitted in any form or by any me
electronic, mechanical, photocopying, recording, or otherwise-without the permission of Harvard Business School.
Distributed by HBS Case Services, Harvard Business School, Boston, MA 02163. Printed in U.S.A.
584-074
History
- 2-
584-074
Two Swiss engineers founded Moto in 1902 to manufacture electric
motors for street cars and other machinery. In 1908, the company began
manufacturing internal combustion engines for European automobile and truck.
assemblers. After World War I, the company began producing electric
generators, electrical parts such as starters for automobiles, and
electromechanical controls such as governors for electric motors.
Organization
After World War II, Moto again grew rapidly. Management used.
knowledge gained from the electromechanical control business and extensive
R&D efforts to launch three additional major product lines: 1)
sophisticated electronic testing and measuring instruments, such as
advanced volt and current meters, 2) products that controlled certain
manufacturing operations, including numerical controls, and 3) integrated
circuits and minicomputers, introduced in 1969.
Moto's organization had evolved into a matrix, with both product
divisions and country organizations, and with profit and revenue figures
kept by each structure. In 1983, Moto had 7 product divisions, each run by
a general manager. (Exhibit 1 lists the divisions and their 1982
revenues.) The 29 country organizations, each run by a country manager,
had responsibility for sales, manufacturing, and administration for all
Moto products sold or made in that country. Europe accounted for 65% of
total revenues, and the U.S. for 22%.
Each product line sales force was organized by country and
reported through the country organizations. The marketing and product
development staff reported through the product divisions. The sales force
worked with the product division staff to adapt product to a particular
country's needs. Division management had to work with the management in
each country to introduce a new pricing policy or new product line.
A 7-member board of management composed of the managing director
(CEO) and 6 other senior officers had final managerial authority. The
board set policy, but seldom intervened in individual negotiations among
company units. But it would intercede when combined efforts, such as those
of two or more product divisions, were needed to address an emerging
market. Such actions were sometimes requested by a division manager, but
they were scrutinized carefully.
Research and Manufacturing
Moto had an extensive central research center, in addition to the
division product development staffs. Research was a top priority and
source of pride. The 1982 central research budget was $650 million, 7% of
sales. This effort had resulted in numerous technological advancements and
new product introductions.
Intense competition in its main product lines had caused Moto to
automate production for lower costs and quality improvement. Central
584-074
Expert Solution

This question has been solved!
Explore an expertly crafted, step-by-step solution for a thorough understanding of key concepts.
This is a popular solution!
Trending now
This is a popular solution!
Step by step
Solved in 3 steps

Recommended textbooks for you
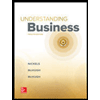
Understanding Business
Management
ISBN:
9781259929434
Author:
William Nickels
Publisher:
McGraw-Hill Education
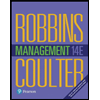
Management (14th Edition)
Management
ISBN:
9780134527604
Author:
Stephen P. Robbins, Mary A. Coulter
Publisher:
PEARSON
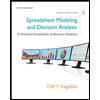
Spreadsheet Modeling & Decision Analysis: A Pract…
Management
ISBN:
9781305947412
Author:
Cliff Ragsdale
Publisher:
Cengage Learning
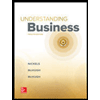
Understanding Business
Management
ISBN:
9781259929434
Author:
William Nickels
Publisher:
McGraw-Hill Education
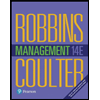
Management (14th Edition)
Management
ISBN:
9780134527604
Author:
Stephen P. Robbins, Mary A. Coulter
Publisher:
PEARSON
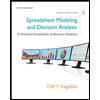
Spreadsheet Modeling & Decision Analysis: A Pract…
Management
ISBN:
9781305947412
Author:
Cliff Ragsdale
Publisher:
Cengage Learning
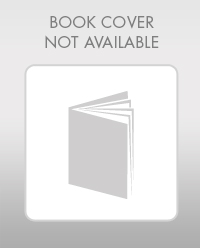
Management Information Systems: Managing The Digi…
Management
ISBN:
9780135191798
Author:
Kenneth C. Laudon, Jane P. Laudon
Publisher:
PEARSON
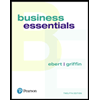
Business Essentials (12th Edition) (What's New in…
Management
ISBN:
9780134728391
Author:
Ronald J. Ebert, Ricky W. Griffin
Publisher:
PEARSON
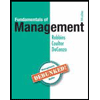
Fundamentals of Management (10th Edition)
Management
ISBN:
9780134237473
Author:
Stephen P. Robbins, Mary A. Coulter, David A. De Cenzo
Publisher:
PEARSON