What are the factors that can affect productivity and some ways that productivity can be improved? NOTE: please based the answer in the given lesson below
What are the factors that can affect productivity and some ways that productivity can be improved? NOTE: please based the answer in the given lesson below
Chapter1: Taking Risks And Making Profits Within The Dynamic Business Environment
Section: Chapter Questions
Problem 1CE
Related questions
Question
What are the factors that can affect productivity and some ways that productivity can be improved?
NOTE: please based the answer in the given lesson below

Transcribed Image Text:FACTORS THAT AFFECT PRODUCTIVITY
Numerous factors affect productivity. Generally, they are methods, capital, quality, tech-
nology, and management.
A commonly held misconception is that workers are the main determinant of produc-
tivity. According to that theory, the route to productivity gains involves getting employ-
ees to work harder. However, the fact is that many productivity gains in the past have
come from technological improvements. Familiar examples include:
Fax machines
Computerized billing and inventories
Automation
Calculators
Computers, personal computers, laptops
Copying machines
Microwave ovens
The Internet
Answering machines, voice mail,
cellular phones
E-mail
Software
However, technology alone won't guarantee productivity gains; it must be used wisely
and thoughtfully. Without careful planning, technology can actually reduce productivity,
especially if it leads to inflexibility, high costs, or mismatched operations. Another cur-
rent productivity pitfall wiults from employees' use of computers for non-work-related
activities (playing games or checking stock prices or sports scores on the Internet). Be-
yond all of these is the dip in productivity that results while employees learn to use new
equipment or procedures that will eventually lead to productivity gains after the learning
phase ends.
Standardizing processes and procedures wherever possible can have a significant im-
pact on both productivity and quality.
Quality differences may distort productivity measurements. One way this can happen
is when comparisons are made over time, such as comparing the productivity of a factory
now with one in the 1970s. Quality is now much higher than it was then, but there is no
simple way to incorporate quality into productivity measurements.
Use of the Internet can lower costs of a wide range of transactions, thereby increasing
productivity. It is likely that this effect will continue to increase productivity in the fore-
seeable future.
Computer viruses can have an immense negative impact on productivity.
Searching for lost or misplaced items wastes time, hence negatively affecting produc-
tivity.
Scrap rates have an adverse effect on productivity, implying inefficient use of re-
sources.
New workers tend to have lower productivity than seasoned workers. Thus, growing
companies may experience a productivity lag.
Safety should be addressed. Accidents can take a toll on productivity.
A shortage of information technology workers and other technical workers hampers
the ability of companies to update computing resources, generate and sustain growth, and
take advantage of new opportunities.
Layoffs often affect productivity. The effect can be positive and negative. Initially, pro-
ductivity may increase after a layoff, because the workload remains the same but fewer

Transcribed Image Text:IMPROVING
PRODUCTIVITY
A company or a department can take a number of key steps toward improving productivity:
1. Develop productivity measures for all operations; measurement is the first step in
managing and controlling an operation.
2. Look at the system as a whole in deciding which operations are most critical; it is over-
all productivity that is important. This concept is illustrated in Figure 2-3, which
shows several operations feeding their output into a bottleneck operation. The capac-
ity of the bottleneck operation is less than the combined capacities of the operations
that provide input, so units queue up waiting to be processed; hence the term bottle-
neck. Productivity improvements to any nonbottleneck operation will not affect the
productivity of the system. Improvements in the bottleneck operation will lead to in-
creased productivity, up to the point where the output rate of the bottleneck equals the
output rate of the operations feeding it.
3. Develop methods for achieving productivity improvements, such as soliciting ideas
from workers (perhaps organizing teams of workers, engineers, and managers), study-
ing how other firms have increased productivity, and reexamining the way work is
done.
4. Establish reasonable goals for improvement.
5. Make it clear that management supports and encourages productivity improvement.
Consider incentives to reward workers for contributions.
6. Measure improvements and publicize them.
7. Don't confuse productivity with efficiency. Efficiency is a narrower concept that per-
tains to getting the most out of afixed set of resources; productivity is a broader con-
cept that pertains to effective use of overall resources. For example, an efficiency
perspective on mowing a lawn given a hand mower would focus on the best way to use
the hand mower; a productivity perspective would include the possibility of using a
power mower.
Expert Solution

This question has been solved!
Explore an expertly crafted, step-by-step solution for a thorough understanding of key concepts.
Step by step
Solved in 2 steps

Recommended textbooks for you
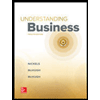
Understanding Business
Management
ISBN:
9781259929434
Author:
William Nickels
Publisher:
McGraw-Hill Education
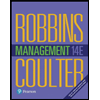
Management (14th Edition)
Management
ISBN:
9780134527604
Author:
Stephen P. Robbins, Mary A. Coulter
Publisher:
PEARSON
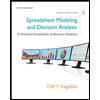
Spreadsheet Modeling & Decision Analysis: A Pract…
Management
ISBN:
9781305947412
Author:
Cliff Ragsdale
Publisher:
Cengage Learning
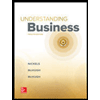
Understanding Business
Management
ISBN:
9781259929434
Author:
William Nickels
Publisher:
McGraw-Hill Education
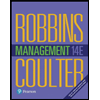
Management (14th Edition)
Management
ISBN:
9780134527604
Author:
Stephen P. Robbins, Mary A. Coulter
Publisher:
PEARSON
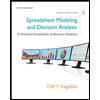
Spreadsheet Modeling & Decision Analysis: A Pract…
Management
ISBN:
9781305947412
Author:
Cliff Ragsdale
Publisher:
Cengage Learning
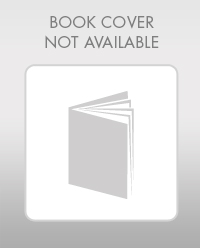
Management Information Systems: Managing The Digi…
Management
ISBN:
9780135191798
Author:
Kenneth C. Laudon, Jane P. Laudon
Publisher:
PEARSON
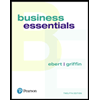
Business Essentials (12th Edition) (What's New in…
Management
ISBN:
9780134728391
Author:
Ronald J. Ebert, Ricky W. Griffin
Publisher:
PEARSON
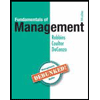
Fundamentals of Management (10th Edition)
Management
ISBN:
9780134237473
Author:
Stephen P. Robbins, Mary A. Coulter, David A. De Cenzo
Publisher:
PEARSON